Introduction To Common Northern Industrial Welders
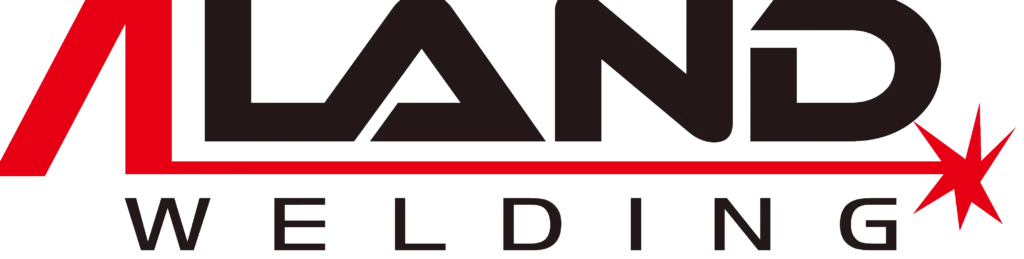
ALAND WELDING Let you feel the most sincere welding service
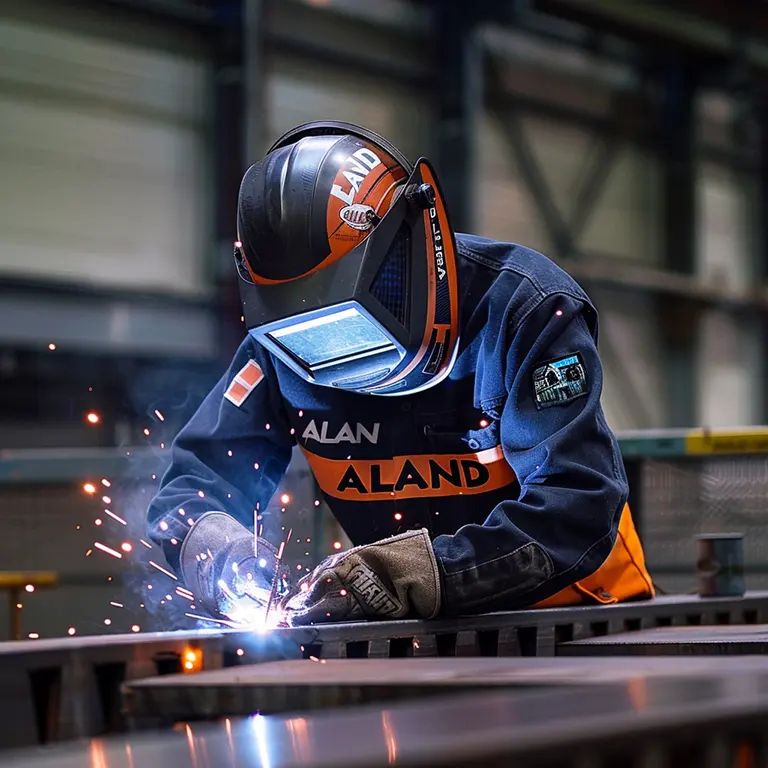
1. Introduction to northern industrial welder
A northern industrial welder is a device used to join metallic materials together. They work by heating two or more metal parts to the melting point and then causing them to fuse with each other to create a strong connection. Northern industrial welder is usually used in manufacturing, construction, automotive and other fields, and its application range is very wide.
Here are some common types of northern industrial welders:
(1) Arc welding machine: The metal is heated to the melting point by generating an arc, and then the filler material is used to fill the weld.
(2) Gas shielded welding machine: Common types include argon arc welding, MIG (metal inert gas) welding and TIG (tungsten arc) welding, which prevent oxygen and other impurities from damaging the weld by providing protective gas in the welding area. pollute.
(3) Welding robot: Automated welding system, usually used in large production lines, can perform welding operations with high efficiency and consistency.
(4) Laser welding machine: Use high-energy laser beam to heat the metal surface to achieve welding.
2. What kind of welding machine belongs to northern industrial welder
The northern industrial welder is a welding equipment specially designed for use in industrial production environments. It is efficient, stable and reliable to meet the needs of mass production. The following are some detailed features of northern industrial welder:
(1) High power and efficiency: Northern industrial welders usually have high welding power and output capabilities, and can handle metal workpieces of large size, thickness, or requiring higher welding speeds. High-power welding capabilities can ensure high efficiency during the welding process and rapid completion of production tasks.
(2) Multiple welding modes and processes: northern industrial welder usually supports multiple welding modes and processes, including arc welding, gas shielded welding (such as MIG/MAG welding, TIG welding), laser welding, etc. These different welding processes can adapt to different materials and welding requirements, providing more flexible options.
(3) Stability and reliability: The industrial production environment has extremely high requirements on the stability and reliability of equipment. Therefore, northern industrial welders usually adopt sturdy and durable designs and materials, and are equipped with various safety features and protection devices to ensure long-term stable operation of the equipment and reduce production downtime due to failures.
(4) Automation and intelligence: With the improvement of industrial automation level, some industrial welding machines have automation and intelligence functions. For example, welding robots can automatically perform welding tasks according to preset programs to improve production efficiency and consistency; intelligent welding systems can monitor the welding process in real time and make automatic adjustments to ensure welding quality.
(5) Suitable for mass production: Industrial welding machines are designed to meet the needs of mass production, can operate stably on busy production lines, and have a long service life and low maintenance costs. They are often highly customizable to suit the needs of different industries and applications.
3. Northern industrial welder operating specifications
The usage specifications of northern industrial welder are very important to ensure safety, improve efficiency and ensure welding quality. The following are some common industrial welding machine usage specifications:
(1) Operator training: All personnel operating welding machines should receive relevant training and understand the operating principles, safety precautions and emergency measures of the welding machine. Training should include the correct use of equipment, maintenance, safe operating procedures, etc.
(2) Safety protection measures: When operating the welding machine, the operator must wear appropriate personal protective equipment, including fire-proof clothing, safety glasses, gloves and protective masks. In addition, ensure that the welding area is well ventilated to eliminate harmful gases and fumes generated during the welding process.
(3) Equipment inspection and maintenance: Before each use of the welding machine, the equipment should be inspected to ensure that the equipment is operating normally, that all components are firmly connected, and that the power and gas sources are supplied normally. Perform regular maintenance on the welding machine, including cleaning, lubrication, replacement of wearing parts, etc., to ensure the stability and reliability of the equipment.
(4) Welding parameter setting: According to the type, thickness and welding requirements of the welding material, correctly set the welding parameters, including welding current, voltage, welding speed, etc. Adjustments should be made according to specific conditions, and test welding should be conducted to confirm that the welding quality meets the requirements.
(5) Welding process monitoring: During the welding process, the operator should monitor the welding quality and the stability of the welding process at any time. If abnormal conditions are found, welding should be stopped immediately and inspection should be carried out to avoid losses caused by unqualified welding quality or equipment failure.
(6) Accident emergency response: For possible accidents, corresponding emergency response measures and emergency evacuation plans should be formulated, and training and drills should be conducted to ensure that emergency situations can be responded to quickly and effectively.
(7) Records and file management: Welding process records and equipment maintenance records should be established to record welding parameters, welding results, maintenance status and other information. These records are important for tracing welding quality, identifying problems, and improving the process.
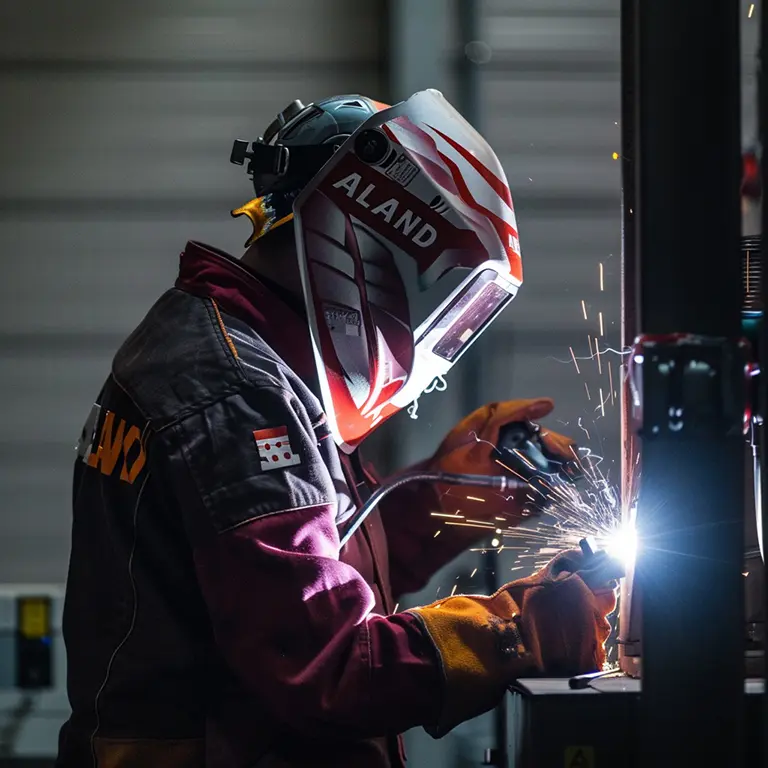
4. Introduction to ALADN northern industrial welder
When it comes to northern industrial welder brands, “ALAND” is an option worth paying attention to. ALAND industrial welding machines are renowned for their superior performance, reliability and innovation. Whether on large production lines or in small workshops, ALAND welding equipment has demonstrated convincing performance.
ALAND industrial welding machines have a variety of welding modes and processes, including arc welding, MIG/MAG welding, TIG welding, etc., which can meet different materials and welding requirements. These devices are well designed and easy to operate, providing an efficient and stable welding process.
In addition, ALAND industrial welding machines also focus on safety and reliability. The equipment is equipped with a variety of safety functions and protection devices, such as overload protection, overheating protection, slow response, etc., to ensure the safety of operators and equipment. At the same time, ALAND welding machines have long service life and low maintenance costs, saving users time and costs.
As a reputable industrial welding machine brand, ALAND product quality and performance have been widely recognized in the market. If you are looking for a reliable northern industrial welder, ALAND is definitely worth considering.
5. Northern industrial welder applicable scenarios
Northern industrial welder is suitable for various industrial production scenarios, and its application range is very wide, including but not limited to the following aspects:
(1) Manufacturing industry: Northern industrial welder plays an important role in the manufacturing industry and is used to connect metal parts, components and structures to manufacture various products, such as automobiles, ships, machinery and equipment, electronic products, furniture, etc. They can perform welding, cutting, soldering and other operations to meet the needs of different manufacturing processes.
(2) Construction industry: In the construction industry, northern industrial welder is often used to connect steel structures, steel beams, pipes and other metal components, and is used to build bridges, buildings, pipeline systems and other large projects. The application of welding technology in construction can improve the strength and stability of the structure and ensure the safety and durability of the building.
(3) Aerospace industry: The aerospace field has extremely high requirements for lightweight and high strength materials. Northern industrial welder plays a key role in aerospace manufacturing. They are used to weld structural components and engine parts of aircraft, rockets, satellites and other aerospace vehicles to ensure their performance and safety.
(4) Energy industry: Industrial welding machines also have important applications in the energy industry, used to manufacture and maintain pipelines, storage tanks, oil wells and other equipment for oil, natural gas, nuclear energy and other energy facilities. The application of welding technology in the energy industry can ensure the safety and stability of energy production and transmission.
(5) Automobile manufacturing industry: In the field of automobile manufacturing, industrial welding machines are used to weld metal parts such as automobile bodies, chassis, and engine parts to ensure the structural strength and safety of the automobile. Efficient welding technology can improve automobile production efficiency and reduce production costs.
(6) Electronic manufacturing industry: Northern industrial welder also has certain applications in the electronic manufacturing industry. It is used to weld tiny metal parts such as circuit boards and electronic components to ensure the connection quality and stability of electronic products.
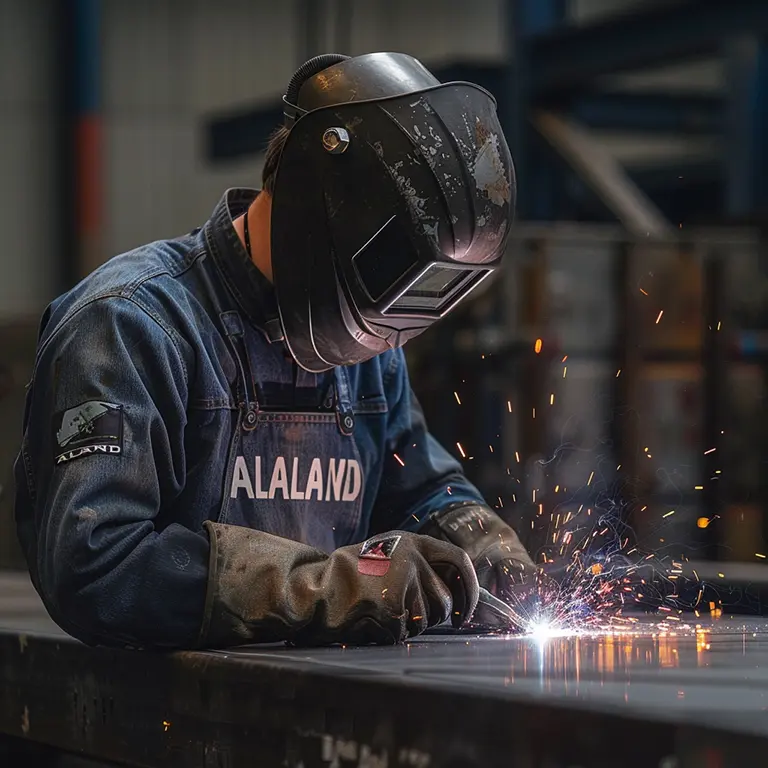
In this article, we discuss the introduction, standards, usage specifications and applicable scenarios of northern industrial welder. As a key manufacturing equipment, northern industrial welder plays an important role in various industrial production fields. By understanding the principles, performance and applications of industrial welding machines, we can better understand its importance in modern industrial production, and be able to select and use suitable equipment more effectively to improve production efficiency, ensure welding quality, and protect workers. Safety.
Whether in manufacturing, construction, aerospace, energy or other fields, northern industrial welders play a vital role. Through continuous technological innovation and quality management, industrial welding machines continue to develop and progress, making important contributions to the development of various industries.
I hope this article can help you better understand northern industrial welder and provide some reference and guidance for your work and research in related fields. If you have any other questions or require further information, please feel free to contact us and we will be happy to serve you.