Choice of different types of welding rods
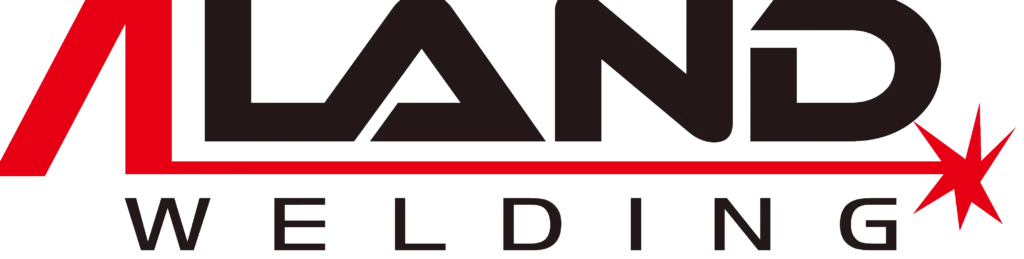
ALAND WELDING Let you feel the most sincere welding service
As a welding material, welding rod plays a vital role in industrial production and repair. It is not only used to connect various metal workpieces, but also widely used in construction, manufacturing, automobile industry and other fields. However, choosing the right welding rod is crucial to ensuring welding quality and efficiency. This article will discuss the types, selection methods and applications of welding rods in different industries to help readers better understand and choose suitable welding materials.
1. The choice of welding rod is not arbitrary. Choosing an inappropriate welding rod may lead to the following adverse consequences:
(1) Poor welding quality: Choosing an inappropriate welding rod may lead to a decrease in welding quality, such as uneven welds, pores, slag inclusions and other defects. This may affect the strength, sealing and corrosion resistance of the weldment, and may even lead to failure of the welded joint.
(2) Slow welding speed: An unsuitable welding rod may require longer welding time to achieve the required welding effect, thereby reducing welding efficiency. This may increase production costs in a large-scale production environment and affect production schedules.
(3) Difficulty in operation: Some types of welding rods may require higher welding technical requirements. If the operator’s technical level is not enough, it may cause problems during the welding process, such as unstable welding joints, unstable arcs, etc., thus affecting Welding quality.
(4) Environmental impact: Choosing inappropriate welding rods may be affected by the welding environment, such as the sensitivity of welding rods to moisture or wind and rain, which may lead to reduced welding quality or difficulty in operation.
(5) Increased cost: If the selected welding rods do not match the actual needs, it may lead to a decrease in welding quality, thereby increasing the cost of repair and re-welding. In addition, some high-performance welding rods are relatively expensive, which may increase unnecessary costs if they do not match actual needs.
2. Welding rods can be divided into many types according to their uses and welding materials. Here are some common types of welding rods:
(1) Carbon steel welding rod: Welding rod used for welding carbon steel workpieces, suitable for general welding work. According to specific needs, carbon steel welding rods can be divided into low carbon steel, medium carbon steel and high carbon steel welding rods.
(2) stainless steel welding rod: a welding rod used for welding stainless steel workpieces to ensure that the welded joint has good corrosion resistance. According to different stainless steel materials, stainless steel welding rods are also divided into different types.
(3) Aluminum welding rods: Welding rods specially used for welding aluminum and aluminum alloy workpieces. Due to the high thermal conductivity and strong oxidation of aluminum, aluminum welding is relatively difficult and special welding rods are required.
(4) Flux-cored electrode: The electrode contains a certain amount of welding additives or flux core, which can be released during the welding process to improve the welding effect and welding quality. Common flux-cored electrodes include steel flux-cored electrodes and aluminum flux-cored electrodes.
(5) Ferrite electrode: An electrode used for welding special materials such as low-temperature alloy steel and high-temperature alloy steel. It has good heat resistance and corrosion resistance.
(6) Low-temperature welding rod: used for welding low-melting-point metals or those that have little thermal impact on the workpiece, such as mild steel, copper, aluminum, etc.
(7) Special-purpose welding rods: For specific application requirements, there are also some special-purpose welding rods, such as wear-resistant welding rods, high-temperature-resistant welding rods, corrosion-resistant welding rods, etc.
3. Different types of welding rods are suitable for different industries and application scenarios, as follows:
(1) Carbon steel welding rod: suitable for a wide range of manufacturing, construction, automobile manufacturing and other fields. Carbon steel electrodes are commonly used to weld carbon steel structures, pipes, mechanical components, etc.
(2) stainless steel welding rod: mainly used in food processing, chemical equipment manufacturing, medical equipment and other fields that require high corrosion resistance. Stainless steel welding rod is often used to weld stainless steel pipes, containers, kitchen utensils, etc.
(3)aluminum welding rods: suitable for aerospace, automobile manufacturing, shipbuilding and other fields. Aluminum welding rods are commonly used to weld aluminum alloy structures, aircraft parts, automobile bodies, etc.
(4) Flux-cored welding rods: Mainly used in heavy machinery manufacturing, shipbuilding, building structures and other fields that require high strength and high quality welding.
(5) Ferrite welding rod: suitable for welding of special materials such as high-temperature alloy steel and low-temperature alloy steel, commonly used in aerospace, energy industries, etc.
(6) Low-temperature welding rod: mainly used for welding low melting point metals, suitable for special materials or occasions sensitive to heat effects, such as mild steel, copper, aluminum, etc.
(7) Special purpose welding rods: such as wear-resistant welding rods, high-temperature-resistant welding rods, corrosion-resistant welding rods, etc., which are used in corresponding industries according to different special needs, such as mining equipment manufacturing, refineries, chemical plants, etc.
4. The selection of welding rods has an important impact on welding quality and efficiency, so it is very important to choose the appropriate welding rods. The following are several key factors that influence the quality of welding rod selection:
(1) Applicable materials and welding requirements: When selecting welding rods, you must first consider the type of material to be welded and the required welding performance. Different welding rods are suitable for different types of materials and welding processes, and choosing the right welding rod can ensure welding quality and efficiency.
(2) Welding position and environment: Welding position and environment are also important considerations in selecting welding rods. In different welding positions and environments, welding rods with appropriate weather resistance, moisture resistance and other properties need to be selected to ensure welding quality.
(3) Welding operator skills: The skill level of the welding operator also affects the selection of welding rods. For welders with higher technical level, they can choose electrodes with better performance to achieve a higher level of welding quality; while for welders with lower technical level, they can choose electrodes that are easier to operate to improve welding efficiency and quality.
(4) Cost and economy: In addition to welding performance, the cost and economy of the welding rod are also one of the selection considerations. Generally speaking, high-performance welding rods tend to be more expensive, while some conventional welding rods may be more affordable. Therefore, a balance between performance and cost needs to be considered when selecting welding rods.
(5) Production volume and batch size: For mass production, welding efficiency and cost are more important, so it may be necessary to choose welding rods with high efficiency and low cost; while for small batch production or welding tasks with special requirements, more emphasis is placed on welding quality. and performance, you can choose higher performance welding rods.
To sum up, as an important welding material, welding rod plays an irreplaceable role in various industries. The correct selection of suitable welding rods can not only improve welding quality and efficiency, but also ensure the safety and reliability of welding work. In the future, with the continuous development of technology and changes in demand, the types and performance of welding rods will continue to be updated and improved, providing more choices and possibilities for welding work in all walks of life. Therefore, strengthening the understanding and research of welding rods will not only help improve the level of welding technology, but also promote the development and innovation of the welding industry.
Articles you may be interested in:
Stick Welding Concept And Process
WSME Welding Machine Introduction
Introduction To TIG Welding Machine
How To Choose A Suitable Wire Feeder
Pipeline Welding Detailed Introduction
Learn More About Resistance Welding
Arc Welding Machine Applicable Industry
Difference Between MIG And TIG Welding
The Importance Of Welding Torch Selection
Ac Dc Tig Welding Comparison Instructions
Basic Knowledge Of Welding Procedure Qualification