Introduction to pulse welding technology
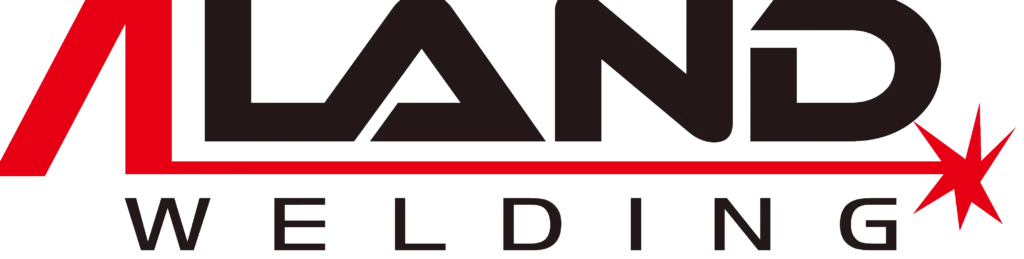
ALAND WELDING Let you feel the most sincere welding service
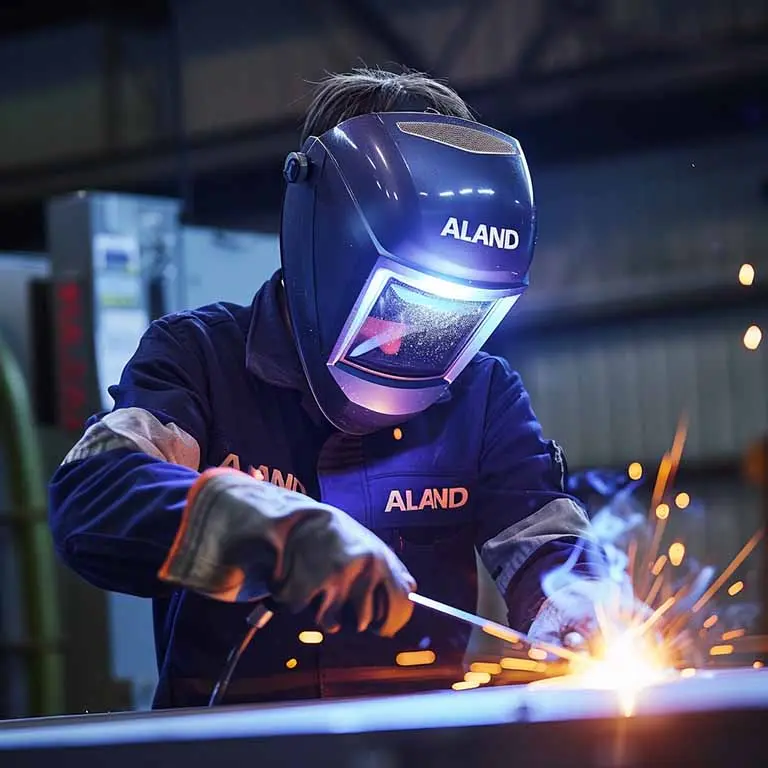
1. What is pulse welding?
Pulse welding is an advanced welding technology that uses periodic pulse current or pulse energy to complete the welding process. This technology offers greater precision and control than traditional continuous current or energy transmission, and is therefore widely used in a variety of industrial fields.
In pulse welder, welding current or energy is delivered to the welding area in a series of short pulses. These pulses can be adjusted in time and amplitude as needed to achieve precise control of the welding process. A typical pulse welder process consists of two main stages: a high peak current or energy stage and a maintenance current or energy stage. During the high peak stage, the current or energy is increased to a level sufficient to instantly melt the welding material to form a weld pool. During the maintenance phase, lower current or energy is maintained in the welding area to maintain the stability and consistency of the welded joint.
The advantages of pulse welder include its precise control of the welding process and reduction of heat input. By adjusting pulse parameters, welding engineers can precisely control every aspect of the welding process, including welding depth, welding speed and weld quality. In addition, because pulse welder only delivers high energy for a brief period of time, the overall heat input is lower, which reduces deformation and heat-affected zones in the weld area, resulting in higher quality welds.
Due to its excellent performance, pulse welding has become the welding process of choice in many industries. In the automobile manufacturing industry, pulse welding is widely used to weld automobile bodies and chassis to achieve high strength and durability. In the aerospace field, pulse welder can be used to weld aircraft structures and engine components to ensure their safety and reliability. In addition, in fields such as electronic equipment manufacturing and metal processing, pulse welder is also widely used to weld electronic components and precision parts to meet high-quality and high-efficiency production needs.
2. Advantages of pulse welding
(1) Precise control: Pulse welding allows precise control of welding parameters, including pulse width, frequency, peak current, etc. This precision ensures stability and consistency in the welding process, resulting in higher quality welds.
(2) Low heat input: Since pulse welding only transmits high energy for a short period of time, the overall heat input is low. Compared with continuous current welding, this low heat input helps reduce the deformation of the welding area and the spread of the heat-affected zone, thereby improving the quality and accuracy of the welded joint.
(3) Reduce welding deformation: Low heat input and precise control enable pulse welding to better control the temperature distribution in the welding area and reduce the occurrence of welding deformation. This is particularly important for welding tasks that require a high degree of precision and shape retention.
(4) Wide applicability: Pulse welding is suitable for various metal materials and thicknesses, as well as a variety of welding positions and conditions. It can be used to weld common metals such as steel, aluminum, copper, and can also be used to weld non-metallic materials such as plastics and ceramics.
(5) High efficiency: Due to the precise control of the welding process and low heat input, pulse welder is usually able to achieve higher production efficiency. Welding speed can be increased while maintaining welding quality and stability, saving time and costs.
(6) Suitable for automation: Pulse welder technology can be easily integrated into automated welding systems. By using robots or automated equipment, a highly automated welding production line can be achieved to improve production efficiency and consistency.
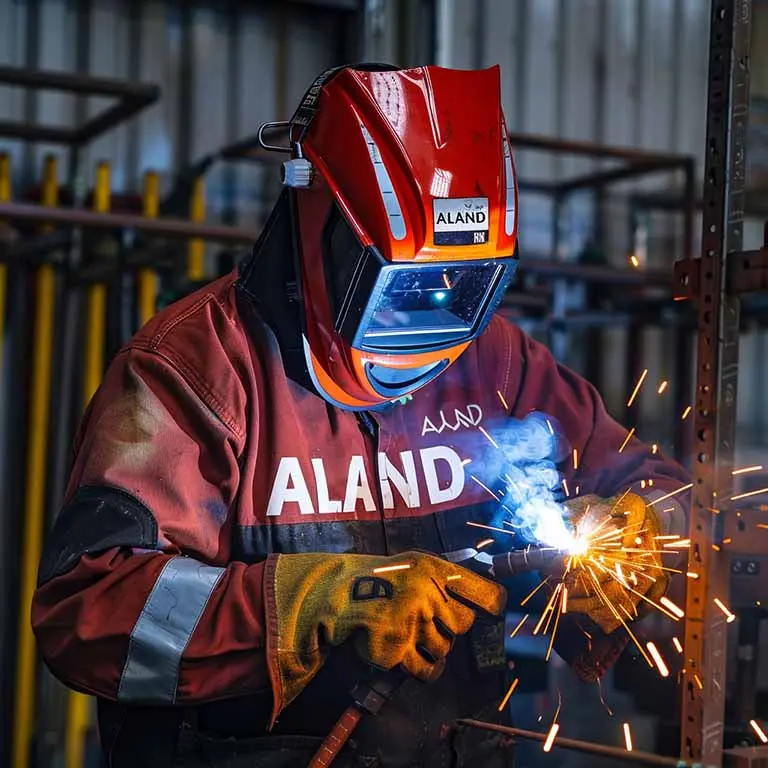
3. Defects of pulse welder
(1) Equipment costs are high: The equipment required for pulse welding usually includes advanced control systems, high-performance power supplies and special welding guns or welding heads. The cost of these devices is relatively high, making the initial investment larger.
(2) Complex operating technical requirements: pulse welder requires operators to have a high technical level and professional knowledge. Operators need to understand and be proficient in the adjustment and control of welding parameters, as well as appropriate welding techniques and operating procedures. Wrong settings or operations may result in reduced welding quality or welding defects.
(3) Slow welding speed: Pulse welding usually requires the application of high energy in an instant to melt the welding material, and then maintain the welding at lower energy. This welding process is relatively slow, resulting in low welding speeds and may not be suitable for situations where high throughput and rapid production are required.
(4) Welding material limitations: Although pulse welder is suitable for a variety of metal materials, not all materials are suitable for this welding method. Some special materials or alloys may have more stringent heat input and control requirements for pulse welder, and may require other types of welding methods to meet the needs.
(5) Welding gas requirements: Pulse welding usually requires the use of inert gas as a protective gas to prevent oxidation and the generation of pores. This increases welding costs and requires additional gas supply and handling equipment. At the same time, if the gas supply is insufficient or the gas flow is unstable, the welding quality may be affected.
(6) Complex welding process: The welding process of pulse welder is relatively complex and requires more adjustment and optimization in welding parameters and control. This may require more time and resources for research and development to ensure welding quality and stability, increasing the complexity and difficulty of the welding process.
4. Metal welding materials suitable for pulse welding
(1) Carbon steel: Carbon steel is one of the most common metal materials and is widely used in many industries, including automobile manufacturing, construction, and machinery manufacturing. Pulse welding is suitable for welding carbon steel and can achieve molten pool control, heat input control and optimization of weld morphology. This control helps reduce the deformation of the welding area and the spread of the heat-affected zone, ensuring welding quality and stability.
(2) Stainless steel: Stainless steel has good corrosion resistance and mechanical properties and is widely used in food processing, chemical industry and other fields. Pulse welder can be used for welding stainless steel. By adjusting the pulse parameters, the oxidation and grain growth during the welding process can be effectively controlled to maintain the quality and appearance of the weld.
(3) Aluminum alloy: Aluminum alloy is commonly used in aerospace, automotive manufacturing, construction and other fields. Its high thermal conductivity and low melting point make the welding process more challenging. Pulse welder is suitable for welding aluminum alloys, which can increase the welding speed and make the weld clearer, while reducing the occurrence of pores and cracks.
(4) Copper and copper alloys: Copper has good electrical and thermal conductivity and is widely used in electronics, electrical and communications fields. Pulse welder can effectively control the heat input and heat distribution during the welding process to ensure the quality and stability of the weld. It is suitable for welding tasks of copper and copper alloys.
(5) Other metals: In addition to the common metal materials mentioned above, pulse welding is also suitable for other metals, such as nickel, titanium, magnesium, etc. The welding of these metal materials usually requires high welding quality and stability, and pulse welder technology can meet these requirements and improve production efficiency and welding quality.
5. Precautions for pulse welder
(1) Familiar with equipment operation: Before performing pulse welder, the operator should fully understand the operating manual and relevant safety instructions of the welding equipment. Ensure a clear understanding of the equipment’s operating methods and parameter settings.
(2) Accurately adjust welding parameters: According to the welding task and material characteristics, accurately adjust the parameters of pulse welder, including pulse width, frequency, peak current and reference current, etc. Correct parameter settings are crucial to obtain good welding quality.
(3) Keep the welding area clean: Before welding, make sure the surface of the welding area is clean and remove any dirt, oxides or coatings that may affect the quality of the weld.
(4) Select appropriate welding materials: Select appropriate welding materials and filling materials according to specific welding requirements. Different materials may require different welding parameters and welding methods.
(5) Appropriate welding position and angle: Select the appropriate welding position and angle according to the welding task and the geometry of the workpiece. Make sure the welding gun or tip has full access to the welding area and maintains a proper welding gap.
(6) Maintain a stable welding power supply: Ensure that the power supply of the welding equipment is stable and avoid the impact of power supply fluctuations or interference on the welding quality.
(7) Pay attention to gas protection during the welding process: For welding processes that require protective gas, ensure a stable gas supply, and adjust the gas flow and gas type as needed.
(8) Regular inspection and maintenance of equipment: Regular inspection and maintenance of welding equipment, including welding guns, cables, gas pipelines and power systems, etc., to ensure their normal operation and safety.
(9) Pay attention to safety during welding: When performing welding operations, always follow welding safety regulations, including wearing personal protective equipment, preventing fire and explosion hazards, and ensuring that the surrounding environment is well ventilated.
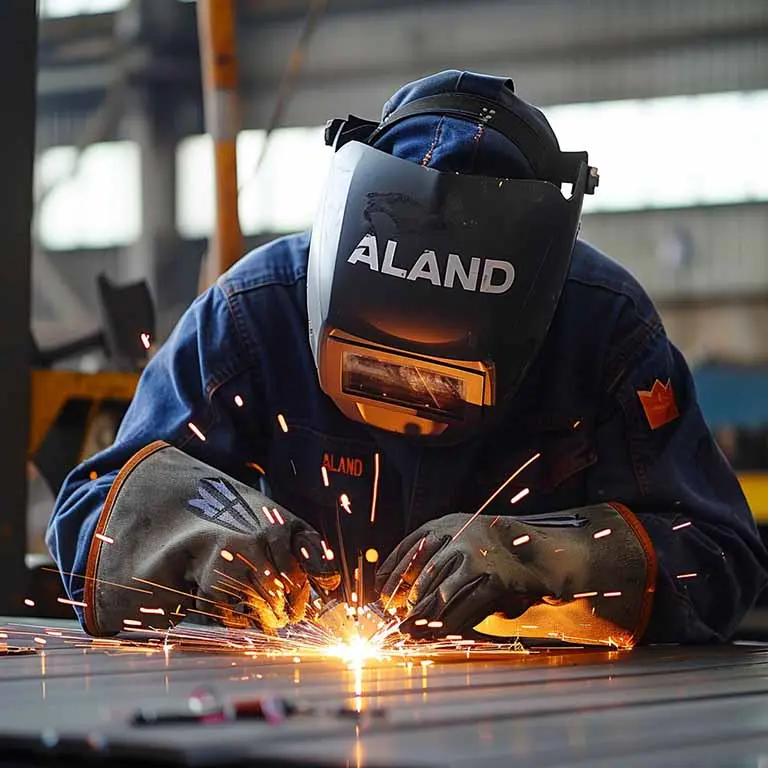
6. Recommended machines for pulse welding
ALAND brand pulse welder machines are also well received in the market. Known for their versatile styles and reliable performance, they are the first choice of many welding professionals and industrial manufacturing companies.
ALAND brand pulse welder machines are available in various models and specifications to meet the needs of different users. Whether it is a task with high requirements on welding accuracy, welding speed or welding quality, ALAND can provide suitable solutions. Its products are well designed, have advanced control systems and stable performance, ensuring the stability and consistency of the welding process.
In addition to reliable performance, ALAND pulse welder machines also focus on appearance design and user-friendly operation interface. They have diverse appearance styles, simple and elegant designs, and are easy to operate and maintain. Whether it is a modern industrial production line or personal use, ALAND brand pulse welder machines can provide excellent welding experience and high production efficiency.
In general, ALAND brand pulse welder machines are known for their diverse styles, reliable performance and excellent user experience. Whether in industrial production or personal use, they are a trustworthy choice.
Among welding processes, pulse welder, as an advanced technology, provides important solutions for various industrial applications. Through periodic pulse current or energy transmission, pulse welder achieves precise control of the welding process while reducing heat input, thereby reducing welding deformation and thermal effects. This article provides readers with a comprehensive understanding by exploring the concepts, advantages, applicable metals, disadvantages, and considerations of pulse welder.
The advantages of pulse welder are its precise control, low heat input, reduced deformation, wide applicability and high efficiency. However, it is also necessary to realize that there are some challenges in pulse welder, such as higher equipment costs, higher operating technical requirements, and slower welding speeds. When performing pulse welder, operators need to fully understand important matters such as equipment operation, precise adjustment of parameters, and keeping the welding area clean to ensure welding quality and safety.
In short, the continuous development and application of pulse welding technology will further promote the advancement of welding processes and provide more reliable and efficient welding solutions for various industrial fields. By deeply understanding pulse welder technology and combining it with practical application needs, its advantages can be maximized and bring more innovation and progress to the production and manufacturing fields.