stick welding concept and process
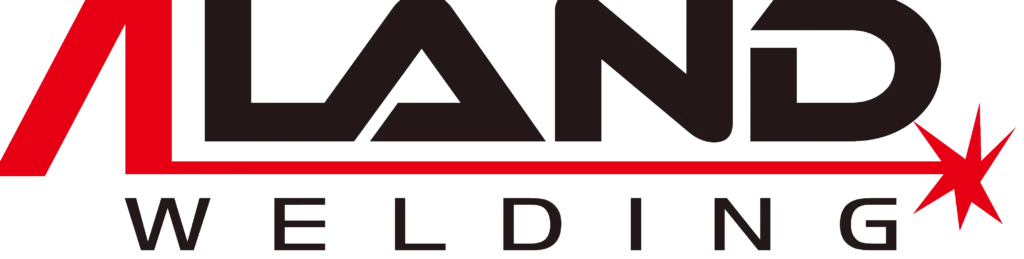
ALAND WELDING Let you feel the most sincere welding service
Welding is a vital process in modern industry and is widely used in manufacturing, construction and repair. As one of the oldest and most common welding methods, stick welding has always played a vital role. By utilizing an arc created by an electric current to heat metal and form a connection, manual arc welding provides engineers and welders with a flexible and efficient means of joining a variety of metal workpieces to create strong and durable structures. In this article, we will explore the principles, advantages, disadvantages and areas of application of stick welding, as well as how to ensure a high-quality welded connection during the welding process.
1. Thoughts on manual arc welding
Manual arc welding is a common welding method used to join metal parts together. In stick welding, a welding current is passed between two metal parts to create an arc and heat them to a temperature high enough to melt the metal. A welder uses welding material (usually a welding rod or wire) to fill the weld on a molten metal surface, creating a strong connection.
The basic principle of stick welding is to use an arc generated by an electric current to heat the metal, melt it, and then form a connection through the filler material. This method usually uses AC or DC power, and selects the appropriate welding current and voltage according to the welding materials and requirements. Manual arc welding is widely used to join various metal workpieces, including steel, aluminum and copper.
2. Advantages and disadvantages of manual arc welding
Advantage:
Wide Applicability: Manual arc welding is suitable for various types of metals, including steel, stainless steel, aluminum and copper, etc.
Simple equipment: Compared with other advanced welding methods, the equipment required for stick welding is relatively simple, including welding machines, electrodes, welding masks and welding gloves.
Low cost: Compared to other welding methods, the equipment and material costs of manual arc welding are relatively low, making it the preferred welding method for many industries and individuals.
Adaptable: Manual arc welding is able to handle thicker metal workpieces and complex welding positions, making it useful in a variety of environments.
Proficiency can be improved: Although stick welding requires certain skills and experience, welders can continuously improve their proficiency and skill level through practice.
Shortcoming:
Welding quality is affected by skills: The welding quality of stick welding is greatly affected by the welder’s skills and experience. Improper operation may lead to unstable welding quality or defects.
Slow welding speed: Compared with other automated or semi-automatic welding methods, stick welding has a slower welding speed and takes longer to complete the welding task.
Problems with welding slag and bubbles: During the manual arc welding process, the generation of welding slag and bubbles is a common problem, and if not paid attention to, it may lead to a decrease in welding quality.
Not suitable for high-precision welding: For applications requiring high-precision welding, manual arc welding may not provide sufficient accuracy and control, requiring the use of other, more advanced welding methods.
Manual and labor-intensive: Manual arc welding relies on manual operations and requires welders to spend a lot of time and labor to complete the welding task, so it may not be suitable for mass production.
3. Manual arc welding process
(1) Preparation work:
Check the work area: Make sure the work area is dry, well ventilated, and away from flammable materials.
Prepare the metal surface: Use a wire brush or grinding wheel to clean the surface of the workpiece to remove grease, oxides and other impurities.
Safety Measures: Wear appropriate personal protective equipment such as welding mask, gloves, fire-resistant clothing and safety shoes.
(2) Select welding equipment and materials:
According to the material and thickness of the welding workpiece, select the appropriate welding equipment (AC or DC) and welding materials (welding rod or wire).
Ensure that the welding equipment meets the power requirements of the work environment and has the necessary safety certifications.
(3) Prepare welding equipment:
Check the welding equipment: Make sure the welding machine cables and connectors are not damaged and that the electrode clamp and ground clamp are well connected.
Adjust welding parameters: adjust welding current, voltage and welding polarity according to welding material and thickness.
(4) Prepare welding materials:
Welding rod preparation: Select the appropriate diameter of the welding rod as needed, and check whether there is damage or oxidation on the surface of the welding rod.
Welding wire preparation: Set the wire supply device and the wire supply speed of the welding gun according to the diameter and type of the welding wire.
(5) Ignition arc:
Make sure the welding location is clean and dry to avoid affecting arc ignition.
Using an arc igniter or manual method, lightly contact the electrode with the surface of the workpiece and quickly separate it to generate an arc.
(6) Start welding:
Maintain proper welding position and welding angle to ensure good welding quality and operability.
Control the arc length and movement speed to adapt to the melting and filling of welding materials.
(7) Filling welding materials:
Under the arc, slowly move the end of the welding rod or wire to the weld, wait for it to melt, and then gently twist your wrist to control the supply of filler material.
Make sure the filler material covers the entire weld evenly to avoid bubbles or defects.
(8) Control the welding process:
According to the welding material and workpiece thickness, the welding current and voltage are adjusted to ensure a stable welding process.
Continuously monitor welding quality and welding position, and adjust welding parameters in time to deal with any problems.
(9) Complete welding:
After completing the welding, allow the welding location to cool to room temperature and inspect the appearance and quality of the weld, including weld strength, uniformity, and appearance.
If necessary, carry out subsequent processing such as grinding, welding slag removal and cleaning.
(10)Cleaning and maintenance:
Turn off the welding equipment and clean the work area to ensure safe disposal of welding residues.
Regularly inspect and maintain welding equipment, including cleaning, replacing worn parts and calibrating welding parameters.
To sum up, manual arc welding, as an ancient and classic welding method, still maintains its unique status despite many competitors in modern welding technology. Its wide applicability, relatively low cost, and reliability in a variety of environmental conditions make it the first choice in many industries. However, as technology continues to advance, we are also seeing the rise of automated and mechanized welding technologies that may replace manual arc welding in some areas. Despite this, manual arc welding remains an indispensable welding process, and its exquisite skills and traditional charm will continue to play an important role in future welding practices.
Articles you may be interested in:
WSME Welding Machine Introduction
Safety Precautions When TIG Welding
Safety Precautions When MIG Welding
Introduction To TIG Welding Machine
Pipeline Welding Detailed Introduction
Learn More About Resistance Welding
Arc Welding Machine Applicable Industry
Difference Between MIG And TIG Welding
A Must-read For Newbies: GTAW Welding
Ac Dc Tig Welding Comparison Instructions
Basic Knowledge Of Welding Procedure Qualification