MIG welding machine and process introduction
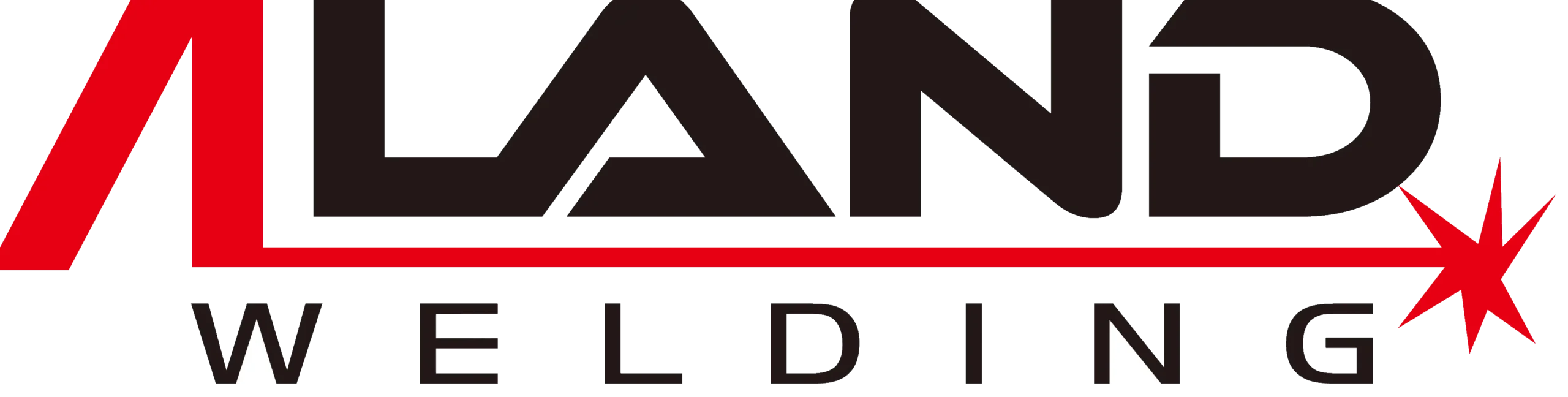
ALAND WELDING Let you feel the most sincere welding service
In modern manufacturing, welding technology plays an indispensable role, and MIG welding technology is a favored welding process. MIG welding has been widely used in automobile manufacturing, shipbuilding, aerospace and other fields because of its high efficiency, stability and suitability for a variety of metal materials. This article will deeply explore the process principles, application scope and key technical points of MIG welding technology, hoping to provide some useful reference and guidance for welding workers.
1. Introduction to MIG welding machine
MIG welding machine (Metal Inert Gas Welding Machine), also known as gas shielded welding machine or arc gas shielded welding machine, is a commonly used arc welding equipment. The following is an overview of MIG welding machines:
Principle: MIG welding machine uses the high temperature generated by arc discharge to melt the workpiece surface and welding wire to form a weld. During the welding process, the molten metal is protected by injecting an inert gas (such as carbon dioxide or argon) to prevent it from reacting with oxygen in the surrounding environment.
Working method: MIG welding machine provides electric energy through the power supply, adjusts the welding current and voltage through the controller, and controls the flow and speed of the injection gas at the same time. The welder moves the welding gun to the location where welding is required and controls the welding process manually or automatically.
Application: MIG welding machines are widely used in welding various metal materials, including steel, aluminum, magnesium, copper, etc. It has important applications in manufacturing, construction, automobile manufacturing, shipbuilding, and home repair.
advantage:
Efficiency: fast welding speed and high production efficiency.
Stable quality: high-quality, uniform welding can be achieved.
Strong adaptability: suitable for different types of metal materials.
Easy to operate: Compared with other welding methods, the operation is relatively simple and easy to learn.
shortcoming:
The quality of welds is affected by the environment: Affected by factors such as wind speed and gas flow, the quality of welds may decline.
High power requirements: A stable power supply is required to ensure welding quality.
High requirements on the workpiece surface: the workpiece surface must be clean, otherwise the welding quality may be affected.
Equipment composition: MIG welding machines usually include the following main components:
Power supply: Provides the electrical energy required for welding.
Controller: regulates welding current, voltage and gas flow.
Welding gun: used to spray welding wire and shielding gas and complete the welding operation.
Welding wire supply device: Provides welding wire to ensure continuous supply.
Gas supply device: Provides protective gas to protect the welding area.
2. Introduction to MIG welding work
Preparation:
Prepare welding equipment: Make sure the power supply, controller, welding gun, wire supply device and gas supply device of the MIG welder are working properly.
Clean the workpiece surface: Remove oil, oxides and other impurities from the workpiece surface to ensure welding quality.
Select appropriate welding parameters: Select appropriate welding current, voltage and gas flow according to the welding material and thickness.
Set welding parameters:
Current and voltage: According to the material and thickness of the welding workpiece, adjust the current and voltage of the MIG welder to ensure welding stability and proper melting.
Gas flow: According to the welding materials and welding environment, the flow rate of the shielding gas (usually carbon dioxide or argon) is adjusted to ensure effective protection of the welding area.
Steps:
Welding gun position: Aim the welding gun at the location to be welded and maintain the appropriate angle and distance.
Start welding: Press the trigger of the welding gun to start the arc and start adding welding wire to the weld while moving the welding gun to form an even weld.
Control the welding speed: According to the welding material and thickness, control the welding speed and the addition of filler materials to ensure the quality and uniformity of the weld.
End of welding: After completing the welding, release the trigger of the welding gun, stop the arc, and ensure that the welding area cools down before processing.
Welding safety:
Wear appropriate personal protective equipment such as welding masks, welding gloves and protective clothing.
Pay attention to ventilation around the welding area to prevent the accumulation of harmful gases.
Take care to avoid contact with the welding arc and molten metal to prevent burns and other injuries.
3. Processes that MIG welders need to master
Process parameter settings:
Understand the impact of parameters such as welding current, voltage, wire diameter and gas flow on welding quality.
Learn to adjust these parameters based on the type and thickness of the welding material to achieve the best welding results.
Arc formation and maintenance:
Gain an in-depth understanding of arc formation and maintenance mechanisms, including arc characteristics, arc stability, and impact on welding quality.
Master arc control techniques to ensure stability and consistency during welding.
Welding material preparation and handling:
Understand the welding characteristics of different metal materials, including steel, aluminum, copper, etc., as well as their surface treatment requirements.
Master welding material preparation techniques such as cleaning, grinding and preheating to ensure welding quality.
Selection and use of welding wire:
Gain an in-depth understanding of the different types of welding wires, including solid wires, flux-cored wires, and more, as well as their applications and characteristics.
Able to select appropriate welding wire according to welding needs, and master the correct welding wire feed speed and extension adjustment technology.
Gas protection technology:
Understand the principles and functions of gas protection, including the application of different inert gases (such as carbon dioxide, argon) in the welding process.
Master gas flow adjustment techniques to ensure that the welding area is fully protected and clean.
Welding technology and operations:
Be proficient in the use of welding guns, including correct welding angle, movement speed and welding distance.
Ability to perform different types of weld joint arrangements and weld seam filling to obtain uniform and strong welds.
Welding quality control:
Master welding quality inspection and evaluation techniques, including visual inspection, weld penetration testing and weld size measurement.
Ability to identify and repair welding defects to ensure welding quality meets standards and requirements.
Safety and environmental protection:
Have an in-depth understanding of the safety risks and environmental protection requirements during the welding process, including the emission of harmful gases and ventilation measures in the welding area.
Able to effectively take preventive and emergency measures to ensure safety and health in the workplace.
4. What skills do high-paid MIG welders need to master
Welding technology:
Proficient in the principles, process parameters and operating techniques of MIG welding.
It can adjust the welding current, voltage and gas flow according to different welding materials and thicknesses to ensure welding quality.
It has good welding feel and uniform welding speed to ensure the quality and appearance of the weld.
Safety consciousness:
Have strict safety awareness and be able to properly use personal protective equipment such as welding masks, welding gloves and protective clothing.
Be familiar with the safe operating procedures in the welding area and pay attention to preventing fires, explosions and other accidents.
Quality control:
Familiar with welding quality standards and testing methods, and able to conduct quality inspection and evaluation of welds.
Have the ability to solve welding defects and quality problems to ensure that the welding work meets the requirements.
Problem solving skills:
Have the ability to quickly identify and solve problems during the welding process, such as arc instability, welding slag, pores, etc.
Able to effectively adjust welding parameters and operating methods to solve challenges during the welding process and ensure welding quality.
Teamwork:
Good team spirit and communication skills, able to work effectively with other workers, supervisors and engineers to complete team tasks.
Able to flexibly adjust work arrangements according to work needs, coordinate with the team, and improve work efficiency.
Continuous learning:
Maintain continuous attention to welding technology and industry development, constantly learn new welding technologies and processes, and improve your professional level.
Participate in relevant training courses and certification exams, obtain welding technology and qualification certificates, and improve your competitiveness.
To sum up, MIG welding technology, as an important modern welding process, plays an important role in industrial production. By having an in-depth understanding of the process principles and technical points of MIG welding, welding workers can master efficient and stable welding methods and improve welding quality and production efficiency. With the continuous development and advancement of technology, it is believed that MIG welding technology will continue to play an important role in the future welding field and make greater contributions to the development of the manufacturing industry.
Articles you may be interested in:
Introduction To Welding Pad Process
How To Choose A Suitable Wire Feeder
Stick Welding Concept And Process
WSME Welding Machine Introduction
Introduction To TIG Welding Machine
Learn More About Resistance Welding
How To Choose Industrial Water Chiller
Arc Welding Machine Applicable Industry
Difference Between MIG And TIG Welding
Choice Of Different Types Of Welding Rods
The Importance Of Welding Torch Selection
Introduction To Common Welding Techniques