Introduction To No Gas Welder And Gas Welder (2)
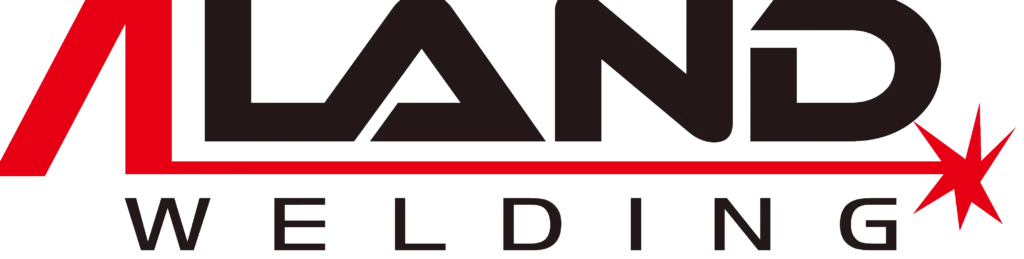
ALAND WELDING Let you feel the most sincere welding service
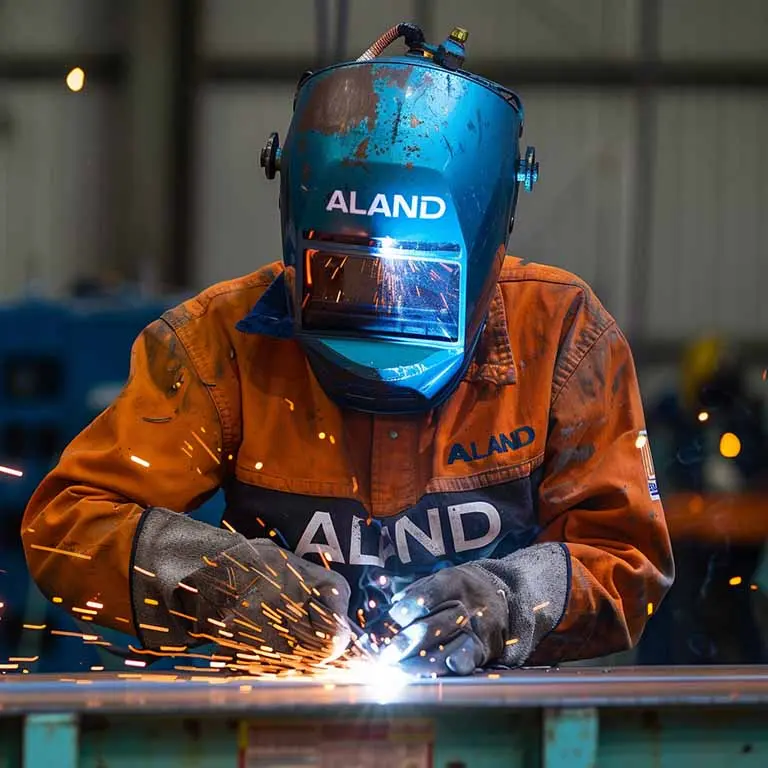
The main difference between a gas welder and a gasless welder is whether gas protection is used during the welding process.
Gas welder: gas welder uses shielding gas during the welding process. This gas is usually carbon dioxide, argon, or a mixture of the two. The main function of the gas is to protect the welding area from oxidation and pollution in the atmosphere and ensure welding quality and strength. Common types of gas welding machines include gas shielded welding machines (MIG, MAG, TIG, etc.).
Gasless welding machine: Gasless welding machine does not use external gas protection during the welding process. Instead, it relies on a special flux core or flux in the self-shielding wire to protect the weld area from oxidation. This kind of welding machine is usually suitable for outdoor use or in environments with poor ventilation. It is more convenient to use because it does not require additional gas bottles and related equipment.
This article mainly introduces readers to what is a self-shielded welding machine:
1. The concept of self-shielding welding machine
The self-shielded welding machine is a kind of welding equipment that uses flux-cored welding wire for welding without the need for external shielding gas. The flux core creates a protective layer during welding to prevent the welding area from coming into contact with air. This makes the self-shielded welding machine suitable for welding outdoors and in windy environments, because it is not affected by airflow, does not require additional gas equipment, and is easy to operate. It is commonly used in construction, manufacturing, repair and other fields, and is especially suitable for portability and flexibility in welding tasks.
2. Structural principle of self-shielding welding machine
Welding wire is also called tubular welding wire and flux-cored welding wire. The outer sheath is made of low carbon steel or low alloy steel and contains a flux core. The self-protection effect is achieved by relying on the protective effect of the slag-forming agent and gas-generating agent in the core and the nitrogen-fixing protective effect of alloy elements (Al, Ti, etc.) that can fix nitrogen. During welding, the meltable tubular wire serves as one pole and the base metal serves as the other pole. Under the action of arc heat, the molten flux material, wire metal, base metal and shielding gas interact metallurgically with each other to form a weld. Equipment includes welding power supply, wire feeding device, welding gun, etc. Working parameters include arc voltage, welding current, wire diameter, wire extension length, wire feeding speed, etc.
3. Advantages of self-shielding welding machine
(1) No external protective gas is required: The flux-cored wire used in the self-shielded welding machine will produce a layer of self-protecting gas and slag layer during the welding process to form welding protection. This eliminates the need for additional protective gas systems such as carbon dioxide or argon. Therefore, this welding machine can maintain stable welding quality outdoors and in windy environments, and is not affected by wind or airflow.
(2) Portability and ease of use: Since it does not need to be equipped with bulky gas bottles and complex piping systems, self-shielded welding machines are more lightweight and portable. They are ideal for field work, outdoor welding, and remote location welding needs. At the same time, it is simple to operate and does not require adjustment of gas flow or pressure, making it suitable for less experienced welders.
(3) Flexibility and versatility: Self-shielded welding machines can weld a variety of materials, including carbon steel, low alloy steel, etc., and are suitable for workpieces of different thicknesses. This makes it widely used in construction, maintenance, manufacturing and piping construction.
(4) High cost-effectiveness: Since no shielding gas is required, the self-shielded welding machine reduces operating costs during use. In addition, it is relatively simple to set up and maintain, reducing training and maintenance costs. Because there are no protective gas bottles and related equipment, the cost of the entire system is relatively low.
(5) Suitable for harsh environments: The design of the self-shielded welding machine enables it to maintain stable performance in harsh working environments, especially when it is outdoors, windy or with limited conditions. This property makes it ideal for construction sites, farms and other outdoor situations.
(6) Reduce environmental pollution: The self-shielded welding machine generates relatively less smoke and waste gas during the welding process because it does not rely on external shielding gas. It reduces the emission of harmful gases such as carbon dioxide and has less impact on the environment.
(7) Suitable for emergency and temporary repairs: Due to the portability and ease of operation of the self-shielded welding machine, it is particularly suitable for emergency repairs or temporary welding work. Whether it is an emergency on the construction site or emergency repair of outdoor equipment, the self-shielding welding machine can be put into use quickly.
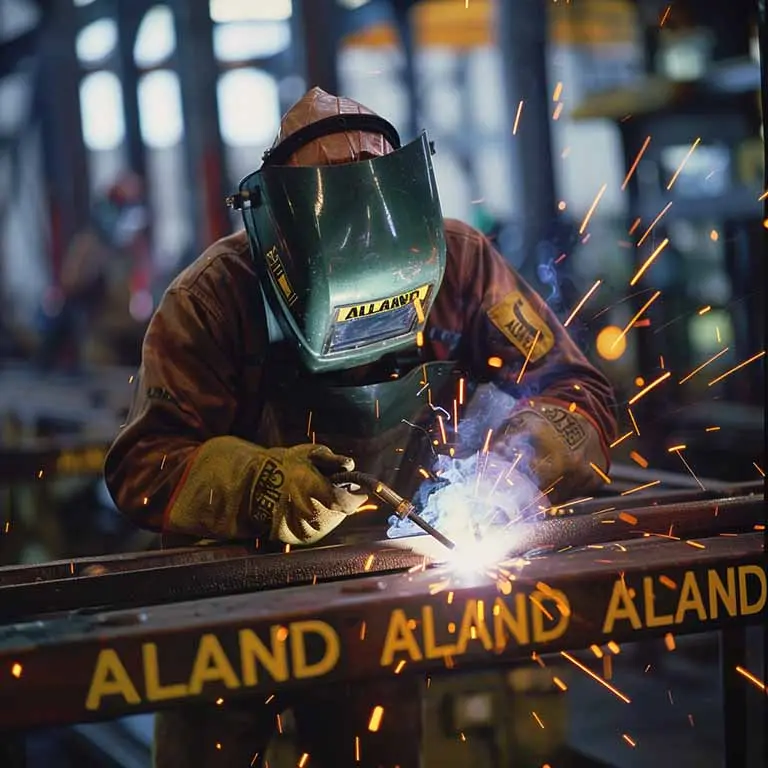
4. Disadvantages of self-shielding welding machines
(1) No external protective gas required:
Self-shielded welding machines use self-shielded flux cored wire, which generates shielding gas and slag layer through the internal flux core during welding. This eliminates the need for external shielding gas, so the welding equipment is smaller and less complex.
(2) Portability and lightweight:
Since there is no need for additional gas bottles and related piping, self-shielded welders are usually lighter and easier to carry. This feature makes them excellent in situations where mobility is required, such as construction sites, farms or outdoor repairs.
(3) Easy to operate and set up:
The operation of the self-shielded welding machine is relatively simple and does not require additional gas adjustment devices. You only need to connect the power supply and welding wire to start welding. This is very friendly to inexperienced welders and reduces the risk of operational errors.
(4) Versatility and wide application:
Self-shielded welding machines are suitable for welding a variety of materials, including carbon steel, low alloy steel, etc. It can also handle materials of varying thicknesses, from thin plates to thicker steel. This versatility makes it suitable for use in a variety of fields including construction, maintenance, manufacturing, plumbing and farm equipment.
(5) Low operation and maintenance costs:
Operation and maintenance costs are lower as gas bottles and related equipment are not required. At the same time, the structure of the welding machine is relatively simple, reducing the complexity of maintenance and repairs. This means that the self-shielded welding machine remains cost-effective after long-term use.
(6) Suitable for harsh environments:
The self-shielded welding machine can maintain stable performance in harsh environments, especially outdoors or in windy locations. Because it does not rely on external gas, this welding machine has advantages in outdoor construction, field operations and other environments where gas protection cannot be used.
(7) Reduce environmental pollution:
Self-shielded welders produce relatively little smoke and harmful gases because no external shielding gas is required. Reduces the emission of carbon dioxide and other greenhouse gases and is more environmentally friendly. This is particularly important today as environmental awareness is increasing.
(8) Suitable for emergency and temporary repairs:
The portability and ease of operation of self-shielded welders make them excellent in emergency and temporary repair jobs. Whether dealing with emergencies on a construction site or repairing farm equipment in the field, self-shielded welders can be put to use quickly to help reduce downtime.

5. Precautions for self-shielding welding machines
(1) Personal protective equipment (PPE)
Welding Helmets: Choose an auto-darkening visor with the right filter to protect your eyes and face from arcing and spatter.
Goggles: Make sure your goggles meet welding safety standards to protect your eyes from splashes and debris.
Welding clothing and gloves: Wear high-temperature-resistant, flame-retardant welding clothing and gloves to avoid direct skin exposure to the welding arc and high temperature.
Earmuffs or earplugs: Use in noisy welding environments to prevent hearing damage.
(2) Ventilation and smoke exhaust in the welding area
Ventilation equipment: Ensure there is proper ventilation in the welding area and use an extraction device or fume extraction system to reduce the accumulation of smoke, dust and harmful gases.
Outdoor welding: If you are welding outdoors, pay attention to the wind direction to ensure that smoke and dust are not blown towards the operator during welding.
(3) Preparation of welding environment
Clean the work area: Make sure there are no flammable or explosive items in the welding area, and remove flammable debris, grease, paint, etc.
Provide a good work surface: The welding workbench should be stable, sturdy, and able to withstand the heat and weight of welding.
(4) Inspection and maintenance of welding equipment
Power supply and cables: Check the welding machine’s power cord, welding wire, welding gun, etc. to make sure they are not damaged or broken. Any worn parts should be replaced immediately.
Ground clamp: Make sure the ground clamp is in good contact to avoid unstable current or accidental electric shock during welding.
Welding gun and welding wire: Check whether the welding gun nozzle and welding wire are intact to ensure that there is no obstruction during welding.
(5) Correctly set welding parameters
Adjust current and voltage: Adjust current and voltage according to welding materials and wire diameter to ensure welding quality.
Welding speed and wire feed: Adjust the welding speed and wire feed speed according to the welding task to prevent welding defects.
(6) Prevent the risk of electric shock
Keep the environment dry: Make sure the welding area is free of water stains and avoid welding in humid conditions. Use insulating mats or shoes to prevent electric shock.
Use safety devices: Make sure your welder has a leakage protection device to prevent accidental electric shock.
(7) Precautions during welding
Maintain a stable welding arc: Avoid tilting the welding gun excessively or getting close to the weldment, and keep the welding action smooth and even.
Avoid excessive heating: Control the welding heat to avoid excessive welding burn-through or material deformation.
(8) Cleaning after welding
Remove welding slag: Use a slag hammer or wire brush to clean the welding slag from the weld to ensure the welding area is clean.
Check the welding quality: After welding, check whether the weld is firm and make sure there are no welding defects.
(9) Comply with the rules and regulations of welding operations
Comply with safety regulations: Ensure that welding operations comply with relevant safety standards and regulations. Different regions and industries may have different requirements.
Understand emergency measures: Be familiar with emergency fire extinguishers, first aid kits and escape routes in the welding area in case of emergencies.
(10) Training and certification
Obtain welding qualifications: Welding operators should undergo relevant training and hold a welding qualification certificate to ensure they have the necessary skills and knowledge.
Continuous education: Participate in welding safety training regularly to learn about the latest welding technology and safety standards.