Introduction to welding pad process
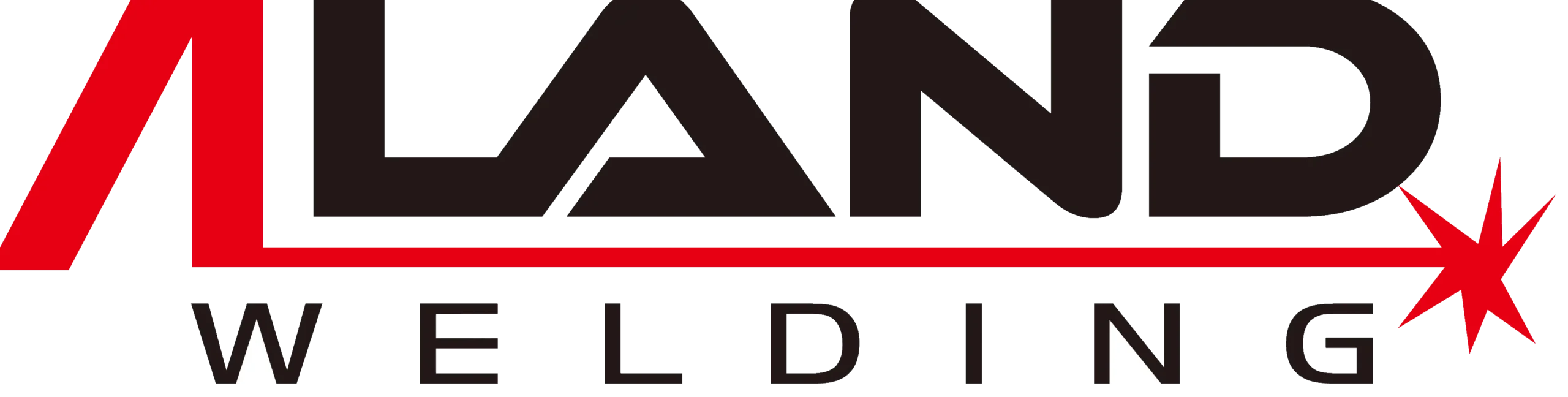
ALAND WELDING Let you feel the most sincere welding service
In modern welding processes, welding backing play a vital role. They not only provide support and protection for the welding area, but also adjust the weld gap and ensure welding quality. Welded Ceramic Liner and fiberglass liner are common welding auxiliary materials, each with unique characteristics and applicable scenarios. This article will explore the characteristics of these two gaskets and their application in the welding process.
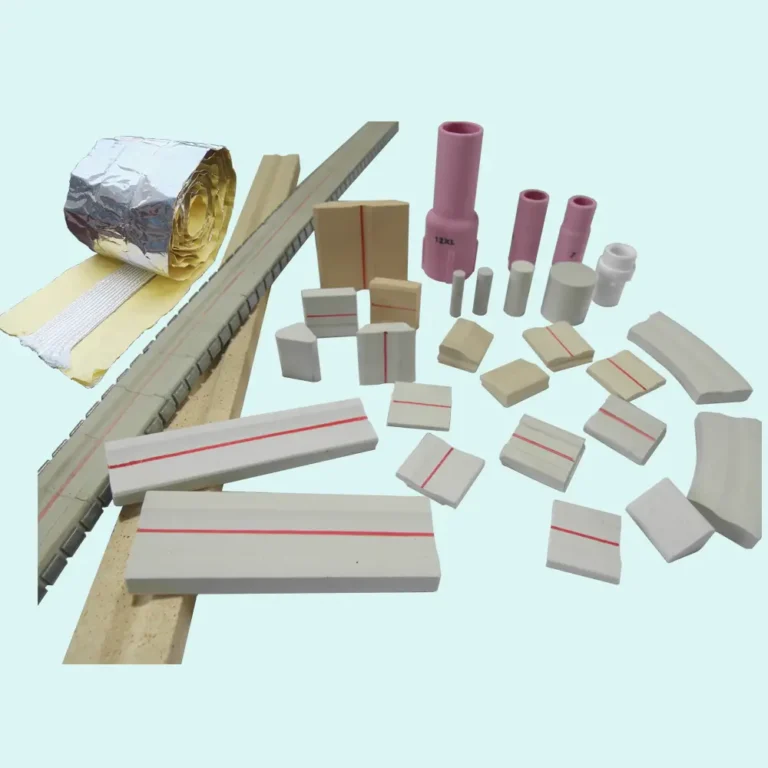
1. Common welding backing
Welding backing usually refers to the material used to support the workpiece, adjust the weld gap, or protect the welding area during the welding process. These pads can be made in a variety of shapes and materials, depending on the specific welding application. Here are some common types of welding backing:
(1)Metal gasket: Usually made of metal materials such as steel, aluminum, etc., it is used to support and fix the welding workpiece to maintain the correct position and gap of the weld.
(2)Welded Ceramic Liner: These welding backing are usually made of ceramic materials and have high temperature resistance and corrosion resistance. They are used to protect the welding area from welding slag, gases or spatter, and can provide additional protection for certain special welding processes (such as TIG welding).
(3) Fiberglass liner: These welding backing are often used to support welding workpieces, and due to their high temperature tolerance and mechanical strength, are also used as thermal insulation layers in some cases to prevent heat transfer to areas where welding is not required.
(4) Adhesive liner: This type of liner is usually applied or coated with a layer of adhesive in the welding area to protect the surrounding area from sputtering, gas, etc.
(5) Silicone gaskets: Silicone gaskets are often used in special welding applications, such as for microscopic components that require highly precise welding. Silicone gaskets can provide soft support and reduce vibration.
2. Introduction of Welded Ceramic Liner
Welded Ceramic Liner is an auxiliary material commonly used in the welding process. It is mainly used to protect the welding area, provide heat insulation and isolation functions, and has high temperature resistance and corrosion resistance. The following is a detailed introduction to Welded Ceramic Liner:
(1) Material characteristics: Welded Ceramic Liner is usually made of ceramic materials such as Alumina or Zirconia. These materials have excellent high temperature resistance, mechanical strength and chemical stability, allowing them to maintain stable performance over time during high temperature welding processes.
(2) Application scope: Welded Ceramic Liner is widely used in various welding processes, especially for welding processes that require high temperature and high precision, such as TIG welding, plasma arc welding, etc. They can be used to support and secure welding workpieces while providing protection and isolation.
(3) Protection function: During the welding process, Welded Ceramic Liner can effectively protect the welding area from gas, sputter, spatter and heat. They prevent welding slag, gases and spatter from entering the weld or surrounding area, ensuring welding quality and stability.
(4) Thermal insulation function: Since ceramic materials have good thermal insulation properties, Welded Ceramic Liner can effectively isolate the heat conduction in the welding area and surrounding areas, preventing heat from spreading to parts that do not need to be welded, thereby reducing thermal deformation and damage.
(5) Shape and size: Welded Ceramic Liner can be made into various shapes and sizes according to specific welding requirements, such as square, round, rectangular, etc. They usually have flat surfaces and precise dimensions to ensure stability and precision during welding.
3. Introduction to fiberglass liner
Fiberglass liner is a common welding auxiliary material. It is mainly used to support and protect the welding area, isolate heat and prevent the impact of spatter on the surrounding area. The following is a detailed introduction to fiberglass liner:
(1) Material characteristics: fiberglass liner is usually made of fiberglass cloth or fiberglass felt. Glass fiber has excellent properties such as high strength, high temperature resistance, and corrosion resistance, and can withstand high temperatures and mechanical stress during the welding process.
(2) Application scope: fiberglass liner is widely used in various welding processes, especially for welding processes that require heat insulation and isolation functions. They are often used to support and protect the welding workpiece during the welding process to prevent heat from being conducted to parts that do not need to be welded.
(3) Protection function: During the welding process, fiberglass liner can effectively protect the welding area from the impact of sputter, splash, gas, etc. on the surrounding area. They prevent welding slag and spatter from entering the weld or surrounding areas, ensuring welding quality and safety.
(4) Heat insulation function: Glass fiber has good heat insulation properties, so fiberglass liner can effectively isolate the heat conduction in the welding area and surrounding areas, prevent heat from spreading to parts that do not need to be welded, thereby reducing thermal deformation and damage.
(5) Shape and size: fiberglass liner can be made into various shapes and sizes according to specific welding requirements, such as cloth, felt, etc. They are usually soft in nature, able to adapt to different shapes of welding workpieces, and provide good support and protection.
4. Applicable scenarios for lining
Welded Ceramic Liner and fiberglass liner are common welding auxiliary materials, and they have their own applicability in different scenarios. The following are the scenarios in which they are applicable:
(1) Scenarios for Welded Ceramic Liner:
High-temperature welding: Welded Ceramic Liner has good high-temperature tolerance, so it is particularly suitable for scenarios that require welding in high-temperature environments, such as TIG welding, plasma arc welding, etc.
Precision welding: Because the Welded Ceramic Liner has a flat surface and precise dimensions, it is suitable for scenarios that require high welding accuracy, such as micro welding, welding of precision parts, etc.
Corrosive environment: Ceramic materials have good chemical stability and can be used in corrosive gas or liquid environments, so they are suitable for scenes that require welding in corrosive environments.
Welding support: Welded Ceramic Liner usually has high mechanical strength and can provide good support, and is suitable for scenarios where welding workpieces need to be supported and fixed.
(2) Scenarios where fiberglass liner is applicable:
Thermal insulation protection: Glass fiber has good thermal insulation properties, so it is suitable for scenes that require thermal insulation protection during the welding process, and can prevent heat from being conducted to parts that do not need to be welded.
Soft support: Fiberglass liner usually has soft characteristics, can adapt to different shapes of welding workpieces, and provides good support and protection, so it is suitable for scenes that require soft support.
Lightweight applications: fiberglass liner is generally lighter than Welded Ceramic Liner, so it is suitable for scenarios that require lower weight of welding equipment.
Single-use: Fiberglass liners are generally less expensive and suitable for one-time or small-scale use, such as in special welding tasks or temporary repairs.
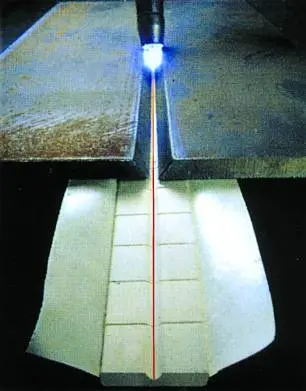

All in all, Welded Ceramic Liner and fiberglass liner are important auxiliary materials in the welding process, each with unique characteristics and applicable scenarios. Proper selection and use of these pads can improve weld quality, protect the workpiece and ensure operator safety. Therefore, in practical applications, it is crucial to select the appropriate gasket based on specific welding requirements and environmental conditions. We hope that this article can provide useful information to readers and encourage more people who are interested in the welding process to deepen their understanding and research in this field.
Articles you may be interested in:
Stick Welding Concept And Process
WSME Welding Machine Introduction
Introduction To TIG Welding Machine
Learn More About Resistance Welding
How To Choose Industrial Water Chiller
Arc Welding Machine Applicable Industry
Difference Between MIG And TIG Welding
Choice Of Different Types Of Welding Rods
The Importance Of Welding Torch Selection
Ac Dc Tig Welding Comparison Instructions
Introduction To Common Welding Techniques
Basic Knowledge Of Welding Procedure Qualification