Introduction to welding machine wire feeder
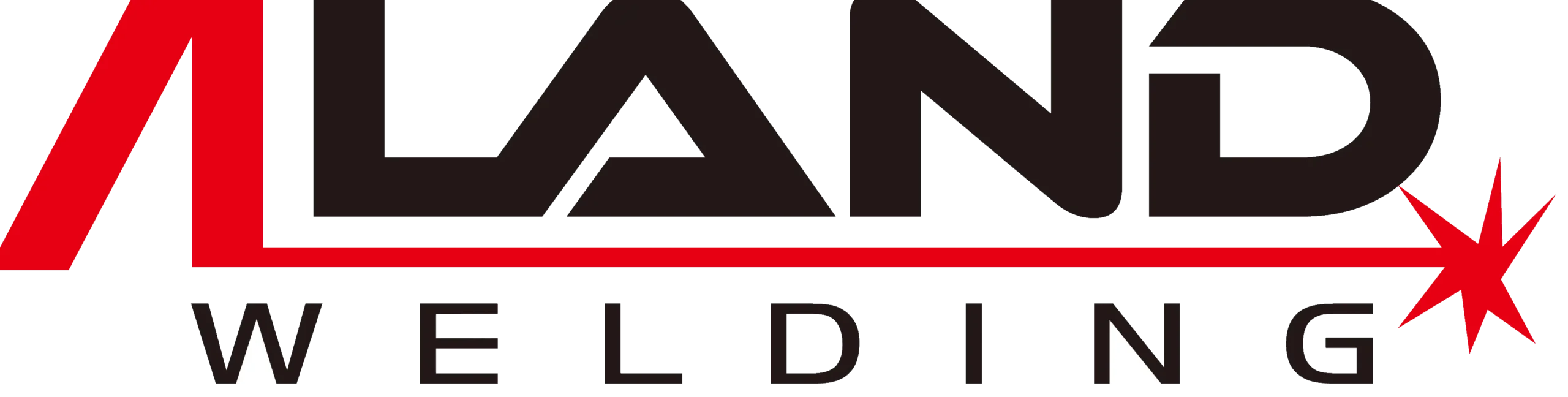
ALAND WELDING Let you feel the most sincere welding service
1. Wire feeder concept
The wire feeder is a device used for the automatic welding process. It drives the wire feed wheel through a motor to continuously and evenly feed the welding wire into the welding area to achieve stable and efficient welding operations. A wire feeder usually includes a wire feed motor, a wire feed wheel, a wire feed guide, a control system and a welding wire drum. Its working principle is to use a motor to drive the wire feed wheel to rotate, unwind the welding wire from the reel and send it to the welding gun or welding head through the conduit. Under the action of the welding arc, the welding wire is melted and fused with the base material to form a weld. The wire feeder can accurately control wire feeding speed and pressure, adapt to different welding currents and voltages, and ensure welding quality. It is widely used in automobile manufacturing, shipbuilding, bridge construction, pressure vessels, pipeline engineering, steel structures and other fields, significantly improving welding efficiency and welding quality while reducing the labor intensity of welders.
2. Purpose of wire feeder
Wire feeding is a very important operation in the welding process. The wire feeding method of manual argon arc welding mostly uses the welder’s fingers to twist the wire to complete the wire feeding process. It is very inconvenient for the welder to operate the wire feeding. Therefore, manual wire feeding must be accurate. Poor performance, poor consistency, and unstable wire feeding result in low welding production efficiency and poor welding forming consistency. In addition, the length of the welding wire held by the welder is limited. When welding for a long time, the welding wire needs to be taken frequently, which results in low welding efficiency. When each section of welding wire is welded, a small section of welding wire will remain unusable, resulting in waste.
The new TWA-I automatic wire feeder is an automatically driven mechanized wire feeding device. It is mainly used for automatic wire feeding for manual welding, automatic wire feeding for automatic argon arc welding, automatic wire feeding for plasma welding and automatic wire feeding for laser welding. The system adopts microcomputer control and stepper reduction motor transmission, with high wire feeding accuracy and good repeatability.
Arc Feeder Iv is a wire feeder that regards arc voltage as Working voltage and adopts arc voltage sensing control technology. It is applicable to solid wire, flux-cored wire and self shielded welding wire.
Main Features
- Strikingarc is in good perfor
- Without control cable, it can match CCor CV DC welding machine and avoid the equipment failure caused by the short circuit and disconnection of output control cable and the instability of the welding process caused by extended cable.
- Four-wheel drive ensures reliable wire feeding.
- Upgrading the common Dc manual welding machine intoMIG,MAG improves production effi
- Common MIG/MAG is upgraded into high-speed gasshielded welding.
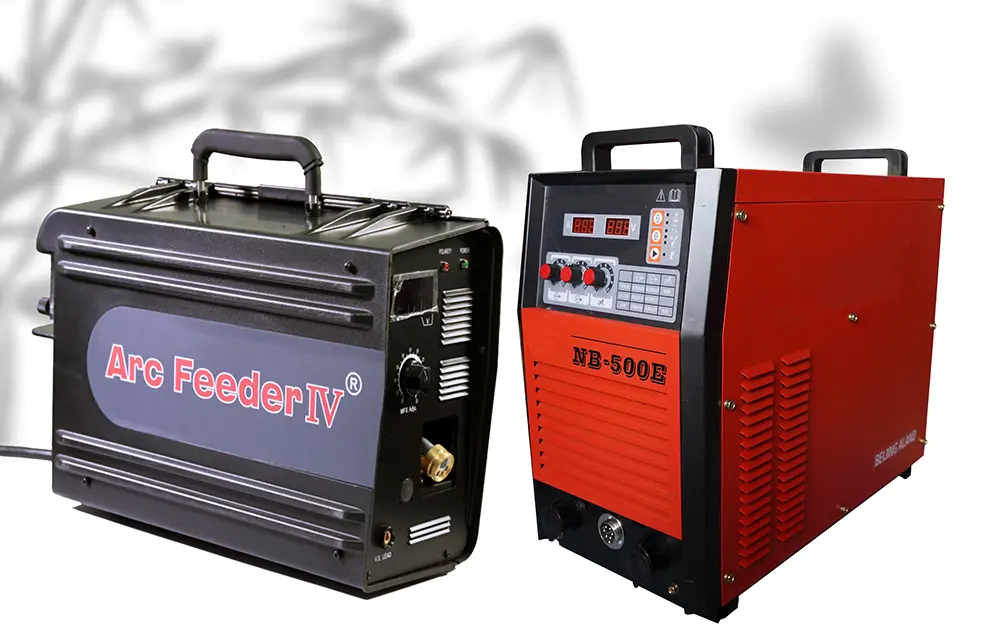
3. Working principle of wire feeder
Automatic wire feeders generally have a control part that provides parameter settings. The drive part drives the wire under the control of the control part, and the wire feed nozzle part sends the welding wire to the position of the welding gun.
(1) Control part
It has the functions of delayed wire feeding and early wire drawing.
It can not only realize stand-alone automatic control (internal control), but also can receive control from the host computer (485 communication).
Wire feeding and wire drawing can be controlled through the foot switch, or the high-frequency switch of the welding gun can be used to achieve synchronous control (high-frequency incoming wire, high-frequency outgoing wire).
The wire feeding speed is 0-1000mm/min (generally can be customized according to customer requirements), and the repeatability error of the wire feeding speed is within ±5%.
It has the functions of continuous wire feeding and intermittent wire feeding, and the frequency and duty cycle of intermittent wire feeding are adjustable.
(2) Drive part
The wire feeding driving part of the automatic wire feeding machine is generally composed of an adjustable preload pressure rod, a driving wheel, and a driven wheel. Adjustable preload pressure rod: used to compress the welding wire, and the handle can be rotated to adjust the compression degree.
Driving wheel: The motor drives the driving wheel to rotate to provide power for wire feeding.
Driven wheel: Press the welding wire into the wire feed groove on the wire feed wheel to increase the friction between the welding wire and the wire feed wheel, so that the welding wire can be sent out smoothly.
(3) Wire feeding nozzle part
The wire feed nozzle part can relatively fix the wire feed nozzle and the welding gun, and can adjust the angle of the wire feed and the distance between the wire feed nozzle and the tungsten electrode to ensure the welding effect.
4. How to operate the wire feeder
(1) Connect the main body of the wire feeder and the wire feed nozzle with the wire feed tube, and install the appropriate wire reel.
(2) If you use a foot switch to control wire feeding and drawing, you only need to connect the foot switch to the wire feeding and drawing interface on the control panel; if you use a high-frequency switch of the welding gun to synchronously control wire feeding and drawing, you need to connect the control Connect the high-frequency outlet interface on the panel to the high-frequency interface on the argon arc welding machine, and then connect the high-frequency incoming line on the control panel to the high-frequency arc pilot line on the welding gun.
(3) If the host computer is required to control the wire feeder, the internal control communication switch on the control panel needs to be placed on the communication side; if the host computer is not required to control the wire feeder, the internal control communication switch on the control panel should be placed on the internal control side.
(4) Install an appropriate wire feed wheel according to the selected welding wire diameter.
(5) Connect the power plug, turn on the power switch, adjust the wire feeding speed to the fastest, press the pressure lever, step on the foot switch, or use the wire feeding and pulling switch on the control panel to make the welding wire reach the feeding wire as soon as possible. Silk mouth. Stop feeding the wire when it passes through the wire feed nozzle.
(6) Adjust the wire feed nozzle to meet the angle requirements of welding. Adjust the parameters of the wire feeder and select the appropriate wire feeding method to achieve the appropriate speed.
(7) Turn on the welding machine and weld normally.
(8) After completing the welding, turn off the power switch and unplug the power plug.
5. Things to note
(1) General matters
① Please be sure to follow the precautions specified in the manual, otherwise an accident may occur.
② Please follow relevant standards and regulations for the design and construction of input power supply, selection of installation site, use of high-pressure gas, etc.
③ Irrelevant personnel are not allowed to enter the welding workplace.
(2) Welding smoke hazards
① Please use the prescribed exhaust equipment to avoid accidents such as gas poisoning and suffocation.
② When working at the bottom of the container, protective gas will be deposited around it, causing suffocation. Special attention should be paid to ventilation.
(3) Welding arc light hazards
① Please wear protective glasses with sufficient shading. Arc light can cause eye inflammation, and spatter and welding slag can burn your eyes.
② Please use welding leather protective gloves, long-sleeved clothes, hats, foot guards, aprons and other protective equipment to prevent arc light, spatter and welding slag from burning or scalding the skin.
(4) Fire and explosion accidents
①No combustibles should be placed in the welding site. Spatter and hot welds may cause fire.
② The welding cable and the base material must be connected tightly, otherwise it will generate heat and cause a fire.
③Do not weld in flammable gas or on containers containing flammable substances, otherwise it may cause an explosion.
④Do not weld closed containers, otherwise they may break.
⑤ A fire extinguisher should be prepared just in case.
(5) Prevent rotation from injuring people
①Do not put your fingers, hair, clothes, etc. close to rotating parts such as wire feed wheels.
② When feeding the welding wire, do not put the end of the welding gun close to your eyes, face or body to avoid injury to people from the welding wire.