Common weld aluminum introduction
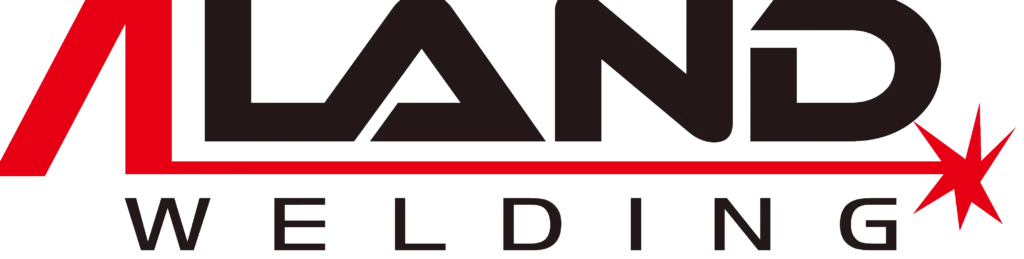
ALAND WELDING Let you feel the most sincere welding service
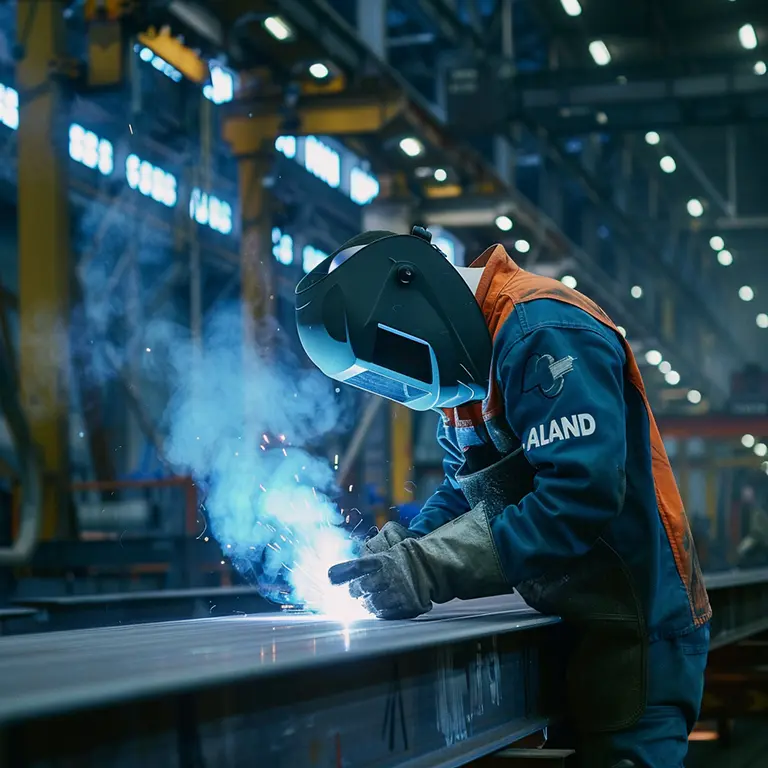
Welded aluminum is a process in which aluminum and its alloys are heated to their melting point and joined with other aluminum or non-aluminum materials. Aluminum can be welded using a variety of methods, including TIG (Tig Welding), MIG (Gas Metal Arc Welding), brazing, resistance welding, and laser welding, among others. Selecting the appropriate welding method depends on the shape of the workpiece, its material, the required welding quality, and production requirements. During the weld aluminum process, due to aluminum’s high thermal conductivity and high thermal shrinkage, special welding techniques and alloys are usually required to ensure the quality and stability of the weld.
1.weld aluminum technology
(1) Resistance welding
weld aluminum alloy resistance butt welding (spot welding) can generally only be used for overlapping welding of plates with a thickness of less than 5mm, or overlapping welding of rods with a thickness of less than 10mm. The advantages are low welding cost, high welding efficiency, and easier to integrate into automated production lines. For example, it is widely used in automobile manufacturing. The limitation is that the thickness that can be welded is limited, and different electrodes must be made for different products and structures.
(2) Argon arc welding
Manual tungsten arc welding is mainly used to weld aluminum alloy thin plate (thickness < 6mm) structures. Due to the protective effect of argon gas and the crushing effect of argon ions on the oxide film of aluminum alloy, argon arc welding does not require welding powder, thereby avoiding corrosion of the joints by post-weld residues. Therefore, there is no need to clean up after argon arc welding. The joint form Can also be unlimited. In addition, the flushing of the welding area by the argon gas flow during welding can significantly cool the welded joint, thus improving the structure and performance of the joint and reducing the deformation of the weldment.
(3) Gas shielded welding
It is generally difficult to master the single-sided and double-sided forming of gas-shielded aluminum alloys. If there is a gap between the butt plates, it will be easy to weld through. The back penetration of the weld without leaving a gap is difficult to control. Domestic welding of aluminum alloys generally uses AC argon arc welding, but for thicker plates, the efficiency of argon arc will be very low. Currently, in some examination projects, melting electrode pulse gas shielded aluminum alloy welding is used. Moreover, most of the butt plate welding is performed in the overhead welding position, which is mainly used in the welding of aluminum alloy car bodies and frames of EMUs.
(4) Friction welding
The aluminum alloy friction stir welding seam is formed through plastic deformation and dynamic recrystallization. The grains in the welding area are refined, there are no dendrites in the fusion welding, the structure is fine, the heat affected zone is narrower than that in the melting welding, and there is no burning loss of alloy elements. , cracks and pores and other defects, and the overall performance is good. Compared with traditional fusion welding methods, it has no spatter, smoke, no need to add welding wire and protective gas, and the joint performance is good. Because it is a solid phase welding process, the low heating temperature results in small welding deformation. The disadvantage is that the welding speed is slow and the process is not mature enough.
(5) Gas welding
The thermal power of the oxygen-acetylene gas welding flame is low and the heat is relatively dispersed, so the weldment deforms greatly and the productivity is low. Preheating is required when welding thicker weld aluminum ments with gas welding. The weld metal after welding not only has coarse grains and loose structure, but is also prone to defects such as aluminum oxide inclusions, pores and cracks. This method is only used for welding repair of unimportant aluminum structural parts and castings with thickness ranging from 0.5 to 10mm.
(6) Laser welding
Aluminum alloy laser welding technology is a new technology developed in the past decade. Compared with traditional welding processes, it has the characteristics of strong function, high reliability, no need for vacuum conditions and high efficiency. It has the characteristics of high power density, low total heat input, large penetration depth for the same heat input, small heat affected zone, small welding deformation, high speed, and easy industrial automation. The disadvantage is that it cannot absorb all the energy when welding aluminum alloys. This results in a lot of waste and high equipment procurement costs.
(7) Melting electrode argon arc welding
The arc power of automatic and semi-automatic fusion electrode argon arc welding is large, the heat is concentrated, the heat affected area is small, and the production efficiency can be increased by 2 to 3 times compared with manual tungsten electrode argon arc welding. It can weld pure aluminum and aluminum alloy plates with thickness below 50mm. For example, there is no need to preheat when welding an aluminum plate with a thickness of 30mm. Only the front and back layers can be welded to obtain a smooth surface and high-quality weld. Semi-automatic argon arc welding is suitable for positioning welds, intermittent short welds and weldments with irregular structural shapes. The semi-automatic argon arc welding torch can be used for convenient and flexible welding, but the diameter of the welding wire for semi-automatic welding is thin. Welds are more sensitive to pores.
(8) Pulse argon arc welding
①. Tungsten pulse argon arc welding
This method can significantly improve the stability of the low-current welding process, and facilitate the control of arc power and welding seam formation by adjusting various process parameters. The weldment has small deformation and small heat-affected zone. It is especially suitable for thin plates, all-position welding and other occasions, as well as the welding of forged aluminum, hard aluminum, super hard aluminum, etc. that are highly sensitive to heat.
③. Resistance spot welding, seam welding
It can be used to weld aluminum alloy sheets with a thickness of less than 4mm. For products with higher quality requirements, DC shock wave spot welding and seam welding machines can be used. Welding requires the use of more complex equipment, with large welding current and high productivity. It is especially suitable for mass-produced parts and components.
④. Friction stir welding
Friction stir welding is a solid-state joining technology that can be used to weld various alloy plates. Compared with traditional fusion welding methods, friction stir welding has no spatter, no smoke, no need to add welding wire and protective gas, and the joints have no pores or cracks. Compared with ordinary friction, it is not limited by shaft parts and can weld straight welds. This welding method also has a series of other advantages, such as good mechanical properties of the joint, energy saving, no pollution, and low pre-welding preparation requirements. Due to the low melting point of aluminum and aluminum alloys, friction stir welding is more suitable.
2. Precautions for weld aluminum
(1) Pay attention to choosing a better voltage when welding.
During welding, the size of the base, filling, cover, and groove must not be selected at the same arc voltage. This may easily lead to insufficient penetration depth and width, as well as defects such as undercuts, pores, and flying particles. . Generally, the corresponding long or short welds should be selected for different conditions to obtain better welding quality and work efficiency. For example, when backing welding, the arc voltage should be increased to 7 to obtain better penetration. During fill welding or cover welding, the arc voltage can be appropriately increased in order to obtain higher efficiency and melting width.
(2) Welding requires controlling the welding current.
If the progress of the welding process is 7 and the butt weld of medium and thick plates is not grooved, the strength will decrease, making it fail to meet the standard requirements, and cracks will appear during the bending test, which will affect the performance of the weld joint. It cannot be guaranteed and may pose a potential hazard to structural safety.
When welding, the welding current should be controlled according to the process qualification. 1O~1 is allowed. Therefore, the blunt edge size of the floating φ groove should not exceed 6m. When butt jointing, when the plate thickness exceeds 6m, the groove must be opened for welding.
(3) Pay attention to the coordinated use of welding speed, welding current, and electrode diameter.
Attention should be paid to the coordinated use of welding speed, welding current, and electrode diameter. For example, when performing bottom welding on a fully penetrated corner seam, due to the narrow root size, if the welding speed is too fast, the root gas and slag inclusions will not have enough time to be discharged. It is easy to cause defects such as incomplete penetration, slag inclusions, and pores at the root; during cover welding, if the welding speed is too fast, pores are also likely to occur; if the welding speed is too slow, the weld reinforcement will be too high and the appearance will be irregular; welding When welding a thin plate or a blunt edge with a small size, the welding speed is too slow and burn-through is prone to occur.
Welding speed has a significant impact on welding quality and welding production efficiency. When using the welding table, the welding current, welding seam position (bottom welding, filling welding, cover welding), welding seam thickness, and groove size should be selected appropriately. On the premise of ensuring penetration, easy discharge of gas and welding slag, no burn-through, and good formation, use a higher welding speed to improve productivity.
(4) Pay attention to controlling the arc length when welding.
When welding, the arc length should be adjusted appropriately according to the groove form, number of welding layers, welding form, electrode model, etc. If the welding arc length is used improperly, it will be difficult to obtain a high-quality weld.
In order to ensure the quality of the weld, short welding operations are generally used during welding. However, appropriate welding lengths can be repeatedly used according to different paving conditions to obtain better welding quality, such as V-shaped groove butt joints and corner joints. The first layer should use a shorter arc to ensure penetration without undercutting. The second layer can be slightly longer to fill the box weld. 6 A short arc should be used if the weld gap is small. If the gap is large, the arc can be slightly longer. Longer, the welding speed speeds up. The arc for overhead welding should be the shortest to prevent the molten iron from flowing down; in order to control the temperature of the molten pool during vertical and horizontal welding, small current and short arc welding should also be used. 6 In addition, no matter what kind of welding is used, during the movement Pay attention to always keep the length of the weld unchanged to ensure that the penetration width and depth of the entire weld are consistent.
(5) Pay attention to controlling welding deformation when welding.
When welding, do not pay attention to controlling the deformation from the welding sequence, personnel arrangement, groove form, welding specification iteration and operation method, etc., resulting in large deformation after welding, difficulty in car alignment, and increased cost◊Especially for thick plates and Large workpieces are difficult to correct. Mechanical correcting can easily cause cracks or lamellar cracks. Flame correcting is expensive and can easily cause overheating of the workpiece due to poor operation. For workpieces with high precision requirements, effective control of deformation should be adopted. Otherwise, the installation size of the workpiece will not meet the usage requirements, and even the workpiece or report will use the bench-buried welding sequence and override the bench-appropriate welding specifications and operations. Methods include anti-deformation and rigid fixation measures.
(6) In multi-layer welding, attention should be paid to continuous welding and the temperature between layers should be controlled.
When welding multi-layer thick plates, pay attention to the temperature control between layers. If the interval between layers is too long, do not reheat. Welding will easily cause cold cracks between layers; if the interval is too short, the temperature between layers will be too high. (exceeding 90trc) will also have an impact on the performance of the weld and the heat-affected zone, causing coarse grains, resulting in reduced toughness and plasticity, and leaving potential hidden dangers in the joints. It should be inspected during the continuous welding process. The temperature of the base metal for welding should be kept consistent with the preheating temperature as much as possible. The higher temperature between layers should also be controlled. The welding time should not be too long. In case of inertia where welding is interrupted, measures should be taken. Appropriate post-heating and insulation pinching are performed. When welding again, the re-preheating temperature should be appropriately higher than the initial preheating temperature.
(7) The welding seam needs to be cleaned of welding slag and defects before proceeding to lower layer welding.
When multi-layer welding of thick plates, the welding slag and defects will not be removed after each layer is welded. The lower layer welding will easily cause defects such as slag inclusions, pores, cracks, etc. in the weld, which will reduce the connection strength and cause Flying iron when welding the lower layer. When welding thick plates in layers, each layer should be welded continuously. After welding, the welding slag, weld surface defects and debris should be promptly removed after each layer of welding. If any slag inclusions, pores, etc. that affect the welding quality are found, Defects such as cracks should be completely removed before welding.
(8) Pay attention to the size of the welding legs of the joint weld.
For butt or angle butt assembly welds that require penetration, such as shaped pinch joints, +-shaped joints, corner joints, etc., the size of the weld mesh i0 is insufficient, or the web and upper wing of a crane beam or similar component designed with fatigue verification requirements If the size of the welding hole i0 of the plate mirror connection weld is not enough, the strength and stiffness of the welding will not meet the design requirements. Butt assembly welds that require penetration, such as shaped pinch joints, +-shaped joints, corner joints, etc., should be in accordance with the design requirements and must have sufficient welding mesh i0 requirements. Generally, the welding mesh i0 size should not be less than 0.25t (t is The thinner plate thickness at the connection) ◊The leg size of the weld connecting the crane beam or similar web plate and the upper wing mirror that has fatigue verification requirements is designed to be 0.5t, and should not be greater than 10 m ◊The allowable difference in welding size is 0~4 mm
(9) Pay attention if there are welding rod heads or iron blocks stuck in the gap of the joint.
Since it is difficult to fuse the electrode head or iron block with the workpiece to be welded during welding, it will cause welding defects such as unmelted platform and insufficient penetration, resulting in low connection strength. If filled with rusty electrode head or iron block, it will be difficult to Ensure that the material is consistent with the base material; if filled with welding rod tips or iron blocks containing oil, impurities, etc., the weld will produce defects such as pores, slag inclusions, cracks, etc. ◊These inert conditions will greatly improve the quality of the joint’s weld It is too low to meet the design and specification requirements for weld quality. In order to meet the standard weld quality requirements, there are mesh bars to solve the following problems: (1) When the assembly gap of the workpiece is large, but does not exceed the allowed range of use, and the assembly gap exceeds 2 times the thickness of the plate or is greater than 20m , use the surfacing method to fill the concave PS parts or small assembly gaps ◊ It is strictly prohibited to use filling in the joint gap; the method of repair welding with headers or iron blocks ◊ (2) When processing and marking parts, attention should be paid to leaving enough cutting margin and The welding shrinkage after cutting should be controlled. Control the size of the parts and do not add gaps to ensure the outer dimensions.
(10) When plates of different thicknesses are butted together, gentle over-processing is required.
When using plates of different thicknesses and widths to butt together, pay attention to whether the thickness difference of the plates is within the allowable range of the standard. If it is not within the allowable range and does not make a smooth transition, the weld will easily cause stress concentration and generation at the point higher than the thickness of the thin plate. Welding defects such as lack of fusion affect the welding quality. When the relevant regulations are exceeded, the weld should be welded into a slope, and the maximum allowable slope value should be 1: 2.5; or the thickness side or the mesh surface should be processed into a slope before welding, and the maximum allowable slope value should be 1: 2.5 , when the structural slope is connected to bear dynamic load and is subject to fatigue check, the slope should not be greater than 1: 4 ◊When plates of different widths are butted together, thermal cutting, mechanical processing or grinding wheel grinding should be used to make them smooth according to factory and construction site conditions. transition, and the maximum allowable slope value of its connection is 1: 2.5»n.
(11) Pay attention to the welding sequence of components with intersecting welds.
For components with cross welds, if we do not pay attention to arrange the welding sequence by analyzing the welding stress SM and the influence of welding stress on the shape of the component, but weld randomly vertically and horizontally, the result will be that the vertical and horizontal seams are mutually constrained, resulting in larger Temperature shrinkage stress causes the board to deform, make the board surface uneven, and may cause cracks in the welds. For components with cross welds, a buried welding sequence should be formulated. When there are several vertical and horizontal cross welds to be welded, the transverse seams with larger shrinkage and deformation should be welded first, and then the longitudinal welds, so that the transverse welds are welded. The seam will not be constrained by the longitudinal weld, so that the shrinkage stress of the transverse seam can be released without restraint, which can reduce the welding deformation and ensure the quality of the weld, or weld the butt weld first and then the fillet weld.
3. Weld aluminum scene
(1) Automobile manufacturing industry:
Welding is usually performed in specialized workshops at automobile manufacturing plants.
The environment may include welding workstations, welding equipment (such as TIG or MIG welding machines), ventilation systems to control welding fumes and odors, and other ancillary equipment such as welding jigs and workpiece handling equipment.
(2) Aerospace industry:
Welding may be performed in a dedicated workshop at an aerospace manufacturing facility.
Due to the precision and safety requirements of aerospace components, the welding environment may be subject to more stringent controls, including stricter environmental conditions, stricter quality control, and higher-level welding processes.
(3) Building and structural engineering:
Welding can be performed indoors or outdoors, depending on the needs of the specific structural project.
Indoor welding may be performed in a dedicated welding shop with appropriate ventilation and gas extraction systems to control fumes and odors generated during the welding process.
(4) Electronic product manufacturing:
Welding is typically performed in a welding shop within an electronics manufacturing plant, which may be separated from other production lines to ensure that the welding process is not affected by other manufacturing steps.
Welding equipment and environments may need to meet specific electronics manufacturing standards to ensure product quality and safety.
(5) Food and medical equipment:
Welding is often performed in hygienic environments, such as in factories where medical devices or food processing equipment are manufactured.
Welding equipment and the environment need to be cleaned and disinfected regularly to ensure that the welding process does not affect the health and safety of the final product.
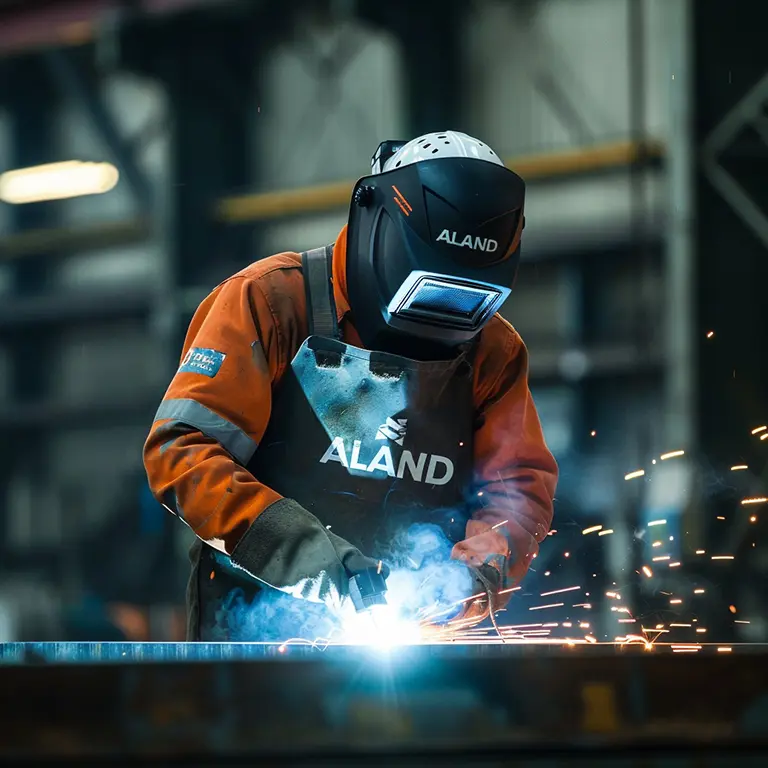
In the wide application environment of aluminum welding, we have witnessed the key role of this technology in various fields. However, as technology continues to develop and its application scope expands, we are also facing new challenges and opportunities.
The continuous improvement of weld aluminum technology, including innovations in welding equipment, welding processes and material science, will bring broader development space to the future manufacturing industry. As the demand for lightweight and high-strength materials continues to increase, aluminum welding technology will continue to play an important role in fields such as automotive, aerospace, construction, electronics, and medical devices.
At the same time, we should also be aware that we need to continue to pay attention to environmental protection and safety issues during the weld aluminum welding process. Effective exhaust gas treatment systems, sound safety management measures, and personnel training and skills improvement will be the key to ensuring safe and reliable aluminum welding work.
Therefore, we are full of confidence in the future of welded aluminum technology and believe that with continuous innovation and efforts, aluminum welding will continue to bring more efficient, more reliable and more sustainable solutions to various industries, and promote the development and development of manufacturing industry. Make greater contributions to progress.
Articles you may be interested in:
Different Welding Power Sources
Introduction To Welding Pad Process
How To Choose Industrial Water Chiller
The Important Role Of Welding Positioners
Introduction To 1G To 6G Welding Positions
Underwater Welding Salary And Death Rate
Introduction To Common Weld Stainless Steel
Introduction To Common Welding Techniques
MIG Welding Machine And Process Introduction
MMA Welding Machine Introduction And Process
Tig Welding Welding Machine And Process Introduction
Different Weldings Are Suitable For Different Welding Consumables