MMA welding machine introduction and process
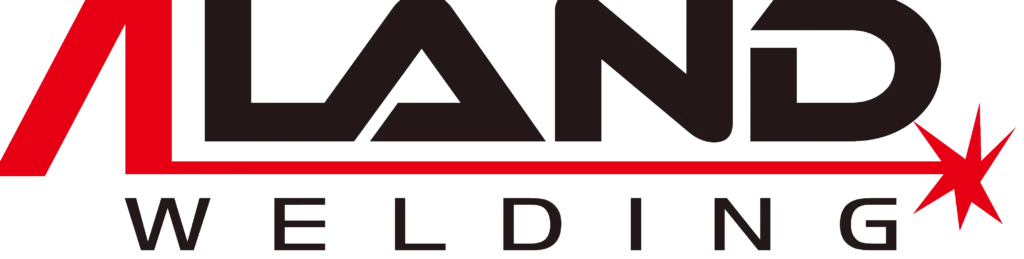
ALAND WELDING Let you feel the most sincere welding service
Manual arc welding is a welding method widely used in the metal processing and manufacturing industries. It uses an electric arc to heat and melt the electrode and the surface of the workpiece to form a strong welded joint. In modern industry, manual arc welding technology has become an integral part, used to join and repair various metal workpieces, everywhere from shipbuilding to building structures. However, it is not easy to obtain high wages in this field. It requires certain professional skills and experience, as well as the motivation to continuously learn and improve.
1. What is MMA Welding
Manual arc welding (MMA), also known as rod welding, refers to a welding method that uses a filler rod in a welding clamp as the electrode. The arc burns between the filler rod and the workpiece. The difference from other welding methods is that the filler rod used as the welding rod in MMA welding shortens as the welding progresses. In TIG and GMA welding, the distance between the welding gun and the workpiece must always remain constant. But in MMA welding, the welding gun must constantly move toward the workpiece to ensure that the distance between the electrode and the molten weld remains constant. This creates special challenges for MMA welding.
2. MMA welding method
MMA welding has a variety of different welding techniques, each suitable for specific welding needs and workpiece shapes. The following are common MMA welding techniques:
(1) Flat position:
This is one of the most common welding methods and is suitable for welding on horizontal workpiece surfaces.
The angle between the welding rod and the workpiece should be kept horizontal, and the moving direction of the welding gun should be parallel to the welding line.
(2)Vertical Position:
The angle between the welding rod and the workpiece remains vertical, and the welding gun moves from bottom to top or from top to bottom.
This method is suitable for welding vertical surfaces or steeper workpiece surfaces.
(3)Horizontal Position:
The angle between the welding rod and the workpiece remains horizontal, and the moving direction of the welding gun is perpendicular to the welding line.
Typically used for welding horizontal joints on horizontal surfaces or transverse welding.
(4) Overhead position:
The angle between the welding rod and the workpiece is kept upward, and the welding gun moves downward.
Suitable for welding workpiece surfaces that are above, such as ceilings or floors.
(5)Vertical Up Position:
The angle between the welding rod and the workpiece remains vertical, and the welding gun moves from bottom to top.
This technique is also used for welding vertical surfaces, but the welding speed is usually slower to ensure that the weld is fully filled.
(6)Joint Position:
The angle between the welding rod and the workpiece is between horizontal and vertical, and the moving direction of the welding gun moves along the angle of the welding line.
This method is suitable for welding joints at various angles and positions.
(7) Circular Position:
The welding gun moves in a circle or curve and is used to weld ring-shaped workpieces or curved joints.
This method requires welding tools to have a high technical level to maintain the welding speed and the consistency of the welding lines.
(8) Repeated welding (Backhand Position) and forward welding (Forehand Position):
In flat welding, longitudinal welding and horizontal welding, the angle and movement direction of the welding gun can be backhand (the side moving away from the welding seam) and forehand (the side moving closer to the welding seam) respectively.
Repeated welding is more suitable for welding narrow gaps, while forward welding is more suitable for filling wider welds.
3. MMA welding process
(1) Preparation work:
Clean the work area: Remove debris from the work area, ensure the floor is clean and level, and remove flammable items.
Ventilation and protection: Ensure there is good ventilation in the work area and wear personal protective equipment, including welding masks, heat-resistant gloves, fire-resistant clothing and safety shoes.
Check the equipment: Check whether the power cord, welding fixture and grounding wire of the welding machine are intact, and make sure the power switch is turned off.
(2) Select welding materials:
Select the appropriate welding material (welding rod) based on the material type and thickness of the workpiece.
Consult the welding manual or consult a professional to select welding materials that match the workpiece material.
(3) Set welding parameters:
According to the material and thickness of the welding workpiece, adjust the current intensity and arc length of the welding machine.
Use the parameters provided in the welding manual as a reference and make fine adjustments according to the actual situation.
(4) Prepare the welding surface:
Use a steel brush or grinding wheel to clean the surface of the workpiece to remove grease, oxides and other impurities.
Make sure there is no residual paint or plating around the welding area to avoid affecting the welding quality.
(5) Install and prepare welding rods:
Insert the electrode into the electrode clamp and be sure to clamp the clamp to secure the electrode.
Leave about 2-3 mm of the end of the electrode exposed outside the fixture to facilitate ignition.
(6) Ignition and welding:
Turn on the welder and light the end of the electrode with a lighter or match.
Lightly touch the electrode to the surface of the workpiece to ignite the arc and start welding.
Maintain an appropriate arc length (usually 2-4 mm) and a stable welding speed.
(7)Welding skills:
Maintain a stable welding speed and welding gun angle so that the weld seam is filled evenly.
When moving the welding rod, maintain constant contact with the workpiece to ensure welding quality.
Avoid shaking or moving the electrode too quickly during welding to avoid uneven welds or pores.
(8) Observe and adjust:
Carefully observe the arc stability and weld quality during the welding process and make adjustments as necessary.
If you need to adjust the welding parameters, you can gradually increase or decrease the current intensity, or adjust the welding angle between the electrode and the workpiece.
(9) Post-weld treatment:
After welding is completed, turn off the power of the welder and wait for the weld to cool.
Use appropriate tools to clean the welding area to remove welding slag and residual welding rod.
If necessary, perform subsequent surface treatments such as grinding, polishing or plating to improve the appearance and corrosion resistance of the welded joint.
(10) Safety precautions:
When operating, always keep the welding area dry and well-ventilated to reduce harmful gases and fumes from welding.
Avoid welding near flammable materials or gases, and make sure nothing flammable is around.
Use appropriate welding gloves and a face shield to protect your eyes, skin and respiratory system from the heat and spatter generated by welding.
4. Salary of MMA welder
When it comes to skills in the manual arc welding field that command high wages, here are some more detailed explanations:
(1) Complex structure welding technology:
For welding workpieces with complex structures, such as pipes, specially shaped parts or thick plates, a high level of welding technology is required. This includes being proficient in welding workpieces of different materials and thicknesses, accurately adjusting welding parameters to suit different situations, and using appropriate welding techniques and techniques to ensure the quality and strength of welds.
For the welding tasks of these complex structures, welding tools usually require a high technical level and rich experience, so they can earn higher wages.
(2) High-end welding process:
High-end welding processes such as TIG (Tig Welding) and MIG/MAG (Gas Shielded Welding) are usually used in industries with high requirements on welding quality and appearance, such as aerospace, automobile manufacturing, etc. These processes require welding tools to have a high technical level and rich experience, and to be able to achieve high-quality welding under complex process conditions, so they can usually earn high wages.
In addition to technical level, proficiency and safety awareness in operating these equipment are also required, which is also one of the important factors in obtaining high wages.
(3)Welding monitoring and quality control:
Understand welding monitoring technology and quality control methods, be able to monitor parameters in the welding process in real time, and perform data analysis and quality assessment to ensure the stability of the welding process and welding quality.
This requires some engineering knowledge and data analysis capabilities, usually relevant professional background or training, and a deep understanding of the welding process and welding materials. Therefore, these skills are also one of the key factors in being able to obtain high wages.
(4) Special material welding:
Understand and be proficient in welding techniques for special materials, such as stainless steel, aluminum alloys, nickel alloys, etc. Welding tasks involving these materials will usually receive higher wages.
The welding of these materials is usually highly technically difficult and requires welding tools with deep expertise and extensive experience to ensure welding quality and integrity. Therefore, these skills are also one of the important factors in obtaining high wages.
Therefore, in the field of manual arc welding, welding tools not only need to have solid welding technology and rich practical experience, but also need to continuously learn and improve, and continue to pursue technological innovation and breakthroughs. By mastering advanced welding technology and processes, accumulating rich industry experience, obtaining relevant certifications and qualifications, and establishing good work performance and interpersonal relationships, you can obtain high wages and career development opportunities in the field of manual arc welding.
Articles you may be interested in:
Introduction To Welding Pad Process
How To Choose A Suitable Wire Feeder
Stick Welding Concept And Process
WSME Welding Machine Introduction
Introduction To TIG Welding Machine
Learn More About Resistance Welding
How To Choose Industrial Water Chiller
Arc Welding Machine Applicable Industry
Difference Between MIG And TIG Welding
Choice Of Different Types Of Welding Rods
The Importance Of Welding Torch Selection
Introduction To Common Welding Techniques