Introduction to spot welding - basics
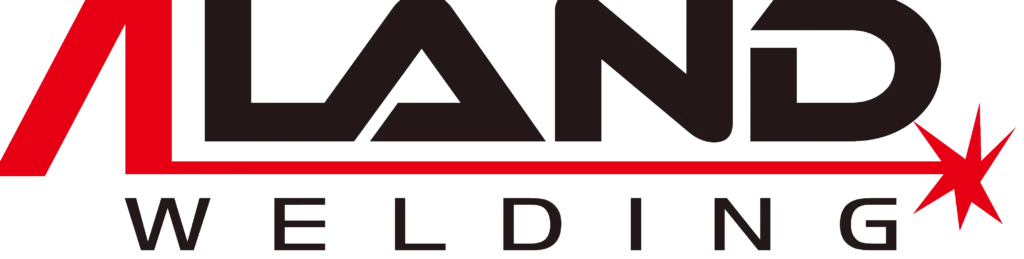
ALAND WELDING Let you feel the most sincere welding service
1. Introduction to resistance spot welding
Resistance spot welding has the characteristics of low energy consumption, low cost, high quality, high efficiency, easy automation and easy use. No consumables, no need for welding rods, welding wires, flux, etc.; the welding process consumes little heat, no smoke and other harmful substances, no dazzling light pollution, and the working voltage is only a few volts. It is a safe, economical, efficient, reliable, and pollution-free method. Environmentally friendly welding method.
Resistance spot welding mainly adopts welding methods such as double-sided single-point welding, double-sided double-point welding, single-sided single-point welding, single-sided multi-point welding, and double-sided multi-point welding. The size and strength of the welding spots are mainly affected by factors such as electrode diameter, welding current and welding time, electrode pressure, current shunt and other factors.
2. Basic principles of resistance spot welding
Resistance spot welding applies and maintains a certain pressure on the workpiece to be welded through the spot welding electrode. Make stable contact between the workpieces. Then the current output by the welding power source generates heat through the workpieces to be welded and their contact surfaces, raising the temperature, melting the contact points locally to form solder joints, and achieving the purpose of welding the metal workpieces together.
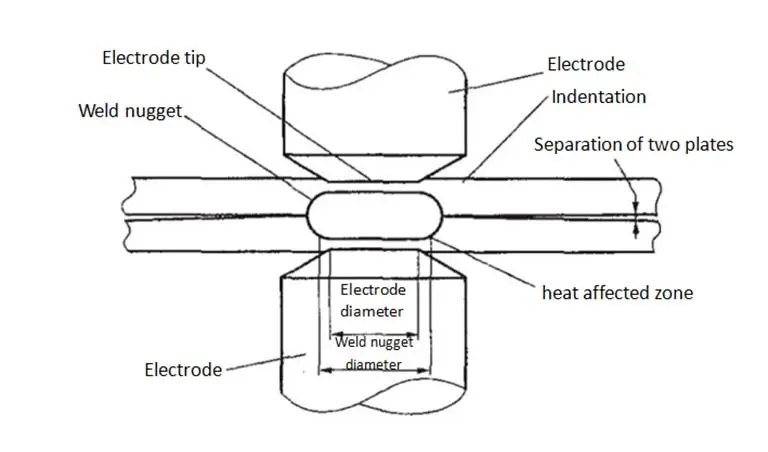
Spot welding structure and heat distribution characteristics diagram
During the resistance spot welding process, the formation process of the solder joint must be divided into 3 consecutive stages:
The first stage – pre-pressure stage. Closely contact the welding point of the workpiece to ensure the required contact resistance.
The second stage – the electric heating stage. The current passes through the workpiece squeezed between the electrodes, generating heat, and the workpiece is heated to a molten state to form a nugget. Due to the small current passing through the metal outside the nugget, a plastic ring is formed surrounding the nugget, which affects the strength of the solder joint.
The third stage – cooling crystallization stage. After the solder joint melts and nucleates, it is accompanied by considerable shrinkage during the cooling and crystallization process. At this stage, the pressure on the electrode must be delayed to release, so that the solder joint can obtain a denser crystal structure under the action of electrode pressure before it is completely cooled. .
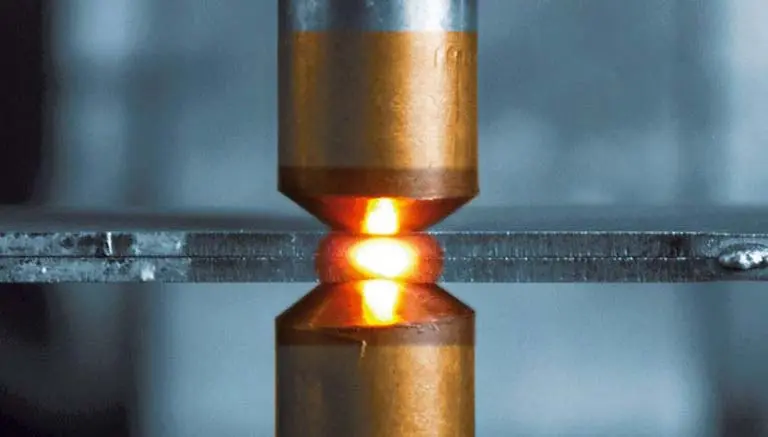
3. Selection of resistance spot welding electrodes
Electrodes have three main functions:
a. Keep current density balanced
b. .Concentrate the current at the solder joint;
c. Maintain heat balance during welding.
d. Correctly select the spot welding electrode. Make sure the electrode is in contact with the workpiece
Good spot welding quality can only be ensured by matching materials. There are also many kinds of electrode shapes, and the commonly used ones are R type, P type, F type and CF type.
The material and shape of the electrode depend on the required pressure, the thermal conductivity of the workpiece to be welded, and the welding process requirements. The most common electrode materials are chromium copper, tungsten, tungsten and platinum. The characteristics of different electrode materials are shown in the table below.
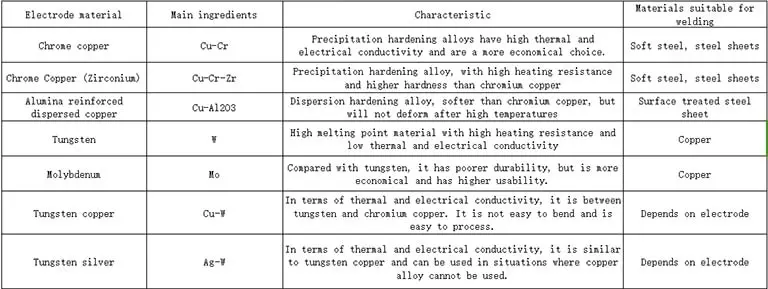