Introduction to common welding techniques
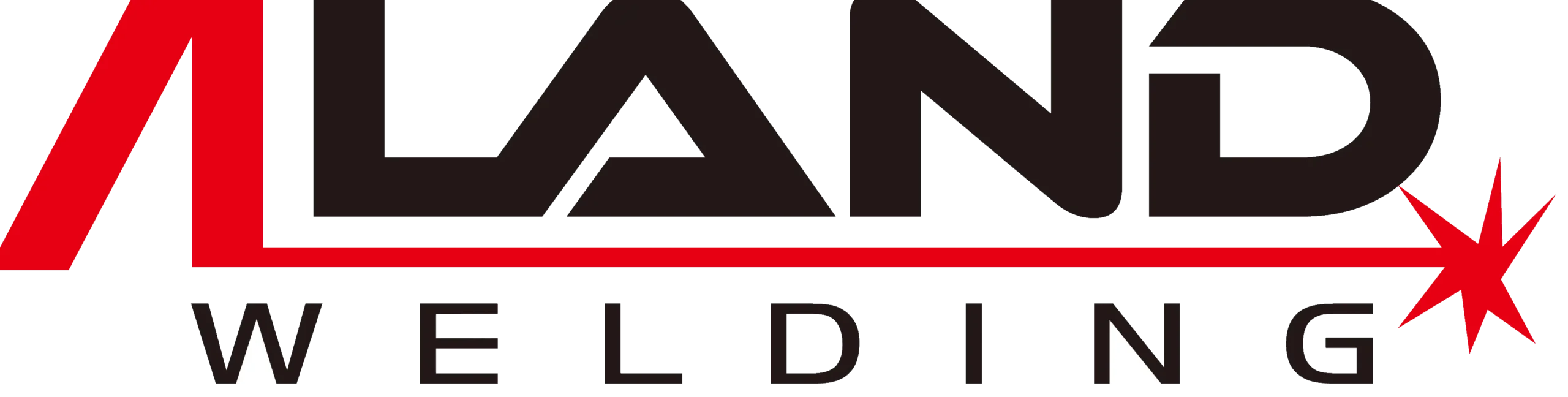
ALAND WELDING Let you feel the most sincere welding service
Welding techniques is a process for joining metal or thermoplastic materials together, usually involving processes such as heating, melting, filling and cooling. It includes the following main aspects: manual welding, automatic welding, gas shielded welding, pressure welding, friction welding, laser welding, electron beam welding, plasma welding
1. Manual welding
Manual welding is a common Welding techniques that relies on manual operation of welding equipment to join workpieces together. Manual welding typically uses arc welding equipment, including handheld arc welding guns and corresponding power supplies. According to the shape and requirements of the workpiece, the welding operator holds the welding gun, controls the current and welding angle, and contacts the welding wire (filler material) with the workpiece to form a molten arc, which generates enough heat in the welding area to melt and connect the workpieces together.
Advantages of hand welding include:
High flexibility: Welding operators can adapt the welding process to specific situations and adapt to workpieces of different shapes and materials.
Wide scope of application: Manual welding is suitable for workpieces of various sizes and welding environments, from small manual workshops to large production lines.
Low cost: Compared with automated welding equipment, manual welding equipment has lower costs and is less dependent on labor costs.
Good controllability: The welding operator can directly observe the welding process and adjust the welding parameters in time to ensure the welding quality.
However, hand welding also has some disadvantages, such as:
Welding quality is affected by the operator’s technical level: differences in Welding techniques level may lead to unstable welding quality.
Lower productivity: Manual welding is generally less productive than automated welding.
Poor repeatability: Due to its reliance on manual operations, manual welding may not be as repeatable and consistent as automated welding.
2. Automatic welding
Automated welding is a method of welding using automated equipment, often using pre-programmed robots or welding machines to operate without the need for human intervention. Automatic welding can greatly improve the production efficiency, consistency and accuracy of welding, and can adapt to the needs of mass production. Here are some of the key features and benefits of automated welding:
High production efficiency: Automatic welding equipment can weld at a stable speed and with high efficiency, thereby improving production efficiency and reducing the need for human resources.
Consistency and accuracy: Since the welding process is entirely performed by pre-programmed robots or welding machines, automatic welding can ensure the consistency and accuracy of welding quality, reducing the impact of human factors on welding quality.
Strong adaptability: Automatic welding equipment can be programmed and adjusted according to specific welding requirements, adapting to workpieces of various shapes, sizes and materials, making it highly adaptable.
High safety: Automatic welding equipment can usually operate in a closed working environment, reducing the exposure of personnel during the welding process to potentially dangerous situations and improving work safety.
Reduce the scrap rate: Since automatic welding can ensure the stability and consistency of welding quality, it can reduce scrap and defective products during the welding process, reducing production costs.
Traceability: By monitoring and recording the automatic welding process, welding quality can be traced, which helps analyze and improve the welding process.
3. Gas shielded welding
Gas Metal Arc Welding (GMAW) is a common automatic or semi-automatic welding method, also known as Gas Metal Arc Welding (MIG) or Inert Gas Metal Arc Welding (Inert Gas Metal Arc Welding, MIG). In this welding process, a continuous wire electrode is fed into the welding area through a welding gun, and together with the workpiece to be welded, passes through a spark area formed by an electric current called an arc. At the same time, the protective gas (usually an inert gas such as argon) released through the welding gun covers the welding area to prevent the oxidation reaction between the molten metal and the outside air.
Here are some of the key features and benefits of gas shielded welding:
High welding speed: Gas shielded welding usually has a high welding speed, which can quickly complete the welding task and improve production efficiency.
High welding quality: Due to the effect of the protective gas, the welding area is well protected, the weld quality is usually higher, and less oxides and other pollutants are produced during the welding process.
Strong adaptability: Gas shielded welding is suitable for various metal materials, including steel, aluminum alloys, magnesium alloys, etc., and is suitable for workpieces of different shapes and thicknesses.
Simple operation: Compared with other welding methods, gas shielded welding is relatively simple to operate and can be operated automatically or semi-automatically, reducing technical requirements and operational difficulty.
Small welding deformation: Due to the small heat input during the welding process, gas shielded welding can usually reduce the welding deformation of the workpiece, which is beneficial to maintaining the shape and size of the workpiece.
Various applicable scenarios: Gas shielded welding can be used to weld different types of workpieces such as thin plates, medium and thick plates, pipes, structural parts, etc., and is suitable for various industrial fields, such as automobile manufacturing, aerospace, metal structures, etc.
4. Pressure welding
Pressure welding is a welding method that brings two or more metal workpieces into close contact at the welding area by applying pressure and welding at a higher temperature to ensure a good welding connection. This welding method does not require additional filler material at the joint, but relies on the material flow of the workpiece itself to form the weld. Pressure welding is often used to join metals with similar or identical chemical compositions, such as steel, aluminum, etc.
The main types of pressure welding include:
Spot welding: Applying high current to the contact points of two or more metal workpieces causes local melting of the contact points and forms a weld under the application of a certain amount of pressure.
Seam welding: By applying pressure on the edge of the workpiece, local melting occurs at the seam, and then the weld is formed by cooling.
Butt welding: Align the ends of two workpieces and apply pressure on the welding area to cause local melting and join together.
Advantages of pressure welding include:
High weld strength: Welds generally have high strength due to the pressure exerted during the welding process.
No filler material required: Pressure welding typically does not require additional filler material, saving costs and process steps.
High production efficiency: Pressure welding is generally an efficient welding method, especially suitable for mass production.
Small welding deformation: Due to the pressure exerted during the welding process, the welding deformation of the workpiece can usually be reduced.
5. Friction welding
Friction Welding techniques is a solid-state welding method that uses heat generated by friction to join workpieces together. During the friction welding process, two workpieces are rubbed together by rotating and applying a certain axial pressure. The heat generated by the friction causes the surface of the workpiece to partially melt, and a welded joint is formed when the friction stops. This welding method is usually suitable for joining metal materials, such as aluminum alloys, titanium alloys, magnesium alloys, etc.
Friction welding is generally divided into the following types:
Friction stir welding (FSW): A specially shaped welding needle rotates between the workpieces and applies axial pressure to stir the workpieces together to form a weld. This method is suitable for welding difficult-to-weld materials such as aluminum alloys.
Friction Stir Friction Welding (FSFW): Based on friction stir welding, the welding is strengthened by applying another certain axial pressure during the welding process.
Friction Welding: By applying axial pressure between two workpieces, they generate heat under the action of friction, and finally form a welded joint. This method is suitable for joining various metals, such as steel, aluminum, nickel alloys, etc.
Advantages of friction welding include:
No filler material required: Friction welding is a solid-state welding method that does not require additional filler material, thus avoiding pores and inclusions created during the welding process.
Small welding distortion: Because there is no melting during the welding process, friction welding usually reduces the distortion of the workpiece.
Environmentally friendly: The friction welding process does not involve molten metal, does not produce welding smoke and gas, and is environmentally friendly.
6. Laser welding
Laser welding is a highly precise Welding techniques that uses the high energy generated by a laser beam to melt the surfaces of workpieces and join them together. During the laser welding process, the laser beam is focused on the workpiece contact point, generating a temperature high enough to melt the material and form a weld. Laser welding is usually suitable for metal materials such as steel, aluminum, stainless steel, etc.
Laser welding is mainly divided into the following types:
Traditional laser welding: In traditional laser welding, the laser beam is focused on the workpiece surface through a focusing lens, generating enough energy to melt the material and form a welded joint.
Deep penetration laser welding: Deep penetration laser welding uses a higher power laser to achieve deeper melting and greater weld depth, and is suitable for applications requiring deeper welds.
Laser brazing: Laser brazing uses a laser beam to heat the solder to a liquid state and form a flow of solder on the surface of the workpiece to connect the workpieces.
Laser hybrid welding: Laser hybrid welding combines laser welding with other traditional welding methods, such as arc welding or gas shielded welding, to increase welding speed and efficiency.
Advantages of laser welding include:
High precision: The laser beam can precisely control the welding position and welding depth, thereby achieving high-precision welding.
Small heat-affected zone: Since the heat input of laser welding is relatively small, the heat-affected zone around the workpiece can be reduced, reducing the risk of workpiece deformation and thermal cracks.
Non-contact: Laser welding is a non-contact welding method that does not cause additional damage to the surface of the workpiece.
Automation: Laser welding can be integrated with automation systems to achieve efficient mass production.
7. Electron beam welding
Electron beam welding is a high-energy welding method that uses high-speed electron beams to heat and melt the surface of the workpiece to achieve welding. In electron beam welding, the high energy of the focused electron beam causes the surface of the workpiece to be locally heated above the melting point, and then the material on the surface of the workpiece is melted and a weld is formed under pressure. This welding method is usually suitable for metal materials with good conductivity, such as steel, stainless steel, aluminum alloy, etc.
The main features of electron beam welding include:
High welding speed: Electron beam welding has a high welding speed, which can complete a large number of welding tasks in a short time and improve production efficiency.
Small welding deformation: Due to the local heating during the welding process and the short welding time, electron beam welding can usually reduce the welding deformation of the workpiece, which is beneficial to maintaining the shape and size of the workpiece.
High welding quality: The heat generated during the electron beam welding process is highly concentrated and the welding area is well controlled, so the welding quality is usually high and the welds have almost no pores and inclusions.
No filler material required: Since the heat above the melting point during welding is provided by the electron beam, no additional filler material is usually required.
Wide scope of application: Electron beam welding is suitable for workpieces of various shapes and sizes, and can weld different types of workpieces such as thin plates, medium and thick plates, and pipes.
Articles you may be interested in:
Stick Welding Concept And Process
WSME Welding Machine Introduction
Introduction To TIG Welding Machine
Learn More About Resistance Welding
Arc Welding Machine Applicable Industry
Difference Between MIG And TIG Welding
Choice Of Different Types Of Welding Rods
The Importance Of Welding Torch Selection
Ac Dc Tig Welding Comparison Instructions
Basic Knowledge Of Welding Procedure Qualification