Common weld on metal
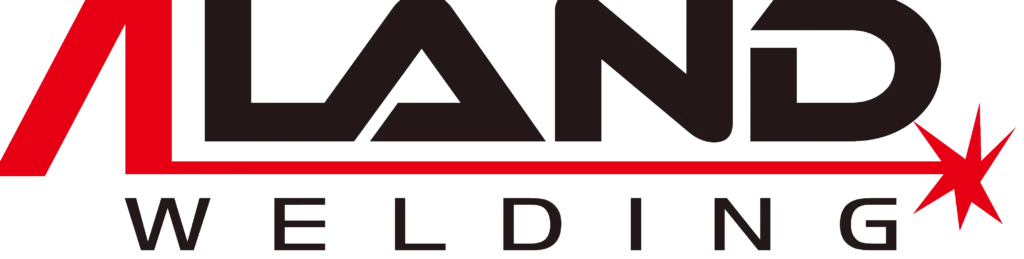
ALAND WELDING Let you feel the most sincere welding service
weld on metal is crucial in real life. It is the cornerstone of manufacturing, construction, transportation, energy industry and many other fields. Through welding technology, various metal components can be connected to build various important facilities and products such as automobiles, aircraft, and building structures. The application of welding metals not only promotes the development and progress of industrial production, but also provides key support for the maintenance and repair of existing equipment, making an important contribution to the sustainable development of society.
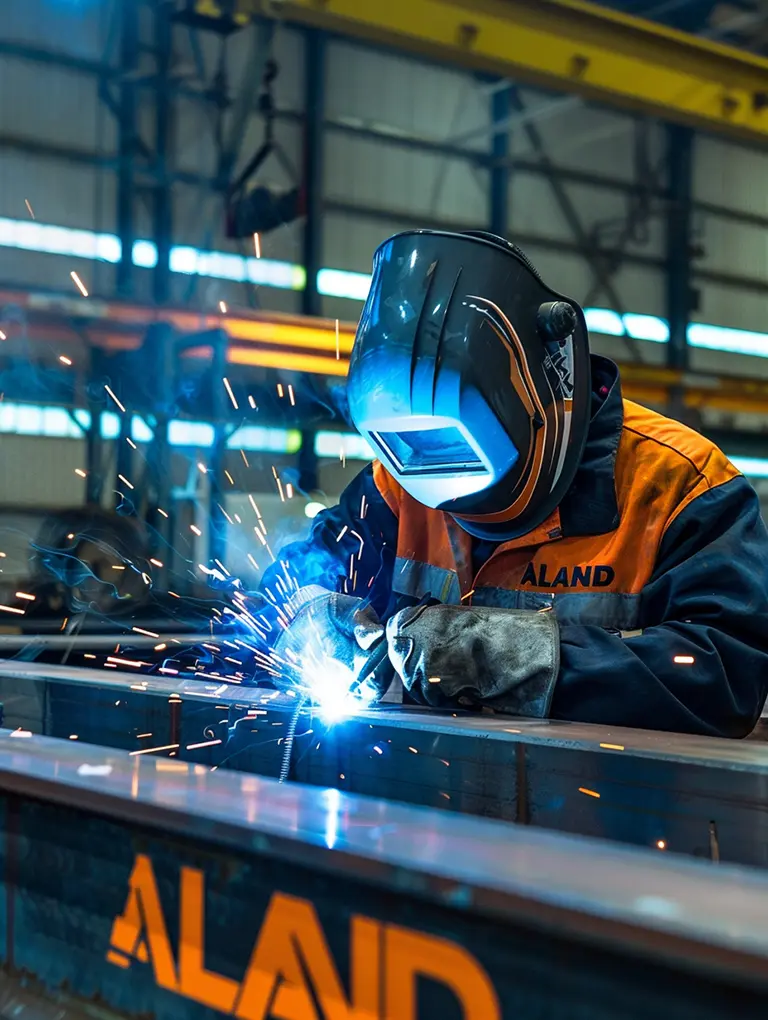
1. Common weld on metal
(1) Carbon steel: Carbon steel is one of the most common weld on metals and is widely used in the manufacturing and construction industries. It can be connected through various welding methods, such as arc welding, gas shielded welding, etc.
(2) Stainless steel: Stainless steel is corrosion-resistant and high-temperature resistant and is often used in food processing, chemical industry, medical equipment and other fields. Stainless steel can be welded by TIG welding, MIG welding and other methods. It is necessary to pay attention to controlling the welding temperature and gas protection.
(3) Aluminum alloy: Aluminum alloy is lightweight and has good thermal conductivity, and is often used in aerospace, automobile manufacturing and other fields. Aluminum alloys can be welded by TIG welding, MIG welding and other methods, but attention needs to be paid to the oxidation of aluminum, and special gas protection and pretreatment methods are usually required.
(4) Copper: Copper has good electrical and thermal conductivity and is often used in electronic devices, pipelines and other fields. Copper can be welded by gas shielded welding, resistance welding and other methods, but care must be taken to avoid oxidation.
(5) Titanium alloy: Titanium alloy has high strength and corrosion resistance and is often used in aerospace, medical equipment and other fields. Titanium alloys are usually welded using TIG welding and other methods, which require strict gas protection and preheating measures.
(6) Nickel alloy: Nickel alloy has good high temperature resistance and corrosion resistance and is often used in chemical industry, energy and other fields. Nickel alloys can be welded by TIG welding, MIG welding and other methods, but attention must be paid to controlling the welding temperature and gas protection to avoid the formation of pores and cracks.
The above are some common weld on metals. Of course, there are other types of metal materials. Each material may require specific welding methods and process parameters. Before welding, it is necessary to fully understand and prepare the weld on metal to ensure the quality and performance of the welded joint.
2. weld on metal process
(1) Electrode arc welding
Welding rod arc welding is a process that uses a stable burning arc established between the welding rod and the workpiece to melt the welding rod and the workpiece to obtain a strong welding joint. During the welding process, the coating continuously decomposes and melts to generate gas and slag, protecting the end of the welding rod, the arc, the molten pool and its surrounding areas, and preventing harmful pollution of the molten metal from the atmosphere. The core of the welding rod also continuously melts under the action of arc heat, enters the molten pool, and forms the filler metal of the weld.
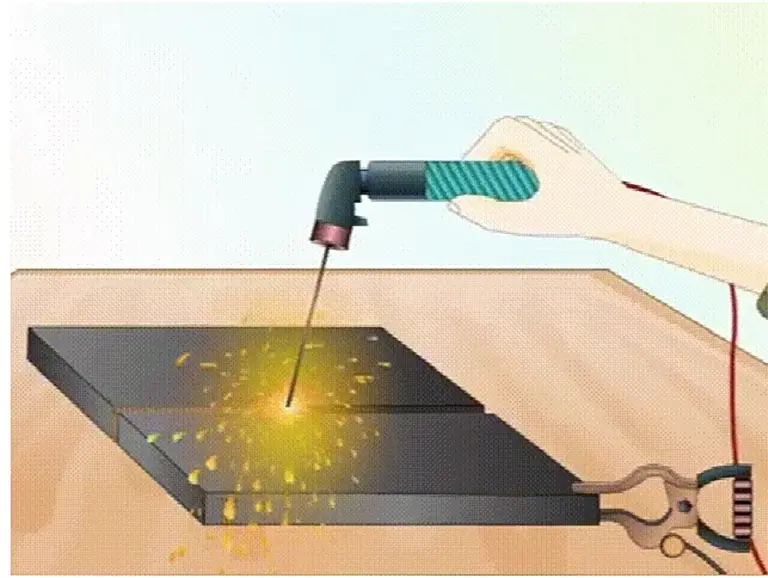
(2) Submerged arc welding
Submerged arc welding (including submerged arc surfacing and electroslag surfacing, etc.) is a method in which the arc burns under the flux layer for welding. Its inherent advantages of stable welding quality, high welding productivity, no arc light, and little smoke make it the main welding method in the production of important steel structures such as pressure vessels, pipe sections, and box beams and columns.
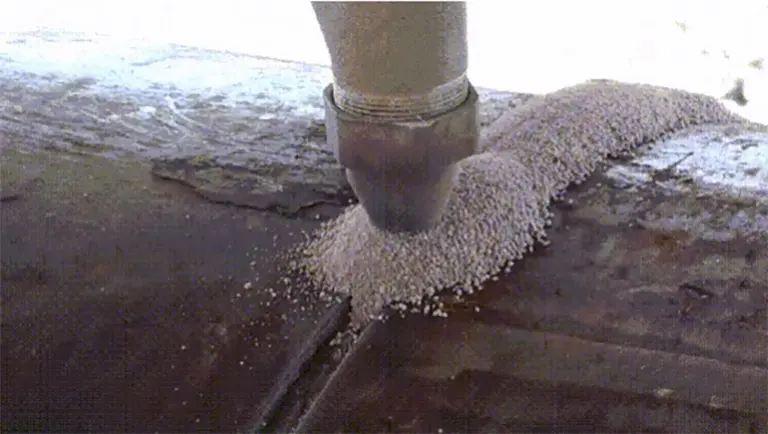
(3) Argon arc welding
Argon arc welding is a welding technology that uses argon as a protective gas. Also called argon gas shielded welding. It is to pass argon protective gas around the arc welding to isolate the air from the welding area and prevent oxidation of the welding area.
Argon arc welding technology is based on the principle of ordinary arc welding, using argon gas to protect metal welding materials, and using high current to melt the weld on metal on the base material to be welded into a liquid state to form a molten pool, making the metal to be welded A welding technology that achieves a metallurgical combination with the welding material. Since argon gas is continuously supplied during high-temperature molten welding, the welding material cannot come into contact with oxygen in the air, thus preventing the oxidation of the welding material. Therefore, stainless steel and iron can be welded Hardware metal.
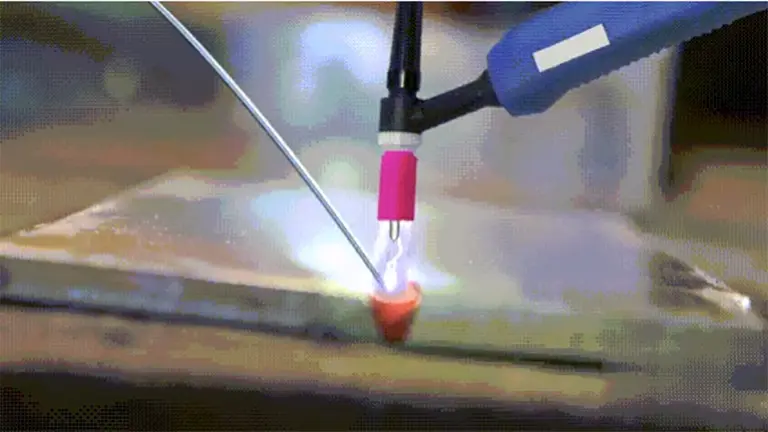
(4) Gas welding
oxygen fuel gas welding (OFW for short). A welding method that uses the flame generated by the mixed combustion of combustible gas and combustion-supporting gas as a heat source to melt the weldment and welding materials to achieve interatomic bonding. The combustion-supporting gas is mainly oxygen, and the combustible gas mainly uses acetylene, liquefied petroleum gas, etc.
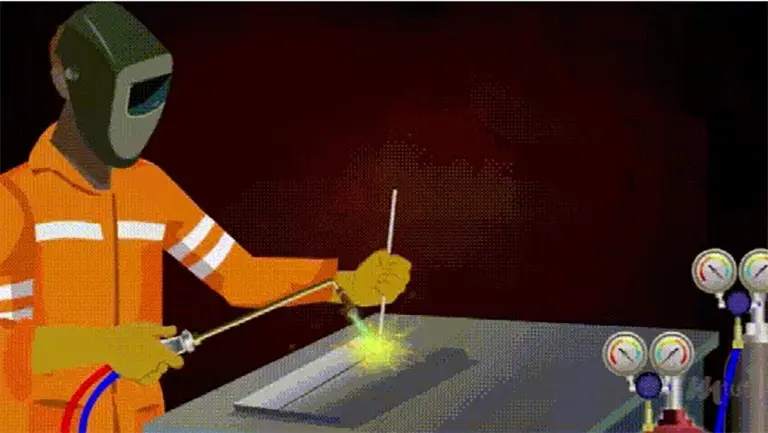
(5) Laser welding
Laser welding is a method of welding using the heat generated by bombarding the weldment with a focused laser beam as an energy source. Because laser has optical properties such as refraction and focusing, laser welding is very suitable for welding micro parts and parts with poor accessibility. Laser welding also has the characteristics of low heat input, small welding deformation, and is not affected by electromagnetic fields.
Due to the expensive price of lasers and low electro-optical conversion efficiency, laser welding has not been widely used.
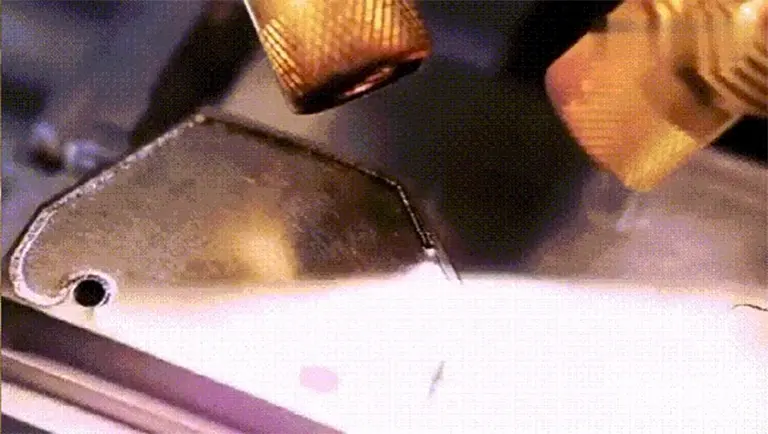
(6) Secondary protection welding
The secondary welding (full name carbon dioxide gas shielded welding) process is suitable for the welding of various large-scale steel structures of low carbon steel and low alloy high-strength steel. It has high welding productivity, good crack resistance, small welding deformation, and can adapt to a wide range of deformation. Welding thin and medium-thick plates.
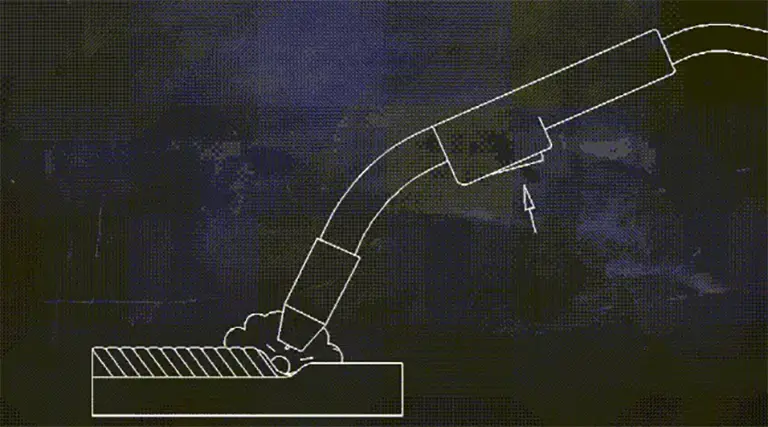
(7) Friction welding
Friction welding refers to a method of welding by using the heat generated by friction on the contact surface of the workpiece as a heat source to cause plastic deformation of the workpiece under pressure.
Under the action of pressure, under the action of constant or increasing pressure and torque, the relative motion between the welding contact end surfaces is used to generate friction heat and plastic deformation heat on the friction surface and its nearby areas, causing the temperature of the friction surface and its nearby areas to rise to In the temperature range close to but generally lower than the melting point, the deformation resistance of the material decreases, the plasticity increases, and the oxide film at the interface is broken. Under the action of the upsetting pressure, the material undergoes plastic deformation and flow, and occurs through molecular diffusion and recrystallization at the interface. Solid state welding method to achieve welding.
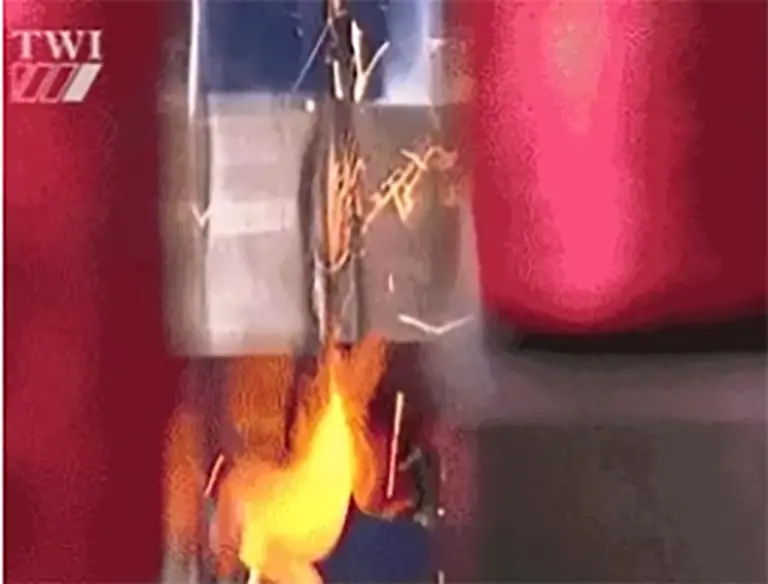
(8) Ultrasonic welding
Ultrasonic welding uses high-frequency vibration waves to transmit to the surfaces of two objects to be welded. Under pressure, the surfaces of the two objects rub against each other to form fusion between the molecular layers.
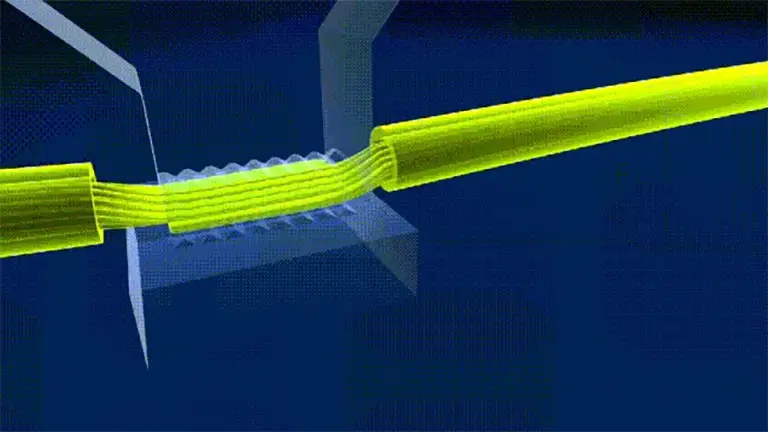
(9) Soft soldering
Soldering is a type of connection method that uses solder with a melting point not exceeding 450°C and is heated to a soldering temperature lower than the melting point of the base metal and higher than the melting point of the solder. The solder is spread on the closely fitting connection surface by capillary action or on the workpiece surface by wetting.
Solder is a soldering material whose liquidus temperature (melting point) does not exceed 450°C. Solder is usually an alloy that does not contain iron. The temperature of 450°C is the dividing point between brazing and soldering. Most of the process parameters and influencing factors involved in brazing are also applicable to soft soldering. In fact, industrial terms such as soldering, brazing or silver soldering are also used to distinguish between soft soldering and brazing.
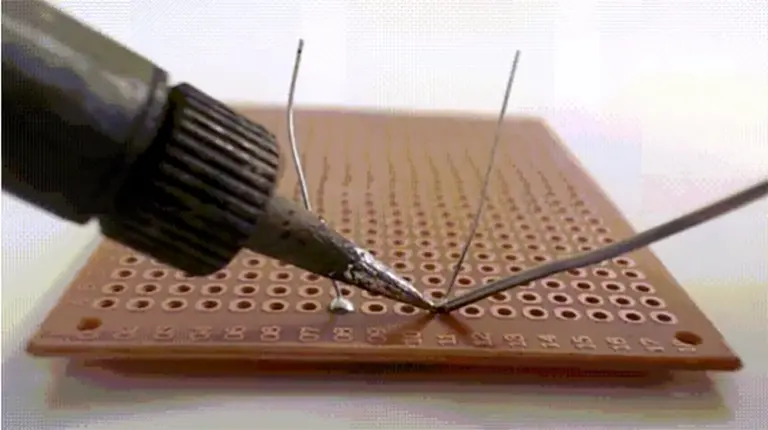
(10) Brazing
Brazing is a high-temperature brazing process. Most brazing temperatures are between 1200 and 1400F° (much higher than soft soldering, but much lower than fusion welding). Like soft soldering, brazing relies on capillary action to fill the joint with solder. There are many different types of braze alloys that can be used to weld almost any kind of metal or metal alloy.
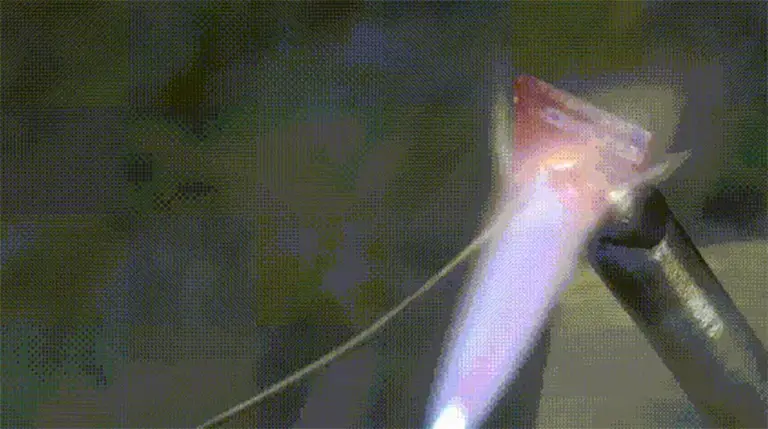
3. Application of weld on metal
(1) Carbon steel:
Manufacturing industry: Carbon steel is one of the most common weld on metals and is widely used in the manufacturing industry to manufacture various structural parts, mechanical parts, tools, etc. For example, carbon steel is commonly used for welding in car body structures, gears in mechanical equipment, and brackets in factory buildings.
Construction Industry: In the construction industry, carbon steel is used to make building structures, bridges, pipes, etc. Welded carbon steel components can build a stable building frame and support structure to ensure the stability and safety of the building.
(2) Stainless steel:
Food processing industry: Stainless steel has excellent corrosion resistance and hygiene, and is widely used in the food processing industry to manufacture food containers, transportation pipelines, etc. Welded stainless steel components ensure hygienic safety during food processing.
Chemical industry: In the chemical industry, stainless steel is used to manufacture chemical equipment, reactors, storage tanks, etc. to withstand corrosion and high temperatures from chemical substances. Welded stainless steel components ensure the stability and durability of the equipment.
(3) Aluminum alloy:
Aerospace industry: Aluminum alloys are lightweight and high-strength and are often used in the manufacture of aerospace devices. For example, aircraft fuselages, wing spars, spacecraft shells, etc. can all be welded with aluminum alloys to reduce weight and improve flight performance.
Automotive industry: In the automotive industry, aluminum alloys are used to manufacture car bodies, engine parts, etc. Welding aluminum alloy components can reduce the overall weight of the car and improve fuel economy and driving performance.
(4) Copper:
Electronics industry: Copper has excellent electrical and thermal conductivity and is widely used in the electronics industry to manufacture cables, wires, electronic devices, etc. Soldering copper components ensures efficient transmission and stable performance of electronic devices.
Construction Engineering: In construction engineering, copper is often used to make pipes, roof coverings, etc. Welded copper components ensure the durability and waterproofing of the building structure.
(5) Titanium alloy:
Medical devices: Titanium alloys are widely used in the field of medical devices due to their biocompatibility and high strength. For example, medical devices such as artificial joints and implants are often welded with titanium alloys to ensure their durability and safety.
(6) Nickel alloy:
Energy industry: Nickel alloys have the characteristics of high temperature resistance and corrosion resistance, and are widely used in the energy industry to manufacture nuclear power equipment, petrochemical equipment, etc. Welded nickel alloy components ensure stable operation of equipment in extreme environments
4. Future trends of weld on metal
Welding metal materials will continue to play an important role in the future. With the advancement of science and technology and innovation of processes, welding technology will become more intelligent, efficient and environmentally friendly. The future development trends of welding metal materials include but are not limited to: the widespread application of intelligent welding equipment, such as the development of automated welding systems and robot welding technology; the development of new welding materials, such as those with higher strength, lower cost, and better reliability. Sustainable metal materials; and optimization and precision of welding processes to improve welding quality and efficiency and reduce environmental impact. As these development trends advance, welded metal materials will continue to play an important role in various fields and promote sustainable social and economic development.
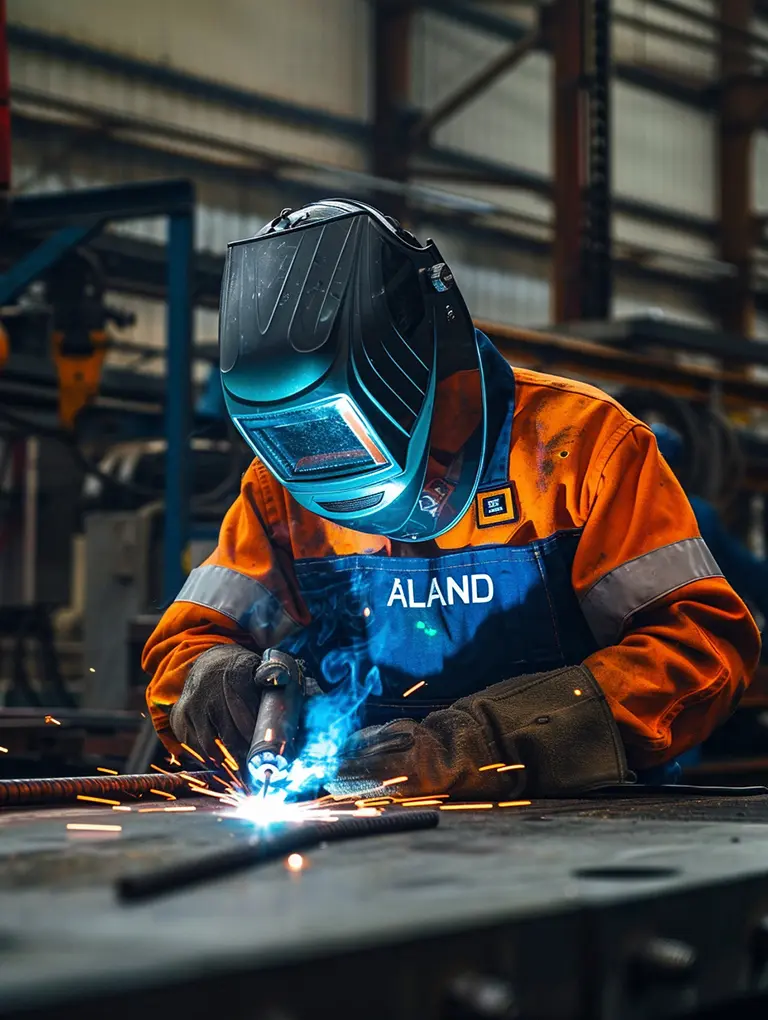
weld on metal plays a vital role in modern society. From manufacturing to construction, from transportation to the energy industry, welded metal materials are widely used in a variety of fields. Common metal materials such as carbon steel, stainless steel, aluminum alloy, and copper, as well as special metal materials such as titanium alloy and nickel alloy, all play an important role in the field of welding. In the future, welding technology will face the development trend of intelligence, efficiency and environmental protection, including the application of intelligent welding equipment, the development of new welding materials, and the optimization and precision of welding processes. As these trends advance, weld on metals will continue to play a key role in various fields and promote sustainable development and progress of social economy.
Articles you may be interested in:
Different Welding Power Sources
Introduction To Welding Pad Process
How To Choose Industrial Water Chiller
The Important Role Of Welding Positioners
Introduction To 1G To 6G Welding Positions
Underwater Welding Salary And Death Rate
Introduction To Common Welding Techniques
MIG Welding Machine And Process Introduction
MMA Welding Machine Introduction And Process
Tig Welding Welding Machine And Process Introduction
Different Weldings Are Suitable For Different Welding Consumables