Introduction to no gas welder and gas welder (Part 1)
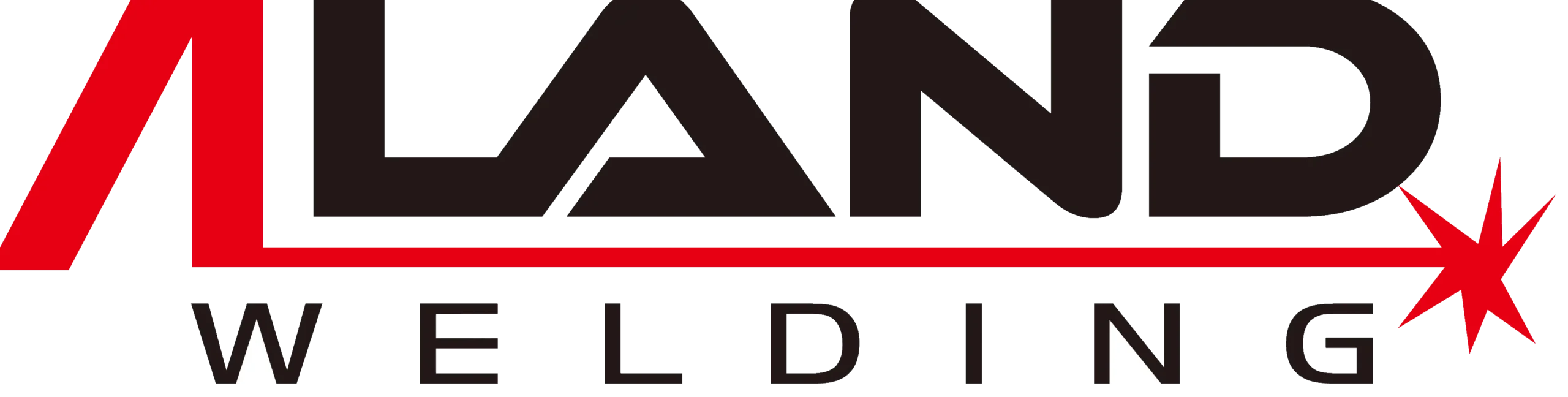
ALAND WELDING Let you feel the most sincere welding service
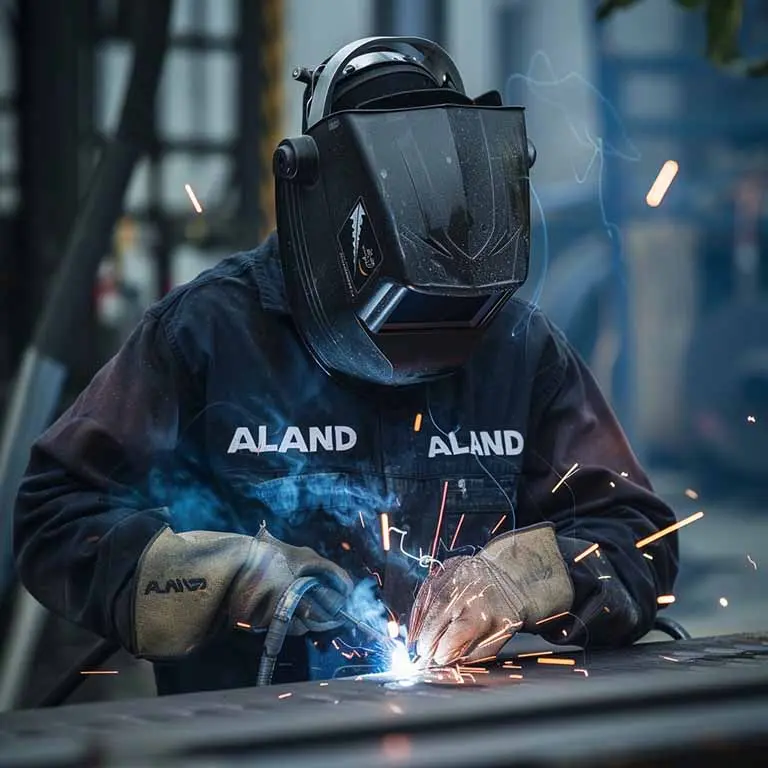
The main difference between a gas welder and a gasless welder is whether gas protection is used during the welding process.
Gas welder: gas welder uses shielding gas during the welding process. This gas is usually carbon dioxide, argon, or a mixture of the two. The main function of the gas is to protect the welding area from oxidation and pollution in the atmosphere and ensure welding quality and strength. Common types of gas welding machines include gas shielded welding machines (MIG, MAG, TIG, etc.).
Gasless welding machine: Gasless welding machine does not use external gas protection during the welding process. Instead, it relies on a special flux core or flux in the self-shielding wire to protect the weld area from oxidation. This kind of welding machine is usually suitable for outdoor use or in environments with poor ventilation. It is more convenient to use because it does not require additional gas bottles and related equipment.
This article mainly introduces readers to what a gas shielded welding machine is:
1. What is gas welder?
Cogas protective welders (cogas protective welders) actually have the ability to convert 220V and 380V AC power into low-voltage DC power. Cogas protective welders can generally be divided into two types according to the type of output power supply. One is AC gas protective welder. Welding machine; one is a DC gas shielded welding machine. The current conversion mode of the DC gas shielded welding machine is AC-DC-AC-DC. The gas shielded welding machine consists of a power supply and a wire feeder. The protective gases include CO2, CO2 and argon mixed gases, and CO2 and helium mixed gases. Make protective gas.
2. Characteristics of gas welder
(1) It has the advantages of light weight, small size, high efficiency and high reliability.
(2) The welding current can output a rectangular pulse waveform to achieve spray transition, making it easy to weld in all positions.
(3) It has automatic compensation function for power grid voltage fluctuations.
(4) Equipped with automatic protection functions such as overvoltage, undervoltage, overcurrent, and overheating.
(5) Automatic compensation according to the cable length to ensure good welding performance for different cable lengths.
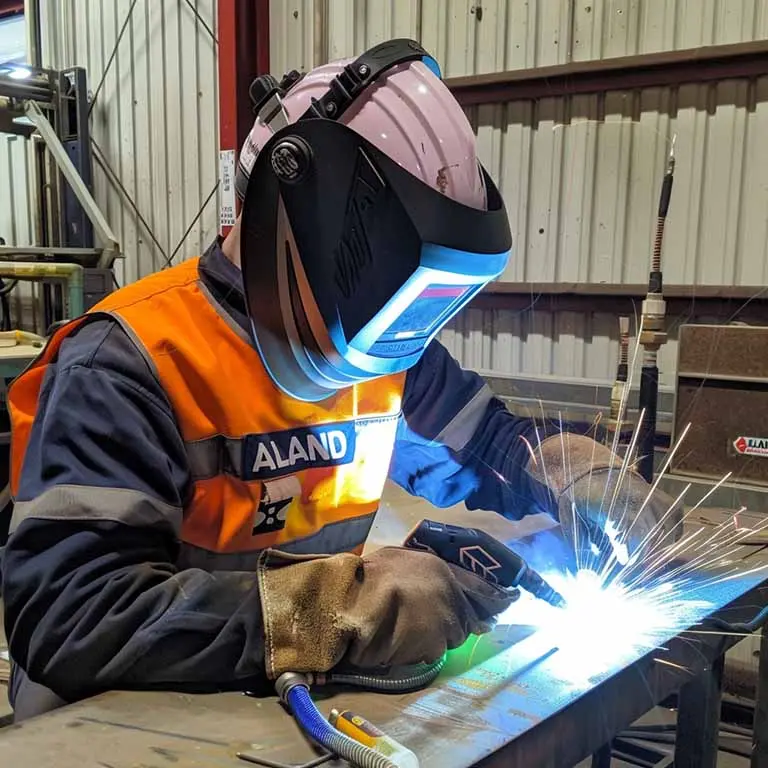
3. Advantages of gas welder
(1) High efficiency
Gas shielded welding machines are capable of continuous welding without the need for frequent replacement of welding rods or other consumables. The welding wire is continuously fed through the welding gun, making the welding process efficient and smooth. Compared with other welding methods, it has faster welding speed and higher production efficiency.
(2) Versatility
Gas welder can be used to weld a variety of materials, including steel, aluminum, stainless steel, copper, etc. This versatility makes it suitable for various industries such as manufacturing, construction, shipbuilding, automotive manufacturing, etc.
(3) Stable welding quality
Shielding gas can prevent oxygen and nitrogen in the atmosphere from reacting with molten metal, reducing welding defects such as pores and oxidation. In addition, the shielding gas ensures a more stable arc, reducing issues such as spatter and uneven welding. This stability improves welding quality.
(4) Easy to operate
The operation of a gas shielded welder is relatively simple, even for novice welders. Features such as continuous wire feeding and adjustable parameters allow welders to master skills faster and reduce training time. In addition, the gas shielded welding machine has automatic control and adjustment functions, which reduces the difficulty of operation.
(5) High welding speed
Due to the effect of the protective gas, the arc of gas welder is more stable and the welding speed is faster. This is very important for large projects or production line operations because a large amount of welding can be completed in a relatively short period of time.
(6) Reduce welding smoke
Using inert gases (such as argon, helium) or reactive gases (such as carbon dioxide) as shielding gases can reduce the fumes generated during welding. This helps improve the working environment and reduces health risks for welders.
(7) Flexibility
The gas shielded welding machine provides a variety of adjustable parameters, such as current, voltage, wire feed speed, etc., allowing it to adapt to different welding needs. This flexibility makes the gas shielded welding machine suitable for a variety of welding tasks, from thin plates to thick steel plates, and from simple structures to complex assemblies.
(8) Adapt to a variety of welding methods
The gas shielded welding machine can adapt to a variety of welding methods, such as flat welding, vertical welding, overhead welding, etc., providing more operating options. This adaptability enables welders to maintain welding quality in a variety of situations.
(9) Widely used
Gas shielded welding machines are widely used in automobile manufacturing, shipbuilding, construction, manufacturing and other fields because of their ability to provide high quality, efficiency and flexibility. Due to their versatility, gas shielded welding machines have become mainstream welding equipment in many industries.
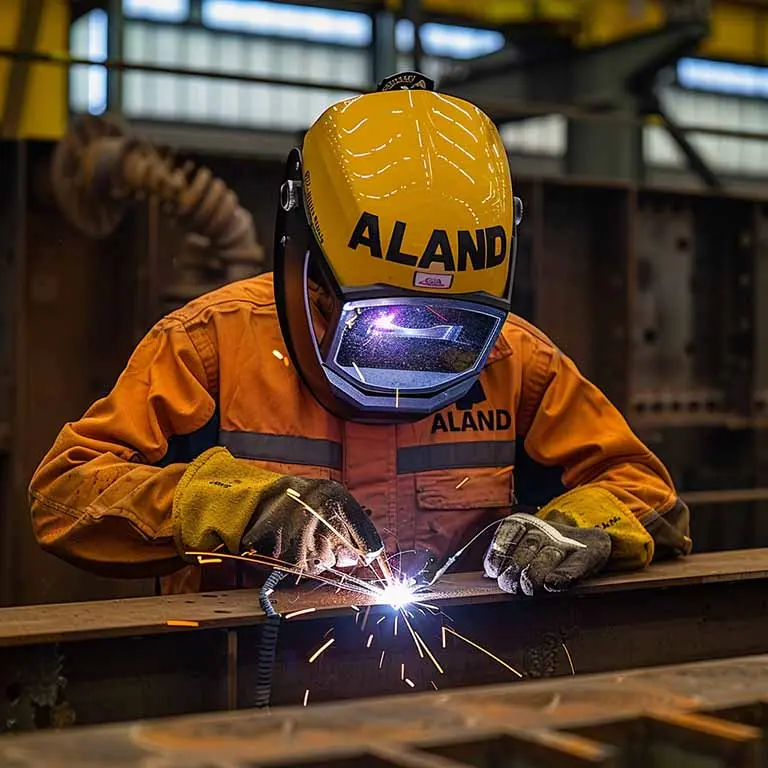
4. Disadvantages of gas welder
Gas shielded welding machines (MIG/MAG) perform well in many welding scenarios, but they also have some important drawbacks that may affect their usability or efficiency in certain applications. Here is a detailed analysis of these shortcomings:
(1) Sensitivity to wind and drafts
Gas shielded welders rely on shielding gas to prevent oxidation and contamination during the welding process. If used outdoors or in a windy environment, the protective gas is easily blown away, resulting in arc instability, reduced welding quality, and increased welding defects. Therefore, when welding outdoors, measures must be taken to protect the gas from being blown away by the wind, which may increase construction costs and complexity.
(2) Equipment costs are high
The initial equipment cost of a gas shielded welder is usually higher. In addition to the welding machine itself, users also need to purchase accessories such as welding guns, protective gas bottles, gas regulators, and wire feeders. The price of these equipment can be significantly higher than other welding methods, such as manual arc welding. Additionally, the ongoing supply and storage of shielding gas can increase operating costs.
(3) Gas supply and management
Gas shielded welding machines require a continuous supply of shielding gas, which requires reliable gas supply chain and storage management. In some areas, shielding gas may be difficult or costly to obtain. In addition, the storage and transportation of gas bottles require compliance with safety regulations, adding to the complexity of management.
(4) Surface preparation requirements before welding
Gas shielded welding machines have higher requirements for the cleanliness of the welding surface. Contaminants such as grease, dirt, and rust can affect welding quality and lead to welding defects such as pores and cracks. Therefore, surface preparation before welding must be very careful, including cleaning, rust removal, grinding, etc. This adds additional hours and costs.
(5) Maintenance and operation complexity
The structure and operation of gas shielded welding machines are more complex than other welding equipment. Users need to master a variety of operating parameters, such as current, voltage, wire feeding speed, protective gas flow, etc. Regular maintenance of the welding machine, cleaning of the welding gun, adjustment of the wire feeder, etc. all require certain technical knowledge. This complexity can increase training costs and maintenance time.
(6) Restrictions on welding positions
Gas shielded welders may not perform well in certain welding positions. For example, in non-planar positions such as vertical or overhead welding, the shielding gas may not effectively cover the welding area, resulting in arc instability and welding defects. In these cases, other welding methods may be more suitable.
(7) Limitations on welding thickness
Gas shielded welders may have difficulty welding thicker metals because the current and voltage may not be enough to adequately melt the thick metal. For thick plate welding, multiple welds may be required or other welding methods may be used, such as manual arc welding or tungsten inert gas (TIG) welding.
(8) Environmental and safety risks
The arc and high temperature generated by the gas welder can produce smoke and harmful gases. This requires good ventilation and protective measures to ensure the safety of the welder. The storage and transportation of gas bottles also require compliance with safety regulations, increasing potential safety risks.
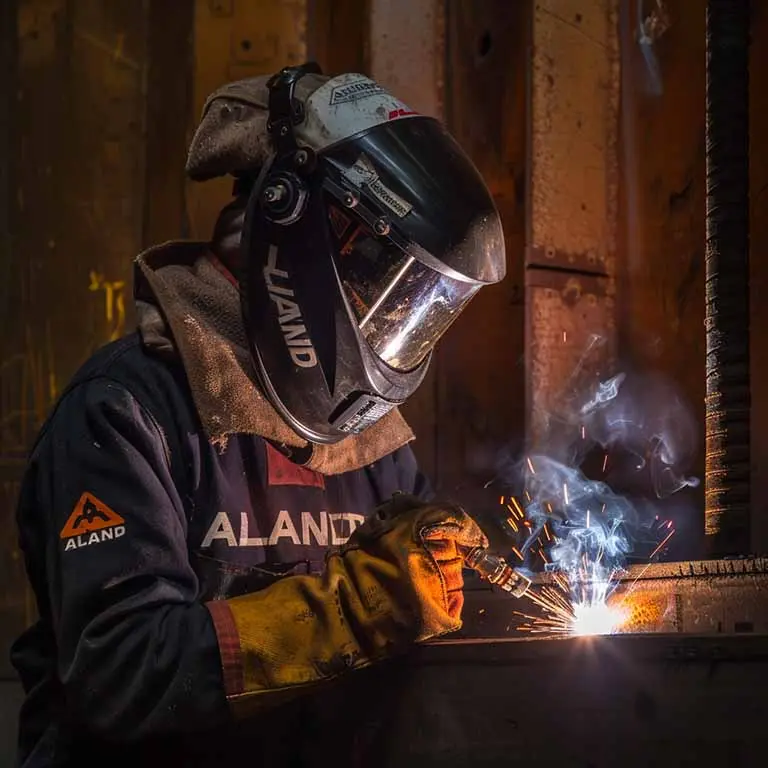
5. Precautions for gas welder
(1) Welding may cause fire or explosion
① During the welding process, protect yourself and others from being harmed by sparks and welding parts;
② Be sure not to weld where there are combustible materials, because flying sparks can easily cause combustion and lead to fire;
③ Be wary of fire and place a fire extinguisher in the welding area;
④ Do not use a gas shielded welder to defrost pipes;
⑤ When the equipment is out of use, please unplug the welding cable from the welding output end;
⑥ Before welding, on-site workers should hand over all flammable and explosive materials such as matches, lighters, etc.
(2) The smoke and gas generated by welding can harm health
① Maintain good ventilation when welding indoors;
② Do not weld near areas where degreasing, cleaning or spraying operations are taking place, because the heat and rays generated by the arc can react with water vapor in the air to produce highly toxic and irritating gases.
(3) Heating parts may cause serious burns
① Do not touch heating components directly with your hands;
② Can be welded with a welding gun after cooling.
(4) Arc rays can burn eyes and skin
① When welding or watching, you must wear a helmet with appropriate filters to protect your face and eyes;
② Use welding protective screens to protect others from interference and stimulation by sparks and strong light.
6. Application of gas welder in related industries
(1) Automobile manufacturing industry: In the automobile manufacturing process, industrial gas shielded welding machines are widely used for body welding to ensure the strength and aesthetics of the welds.
(2) Shipbuilding industry: In shipbuilding, industrial gas shielded welding machines are used to weld ship hull structures, providing high strength and corrosion resistance.
(3) Energy industry: In the power, oil and natural gas industries, industrial gas shielded welding machines are widely used to weld pipelines and storage tanks to ensure safety and reliability.
(4) Aerospace industry: The aerospace industry has extremely high requirements for welding quality and materials, and industrial gas shielded welding machines play an important role in this field.
(5) Heavy machinery manufacturing: When manufacturing heavy machinery and equipment, industrial gas shielded welding machines are used to connect large metal components to ensure strength and stability.
(6) Construction industry: In the welding of building structures, industrial gas shielded welding machines help improve the welding quality and ensure the structural stability of the building.
(7) Food processing industry: In the food equipment manufacturing process, industrial gas shielded welding machines are used to weld stainless steel equipment to ensure product hygiene standards.
(8) Electronic manufacturing industry: In the manufacturing of microelectronics and electronic components, industrial gas shielded welding machines are used to weld fine structures to ensure connection reliability.
(9) Railway transportation: In the manufacturing of railway vehicles, industrial gas shielded welding machines are widely used in the welding of car bodies and vehicle components.
(10) Metallurgical industry: In the metallurgical field, industrial gas shielded welding machines are used to weld metal materials to meet the material performance requirements of different industries.
As a representative of modern welding technology, industrial gas shielded welding machines provide efficient and precise welding solutions for manufacturing industries in all walks of life. It not only improves weld quality and welding efficiency, but also reduces the need for subsequent processing, bringing significant advantages to industrial production.
With the continuous advancement of science and technology, industrial gas shielded welding machines will continue to evolve and improve, contributing more to the development of the manufacturing industry. Let us look forward to the future of this technology together and witness the more surprises and achievements it brings to the industry. Thank you for reading this blog about industrial gas shielded welding machines. I hope it will be inspiring and helpful to you. If you have any questions or additions, please feel free to leave a message and we look forward to continuing the discussion with you!