Different Welding Power Sources
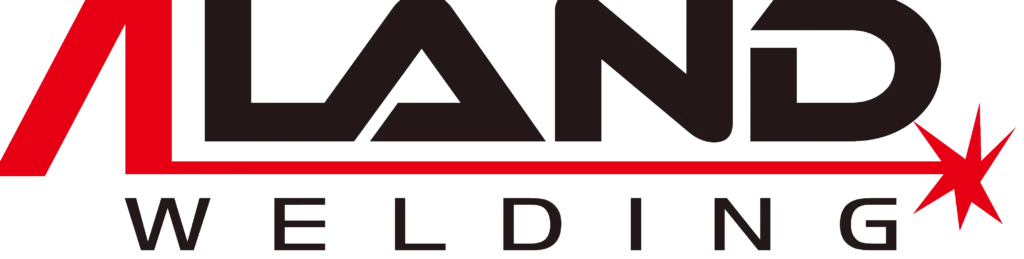
ALAND WELDING Let you feel the most sincere welding service
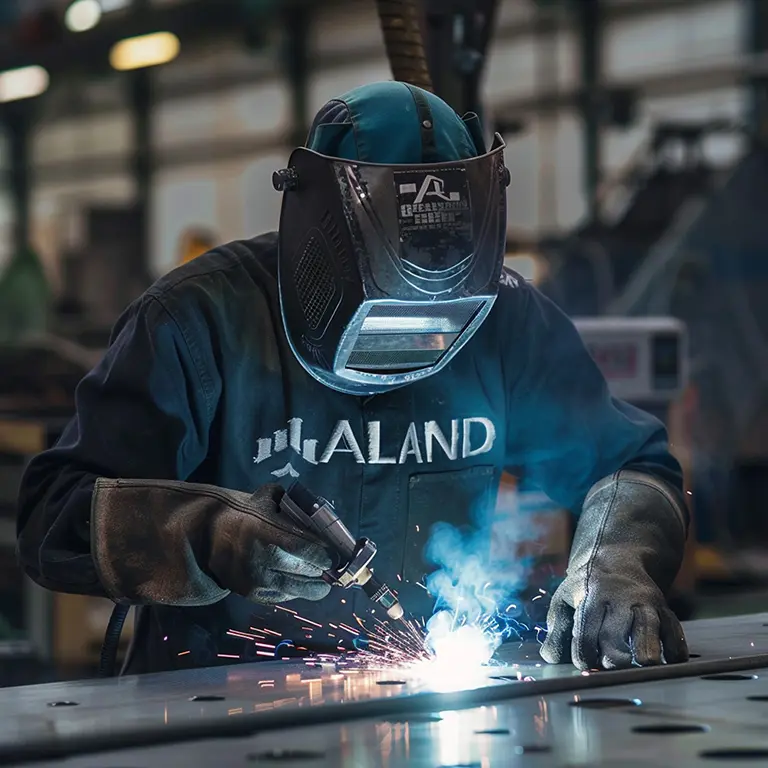
Choosing the right welding power source is crucial to achieving a high-quality welding job. Whether performing simple repair work in a home workshop or complex welding tasks in industrial manufacturing, the right welding power source can provide a stable welding arc, precise welding control, and the portability to meet the needs of your specific environment. When faced with various types of welding power sources, understanding their characteristics, advantages, disadvantages, and applicable scenarios can help you make a wise choice and ensure that you purchase welding equipment that meets your needs.
Introduction to types of welding power sources
The power supply of a welding machine is a device that supplies the electrical energy required for the welding process. Generally speaking, the power supply of welding machines can be divided into the following types:
Alternating Current Power (AC): One of the most common types, AC power draws its power from a regular household power source. AC power sources are typically used for light welding tasks such as home repairs and light industrial applications.
Direct Current Power Supply (DC): DC power supplies provide stable DC current and are often used in applications that require higher welding quality and more precise control, such as shipbuilding, aerospace, and automotive manufacturing.
Inverter power supply: Inverter power supply converts the input AC power into high-frequency AC power, and then converts it into the required DC power. Inverter power supplies are typically lighter and more efficient than traditional transformer-style welders, and can provide better arc stability and control.
Dual power supply: Some advanced welders have dual power supply capabilities that can support both AC and DC power supplies. This type of welder offers greater flexibility and can be used in a wider range of welding applications.
Differences Between Welding Power Sources
When talking about different types of welding power sources, there are several aspects that need to be considered in detail, including performance, scope of application, advantages and disadvantages, and applicable scenarios. Here is a detailed explanation of each type of welding power source:
Alternating current power supply (AC):
Performance characteristics: The AC power supply periodically changes the direction of the current, which causes the welding arc to be unstable and therefore the welding quality is relatively low. However, AC power is suitable for welding lightweight materials such as aluminum and magnesium.
Scope of application: Suitable for home maintenance, agricultural equipment maintenance and light industrial applications, etc.
Advantages: Relatively low cost.
Disadvantages: The welding arc is unstable and the welding quality is low. Not suitable for some applications requiring high welding quality, such as automobile manufacturing, aerospace, etc.
Direct current power supply (DC):
Performance features: DC power supply provides stable current and voltage, resulting in a more stable welding arc and higher welding quality. Suitable for welding various materials, including steel, stainless steel, etc.
Scope of application: Widely used in automobile manufacturing, shipbuilding, aerospace and other industries that require high quality welding.
Advantages: The welding arc is stable and the welding quality is high. Can provide better welding control.
Disadvantages: Relative to AC power, the cost may be higher. Additional equipment such as post-weld cleaning gas is required when welding certain materials such as aluminum.
Inverter power supply:
Performance characteristics: The inverter power supply converts the input AC power into high-frequency AC power, and then converts it into the required DC power. This conversion makes the welding arc more stable and control more precise.
Scope of application: Due to its high efficiency and lightweight characteristics, the inverter power supply is suitable for mobile welding and some application scenarios that require flexibility.
Advantages: small size, light weight, high efficiency, able to provide a more stable welding arc and better welding control.
Disadvantages: Typically more expensive than traditional transformer-style welders.
Dual power supply:
Performance features: Dual power supply combines the advantages of AC and DC power supplies, providing greater flexibility and applicability.
Scope of application: Suitable for a variety of welding needs, the appropriate power source type can be selected according to specific welding tasks.
Advantages: High flexibility, suitable for a variety of welding tasks.
Disadvantages: The cost may be higher, and the complexity may be higher compared to a single type of welding power source.
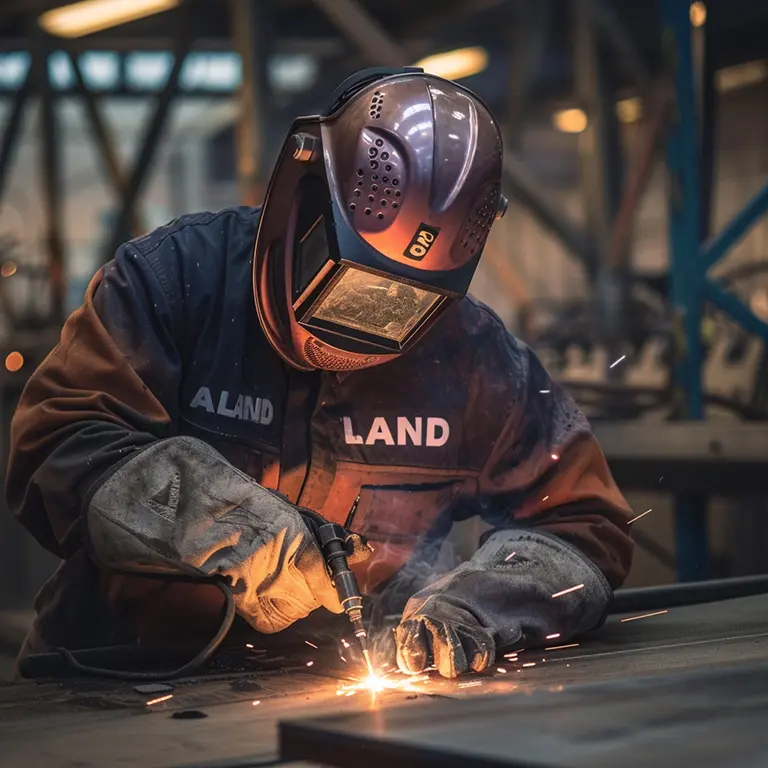
How to choose a welding power source
Choosing the right welding power source is a complex process that requires consideration of multiple factors. Here are some steps and considerations to help you choose the right welding power source for you:
Determine welding needs:
Determine the type and frequency of welding tasks you will perform. This may include things like the type, thickness and shape of the welding material.
Determine the environment in which the welding will be performed, including factors such as indoor or outdoor, mobile or fixed.
Learn about the different types of welding power sources:
Understand the characteristics, advantages, disadvantages and applicable scenarios of different types of welding power sources such as AC power supply, DC power supply, inverter power supply and dual power supply.
Consider welding materials:
If you are going to weld special materials such as aluminum or copper, you need to consider using a DC power source and may need to use additional equipment such as a high-frequency arc starting device.
For welding common metals like steel, AC power may be a more affordable option.
Consider welding quality and control needs:
If you require high-quality welding, as well as more precise welding control, a DC power supply or an inverter power supply may be a better choice.
If your welding tasks are less stringent with weld quality requirements, AC power may be a more affordable option.
Consider budget and costs:
Choose the appropriate welding power source type based on your budget constraints. Inverter power supplies are generally more expensive but may offer better performance and portability.
Consider mobility and portability:
If you need to weld in different locations, or need to work in an outdoor environment, an inverter power supply may be a more suitable option, as it is usually lighter and more portable than a traditional transformer-style welder.
Refer to professional advice:
If possible, consult a professional welding technician or welding equipment supplier to get their advice and opinions to ensure that the welding power source you choose will meet your needs and expectations.
Consider future scalability:
Consider your possible future welding needs and choose a welding power source with some scalability to meet future needs.
The difference is the applicable environment
When considering the suitability of different types of welding power sources in different environments, the following details need to be considered:
Alternating current power supply (AC):
Environmental characteristics: AC power is generally suitable for environments such as home workshops, agricultural sites, and light industrial production lines. These environments typically require lower power welding machines and simpler welding tasks such as simple metal joining and repair work.
Application scenarios: AC power supply is suitable for general home maintenance, agricultural equipment maintenance, light metal welding and other tasks. These tasks typically do not require highly precise welding control and require relatively low welding quality.
Direct current power supply (DC):
Environmental characteristics: DC power supplies are usually used in environments that require higher quality welding, such as industrial manufacturing, automobile manufacturing, shipbuilding, and aerospace industries. These environments often require high-power welding machines and have high requirements for welding quality and control performance.
Application scenarios: DC power supply is suitable for welding various materials such as steel, stainless steel, alloy steel, and applications requiring high welding quality and precise control. These tasks may involve more complex metal joining and structural welding.
Inverter power supply:
Environmental characteristics: Inverter power supplies are usually lightweight and compact, and are suitable for environments that require mobile welding or outdoor work. These environments often require portability and flexibility, such as construction sites, outdoor maintenance sites, etc.
Application scenarios: Inverter power supply is suitable for mobile welding, outdoor maintenance and welding tasks in compact spaces. Due to its portability and high efficiency, inverter power supplies have high applicability in these scenarios.
Dual power supply:
Environmental features: Dual power supply combines the advantages of AC and DC power, with greater flexibility and applicability. These environments usually need to adapt to situations with different welding requirements, such as industrial production lines, professional maintenance services, etc.
Application scenarios: Dual power sources are suitable for a variety of welding needs. The appropriate power source type can be selected according to specific tasks, providing greater flexibility and adaptability. These tasks may involve welding multiple materials as well as situations that require movement and adjustment in different environments.
When selecting a welding power source, factors such as the characteristics of the welding task, required welding materials, quality requirements, working environment, and personal budget should be fully considered. It is also important to seek advice from a professional or welding equipment supplier. The final choice of welding power source should be able to meet your needs, provide high-quality welding results, and provide you with reliable performance and convenient operation over the long term. With careful consideration and selection, you will be able to find the best welding power source for you to achieve your welding goals and job needs.
Articles you may be interested in:
Introduction To Welding Pad Process
How To Choose Industrial Water Chiller
The Important Role Of Welding Positioners
Introduction To 1G To 6G Welding Positions
Underwater Welding Salary And Death Rate
Introduction To Common Welding Techniques
MIG Welding Machine And Process Introduction
MMA Welding Machine Introduction And Process
Tig Welding Welding Machine And Process Introduction
Different Weldings Are Suitable For Different Welding Consumables