pipeline welding detailed introduction
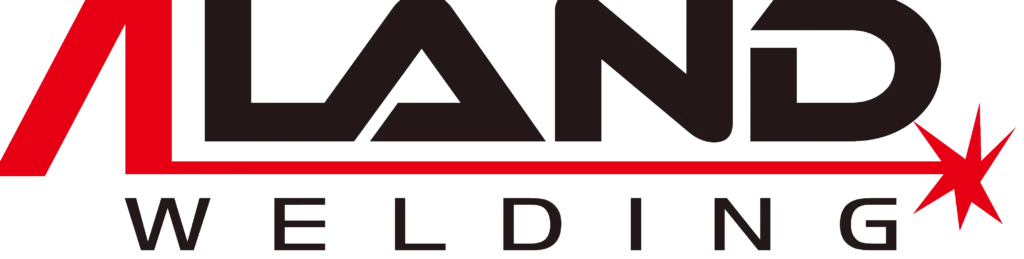
ALAND WELDING Let you feel the most sincere welding service
Pipelines are an integral part of modern industry and infrastructure, used to transport a variety of liquids, gases and other fluids. The connection of pipelines is one of the key links to ensure the safe and efficient operation of the entire system. In pipeline connections, welding technology plays an important role, and its quality directly affects the reliability and long-term operating costs of the pipeline system. This article will deeply explore the principles, applications and importance of pipeline welding technology in different industries, as well as current development trends and challenges.
Due to the increasing demand for infrastructure construction and industrial development, the employment prospects of pipeline welders are relatively good. There is a continuous demand for pipeline welding technology in construction, petrochemical, energy and other industries, so welders have high employment opportunities in these industries. Pipeline Welder’s career prospects after employment are also very good, and Pipeline Welder’s salary is also very generous.
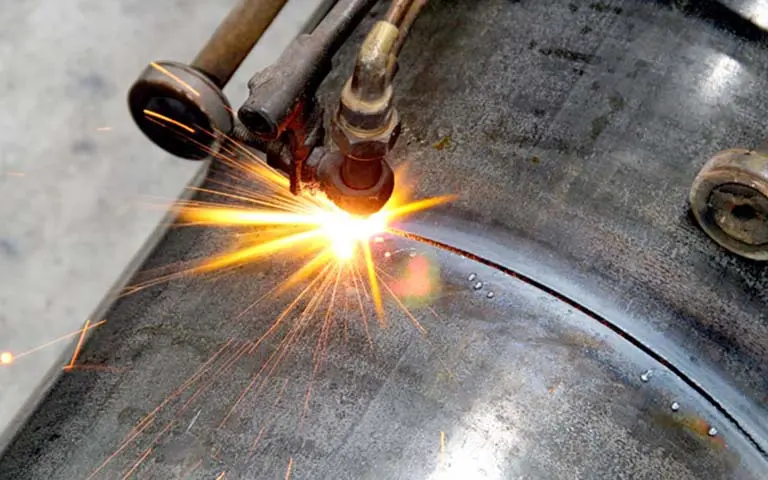
1. Welding method:
(1) Electric arc welding (SMAW): Also known as manual arc welding, it is a common pipe welding method. It uses the high temperature generated by the arc to melt the electrode and base material to form a weld.
(2) Gas shielded welding (GTAW/TIG): Use inert gas shielded welding, such as argon, to prevent the weld from being contaminated by oxygen in the air. TIG welding is usually used for pipes with higher butt welding process requirements.
(3) Plasma arc welding (PAW): Plasma arc welding is a high energy density welding method suitable for welding thicker pipe walls.
(4) Automatic welding: including automatic TIG welding, MIG/MAG welding and wire automatic submerged arc welding (SAW), usually used in large pipeline projects and automated production lines.
2. Preparation work:
Pipe surface cleaning: Remove grease, dirt and oxides to ensure good welding quality.
Pipe End Preparation: Pipe ends must be cut to the proper shape and ensure the ends are flat and free of cracks.
Prepare welding equipment: Prepare appropriate equipment according to the selected welding method, including welding machine, electrode, welding wire, gas shield, etc.
3. Welding process:
Welding parameter setting: Set appropriate welding current, voltage, electrode spacing and other parameters according to the pipe material, wall thickness and welding method.
Welding operation: Carry out welding operation according to the welding process requirements to ensure that the welding area is fully heated and a good weld is formed.
Filler material application: Filler material is added when needed to fill the voids in the weld and ensure the integrity and strength of the weld.
4. Quality control and inspection:
After welding is completed, visual inspection and dimensional measurement of the welds are performed to ensure that the welding quality meets standard requirements.
Non-destructive testing (NDT) such as radiographic testing (RT), ultrasonic testing (UT) and magnetic particle testing (MT) can be performed to detect welding defects and hidden dangers.
5. Post-welding treatment:
After welding is completed, clean the residue from the welding area and perform necessary surface treatment, such as grinding, rust removal and painting, to prevent corrosion and oxidation.
To sum up, pipeline welding technology, as a key link in pipeline connection, plays an irreplaceable role in the fields of industry, construction and infrastructure. With the continuous advancement of science and technology and changing market demands, pipeline welding technology is also constantly innovating and developing. However, there are still some challenges in application, such as welding quality control, increased automation, and the application of environmentally friendly materials. In the future, we look forward to further improving the quality and efficiency of pipeline welding technology through continued research and technological progress, and providing safer and more reliable pipeline systems for all walks of life.
Articles you may be interested in:
WSME Welding Machine Introduction
Safety Precautions When TIG Welding
Safety Precautions When MIG Welding
Introduction To TIG Welding Machine
Learn More About Resistance Welding
Arc Welding Machine Applicable Industry
Difference Between MIG And TIG Welding
A Must-read For Newbies: GTAW Welding
Ac Dc Tig Welding Comparison Instructions
Basic Knowledge Of Welding Procedure Qualification