difference between mig and tig welding
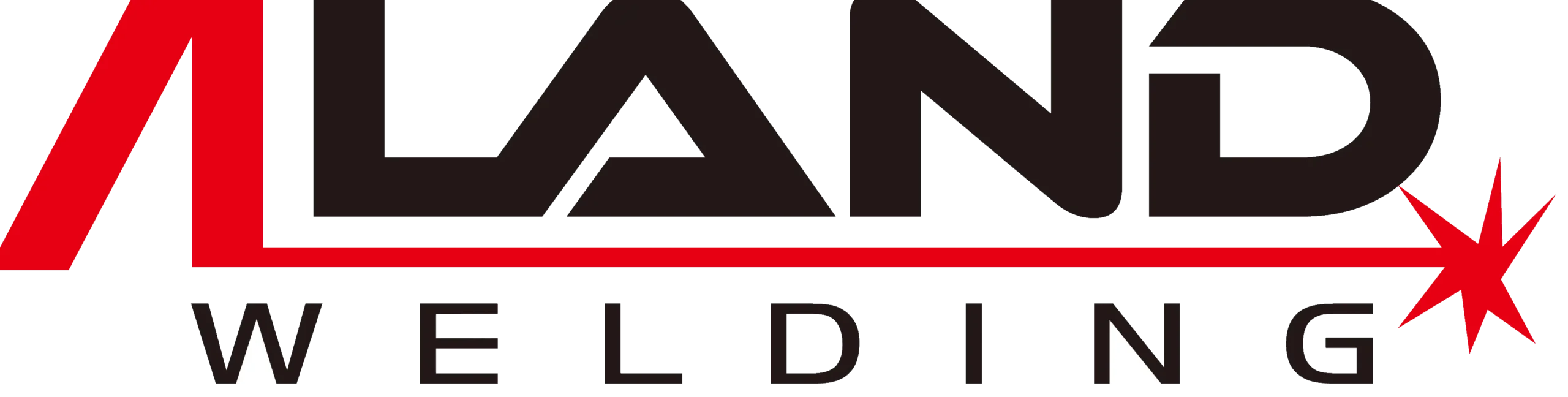
ALAND WELDING Let you feel the most sincere welding service
Difference between mig and tig welding: TIG welding
TIG (Tungsten Inert Gas) welding” stands for “inert gas welding.” This is an arc welding that does not spatter sparks and supports the welding of various metals such as stainless steel, aluminum, and iron. It uses tungsten that is not consumed as a discharge electrode. Inert gases such as argon and helium are used as protective gases. An arc is generated in the inert gas, and the base metal is melted by the heat of the arc for welding. Although welding consumables are also used, since the welding part is surrounded by inert gas, the arc is also Very stable with almost no sputtering.
.webp)
A. Protective gas
B. Tungsten electrode
C. Argon gas
D. Arc
E. Welding metal
F. Molten pool
G. Welding rod
Semi-automatic equipment for TIG welding consists of a welding power source, a welding torch, a liquefied gas bottle, a gas flow regulator, etc. When using a water-cooled welding torch or wire-shaped welding consumables, different necessary equipment needs to be added. In addition, since the polarity of the current (positive/negative) needs to be selected based on the base material, the welding power source must be equipped with a device that can select the polarity based on the base metal.
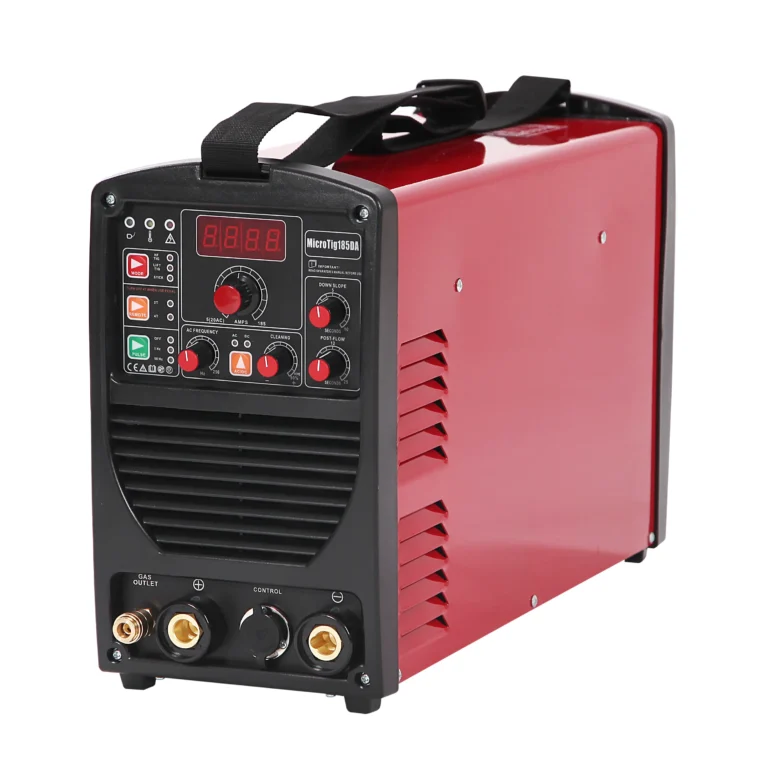
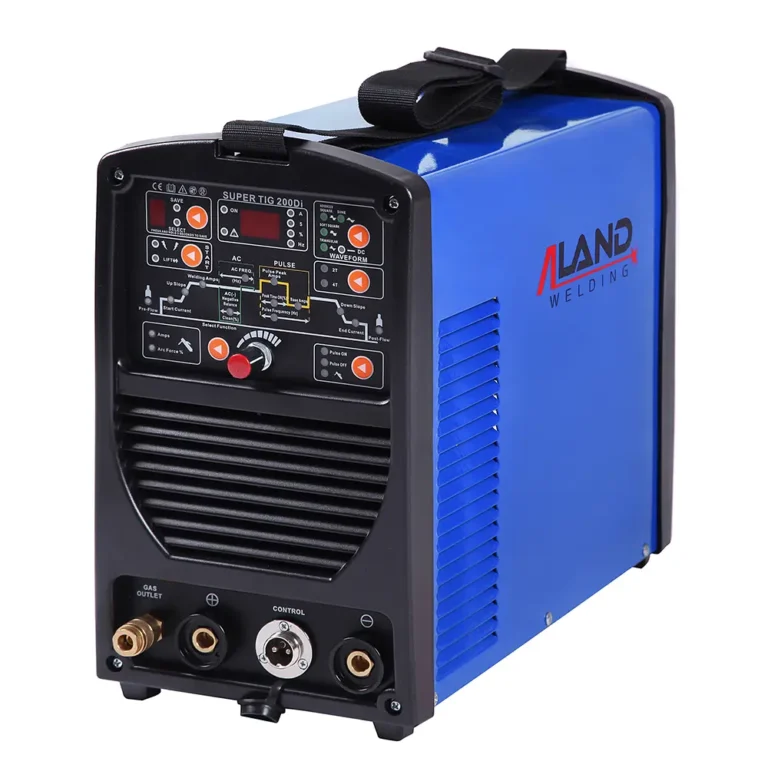
.webp)
A. Liquefied gas cylinder
B. Welding power source
C. Remote control box
D. Welding torch
There are many types of TIG welding, and different types can be distinguished according to AC/DC classification, presence or absence of pulses, presence or absence of welding wire, etc.
Depending on the type of base material, select AC/DC. The presence or absence of pulses can be selected, and welding using pulses is called “pulse TIG welding“. In the pulse TIG welding method, the welding current is changed into pulse current and basic current in a certain period. The base metal is melted during the application of the pulse current and cooled during the application of the base current. This method can periodically form melting points to form a bead-like weld.
.webp)
When using welding wire, it can be divided into “cold wire method” and “hot wire method”. The cold wire method is a method that uses conventional welding materials. The hot wire method releases current and heats the wire in advance, which can increase the amount of deposition per unit time. The hot wire method can deposit about three times the amount of welding material as the cold wire method, achieving rapid welding in a short time. Although TIG welding can achieve high-quality welding, it takes a long time to obtain the necessary amount of welding material for deposition. The hot wire method can make up for this shortcoming.
.webp)
Difference between mig and tig welding: MIG welding
“MIG (Metal Inert Gas) welding” belongs to arc welding. Like TIG welding, inert gas is used as a protective gas, but MIG welding is an electrode consumption welding method that melts the discharge electrode.
It is usually used for joining stainless steel and aluminum alloys, and the shielding gas can be used according to the welding materials.
The electrode uses iron wire-like welding wire. The welding wire will be rolled into a coil shape and installed into the welding wire supply device. The electric motor drives the transfer roller to automatically transfer the welding wire to the top of the welding torch. The operation of energizing the welding wire will be carried out when the contact piece passes. The arc generated between the welding wire and the base metal melts the welding wire and the base metal while welding. At this time, the equipment will supply protective gas around the welding part through the nozzle to isolate the arc, molten material and the atmosphere.
.webp)
A. Ar or Ar+2%O₂ gas
B. Solid wire electrode
Semi-automatic equipment for MIG welding consists of a welding power source, a welding wire supply device, a welding torch, and a liquefied gas cylinder. Its structure is basically the same as the MAG welding machine, but compared with the MAG welding machine, the welding wire supply device has been improved. Since MIG welding is mostly used for aluminum welding, the wire supply unit has been equipped with a design that can stably supply soft aluminum wire (4-axis method).
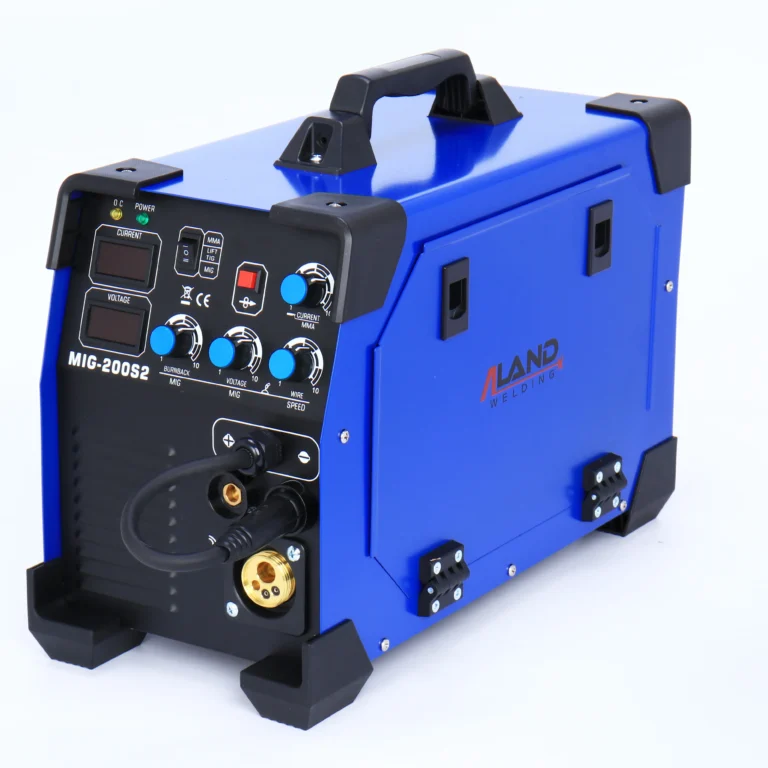
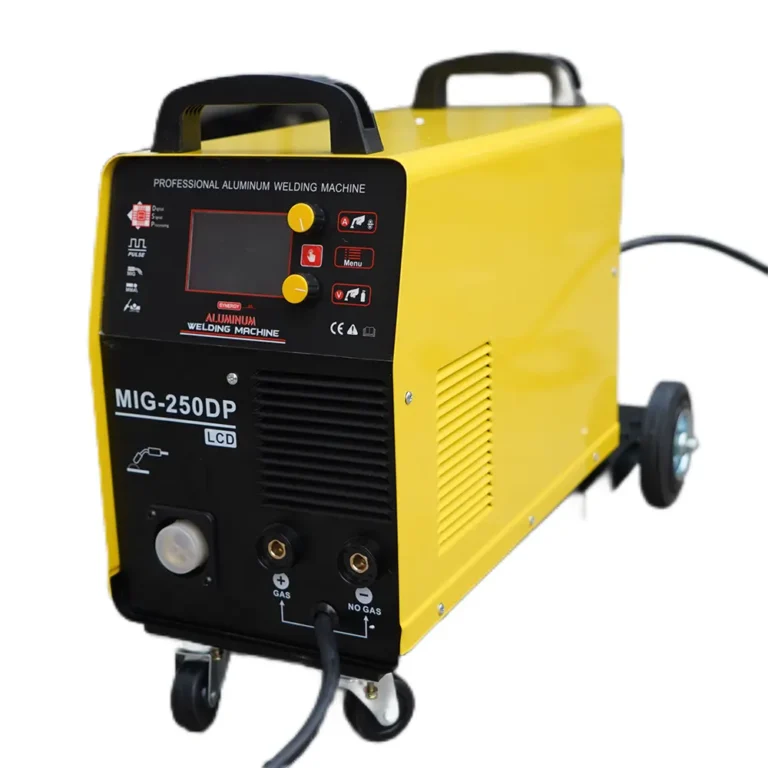
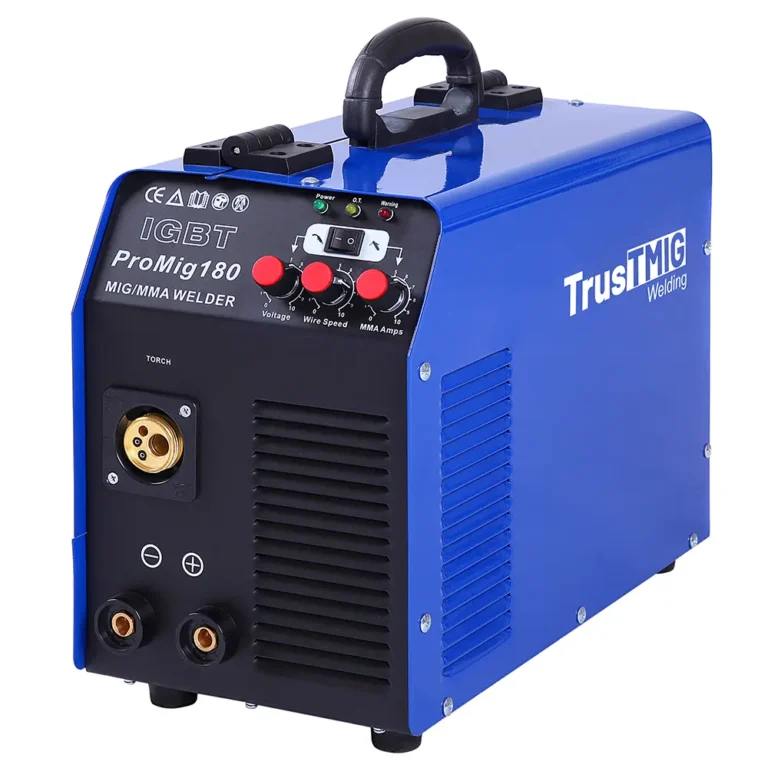
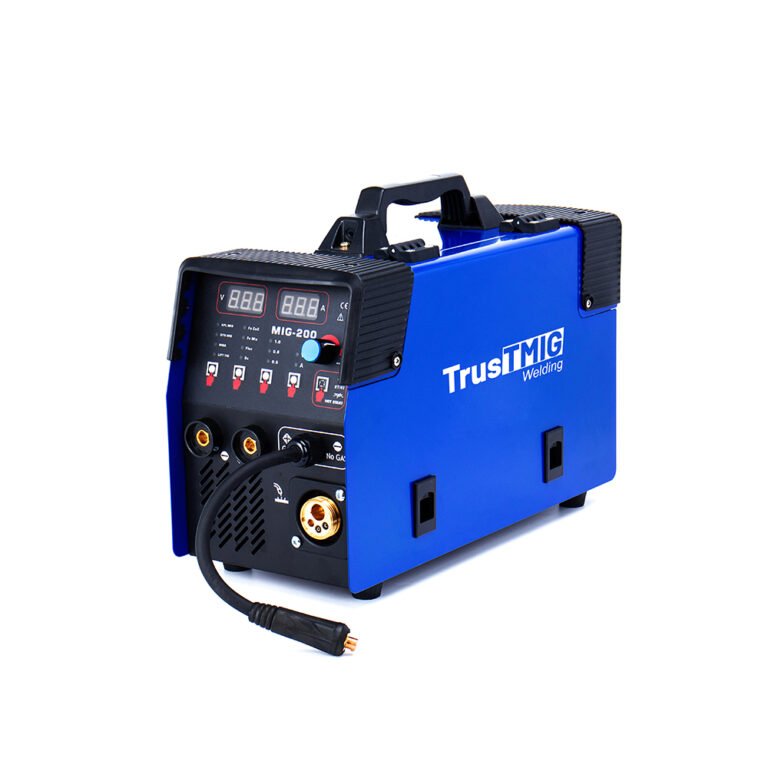
.webp)
A. Liquefied gas cylinder
B. Gas flow regulator
C. Welding power source
D. Welding wire supply device
E. Remote control box
F. Welding torch
MIG welding can also be classified according to AC/DC type, and the presence or absence of pulses.
Classification of MIG welding
.webp)
AC/DC composite pulse MIG welding method
“Short-circuit arc MIG welding” is a welding method that utilizes the phenomenon of short-circuit transition (short-circuit arc). Since there are many semi-automatic weldings, the heat transmitted to the base material is low, so it is suitable for thin plate materials. MAG welding’s short-circuit arc welding is often used to weld medium-thick plates with complex structures. When MIG welding is used to weld medium-thick plates, pulse MIG welding is commonly used.
“Spray MIG welding” is a welding method that sets the welding current above the critical current and increases the arc voltage. MIG welding method that utilizes the “spray transfer phenomenon” where the welding material is melted and atomized to join. When welding aluminum, if welding is performed without sputtering, welding defects such as poor fusion may occur. At this time, the arc voltage can be slightly reduced and welded in a tiny spray transition state. However, since the popularization of the “pulse MIG welding method” that can cover welding of thin to medium-thick plates, the spray MIG welding method has become less commonly used.
.webp)
“High current MIG welding method” uses thick diameter (diameter about 3.2 mm to 5.6 mm) welding wire for welding. The welding device uses a welding torch equipped with dual shielding gas nozzles and a power supply with steady-current characteristics with a rated output current of approximately 1,000 A.
“DC” and “pulse” MIG welding methods are also called “traditional pulse MIG welding methods”. The basic principle is the same as the pulse MAG welding method. A welding method that alternately outputs a basic small current that maintains the arc and a pulse current above the critical current to ensure that even when the average current is lower than the critical current, the welding wire droplets can be atomized. Able to perform efficient and high-quality welding of plates including thin and thick plates.
“Low frequency overlapping pulse welding method” was developed based on the pulse MIG welding method for the purpose of high value-added welding of aluminum. Because it can produce beautiful fish-scale welds, it is often used for welding thin aluminum plates on cars and motorcycles.
Articles you may be interested in:
Detailed Explanation Of Spot Welding Process
Why choose TIG welding? 4 major benefits
How To Maintain And Maintain Welding Equipment
How Should Welders Protect Their Own Safety During Work?
Introduction to TIG welding and basic operating procedures
Advantages And Disadvantages Of Handheld Laser Welder
The Difference Between ARC Welding Machine and Electric Welding Machine
Primary wire, secondary wire, welding wire, ground wire, ground wire
How to distinguish between welding slag and molten iron during welding?
Welder skills and knowledge: What basic knowledge do beginners need to master?