Defective presentation of welding tongs
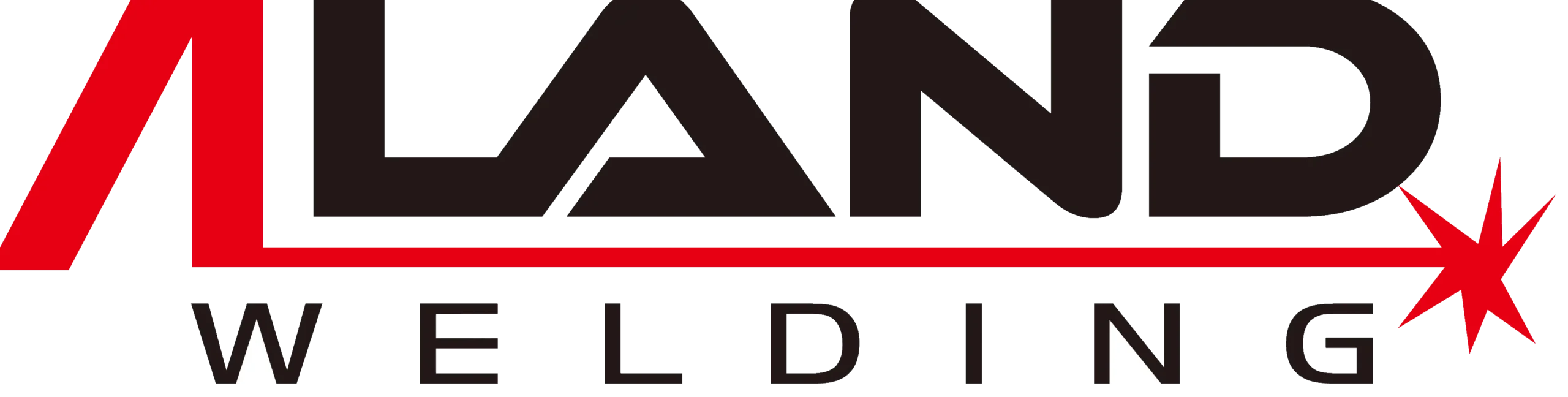
ALAND WELDING Let you feel the most sincere welding service
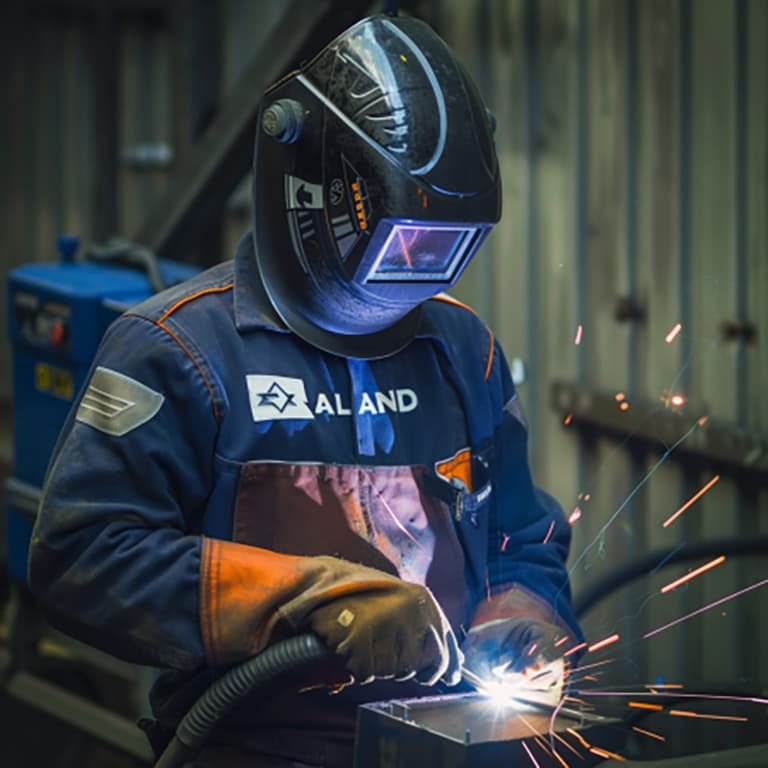
1. Concept of welding tongs
welding tongs refer to the necessary tools used by welders to hold welding rods and achieve welding. The construction of the welding clamp is safe, lightweight and durable. There are two commonly used commercially available welding clamps, 300A and 500A, which can safely and quickly install the welding rod and remove the remaining welding rod fragments; clamp the welding rod at any specified position and weld it until only 50mm is left in length. ; Without the operator exerting any external force, clamp the welding rods of various specifications and diameters specified by the manufacturer; when the welding rod and the workpiece are bonded together, the welding rod can be separated from the workpiece.
2. The role of welding tongs
Its function is to hold the welding rod and conduct the welding current during welding. It is used in conjunction with the arc welding machine. During manual arc welding, it is a hand-held insulating instrument used to hold and manipulate the welding rod and ensure the electrical connection with the welding rod. Welding clamps have main technical indicators such as shell protection, anti-electric shock protection, temperature rise value, welding spatter resistance, and drop resistance.
3. Types of welding tongs
(1) Manual arc welding clamp (welding handle)
Usage: For manual arc welding (SMAW).
Features:
Structure: Generally made of copper alloy to ensure good electrical conductivity. The handle part has an insulating layer to prevent electric shock.
Function: Clamp the welding rod, connect to the welding machine through the welding cable, provide current, make the welding rod generate arc and melt the metal for welding.
Type: Common ones include spiral clamp type, spring clamp type, bayonet type, etc.
(2) Spot welding clamp
Purpose: used for resistance spot welding.
Features:
Structure: It has two pairs of electrode arms. The electrode head is usually made of copper or copper alloy to withstand high temperature and high pressure.
Function: Clamp the workpiece through the electrode arm, and apply pressure and current to locally heat and melt the contact points to achieve welding.
Application: Commonly used in automobile manufacturing, home appliance production and other thin sheet metal connections.
(3) Seam welding clamp
Purpose: used for resistance seam welding.
Features:
Structure: The electrode is wheel-shaped and can roll continuously.
Function: Roll along the gap of the workpiece, apply pressure and current, and form a continuous weld.
Application: Used for welding of sealed containers, fuel tanks, pipes, etc.
(4) Clamp-on welding clamp
Purpose: Used for welding operations requiring strong clamping.
Features:
Construction: Similar to pliers, usually with a screw clamping mechanism.
Function: Provide strong clamping to keep the workpiece stable.
Application: Suitable for welding larger and thick workpieces, such as steel structural parts.
(5) Pneumatic welding clamp
Usage: Used for industrial automation welding.
Features:
Structure: driven by a pneumatic system, including cylinders, control valves and electrodes.
Function: Realize automatic clamping and welding operations to improve efficiency.
Application: Suitable for assembly line operations and mass production.
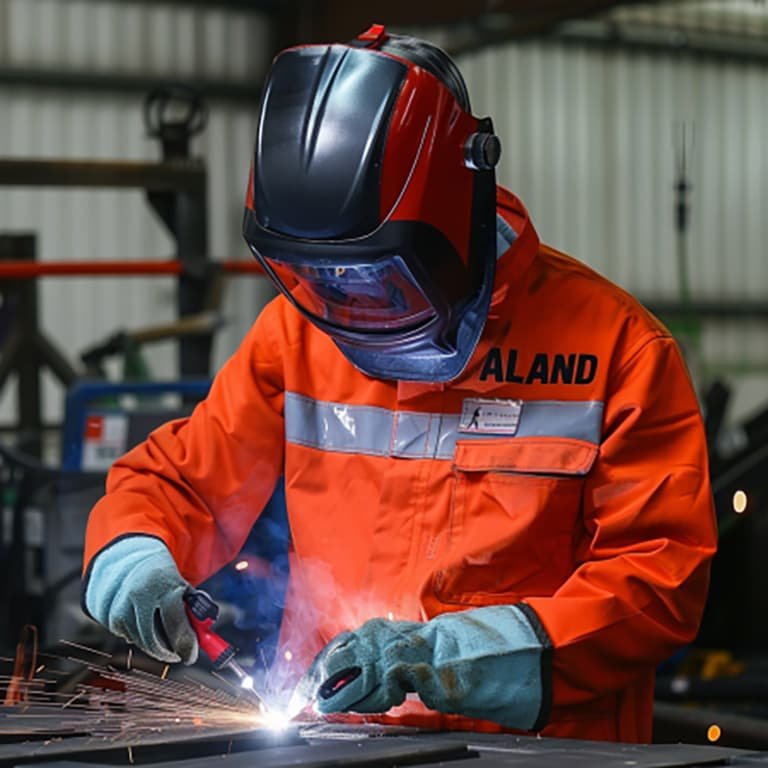
(6) Hydraulic welding clamp
Purpose: For welding tasks requiring high-pressure clamping.
Features:
Structure: Adopts hydraulic system, including hydraulic cylinder and control valve.
Function: Provides high pressure clamping force and stability.
Application: Suitable for welding heavy workpieces and thick plates.
(7) Magnetic welding clamp
Purpose: Used in welding positions that are difficult to clamp.
Features:
Structure: Use strong magnets or electromagnets.
Function: Fix the workpiece through magnetic force.
Application: Suitable for welding irregularly shaped or difficult-to-clamp metal parts.
(8) Tungsten inert gas welding (TIG) welding clamp
Usage: used for TIG welding.
Features:
Structure: Specifically designed to hold tungsten electrodes, the handle is partially insulated.
Function: Provide stable current and protective gas (such as argon) to avoid oxidation of the welding area.
Application: Suitable for high-demand welding of stainless steel, aluminum, etc.
(9) Oxyacetylene welding clamp
Usage: Used for oxyacetylene gas welding and cutting.
Features:
Structure: Used to hold a welding gun for welding or cutting.
Function: Produce high-temperature flame through the mixture of oxyacetylene gas, used for welding or cutting metal.
Application: metal cutting, welding and repair operations.
(10) Multifunctional welding clamp
Usage: Suitable for a variety of welding processes.
Features:
Structure: The design is flexible and can be adjusted to suit different tasks.
Function: Adapt to various welding requirements.
Application: Suitable for small batch and multi-variety welding operations.
4. Advantages of welding tongs
(1) Clamping is stable
Stability: The welding clamp can firmly clamp the workpiece and prevent the workpiece from moving or vibrating during the welding process, thereby ensuring the accuracy and quality of welding.
Versatility: Suitable for workpieces of all shapes and sizes, whether they are small precision parts or large heavy-duty structures, they can be effectively clamped.
(2) Good electrical conductivity
Efficient conductivity: welding tongs are usually made of copper or copper alloy and have excellent conductivity, ensuring smooth conduction of current and reducing resistance and heat loss.
Welding quality: Good electrical conductivity helps form a stable arc, improving the quality and consistency of welded joints.
(3) Easy to operate
Ergonomic design: The handle of the welding clamp is designed to be ergonomic, comfortable to hold and easy to operate, reducing fatigue during long-term use.
Convenient to use: Many welding clamps are designed for one-handed operation, especially suitable for working in small spaces or complex welding positions.
(4) High temperature tolerance
High temperature resistant materials: The welding clamp material has good high temperature resistance and can work in high temperature environments for a long time without deformation or damage.
Long life: High temperature resistant materials extend the service life of the welding clamp, reducing replacement frequency and maintenance costs.
(5) Versatility
Various types: There are many types and specifications of welding tongs, such as manual arc welding clamps, spot welding clamps, seam welding clamps, etc., which can meet the needs of different welding processes.
Wide application: Suitable for metal processing, automobile manufacturing, construction engineering and other industries.
(6) High safety
Insulation protection: The handle of the welding clamp usually has an insulation layer to prevent electric shock during operation and ensure the safety of the operator.
Anti-slip design: Many welding clamp handles are also designed with anti-slip function, which improves the safety and stability of operation.
(7) Easy maintenance
Simple structure: The welding clamp has a relatively simple structure, which is convenient for daily maintenance and upkeep.
Low maintenance costs: Due to its durability and simple design, welding tongs are low-cost to repair and replace.
(8) Improve welding quality
Precise control: The welding clamp provides precise clamping and pressure control to ensure the quality and consistency of welded joints.
Reduce defects: Stable current conduction and firm clamping reduce welding defects such as pores, cracks, and lack of fusion, improving the overall welding quality.
(9) Strong adaptability
Widely applicable: Whether indoors or outdoors, workpieces of various materials and shapes can be welded using welding tongs.
Flexible application: The welding clamp is suitable for various welding methods, such as manual arc welding, spot welding, seam welding, etc., and can flexibly cope with different welding tasks.
(10) Improve production efficiency
Efficient Operation: The design and functionality of the welding clamp make welding operations more efficient, reducing preparation time and operation time.
Reliability: The high reliability and durability of the welding clamp reduces equipment failures and downtime and improves production efficiency.
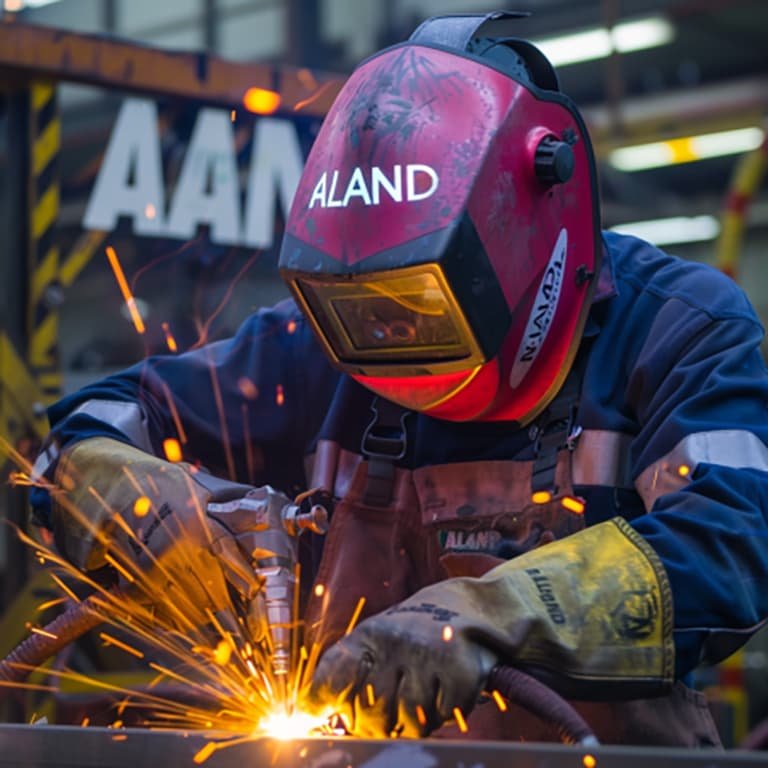
5. Safety requirements for using welding tongs
The function of the welding clamp is to hold the electrode and conduct current. It is the main tool for arc welding. It is directly related to the operational safety of welders, so the following safety requirements must be met:
(1) The welding clamp should be able to clamp the welding rod at any angle it is set, and ensure the safety and convenience of replacing the welding rod.
(2) The handle of the welding pliers should have good insulation and heat insulation properties. It is prohibited to use welding pliers with damaged insulation or no insulation.
(3) The connection between the welding clamp and the welding cable should be simple and reliable, with good contact.
(4) The welding clamp should be light (no more than 0.6kg) and easy to operate.
(5) During the welding process, it is prohibited to put overheated welding pliers into water to cool down and continue to use them.