Learn more about resistance welding
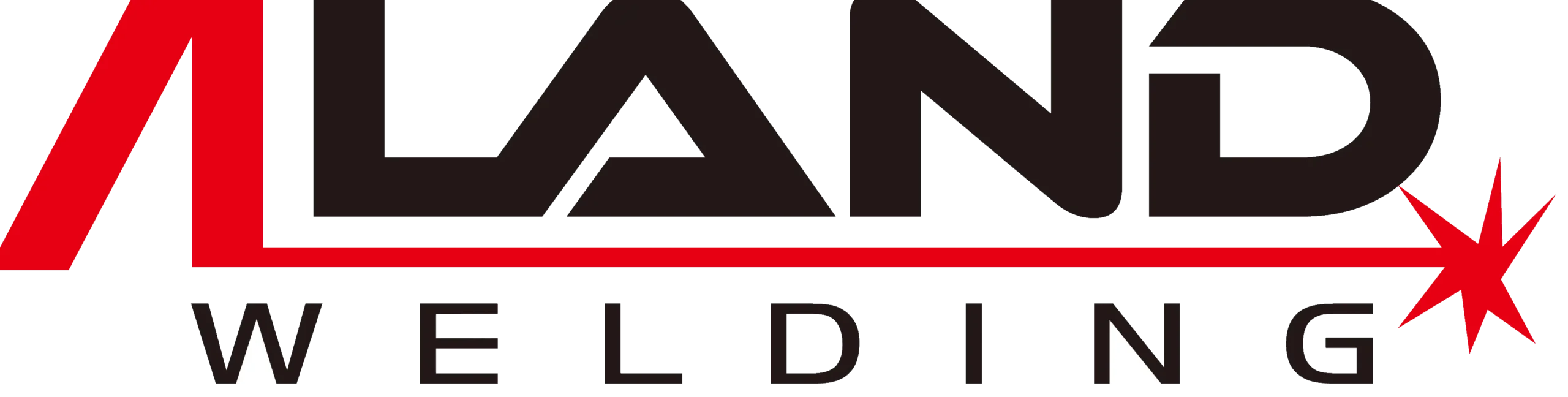
ALAND WELDING Let you feel the most sincere welding service
Resistance welding refers to the method of using the resistance heat generated by current passing through the weldment and the contact as a heat source to locally heat the weldment and pressurize the welding at the same time. When welding, there is no need for filler metal, high productivity, small deformation of the weldment, and easy automation.
Resistance welding is a method that uses the resistance heating effect generated by the current flowing through the contact surface and adjacent areas of the workpiece to heat it to a molten or plastic state to form a metal bond. There are four main resistance welding methods, namely spot welding, seam welding, projection welding, and butt welding.
1.Resistance Welding Principle
Generation of welding heat and factors affecting heat generation The heat generated during spot welding is determined by the following formula: Q =I2Rt
In the formula, Q——The heat generated (J)
I2 – square of welding current (A)
R——Resistance between electrodes (Ω)
t——Welding time (s)
Resistance R and factors affecting R. The resistance between electrodes in the above formula includes the resistance R of the workpiece itself, the contact resistance R between the two workpieces, and the contact resistance R between the electrode and the workpiece.
When the workpiece and electrode are aligned, the resistance of the workpiece depends on its resistivity. Therefore, resistivity is an important property of the material being welded. Metals with high resistivity have poor thermal conductivity (such as stainless steel), and metals with low resistivity have good thermal conductivity (such as aluminum alloys). Therefore, it is easy to generate heat but difficult to dissipate heat when spot welding stainless steel, and it is difficult to generate heat but easy to dissipate heat when spot welding aluminum alloy. When spot welding, the former can use a small current (thousands of amps), while the latter must use a large current (tens of thousands of amps).
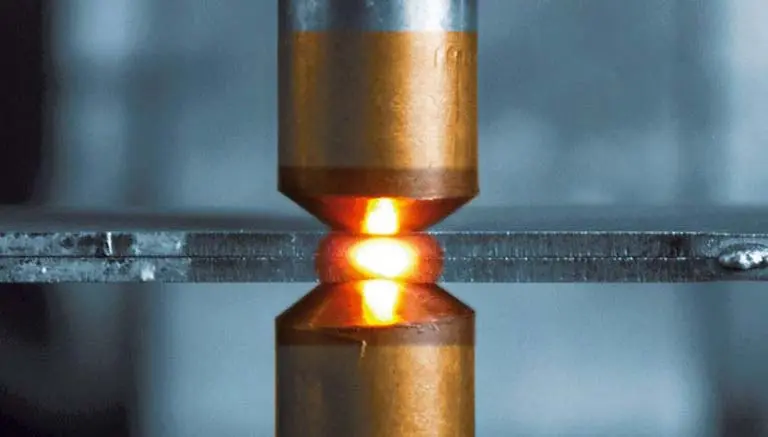
2.Resistance Welding Category
Resistance Spot Welding
Resistance spot welding is a resistance welding method that assembles the weldment into a lap joint and presses it between two columnar electrodes, using resistance heat to melt the base metal to form a solder joint. Spot welding is mainly used for thin plate welding.
Spot welding process:
(1) Preload to ensure good contact between workpieces.
(2) Turn on electricity to form a nugget and plastic ring at the weld.
(3) Cut off the power for forging, so that the molten nugget will cool and crystallize under the continued action of pressure, forming a solder joint with a dense structure and no shrinkage cavities or cracks.
Seam Welding
The process of seam welding is similar to spot welding, except that a rotating disc-shaped roller electrode is used instead of a cylindrical electrode. The weldment is assembled into a lap or butt joint and placed between the two roller electrodes. The roller pressure welding It is a resistance welding method in which the parts are rotated and powered continuously or intermittently to form a continuous weld. Seam welding is mainly used to weld structures with regular welds and required sealing. The plate thickness is generally less than 3mm.
Butt welding
Butt welding is a resistance welding method that welds parts along the entire contact surface.
(1) Resistance Butt Welding
Resistance butt welding is a method of assembling welding parts into butt joints, making their end faces in close contact, using resistance heat to heat to a plastic state, then cutting off the power and quickly applying upsetting force to complete the welding.
Resistance butt welding is mainly used for weldments with simple cross-sections, diameter or side length less than 20mm, and low strength requirements.
(2) Flash Butt Welding
Flash butt welding is to assemble the welding parts into butt joints, turn on the power supply, and gradually move the end faces closer to achieve local contact. The resistance heat is used to heat these contact points. Under the action of large current, a flash is generated to melt the end face metal until the end face. When the part reaches a predetermined temperature within a certain depth range, the power is turned off and the upsetting force is quickly applied to complete the welding.
The joint quality of flash welding is better than that of resistance welding, the mechanical properties of the weld are equivalent to those of the base material, and there is no need to clean the pre-welded surface of the joint before welding. Flash butt welding is often used for welding important weldments. It can weld the same metal or dissimilar metals; it can weld 0.01mm metal wire, and it can also weld 20000mm metal rods and profiles.
Projection Welding
Projection welding is a variant of spot welding; there are prefabricated bumps on a workpiece. During projection welding, one or more nuggets can be formed at the joint at a time.
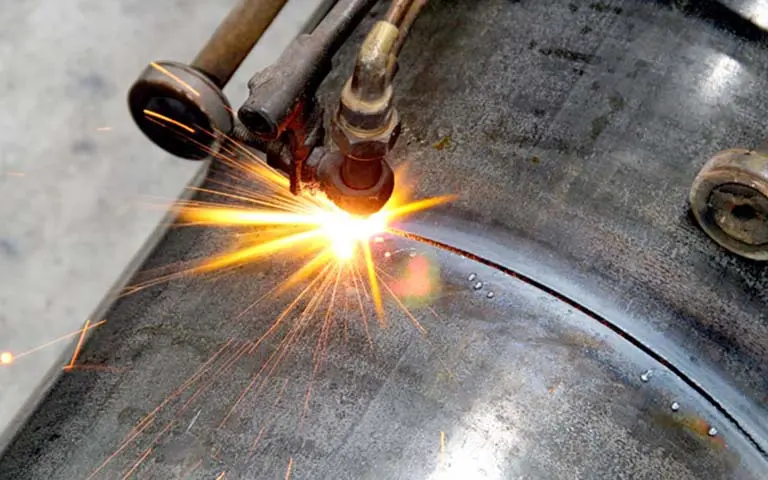
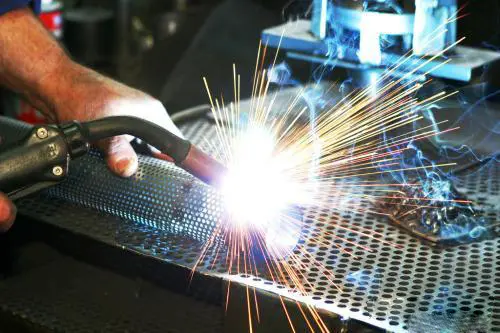
3.Resistance Welding Advantages And Disadvantages
The advantages of resistance welding machine are:
1) Concentrated heat, short heating time, small welding deformation, and good welding quality.
2) The welding process is simple, generally does not require filling materials and fluxes, and does not require protective gas.
3) It can be adapted to the welding of many types of homogeneous and dissimilar metals, including the welding of coated steel plates.
4) The process is simple and easy to implement mechanization and automation. There is no need for long-term training of welders before taking up the job.
5) Welding productivity is high and cost is low.
6) The working environment is good and the pollution is small.
The disadvantages of resistance welding machine are:
1) The equipment is complex and the degree of mechanization and automation is high, which makes the equipment cost high and maintenance difficult.
2) The electric capacity is large, and most of them are single-phase welding machines, which cause serious unbalanced load on the power grid and must be connected to a power grid with a larger capacity.
3) The welding process proceeds very quickly. If fluctuations occur due to certain process factors during welding, it will often be too late to make adjustments if the stability of the welding quality is affected; caution should be used in important load-bearing structures.
4) There is currently a lack of reliable non-destructive testing methods, and welding quality can only be checked by process samples and destructive tests, as well as guaranteed by various monitoring technologies.
5) The tensile strength and fatigue strength of the point and seam welded lap joints are low due to the angle formed around the nugget.
6)The thickness, shape and joint form of welding are restricted to a certain extent.
4.Resistance Welding Limitations
For some materials, especially those with high resistivity such as stainless steel, higher welding energy may be required.
A certain amount of pressure is required to ensure good welding quality, which may cause deformation or deformation.
There are certain requirements for the geometry and surface condition of the workpiece, and the welding contact area needs to be large enough.
5.Application Fields Of Resistance Welding:
Resistance welding is widely used in automobile manufacturing, aerospace, electronic equipment, home appliances and other industries.
Used for welding circuit boards, metal parts, pipes, wire harnesses, etc.
It is often used in situations where high-strength and high-quality connections are required.
Summarize
Resistance welding machine is a process that uses resistance effect to generate heat, heat metal parts to the melting point and connect them. The main categories are spot welding, seam welding, shrink welding, flash welding, brazing and gap welding. Spot welding is suitable for joining thin plates, seam welding is used for welding long strips, shrink welding is used to connect the ends of the workpiece by compressing it, flash welding is used for large workpieces, brazing is used to join different types of metals, and gap welding is used to fill gaps. These methods are suitable for workpieces of different materials and shapes, with efficient, fast and reliable connection characteristics.
Articles you may be interested in:
Difference Between MIG And TIG Welding
A Must-read For Newbies: GTAW Welding
Ac Dc Tig Welding Comparison Instructions
Basic Knowledge Of Welding Procedure Qualification
Pipe Welding Methods—-A Must-read For Newcomers
Main Operating Points Of Ordinary MIG Aluminum Welding
Safety Operating Requirements For Electric Welding Operations