what is fcaw welding
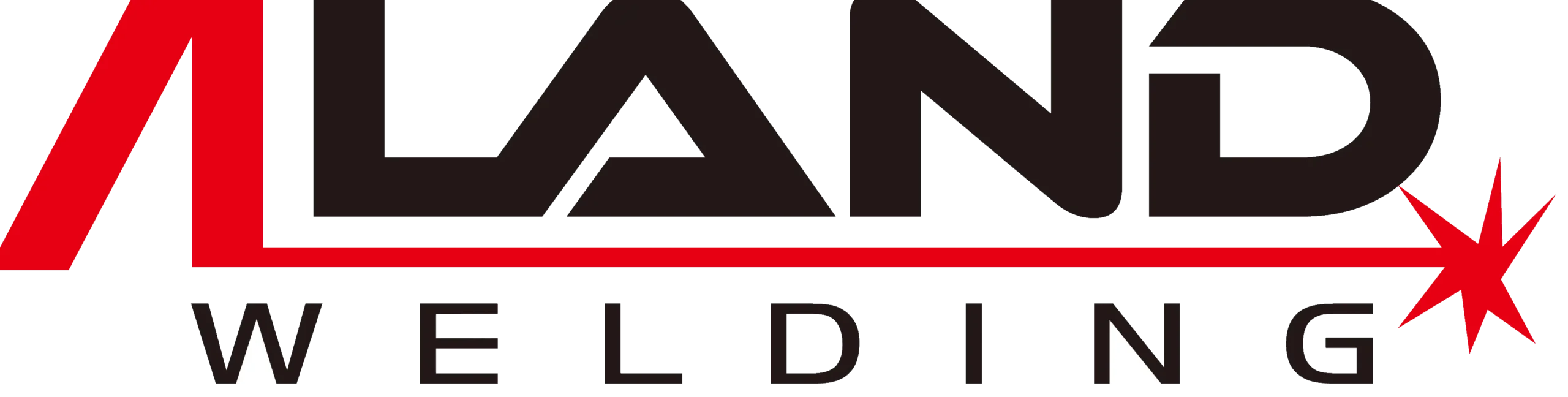
ALAND WELDING Let you feel the most sincere welding service
Introduction to fcaw welding
The basic working principle of fcaw welding is the same as that of ordinary gas metal arc welding. The meltable flux-cored welding wire is used as one electrode (usually connected to the positive electrode, that is, DC reverse connection), and the base material is used as the other electrode. Pure CO2 or CO2+Ar gas is usually used as the protective gas. The main difference from ordinary gas metal arc welding is that the welding wire contains a flux mixture. During welding, the flux material, welding wire metal, base metal and shielding gas in the molten state undergo metallurgical interactions with each other under the action of arc heat. At the same time, a thin layer of liquid slag is formed to coat the droplets and cover the molten pool. The molten metal creates yet another layer of protection. In essence, this welding method is a method of combined gas and slag protection.
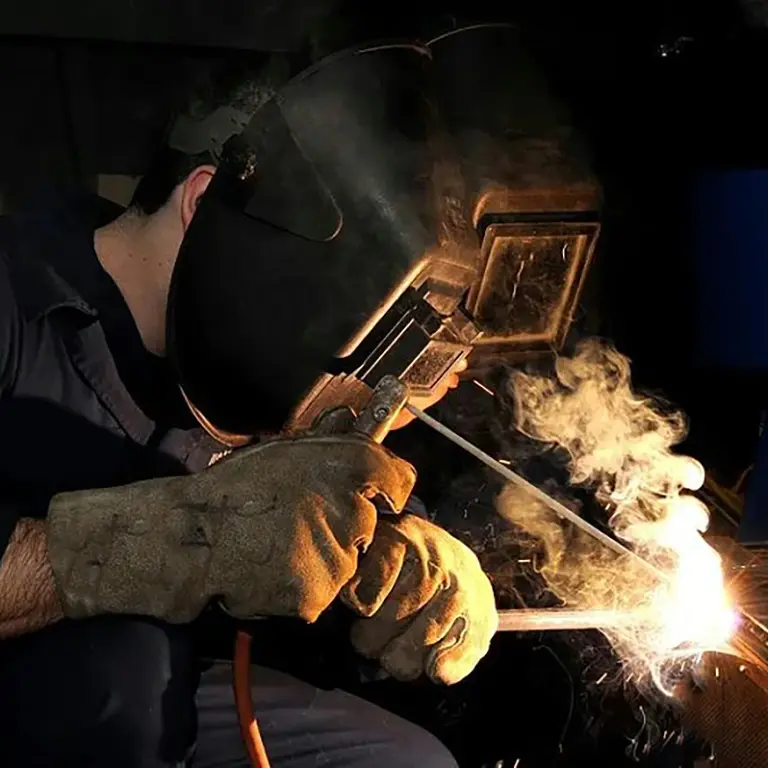
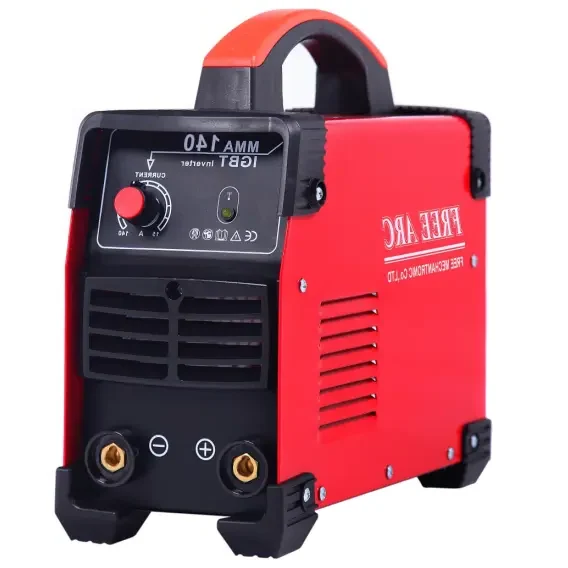
Fcaw Welding Advantages And Disadvantages
Advantage
FCAW welding combines the advantages of manual arc welding and ordinary gas metal arc welding. Its main advantages are:
(1) Using combined gas and slag protection, the welding seam has beautiful appearance, good arc stability, less spatter and fine particles.
(2) The welding wire deposition speed is fast, and the deposition efficiency (about 85%~90%) and productivity are high (productivity is 3~5 times higher than manual welding).
(3) It has strong adaptability to welding various steel materials. By adjusting the composition and proportion of the flux, the required chemical composition of the weld metal can be provided.
(4) High welding efficiency (compared to electrodes), suitable for automatic welding, semi-automatic welding or fully automatic welding.
(5) The welding utilization rate is high (compared to welding rods). The welding utilization rate of welding wires is far higher than that of electric welding rods. Under the same weight, welding wires are more cost-effective than welding rods.
Shortcoming
(1) The welding wire manufacturing process is complicated.
(2) Wire feeding is more difficult than solid welding wire, and a wire feeding mechanism that reduces the wire feeding pressure needs to be used.
(3) The surface of the welding wire is easy to rust, and the powder is easy to absorb moisture. Therefore, the storage of the welding wire needs to be strictly managed.
FCAW Welding Application
Flux cored arc welding can be used for both semi-automatic and automatic welding, but is usually used for semi-automatic welding. Using different welding wires and shielding gases, flat welding, overhead welding and all-position welding can be performed. Compared with ordinary gas metal arc welding, shorter wire extension length and larger welding current can be used. Compared with manual arc welding, fillet welding can produce welds with larger fillet sizes. This welding method is usually used to weld carbon steel, low-reference alloy steel, stainless steel and cast iron. Due to the above characteristics, this method is the most promising welding square heat method to replace ordinary hand arc welding to achieve automatic and semi-automatic welding when welding steel. The outer skin of the flux-cored welding wire is made of low carbon steel or low alloy steel. The pulse making process of the welding wire is to first roll the steel sheet (usually 08A) into a U-shaped section, and then limit the U-shaped steel strip of metered powder material into different shapes. The flux material is compacted and finally Fu Fen pretends to be Du Fen and starts to beat.
Flux-cored wire gas shielded welding uses ordinary gas as the shielding gas. Corresponding protective gas should be used during use.
Safe Operation Technology Of FCAW Welding
(1) During flux cored wire arc welding, the arc temperature is about &000-I 0000 `C, and the arc light radiation is stronger than that of manual arc welding, so protection should be strengthened.
(2) During flux-cored wire arc welding, there is a lot of spatter, especially thick wire welding (diameter greater than 1.6 mm), which also produces large particle spatter. Welders should have complete protective equipment to prevent human body burns.
(3) Carbon dioxide gas is lining the carbon dioxide gas from the arc height to the bottom of the container. When welding, ventilation should be strengthened. , there should be supervision outside the container.
(4) The voltage used by the carbon dioxide gas preheater should not be higher than 36V, and the shell should be reliably grounded. When the work is completed, immediately cut off the power and air supply.
(5) For a cylinder containing liquid carbon dioxide, the full cylinder pressure is about 0. 5MPa, but when it is subjected to external draining. Click to rise.
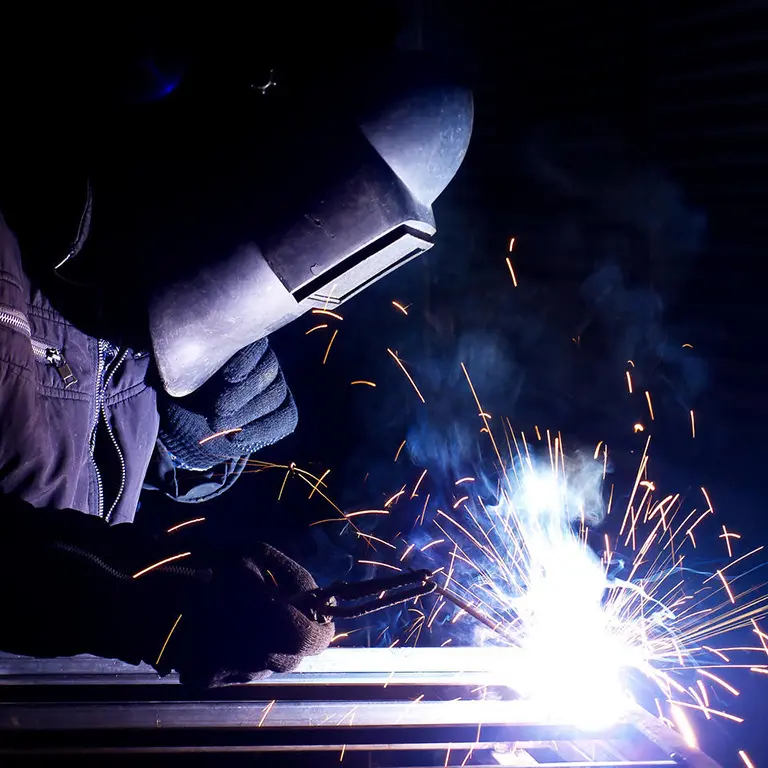
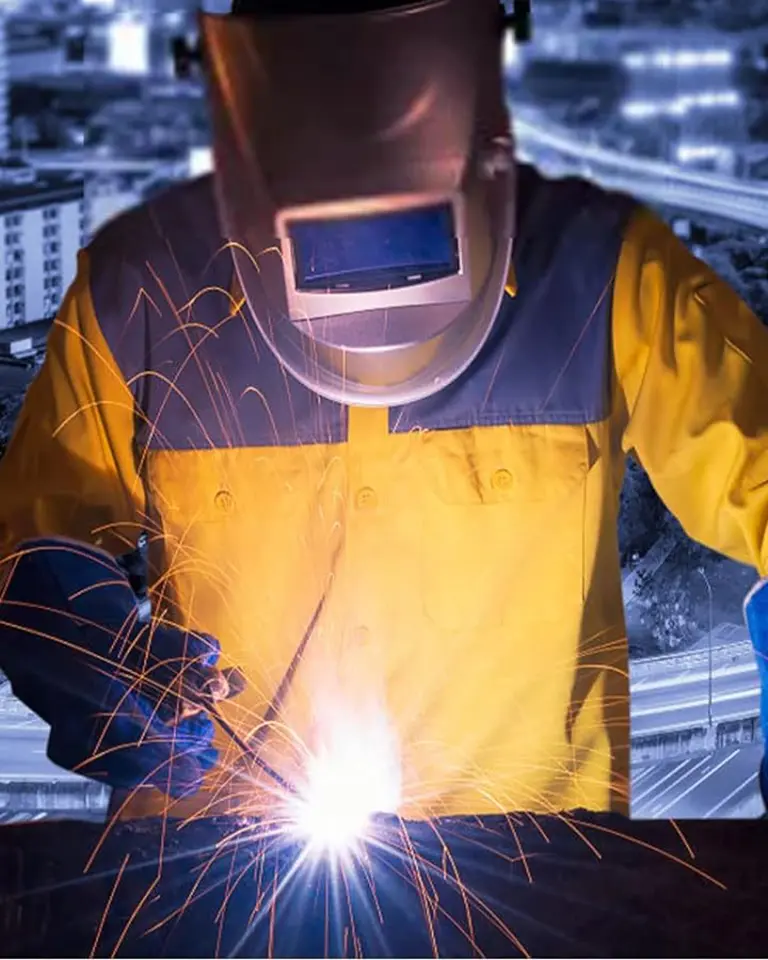
Articles you may be interested in:
Introduction To Welding Gloves
Detailed Explanation Of Spot Welding Process
Difference Between MIG And TIG Welding
How To Maintain And Maintain Welding Equipment
How Should Welders Protect Their Own Safety During Work?
Introduction to TIG welding and basic operating procedures
Advantages And Disadvantages Of Handheld Laser Welder
The Difference Between ARC Welding Machine and Electric Welding Machine
Primary wire, secondary wire, welding wire, ground wire, ground wire
How to distinguish between welding slag and molten iron during welding?
Welder skills and knowledge: What basic knowledge do beginners need to master?