Introduction to water cooled tig welder
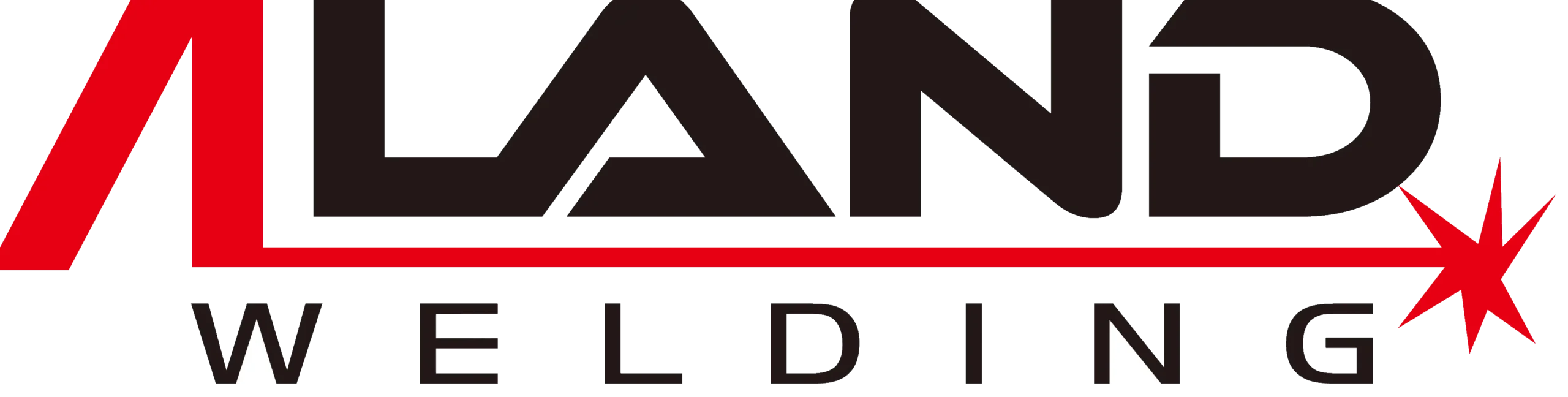
ALAND WELDING Let you feel the most sincere welding service
1. Introduction to water cooled tig welder
The water cooled tig welder TIG welding water tank is an important component used in the TIG welding cooling system, responsible for storing and circulating cooling liquid to maintain the temperature of the welding equipment within a safe range. It is usually made of corrosion-resistant materials and houses a cooling pump and filter, and some are equipped with a radiator and temperature control device. The cooling pump delivers the coolant from the water tank to the welding torch and recirculates it back to the water tank, ensuring continuous flow of coolant and stable temperature. Selecting a water tank with appropriate capacity and cooling capacity, using high-temperature and corrosion-resistant materials, and performing regular maintenance and inspections can improve welding efficiency, ensure welding quality, and extend equipment life. TIG welding water tanks are widely used in industrial welding, precision manufacturing and welding repair to ensure the stability and safety of the welding process.
2. Function of water cooled tig welder
(1) Store coolant:
Coolant storage: The water tank is used to store coolant, usually deionized water or special coolant. These liquids must have excellent thermal conductivity and insulation properties to effectively conduct and dissipate the heat generated during the welding process.
(2) Circulating coolant:
Coolant circulation: The cooling pump transports the coolant from the water tank to the welding torch. The coolant absorbs the heat generated by welding in the welding torch and then returns to the water tank. Through continuous circulation, it takes away the heat generated during the welding process.
Flow channel: The coolant flows between the welding torch and the cooling system, ensuring continuous heat exchange and preventing the welding equipment from overheating.
(3) Temperature control:
Temperature monitoring and adjustment: The advanced water tank system is equipped with a temperature sensor and controller, which can monitor the temperature of the coolant in real time and automatically adjust the temperature of the coolant to ensure that the temperature remains stable during the welding process and prevent the welding torch and welding area from overheating.
Constant temperature function: By accurately controlling the coolant temperature, it maintains a constant temperature in the welding area and improves the consistency of welding quality.
(4) Impurity filtration:
Filtration system: The built-in filter in the water tank is used to filter impurities and particles in the coolant, prevent the cooling system pipes and the internal blockage of the welding torch, and ensure the cleanliness and cooling effect of the coolant.
Easy maintenance: Regularly changing and cleaning filters can extend the life of your cooling system and ensure it operates efficiently.
(5) Heat dissipation:
Radiator configuration: Some advanced water tank systems are equipped with radiators, which further reduce the temperature of the coolant through air or water circulation, enhance the cooling effect, and improve cooling efficiency.
Heat Dissipation: Effectively dissipate heat from the coolant through the radiator, ensuring that the coolant is at the proper temperature before returning to the welding torch.
(6) Protection equipment:
Prevent overheating: Through effective cooling, we prevent the welding torch and welding equipment from overheating, reduce equipment wear and damage caused by overheating, and extend the service life of the equipment.
Equipment maintenance: Maintain the purity and appropriate temperature of the coolant, reduce the frequency and cost of equipment maintenance, and improve the reliability and efficiency of the equipment.
(7) Improve welding quality:
Stable temperature: Stable cooling effect helps maintain a constant temperature in the welding area, reducing thermal stress and welding defects, improving welding quality and the consistency of welded joints.
Precision welding: Especially in fields such as aerospace, electronics and medical equipment that require high-precision welding, the effective operation of the cooling system can significantly improve welding accuracy and quality.
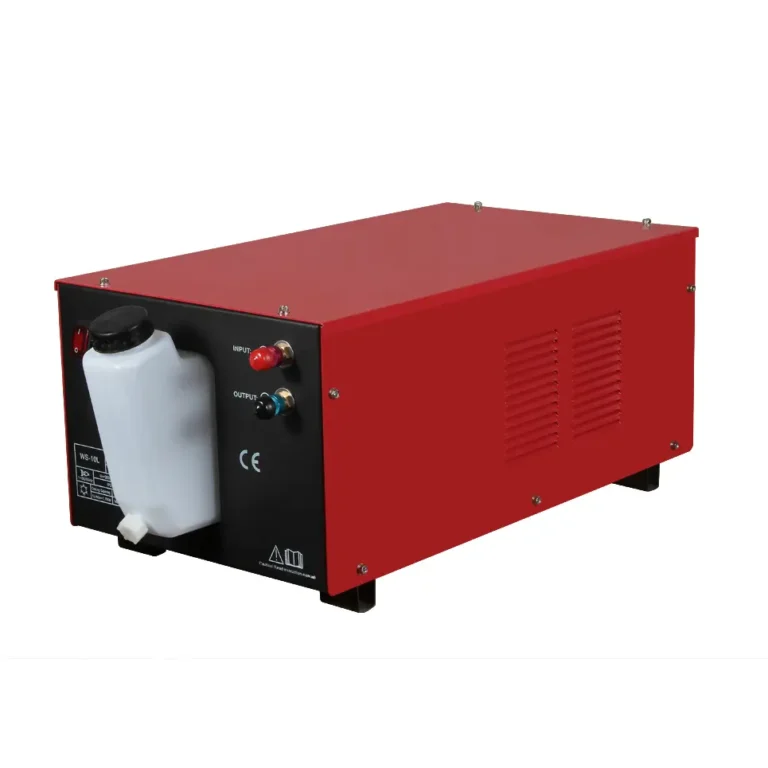
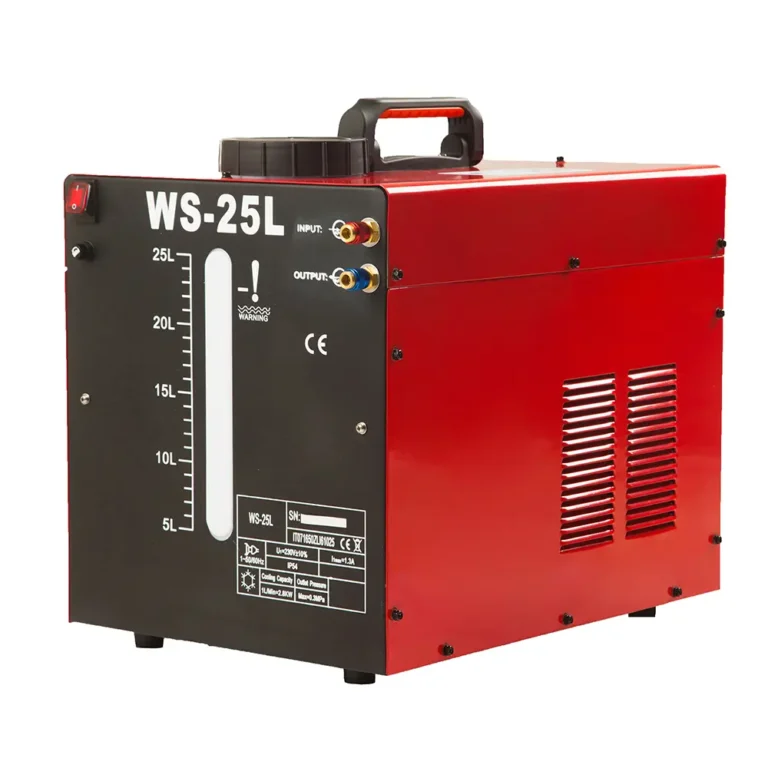
3. Structure ofwater cooled tig welder
(1) Water cooled tig welder water tank body:
Material: Usually made of corrosion-resistant materials such as stainless steel or high-strength plastic, ensuring durability and stability in long-term use.
Structure: Designed as a closed structure to prevent coolant leakage and contamination.
(2) Cooling pump:
Function: Responsible for transporting coolant from the water tank to the welding torch and circulating the coolant that has absorbed heat back to the water tank.
Type: Common ones include centrifugal pumps and gear pumps, which must be efficient, durable and low-noise.
(3) Coolant:
Type: Deionized water or special coolant is usually used, these liquids have good thermal conductivity and insulation properties.
Additives: Anti-corrosion agents and lubricants are sometimes added to protect the internal components of the cooling system.
(4) Filter:
Function: Filter impurities and particles in the coolant, prevent cooling system pipes and internal blockage of the welding torch, and maintain the cleanliness of the coolant.
Type: Can be mesh filter, paper filter or other type of high efficiency filter.
(5) Radiator:
Function: Further reduce the temperature of the coolant through air or water circulation and improve cooling efficiency.
Type: Can be an air-cooled radiator or a water-cooled radiator, depending on the design and needs of the cooling system.
(6) Temperature control device:
Temperature sensor: Monitors the temperature of the coolant to ensure it is within the appropriate range.
Thermostat: Adjusts the temperature of the coolant according to the readings of the temperature sensor to keep the temperature stable during the welding process.
(7) Pipes and connections:
Function: Connect water tank, cooling pump, welding torch and other components to form a circulation path for coolant.
Material: Usually high temperature resistant and corrosion resistant materials are used, such as rubber tubes, plastic tubes or metal tubes.
(8) Liquid level indicator:
Function: Display the coolant level in the water tank to help users add coolant in time to prevent the cooling system from running dry.
(9) Pressure regulating valve:
Function: Regulate and maintain the liquid pressure in the cooling system to ensure that the coolant circulates at appropriate pressure.
Type: including automatic regulating valve and manual regulating valve.
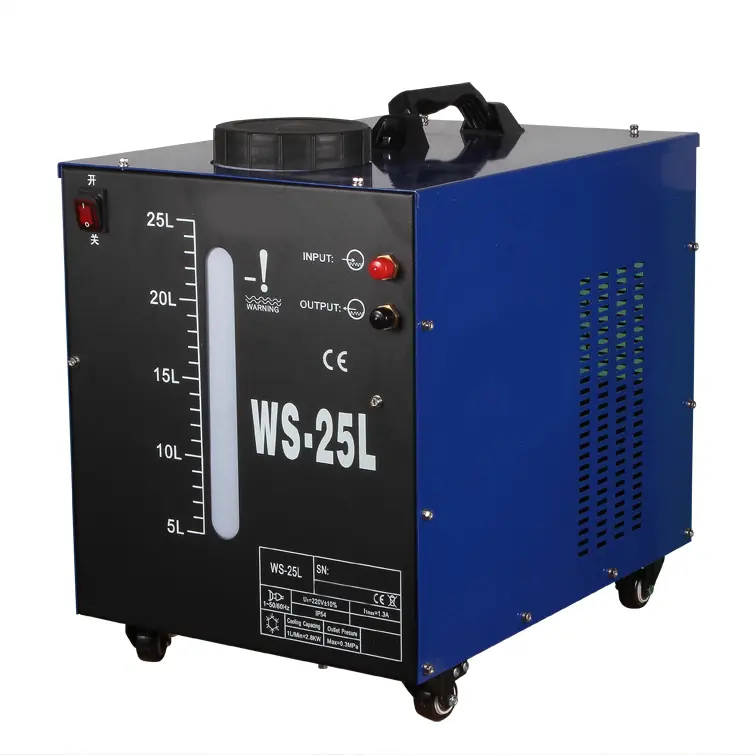
4. Key points for choosing water cooled tig welder
(1) Cooling capacity:
Welding current: Choose the water tank according to the maximum current of the welding equipment. High current welding (e.g. over 200A) requires strong cooling capacity to prevent the torch from overheating.
Heat dissipation requirements: Calculate the heat generated during the welding process and ensure that the water tank can provide sufficient cooling power (usually expressed in W).
(2) Water tank capacity:
Appropriate Capacity: Choose a water tank capacity suitable for your welding equipment and application scenario. If the capacity is too small, the coolant temperature may rise too quickly, affecting the cooling effect; if the capacity is too large, the equipment cost and space will be increased.
Coolant circulation: Ensure that the water tank capacity can support effective circulation of coolant to maintain a constant cooling effect.
(3) Materials:
Corrosion-resistant materials: The water tank material should have good corrosion resistance, such as stainless steel (such as 304 or 316 stainless steel) or high-strength plastic to prevent the coolant from corroding the water tank.
Durability and temperature resistance: Materials should be resistant to high temperatures, high pressures, and have structural stability during long-term use.
(4) Temperature control:
Temperature sensor and controller: Equipped with a precise temperature sensor and control system to monitor the coolant temperature in real time and automatically adjust the operation of the cooling system to ensure temperature stability during the welding process.
Temperature display: The water tank should be equipped with a temperature display to facilitate the operator to understand the temperature of the coolant in real time.
(5) Coolant type:
Compatibility: Choose the appropriate type of coolant for use, such as deionized water or a specialty coolant, and make sure the tank material and design are compatible with those coolants.
Additive Compatibility: If additives (e.g. preservatives, lubricants) are used, ensure that the tank design and materials are compatible with these additives.
(6) Filtration system:
High-efficiency filter: Equipped with a high-efficiency filter to remove impurities and particles from the coolant to prevent clogging and contamination.
Maintainability: Filters should be easy to remove, clean and replace for routine maintenance and care.
(7) Heat dissipation performance:
Radiator type: Choose air-cooled or water-cooled radiator according to actual needs. Air cooling is suitable for general welding scenarios, and water cooling is suitable for high-intensity and long-term welding.
Cooling efficiency: Ensure that the radiator can effectively reduce the coolant temperature and keep the coolant within the appropriate temperature range.
(8) Pipes and connections:
High temperature resistance and corrosion resistance: Use pipes and connections made of high temperature resistance and corrosion resistance materials to ensure smooth circulation of coolant and durability of the system.
Sealing and reliability: Ensure that all pipes and connections are well sealed to prevent coolant leakage and pressure loss.
(9) Pressure adjustment:
Pressure regulating valve: Equipped with a pressure regulating valve to control the liquid pressure of the cooling system, ensuring that the coolant circulates at the appropriate pressure.
Pressure monitoring: The water tank should be equipped with a pressure gauge or pressure sensor to monitor the system pressure in real time to avoid damage to the system caused by excessively high or low pressure.
(10) Maintenance convenience:
Reasonable design: Choose a water tank with a reasonable structural design to facilitate daily inspection, cleaning and maintenance.
Easy to access: Ensure that key components (such as cooling pumps, filters, radiators) are easy to access and replace, reducing downtime and maintenance costs.
Cleaning port and drain port: The water tank should be designed with a cleaning port and a drain port to facilitate regular cleaning and replacement of coolant.
(11) Other functions:
Liquid level indicator: Equipped with a liquid level indicator that displays the coolant level in the water tank in real time to ensure sufficient coolant volume and prevent the cooling system from running dry.
Alarm system: Advanced water tank systems can be equipped with temperature and pressure alarm systems to prompt operators to deal with abnormal situations in a timely manner to ensure safe operation of the system.
5. Maintenance and maintenance of water cooled tig welder
(1) Regular inspection and maintenance
Coolant inspection and replacement:
Regular inspections: Check the coolant level and cleanliness every week to ensure that the coolant is sufficient and free of impurities.
Coolant replacement: Replace the coolant every 3 to 6 months, or adjust appropriately according to frequency of use and environmental conditions. Regularly changing the coolant can prevent the accumulation of impurities and loss of cooling effect.
Coolant type: Make sure to use deionized water or a specialized coolant with anti-corrosion agents and lubricants in the ratios recommended by the manufacturer.
Filter cleaning and replacement:
Regular Cleaning: Check and clean the filter monthly to prevent clogging with impurities and particles.
Replace filters: Replace filters every 3 to 6 months, depending on filter type and usage.
Radiator maintenance:
Radiator cleaning: Clean the surface of the radiator every month to prevent the accumulation of dust and debris from affecting the heat dissipation effect.
Radiator inspection: Regularly check the working status of the radiator to ensure that it can effectively reduce the coolant temperature.
Pipe and fitting inspection:
Leak inspection: Check pipes and connections weekly for leaks and make sure all connections are well sealed.
Pipe cleaning: Clean the inside of the pipes regularly to prevent the accumulation of impurities in the coolant.
Cooling pump maintenance:
Pump performance inspection: Check the working status of the cooling pump every month to ensure that it runs smoothly and makes no abnormal noise.
Pump replacement: According to the service life and performance of the cooling pump, the aging or faulty cooling pump should be replaced in time.
Temperature control system maintenance:
Temperature sensor check: Check the accuracy of the temperature sensor monthly to ensure accurate temperature monitoring.
Thermostat inspection: Regularly test the working status of the thermostat to ensure that it can correctly regulate the temperature of the coolant.
Liquid level indicator inspection:
Fluid level monitoring: Check the working status of the fluid level indicator weekly to ensure it accurately displays the coolant level.
Indicator cleaning: Clean the liquid level indicator regularly to prevent dirt from affecting reading accuracy.
Pressure regulating system maintenance:
Pressure Gauge Check: Check the pressure gauge reading monthly to ensure the cooling system is operating within the proper pressure range.
Pressure regulating valve inspection: Regularly check and adjust the pressure regulating valve to ensure its normal operation and avoid excessive high or low system pressure.
(2) Maintenance records and troubleshooting
Maintenance records:
Record maintenance status: Record in detail the content, date and person performing each maintenance and upkeep, including coolant replacement, filter cleaning, replacement, radiator cleaning, etc.
Monitor equipment operation: Establish equipment operation logs to record the operating parameters and abnormal conditions of the cooling system to facilitate analysis and diagnosis of faults.
Troubleshooting:
Handle faults in a timely manner: When abnormalities in the cooling system (such as excessive temperature, abnormal pressure, water leakage, etc.) are found, stop the machine promptly for inspection and processing.
Replace damaged parts: According to the fault situation, replace damaged or worn parts, such as cooling pumps, filters, pipes, etc., to ensure normal operation of the system.
Regular professional maintenance:
Professional inspection: Comprehensive professional inspection and maintenance are performed annually to ensure the overall performance and safety of the cooling system.
Technology upgrade: Based on the age of the equipment and technological development, consider upgrading the technology and components of the cooling system in a timely manner to improve the efficiency and reliability of the system.