How to maintain and maintain welding equipment
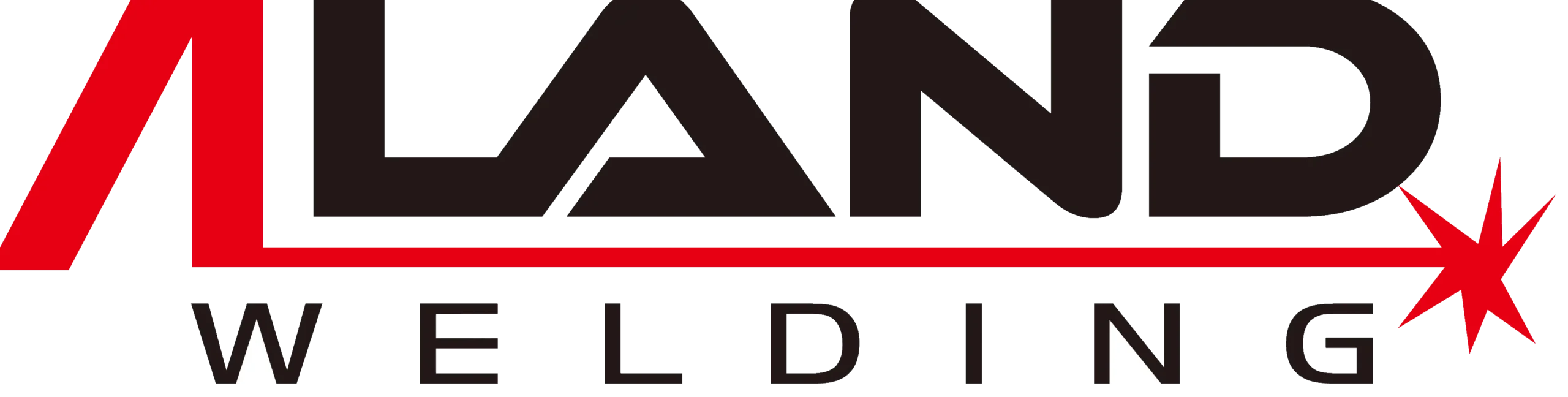
ALAND WELDING Let you feel the most sincere welding service
1. Maintenance of welding gun
(1) Regularly inspect and replace the contact tips
Due to wear and tear, the hole diameter of the contact tip becomes larger, which will cause arc instability, deterioration of the appearance of the weld or wire sticking (burnback); spatter will stick to the end of the contact tip, and the wire feeding will become uneven; the contact tip will not be tightened tightly. Threaded joints will heat up and become welded.
(2)Clean and replace spring hoses regularly
After the spring hose is used for a long time, a large amount of iron powder, dust, welding wire plating chips, etc. will accumulate, which will make the wire feeding unstable. So it is important to clean it regularly. You can curl it and tap it gently to shake off the accumulation, and then blow it away with compressed air. Use a brush to wash the grease on the hose in the oil, and then blow it away with compressed air. If the spring hose is miswired or severely deformed and bent, it must be replaced with a new hose. When replacing the pipe, make sure it is suitable for the diameter and length of the welding wire used, and there should be no burrs on the cut surface.
(3)Inspection of insulating ferrules
If the insulating ferrule is removed for welding, the spatter will adhere to the inside of the nozzle, causing the nozzle to be connected to the live part. The welding gun may be burned due to short circuit. At the same time, in order to make the protective gas flow out evenly, an insulating ferrule must be installed.


2. Maintenance of wire feeding device
(1)Adjust pressure
The wire feed roller pressure should be adjusted appropriately according to the diameter of the welding wire used. If the pressure is insufficient, the welding wire will slip; if the pressure is too high, the welding wire will be scratched and deformed. If flux cored wire is used, the pressure applied by the wire feed wheel is smaller than that of solid cored wire.
(2)Adjustment of welding wire straightening device
The adjustment method of the welding wire straightening device varies depending on the model. It should be adjusted to the appropriate position for the corresponding welding wire diameter according to the manufacturer’s instructions.
(3)Installation of welding wire reel
If the installation is not in place, the wire spool may fall off during rotation, causing serious consequences. Be careful to check whether the brake block or latch is reliably installed.
(4)Wire feed wheel and the diameter of the welding wire used
The wire feed roller must be installed suitable for the diameter of the welding wire used, and check whether the number engraved on the roller matches the diameter of the welding wire used.
(5)Wear and contamination of wire feed roller grooves
Check whether the groove of the wire feed roller is worn, whether the groove surface is scratched, whether dust, iron powder, welding wire plating chips, etc. are adhered to the groove. When cleaning, wipe it with a cotton gauze rag.
(6)Inspection of guide wire nozzle
If the wire guide nozzle installed at the front and rear of the wire feed roller is worn or not level with the wire feed roller. It will cause the welding wire to bend and the wire feed to be unstable. Therefore, it must be inspected and repaired regularly.
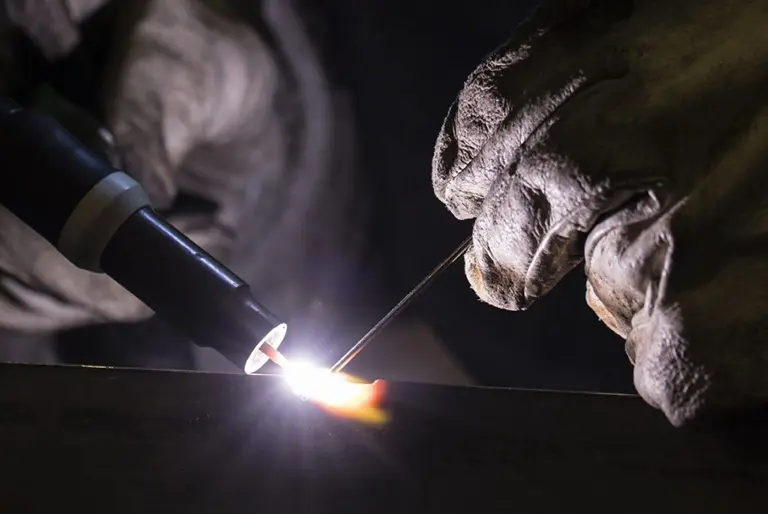

3. Maintenance of welding machine
First of all, special attention needs to be paid to the fact that when inspecting the internal or external connector terminals of the welding machine, the input power switch must be turned off before proceeding.
(1)Carry out regular inspections.
For example, check whether the cooling fan rotates smoothly when the welding machine is powered on; whether there is abnormal vibration, sound and smell; whether there is gas leakage; whether the joints of the welding wire and the insulation wrapping are loose or peeling; whether the welding cables and other Check whether there is any abnormal heating in the wiring area, etc.
(2)Remove accumulated dust regularly
Since the welding machine is forced air-cooled, it is easy to inhale dust from the surroundings and accumulate inside the machine. Therefore, we can regularly use clean and dry compressed air to blow away the dust inside the welding machine. In particular, parts such as transformers, reactor coils, gaps between coil windings, and power semiconductors must be specially cleaned.
(3)Regularly check the wiring locations of power wiring
Check whether the wiring screws on the input side, output side terminals, as well as the wiring parts of external wiring, the wiring parts of internal wiring, etc. are loose. If there is rust, remove the rust to make the contact conductive well.
(4)Regularly replace machine parts
Long-term use of the welding machine will inevitably cause the shell to be deformed due to collision, rust and damage, and the internal parts will also wear away. Therefore, during annual maintenance and inspection, defective parts must be replaced, the shell repaired, and the insulation deteriorated parts must be repaired. Comprehensive repair work such as reinforcement. When replacing defective parts during maintenance, it is best to replace them with new ones at once to ensure the performance of the welding machine.
The above-mentioned regular maintenance and inspection can reduce the occurrence of welding failures. Although it takes some time and effort, it can extend the life of the welding machine, improve the efficiency of the operation, ensure the performance of the welding machine and improve safety. It is an important content that cannot be ignored in welding work.
Articles you may be interested in:
Detailed Explanation Of Spot Welding Process
Why choose TIG welding? 4 major benefits
Introduction to TIG welding and basic operating procedures
Welding, Pressure Welding And Brazing Welding Process
The Difference Between ARC Welding Machine and Electric Welding Machine
Primary wire, secondary wire, welding wire, ground wire, ground wire
How to distinguish between welding slag and molten iron during welding?
Welder skills and knowledge: What basic knowledge do beginners need to master?