what is the difference between tig and mig welding
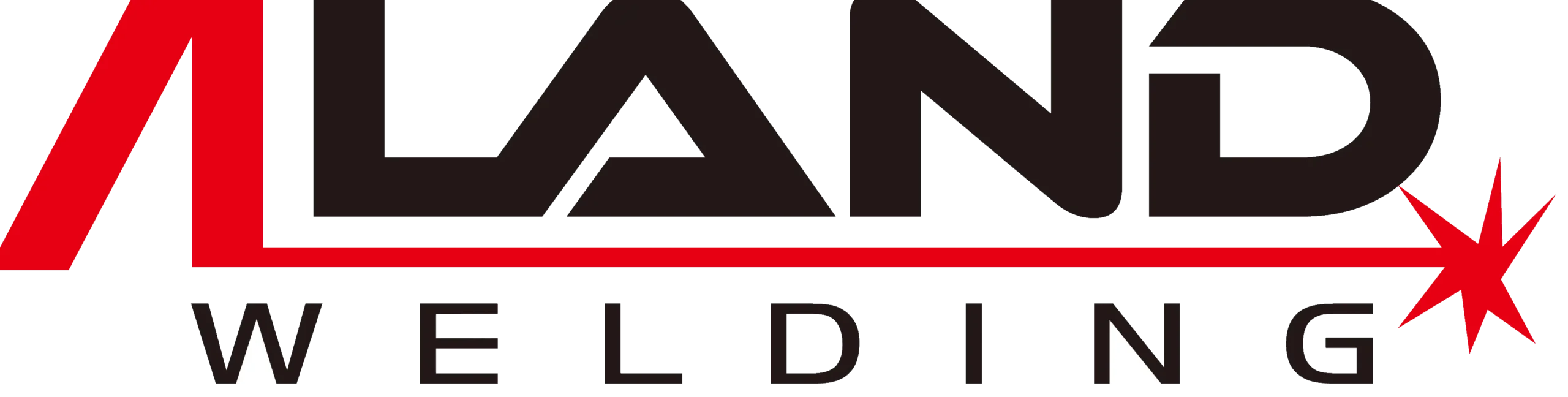
ALAND WELDING Let you feel the most sincere welding service
Arc welding is a welding method that uses the high temperature generated by the arc to melt metal. It is widely used to join various metal materials. Arc welding can be divided into many types according to different electrodes and shielding gases, the two most common of which are mig and tig welding. This article will comprehensively introduce the principles, characteristics, welding methods and precautions of these two arc welding methods, so that readers can choose the appropriate welding method according to different work needs.
1. Introduction to the concept of mig and tig
(1) MIG welding (Melting Inert Gas Welding) is an arc welding method that uses a molten electrode, external gas as the arc medium, and protects the metal droplets, welding pool and high-temperature metal in the welding zone. It is called Melting Gas Shielded Arc. weld. The inert gas (Ar or He) shielded arc welding method using solid wire is called molten extremely inert gas shielded welding, or MIG welding for short.
(2)TIG welding (Tungsten Inert Gas Welding), also known as non-melting extremely inert gas shielded arc welding. Whether it is manual welding or automatic welding of 0.5 to 4.0mm thick stainless steel, TIG welding is the most commonly used welding method. TIG welding with filler wire is often used for bottom welding of pressure vessels because the air tightness of TIG welding is better and can reduce the pores in the weld seam during pressure vessel welding. The heat source of TIG welding is a DC arc, the working voltage is 10 to 95 volts, but the current can reach 600 amps. The correct connection method of the welding machine is that the workpiece is connected to the positive electrode of the power supply, and the tungsten electrode in the welding torch is used as the negative electrode. The inert gas is usually argon.
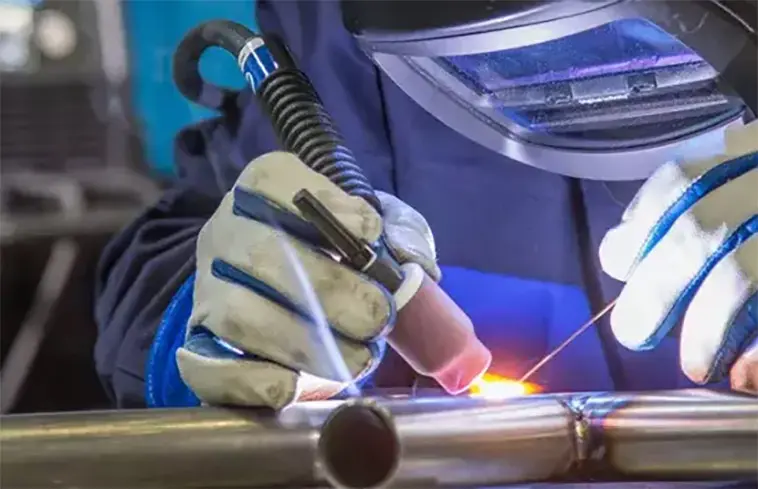
2. Mig and tig difference features
(1) MIG features:
① Like TIG welding, it can weld almost all metals, especially suitable for welding aluminum and aluminum alloys, copper and copper alloys, stainless steel and other materials. There is almost no oxidation and burning loss during the welding process, only a small amount of evaporation loss, and the metallurgical process is relatively simple.
②High labor productivity
③MIG welding can be used in DC reverse connection. It has good cathode atomization effect when welding aluminum, magnesium and other metals, which can effectively remove the oxide film and improve the welding quality of the joint.
④Tungsten electrode is not used, and the cost is lower than TIG welding; it may replace TIG welding.
⑤When MIG welding aluminum and aluminum alloys, sub-jet droplet transfer can be used to improve the quality of the welded joint.
⑥ Since argon is an inert gas and does not react chemically with any substance, it is sensitive to oil stains, rust, etc. on the surface of the welding wire and base metal, and is prone to pores. The welding wire and workpiece must be carefully cleaned before welding.
(2) TIG features:
① Argon gas can effectively isolate the surrounding air; it itself is insoluble in metal and does not react with metal; during the tungsten argon arc welding process, the arc also has the function of automatically removing the oxide film on the surface of the workpiece. Therefore, non-ferrous metals, stainless steel and various alloys that are easily oxidized, nitrided and chemically active can be successfully welded.
② The tungsten arc is stable and can still burn stably even under very small welding current (<10A). It is especially suitable for welding thin plates and ultra-thin plate materials.
③The heat source and filling wire can be controlled separately, so the heat input is easy to adjust and welding can be performed in various positions. It is also an ideal method to achieve single-sided welding and double-sided forming.
3. Welding method mig and tig difference
(1) TIG welding: A welding method that uses pure Ar as the shielding gas and tungsten as the electrode.
(2)MIG welding: MIG welding is melting extremely inert gas shielded electric welding. It uses inert gases such as Ar as the main protective gas, including pure Ar or Ar gas mixed with a small amount of active gas (such as O2 below 2% or O2 below 5%). CO2 gas) welding method for metal arc welding.
4. Welding precautions mig and tig difference
(1) MIG welding
①The appropriate protective gas flow rate is 20-25L/min;
②The arc length is generally controlled at about 4-6mm;
③The influence of wind is particularly detrimental to welding. When the wind speed is greater than 0.5m/s, windproof measures should be taken; pay attention to ventilation to avoid harm to the operator;
④ Using pulse arc current, a stable spray arc can be obtained, which is especially suitable for welding stainless steel, thin plates, vertical welding, and surfacing welding;
⑤ Please use Ar+2% O2 gas combination to weld ultra-low carbon stainless steel, do not use Ar and CO2 mixed welding steel;
⑥ When welding, strictly remove oil, rust, and water impurities from the welding joint.
(2) TIG welding
① Protective gas flow requirements: 7-12L/min when the welding current is between 100-200A; 12-15L/min is appropriate when the welding current is between 200-300A. Due to the damage of the air supply pipe, the protective gas is mixed with moist air, which has an impact on the performance of the welded joint;
② The extension length of the tungsten electrode should be as short as possible relative to the nozzle, and the arc length should be generally controlled at 1-4mm (2-4mm when welding carbon steel; 1-3mm when welding low-alloy steel and stainless steel);
③When the wind speed is greater than 1.0m/s, windproof measures should be taken; pay attention to ventilation to avoid harm to the operator;
④ When welding, strictly remove oil, rust, and water impurities from the welding joint.
⑤ It is recommended to use a DC power supply with steep dropout characteristics and tungsten as the positive electrode.
⑥When welding low alloy steel with more than 1.25% Cr, the back side should also be protected.