Fusion welding, Pressure welding and Brazing - three types of welding give you a comprehensive understanding of the welding process
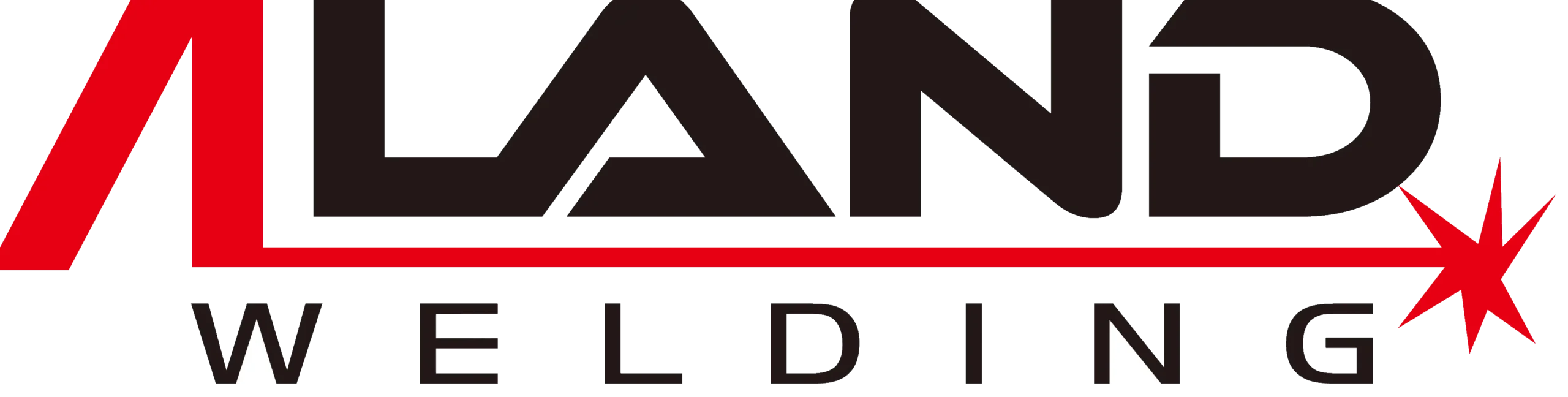
ALAND WELDING Let you feel the most sincere welding service
Welding, also known as welding and welding, is a manufacturing process and technology that uses heat, high temperature or high pressure to join metal or other thermoplastic materials such as plastics. According to the state of the metal during the welding process and the characteristics of the process, welding methods can be divided into three categories: fusion welding, pressure welding and brazing.
Fusion welding
The workpieces to be joined are heated to partially melt them to form a molten pool. After the molten pool cools and solidifies, they are joined. If necessary, melt fillers can be added to assist;
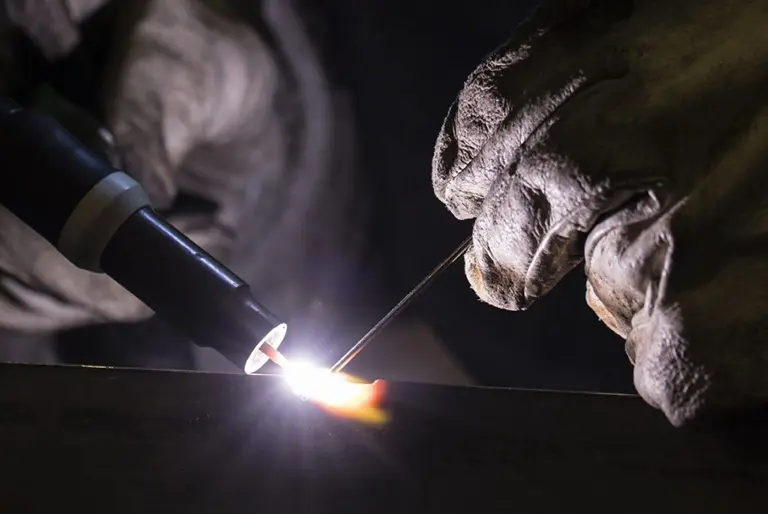
1. Laser welding
Laser welding uses the heat generated by bombarding the workpiece with a focused laser beam as an energy source to weld. It can weld various metal materials and non-metal materials such as carbon steel, silicon steel, aluminum and titanium and other metals and their alloys, tungsten, molybdenum and other refractory metals and dissimilar metals, as well as ceramics, glass and plastics. Currently it is mainly used in electronic instruments, aviation, aerospace, nuclear reactors and other fields. Laser welding has the following characteristics:
(1) The energy density of the laser beam is high, the heating process is extremely short, the welding spots are small, the heat affected zone is narrow, the welding deformation is small, and the dimensional accuracy of the weldment is high;
(2) It can weld materials that are difficult to weld with conventional welding methods, such as welding tungsten, molybdenum, tantalum, zirconium and other refractory metals;
(3) Non-ferrous metals can be welded in the air without the need for external protective gas;
(4) The equipment is complex and costly.
2. Gas welding
Gas welding is mainly used for welding thin steel plates, low-melting point materials (non-ferrous metals and their alloys), cast iron parts, carbide cutting tools and other materials, as well as repair welding of worn and scrapped parts, flame correction of component deformation, etc.
3. Arc welding
It can be divided into manual arc welding and submerged arc welding.
(1)Manual arc welding can perform multi-position welding such as flat welding, vertical welding, horizontal welding and overhead welding. In addition, because arc welding equipment is light and flexible in transportation, welding operations can be performed anywhere where there is a power source. Suitable for welding of various metal materials, various thicknesses and various structural shapes;
(2) Submerged arc welding is generally only suitable for flat welding positions and is not suitable for welding thin plates with a thickness less than 1mm. Due to its large penetration depth. High productivity and high degree of mechanized operation, submerged arc welding is suitable for welding long welds of medium and thick plate structures. The materials that can be welded by submerged arc welding have developed from carbon structural steel to low alloy structural steel, stainless steel, heat-resistant steel, etc., as well as certain non-ferrous metals, such as nickel-based alloys, titanium alloys, and copper alloys.
4. Gas welding
Arc welding that uses external gas as the arc medium and protects the arc and welding zone is called gas shielded arc welding, or gas arc welding for short. Gas welding is usually divided into non-melting electrode (tungsten electrode) inert gas shielded welding and melting electrode gas shielded welding, oxidation mixed gas shielded welding, CO2 gas shielded welding and tubular wire gas shielded welding according to whether the electrode is melted and the shielding gas is different.
Among them, non-melting extremely inert gas shielded welding can be used for the welding of almost all metals and alloys. However, due to its high cost, it is usually used for welding non-ferrous metals such as aluminum, magnesium, titanium and copper, as well as stainless steel and heat-resistant steel. In addition to the main advantages of non-melting arc gas shielded welding (can be welded in various positions; suitable for welding of non-ferrous metals, stainless steel, heat-resistant steel, carbon steel, alloy steel and most metals), gas shielded arc welding also has the following advantages: It also has the advantages of faster welding speed and higher deposition efficiency.
5. Plasma arc welding
Plasma arc is widely used in welding, spraying and cladding. It can weld finer and thinner workpieces (such as the welding of extremely thin metals below 1mm).
6. Electroslag welding
Electroslag welding can weld various carbon structural steels, low-alloy high-strength steels, heat-resistant steels and medium-alloy steels. It is now widely used in the manufacturing of boilers, pressure vessels, heavy machinery, metallurgical equipment and ships. In addition, electroslag welding can be used for large-area surfacing and repair welding.
7. Electron beam welding
Electron beam welding equipment is complex, expensive, and requires high maintenance. Welding parts have high assembly requirements, and their size is limited by the size of the vacuum chamber. They need to be protected from X-rays. Electron beam welding can be used to weld most metals and alloys as well as workpieces requiring small deformation and high quality. At present, electron beam welding has been widely used in precision instruments, instruments and electronic industries.
Pressure welding
The welding process must exert pressure on the weldment and is divided into resistance welding and ultrasonic welding.
1. Resistance welding
There are four main resistance welding methods, namely spot welding, seam welding, projection welding and butt welding. Spot welding is suitable for stamped and rolled thin plate components that can be overlapped, the joints are not required to be airtight, and the thickness is less than 3mm. Seam welding is widely used in thin plate welding of oil drums, cans, radiators, aircraft and automobile fuel tanks. Projection welding is mainly used to weld stamping parts of low carbon steel and low alloy steel. The most suitable thickness for projection welding of plates is 0.5-4mm.
2. Ultrasonic welding
Ultrasonic welding is in principle suitable for welding most thermoplastics.
Brazing
A metal material with a lower melting point than the base metal is used as the solder, and the liquid solder is used to wet the base metal, fill the gap, and mutually diffuse with the base metal to achieve the connection of the weldment.
1. Flame brazing
Flame brazing is suitable for brazing carbon steel, cast iron, copper and its alloys and other materials. Oxyacetylene flame is a commonly used flame.
2. Resistance brazing
Resistance brazing is divided into two methods: direct heating and indirect heating. Indirect heating resistance brazing is suitable for brazing of weldments with large differences in thermophysical properties and thicknesses.
3. Induction brazing
Induction brazing is characterized by fast heating, high efficiency, local heating, and easy automation. According to the protection method, it can be divided into induction brazing in air, induction brazing in protective gas and induction brazing in vacuum.
Articles you may be interested in:
The difference between TIG VS MIG?
What is a plasma cutting machine ?
10 Common Types of Welding And Various Welding Principles?
Why choose TIG welding? 4 major benefits
Welder skills and knowledge: What basic knowledge do beginners need to master?
The Most Complete Welding Defects And Solutions, A Must-read for Welders!(1)
The Most Complete Welding Defects And Solutions, A Must-read for Welders!(2)