Detailed explanation of spot welding process
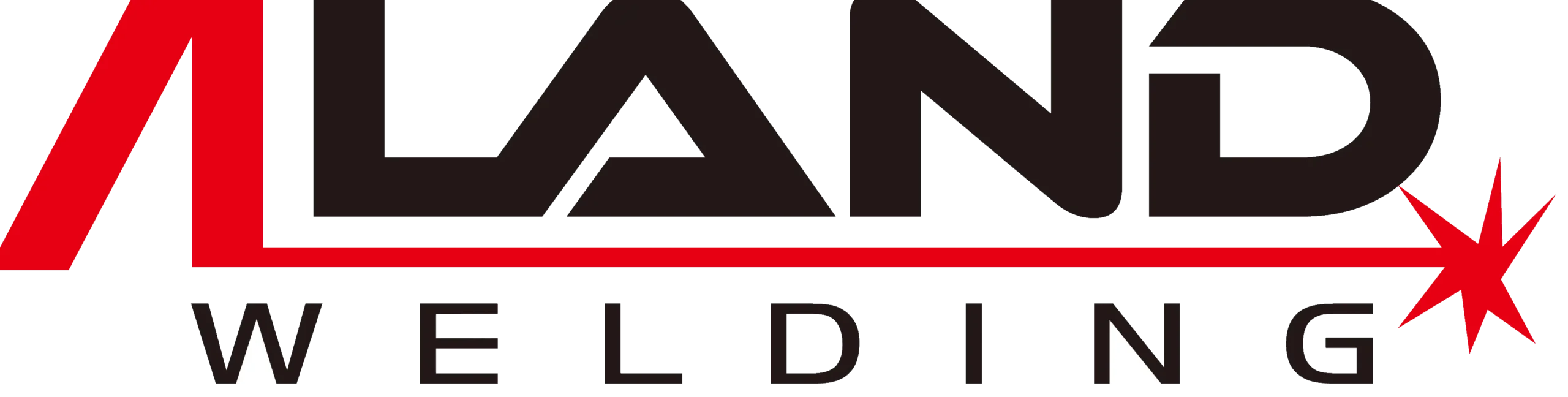
ALAND WELDING Let you feel the most sincere welding service
1、Brief description
Spot welding is a resistance welding method in which welding parts are assembled into lap joints and pressed between two electrodes, using resistance heat to melt the base metal to form solder joints.
Spot welding is mainly used in the following aspects:
(1)Overlap of thin plate stamping parts, such as automobile cabs, compartments, harvester fish scale screens, etc.
(2)Thin plate and shaped steel structures and skin structures, such as carriage side walls and ceilings, trailer carriage panels, combine harvester funnels, etc.
(3)Screens, space frames and cross steel bars, etc.
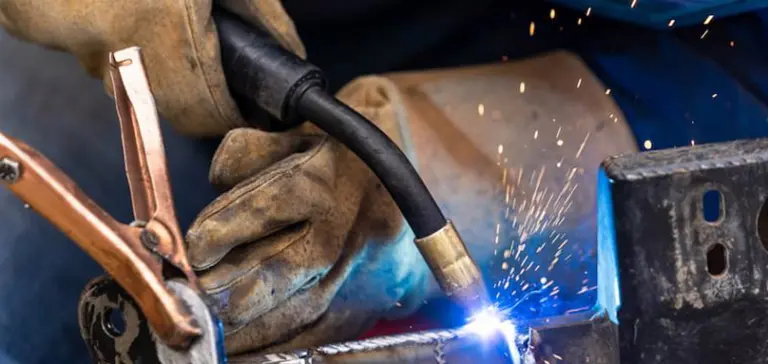
2、Features
During spot welding, the weldment forms an overlapping joint and is pressed between the two electrodes. Its main features are as follows:
(1) During spot welding, the heating time of the connection area is very short and the welding speed is fast.
(2) Spot welding only consumes electric energy and does not require filling materials, flux, gas, etc.
(3) The quality of spot welding is mainly guaranteed by the spot welding machine. It has simple operation, high degree of mechanization and automation, and high productivity.
(4) Low labor intensity and good working conditions.
(5) Since welding is completed in a short period of time and requires large current and pressure, the program control of the process is more complicated, the welding machine has a large electrical capacity, and the price of the equipment is relatively high.
(6) It is difficult to conduct non-destructive testing of solder joints
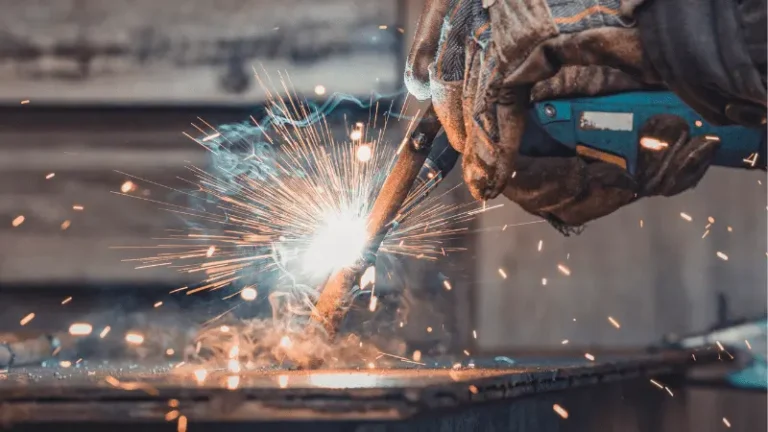
3、Operation process
Before welding, the surface of the workpiece must be cleaned. The commonly used cleaning treatment is pickling, that is, it is first pickled in heated sulfuric acid with a concentration of 10%, and then washed in hot water. The specific welding process is as follows:
(1) Feed the workpiece joint between the upper and lower electrodes of the spot welding machine and clamp it;
(2) When electricity is applied, the contact surfaces of the two workpieces are heated, partially melted, and a nugget is formed;
(3) Maintain pressure after power off, so that the molten nugget cools and solidifies under the pressure to form solder joints;
(4) Remove the pressure and take out the workpiece.
4、Influencing factors
The main influencing factors of welding quality include welding current and energization time, electrode pressure and shunt, etc.
(1) Welding current and power-on time
According to the size of the welding current and the length of power-on time, spot welding can be divided into two types: hard gauge and soft gauge. The specification that passes a large current in a short period of time is called a hard specification. It has the advantages of high productivity, long electrode life, and small deformation of the weldment, and is suitable for welding metals with good thermal conductivity. A gauge that passes a smaller current over a longer period of time is called a soft gauge, which has lower productivity and is suitable for welding metals that tend to harden.
(2) Electrode pressure
During spot welding, the pressure exerted on the weldment by the electrode is called electrode pressure. The electrode pressure should be selected appropriately. When the pressure is high, the shrinkage and shrinkage cavities that may occur when the nugget solidifies can be eliminated. However, the resistance and current density of the welding system are reduced, resulting in insufficient heating of the weldment and a reduction in the diameter of the welding nugget. The strength of the solder joint decreases. The size of the electrode pressure can be selected based on the following factors:
1. Material of weldment. The higher the high temperature strength of the material. The greater the electrode pressure required. Therefore, when welding stainless steel and heat-resistant steel, a higher electrode pressure should be used than when welding low carbon steel.
2. Welding parameters. The harder the welding specification, the greater the electrode pressure.
(3) Diversion
During spot welding, the current flowing outside the main welding circuit is called shunt. The shunt reduces the current flowing through the welding area, resulting in insufficient heating, causing a significant decrease in the strength of the solder joint and affecting the welding quality. The factors that affect the degree of diversion mainly include the following aspects:
1. Weldment thickness and solder point spacing. As the distance between solder joints increases, the shunt resistance increases and the degree of shunting decreases. When a conventional point spacing of 30 to 50 mm is used, the shunt current accounts for 25% to 40% of the total current, and as the thickness of the weldment decreases, the degree of shunting also decreases.
2. Surface condition of weldment. When there are oxides or dirt on the surface of the weldment, the contact resistance between the two weldments increases, and the current passing through the welding area decreases, that is, the degree of shunting increases. The workpiece can be pickled, sandblasted or polished.
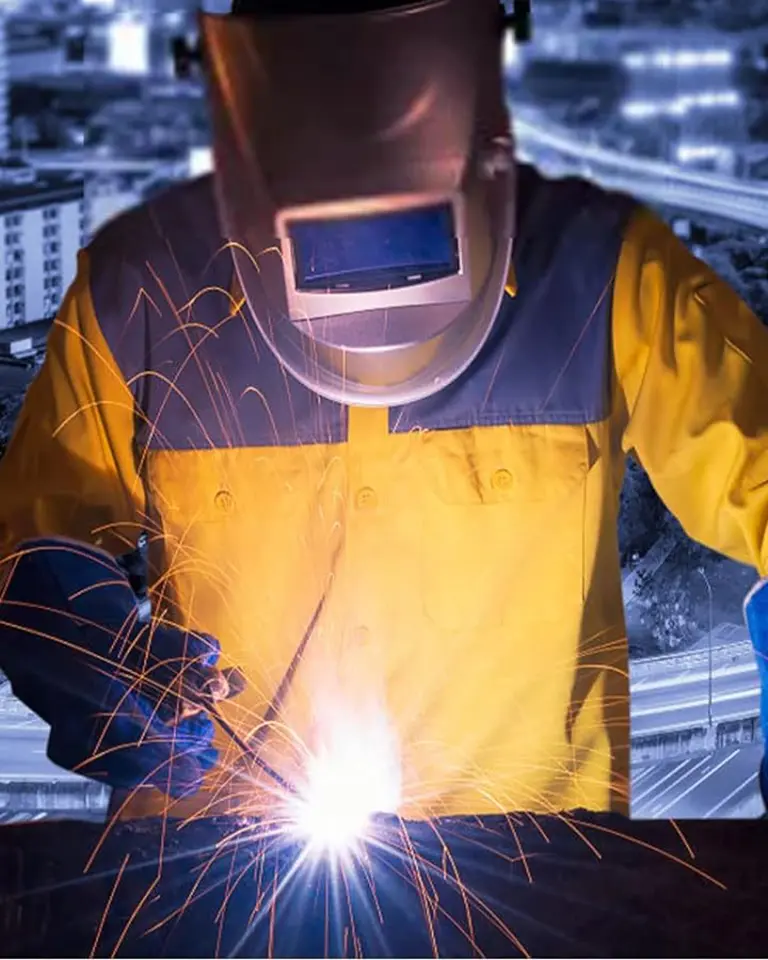
5、Safety Precautions
(1) Furthermore, the foot switch of the welding machine should have a strong protective cover to prevent accidental activation.
(2) The working point should be equipped with baffles to prevent working sparks from flying.
(3) Welders should wear flat protective glasses when welding.
(4) The place where the welding machine is placed should be kept dry, and the floor should be paved with anti-skid plates.
(5) After the welding work is completed, it is crucial to cut off the power supply. Additionally, extend the cooling water switch for 10 seconds before closing it. When the temperature is low, make sure to remove the accumulated water in the waterway to prevent freezing.
Articles you may be interested in:
Why choose TIG welding? 4 major benefits
Introduction to TIG welding and basic operating procedures
Welding, Pressure Welding And Brazing Welding Process
Primary wire, secondary wire, welding wire, ground wire, ground wire
How to distinguish between welding slag and molten iron during welding?
Welder skills and knowledge: What basic knowledge do beginners need to master?