Introduction to the features of multifunction welder
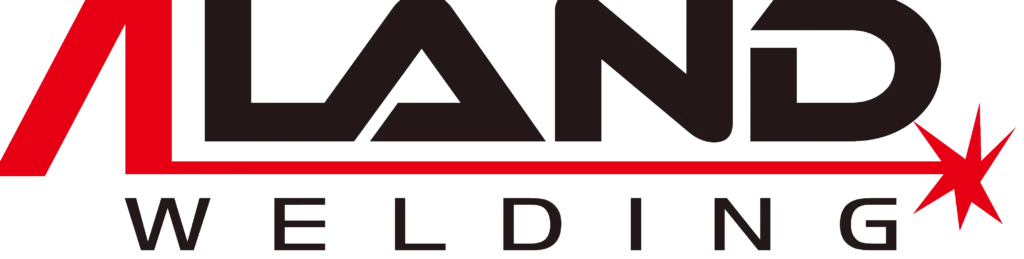
ALAND WELDING Let you feel the most sincere welding service
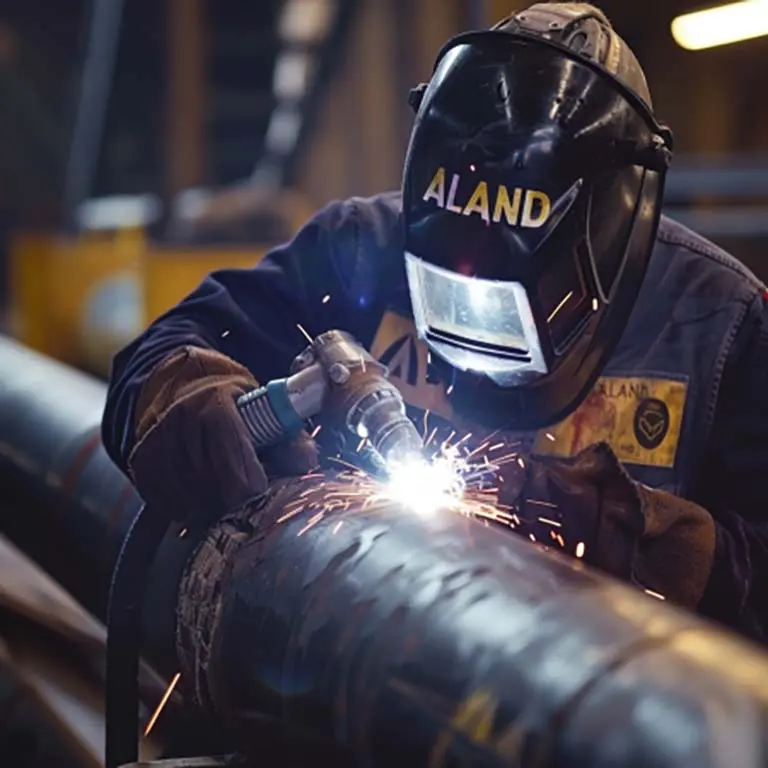
1. Multifunction welder machine concept
Multifunction welder machine generally refers to digital welding machine. Digital welding machines are welding machines controlled by embedded microprocessors such as DSP and ARM. They are the mainstream direction of welding machine development and are characterized by safety, efficiency, speed, stability, and professional automation.
A multi-function welding machine is a device that integrates multiple welding technologies (such as MIG, TIG, MMA, etc.) and functions. It is designed to improve welding efficiency and flexibility and is suitable for different materials and working scenarios. It is usually equipped with a digital control panel and automatic setting function for user-friendly operation, and has safety measures such as overheating protection. It is widely used in manufacturing, maintenance, training and other fields. A variety of welding tasks can be accomplished with one piece of equipment, saving space and costs and improving production efficiency.
2. Features of multifunction welder machine
(1) Rich functions
The functions of traditional welding machines are realized by many analog and logic circuits. Every time a function is added, a lot of components are added. To have more than two functions, a lot of circuit boards are needed. This will not only significantly increase the cost of the welding machine. , and the performance and reliability of the welding machine will drop sharply as the number of components increases, so it is difficult for traditional welding machines to integrate multiple welding functions into one welding machine.
The functions of the digital welding machine are realized by software. To increase the functions of the welding machine, you only need to change the software. Each functional module is independent of each other. Adding new functions does not affect the original functions and performance at all, so the functions of the digital welding machine can be Very rich.
For example, the Nebula series welding machine has coating manual welding, DC TIG welding, pulse TIG welding, TIG spot welding, gas shielded welding (CO2, MIG, MAG), pulse gas shielded welding, double pulse gas shielded welding and carbon arc Eight welding methods of gouging. Each function has many adjustable parameters. Users can either use the system default parameters to set up the welding machine very conveniently, or they can finely adjust the welding machine according to different welding requirements to achieve the best welding effect.
(2) Product consistency is good, performance is stable and reliable
The composition characteristics of a traditional welding machine determine that its performance characteristics completely depend on the parameters of each component. Inconsistencies in component parameters directly lead to inconsistencies in the performance of the welding machine. It is impossible for components produced by any manufacturer to guarantee that their parameters are completely consistent, so There is often a problem that one welding machine of the same brand is different from another. In addition, the parameters of components will change with changes in temperature, humidity and other environments, so the performance of the welding machine will be good and bad.
The characteristic of digital circuits is that they are insensitive to changes in component parameters. For example, a change in input or output resistance from 1K to 10K will not affect the performance of the welding machine. Therefore, the consistency and stability of digital welding machines are far better than traditional welding machines.
(3) High reliability
The digital welding machine adopts high-speed DSP control, which can detect and correct the main transformer bias in time, effectively avoiding damage to the welding machine due to the main transformer bias, greatly improving its reliability; it has under-voltage, over-voltage and over-heat protection functions; IGBT Isolated from the air duct to avoid damage to the welding machine from rain, dust, etc. In addition, due to the use of digital technology, the number of components is greatly reduced and the reliability of the circuit is improved.
(4) High control accuracy
The accuracy of analog control is generally determined by errors caused by component parameter values and errors caused by non-ideal characteristic parameters of operational amplifiers, making it difficult to achieve high-precision control. The accuracy of digital control is only related to the quantization error of analog-to-digital conversion and the limited word length of the system, so digital control can achieve high accuracy.
Especially for advanced welding methods such as pulse gas shielding, the requirements for arc energy control are very strict. To achieve the goals of no spatter, short arc, and low heat input, the current and voltage of each pulse must be accurately controlled to truly achieve one pulse and one drop. Base value transition. The current error of Nebula 500D series welding machine is <1A, the voltage error is <1V, and the time error is <1 microsecond, and the pulse transition is well realized.
(5) Fast dynamic response
Most of the new digital welding machines adopt high-frequency soft switching technology, which greatly improves the dynamic response speed of the welding machine. For example, the inverter frequency of FRONIUS’s TPS5000 welding machine is as high as 70KHZ, and the dynamic response speed is very fast. The improvement of the dynamic speed has greatly improved the The welding performance of the welding machine makes FRONIUS the digital welding machine recognized worldwide as having the best welding performance.
Nebula 500D series welding machine newly developed by Nebula adopts 100KHZ high-frequency soft switching technology and adaptive control technology. Its dynamic response speed is greatly improved. The pulse width adjustment from minimum to maximum only takes 20 microseconds, which is the fastest adjustment speed in the world. Fast welding machine.
(6) Excellent welding performance
Domestic and foreign experts have done a lot of work on how to improve welding performance and proposed many excellent mathematical control models. However, these complex mathematical models are difficult to implement on traditional analog welding machines because they require very complex circuits, so they have long been Stay in the theoretical stage. The emergence of digital welding machines makes it easy to implement these mathematical models on the welding machines. NEBULA series digital welding machines adopt the world’s most advanced control model, and their welding performance has reached the world’s advanced level.
(7) Authoritative welding expert database
The application of digital technology makes the welding machine become an intelligent device, which can have database functions like a computer and can store the experience of many welding experts into the database, making it easy for ordinary welders to weld to the welding level of experts. Especially for some advanced welding methods, there are many parameters that need to be adjusted. It is very difficult for users to match so many parameters themselves, so the expert database has become the most prominent advantage of digital welding machines.
Nebula 500D series welding machine has 100 sets of built-in expert databases. The applicable materials include aluminum, aluminum-magnesium alloy, aluminum-silicon alloy, copper-silicon alloy, copper-aluminum alloy, stainless steel 307, stainless steel 308, stainless steel flux-cored wire, carbon steel, and alkaline chemical. Core welding wire, acid flux cored welding wire, iron powder cored flux cored wire, etc. are particularly suitable for military industry, locomotives, steel structures, shipbuilding, non-ferrous metal welding and other fields that require high welding quality.
(8) Safety and energy saving
The welding machine has LVO function, which can effectively save electric energy and avoid no-load voltage electric shock and injuries, and complies with European safety requirements for operations in hazardous locations.
(9) Network and automated welding
With the development of network and automation technology, more and more enterprises require that their various devices can be connected into a network, which can be monitored and controlled centrally to realize automated operations. The trend of using robots to replace manual welding in the field of welding is developing rapidly. Only digital welding machines can handle this application. Nebula’s 500D digital welding machine is the only welding machine in the world that integrates the fieldbus DEVICENET internally. Since it eliminates the need for an external DEVICENET conversion module, its communication speed is at least 20 times faster than FRONIUS, and it can directly connect hundreds of devices inside the welding machine. Parameters and variables can be read and set directly, which greatly improves the application level of robot welding. It fully supports the DEVICENET protocol and can communicate directly with robots from most manufacturers in the world.
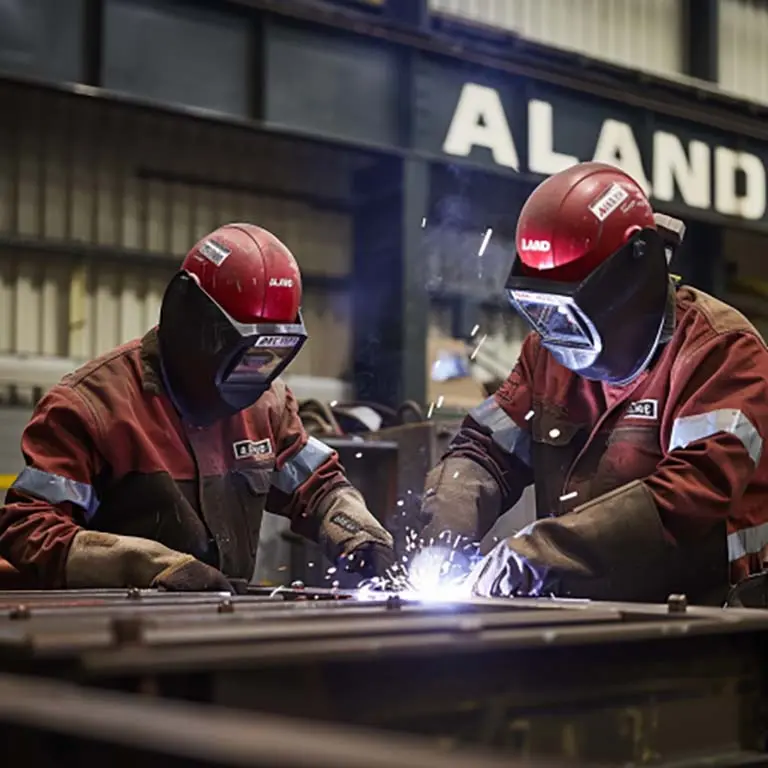
3. Advantages of multifunction welder machine
(1) Multifunction welder integration
Multiple welding modes: Multi-function welding machines usually integrate a variety of welding technologies, including MIG (Metal Inert Gas Welding), TIG (Tungsten Inert Gas Welding), MMA (Manual Arc Welding), etc., and some also include plasma cutting functions. These models cover the vast majority of industrial welding needs, capable of handling a variety of tasks from fine welding to heavy industrial welding.
Flexibility: Users can perform different types of welding work on the same equipment to adapt to different materials and welding requirements, improving the flexibility and adaptability of the workplace.
(2) Cost savings
Reduced equipment investment: Since one multi-functional welding machine can replace multiple dedicated welding machines, companies can significantly reduce equipment purchase costs and long-term maintenance expenses.
Reduce space occupied: One device integrates multiple functions, reducing the space occupied by multiple welding equipment and making the working environment cleaner and more efficient.
(3) Improve efficiency
Quick switching mode: Operators can quickly switch between different welding modes without changing equipment, which greatly saves setup and adjustment time and improves production efficiency.
Digital control and automatic settings: Modern multifunction welder machines are equipped with digital control panels that allow a variety of welding parameters and programs to be preset and stored, which users can quickly recall, reducing preparation time for each operation.
Programming capabilities: Some high-end models support programming of complex welding tasks, enabling repeatable precision welding to improve consistency and quality.
(4) User friendly
Easy to operate: Devices are usually designed with an intuitive user interface, including a clear display and easy-to-understand control buttons, making operation simple and even novices can quickly master how to use it.
Portable design: Many multi-purpose welders are designed to be lightweight with portable handles or wheels for easy movement between jobsites, making them ideal for on-site repairs and field work.
(5) Multi-material adaptability
Wide Material Compatibility: The multifunction welder machine is suitable for welding a variety of metal materials, including steel, stainless steel, aluminum, copper, etc., and can meet the needs of various industrial fields, from light manufacturing to heavy industrial applications.
Adjust welding parameters: The equipment can adjust welding parameters according to different materials and thicknesses to provide the best welding quality.
(6)Safety
Built-in protection functions: Multi-function welding machines are usually equipped with safety measures such as overheating protection, current overload protection and gas flow detection to prevent equipment damage and operator injuries and improve work safety.
Stable performance: The high-quality multi-function welding machine design focuses on stability and durability to ensure reliable performance under long-term, high-intensity working conditions.
(7) Adapt to a variety of application scenarios
Manufacturing industry: Especially suitable for production lines that require a variety of welding processes. It can flexibly switch between different processes to improve production efficiency and product quality.
Repair and maintenance: It is convenient to carry out various welding repair work at different sites, especially suitable for repair tasks that need to be carried out outdoors or in hard-to-reach places.
Training and education: Welding skills training institutions can teach a variety of welding techniques through multi-functional welding machines, provide comprehensive training, and improve students’ comprehensive abilities and employment competitiveness.
4. Defects of multifunction welder
(1) The initial cost is higher
Equipment price: Because multi-function welding machines integrate multiple welding technologies, their design and manufacturing costs are high, so the market price is often higher than that of single-function welding machines. For some small and medium-sized enterprises or individual users with limited budgets, purchasing such equipment requires a large capital investment.
Additional costs: In addition to purchasing the equipment itself, users also need to purchase various accessories and consumables, such as different types of welding electrodes, welding wires and shielding gases, etc. These are additional expenses.
(2) Increased operational complexity
Learning curve: The multi-function welding machine integrates a variety of welding technologies, each of which has its own specific operating methods and setting parameters. For beginners or operators without a variety of welding experience, it takes more time and effort to master and use these functions proficiently.
Complex user interface: Although modern multi-function welding machines are usually equipped with digital control panels, the interface settings are complex due to the wide range of functions, and users may need to spend time learning and adapting to the different menus and operating options.
(3) Difficulty of repair and maintenance
High technical requirements: The internal structure of the multi-function welding machine is complex and integrates a variety of welding technologies, so the technical requirements for maintenance personnel are high. When a malfunction occurs, professional maintenance technicians may be required to solve it, which increases the difficulty and cost of repair.
Accessories supply: Since the equipment integrates multiple functions and has a wide variety of spare parts, some special accessories may be difficult to find in the market, or may take a long time to be supplied, resulting in extended equipment repair and maintenance time.
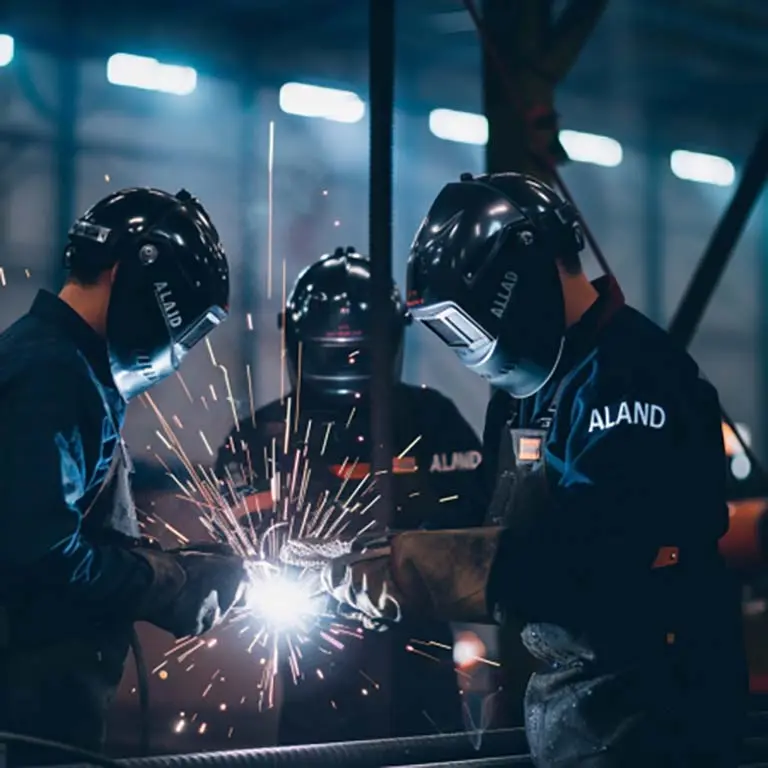
(4) Performance compromise
Lack of specialization: Although a multi-function welder is capable of performing a variety of welding tasks, it may not perform as well as a dedicated welder for certain welding applications. For example, in TIG welding or welding of certain special materials that require extremely high precision and control, a dedicated TIG welding machine may provide better welding quality and results.
Power limitation: Multi-function welding machines are usually designed to take into account multiple functions, which may compromise power output and cannot meet the needs of some high-intensity, long-term heavy industrial welding.
(5) Dimensions and weight
Portability issues: Although multifunction welder machines are designed with portability in mind, their size and weight tend to be larger due to the integration of multiple functions. This can still be an inconvenience for users who need to move frequently or work in small spaces.
Restricted use scenarios: In some application scenarios that require lightweight equipment, such as high-altitude operations or field work, the size and weight of a multi-function welder may limit its use.
(6) Heat management
Heat dissipation problem: When a multi-function welder works at high intensity for a long time, a large amount of heat may be generated internally. Although most equipment is equipped with overheating protection, poor heat dissipation may still cause the equipment to overheat, thus affecting the welding quality and equipment life.
Cooling needs: In order to ensure the normal operation of the equipment and extend its service life, users may need additional cooling equipment or improved ventilation conditions in the working environment, which is also an additional expense.
(7) Power requirements
High power requirements: Multifunctional welders often require a higher power supply, especially when using high-power welding modes. This places higher demands on workplaces with insufficient electrical infrastructure, which may require additional power support or electrical system modifications.
Power supply stability: There are high requirements for the stability of current and voltage during the welding process. Power supply fluctuations may affect the welding effect and even damage the equipment.
(8)Compatibility and updates
Compatibility issues: With the development of technology, multi-function welding machines need to be compatible with accessories and consumables of different models and specifications to ensure their normal function. However, compatibility issues between different brands and models may cause inconvenience in use.
Technology updates: Welding technology and equipment are constantly updated, and users need to understand and adapt to new technologies in a timely manner, which may require continuous upgrading of equipment and training of operators, increasing long-term use costs.