Advantages And Disadvantages of handheld laser welder
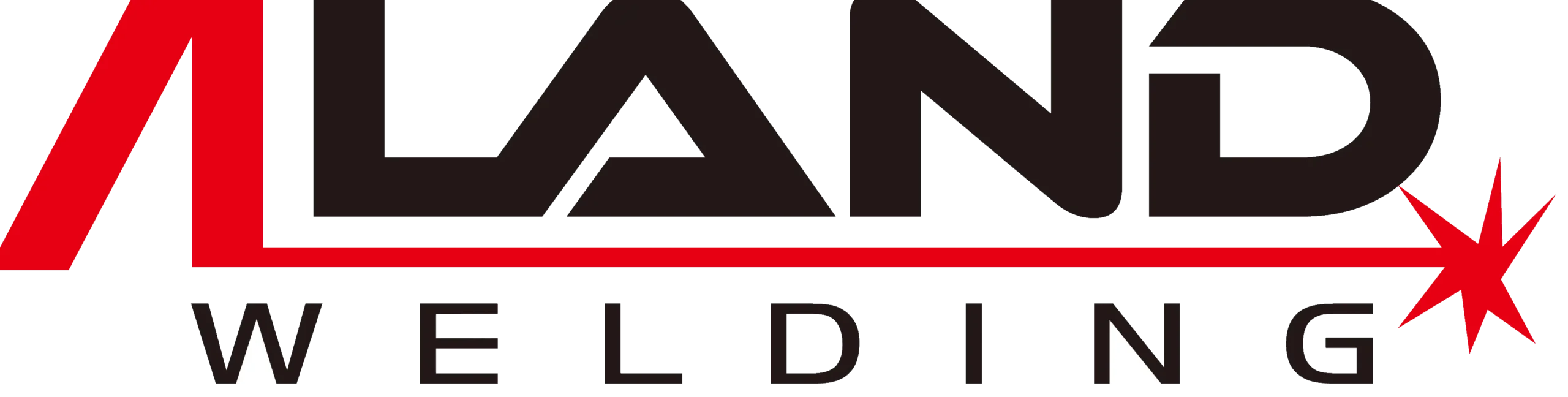
ALAND WELDING Let you feel the most sincere welding service
Advantages and Disadvantages of Laser:
Handheld Laser Welder Advantage:
(1) Reduces caloric input requirements to the minimum;
(2) The welding process parameters for single-pass welding of 32mm plate thickness have been certified, which can reduce the time required for thick plate welding and even eliminate the use of filler metal;
(3) There is no need to use electrodes, and there is no concern about electrode contamination or damage. And because it is not a contact welding process, the wear and deformation of the machine tools can be minimized;
(4) The laser beam is easy to focus, align and guide by optical instruments. It can be placed at an appropriate distance from the workpiece and can be redirected between machines or obstacles around the workpiece. Other welding methods cannot be used due to the above-mentioned space restrictions;
(5) Workpieces can be placed in enclosed spaces;
(6) The laser beam can be focused on a small area and can weld small and closely spaced parts;
(7) There is a wide range of weldable materials, and various dissimilar materials can be joined;
(8) Easy to automate high-speed welding and can be digitally or computer controlled;
(9) When welding thin materials or fine-diameter wires, unlike arc welding, there is no problem of remelting;
(10) Not affected by magnetic fields, can accurately align welding parts;
(11) Can weld two metals with different physical properties (such as different resistance);
(12) No vacuum or X-ray protection is required;
(13) If through-hole welding is used, the depth-to-width ratio of the weld bead can reach 10:1;
(14) The unit can be switched to deliver the laser beam to multiple workstations.
Handheld Laser Welder Shortcoming:
(1) The position of the weldment needs to be very precise and within the focus range of the laser beam;
(2) When a fixture is required for the weldment, it must be ensured that the final position of the weldment is aligned with the welding point where the laser beam will impact;
(3) Laser welding is not suitable for use on the production line;
(4) The weldability of highly reflective and high thermal conductive materials such as aluminum, copper and their alloys will be changed by laser;
(5) When performing medium to high energy laser beam welding, a plasma controller needs to be used to remove the ionized gas around the molten pool to ensure the reappearance of the weld bead;
(6) Energy conversion efficiency is too low, usually less than 10%;
(7) The weld bead solidifies quickly, and there may be concerns about porosity and embrittlement;
(8) Equipment is expensive.
Articles you may be interested in:
Detailed Explanation Of Spot Welding Process
Why choose TIG welding? 4 major benefits
How To Maintain And Maintain Welding Equipment
How Should Welders Protect Their Own Safety During Work?
Introduction to TIG welding and basic operating procedures
Welding, Pressure Welding And Brazing Welding Process
The Difference Between ARC Welding Machine and Electric Welding Machine
Primary wire, secondary wire, welding wire, ground wire, ground wire
How to distinguish between welding slag and molten iron during welding?
Welder skills and knowledge: What basic knowledge do beginners need to master?