co2 welding principle and advantages and disadvantages
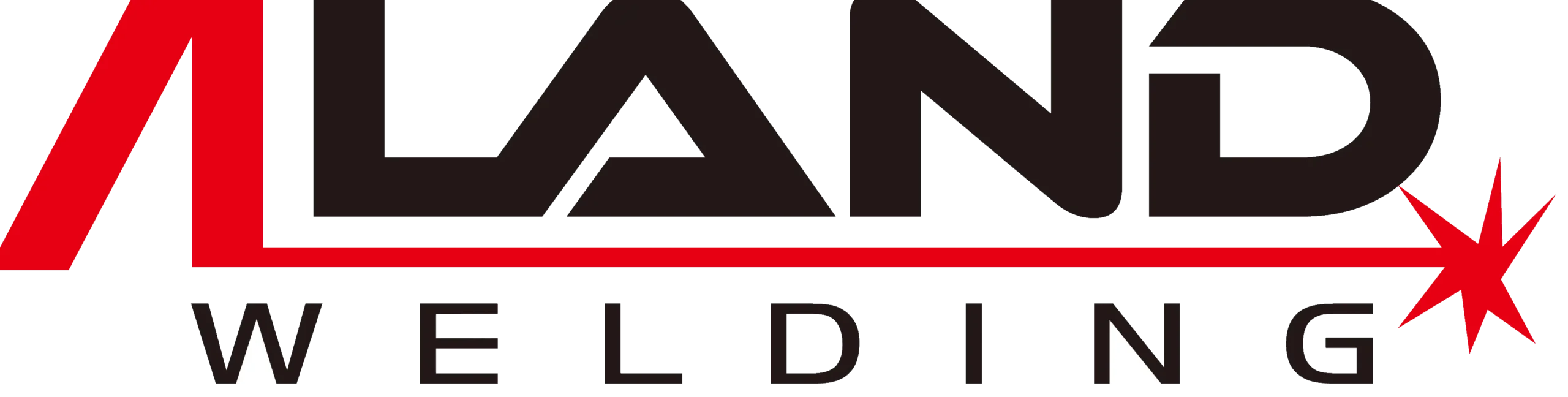
ALAND WELDING Let you feel the most sincere welding service
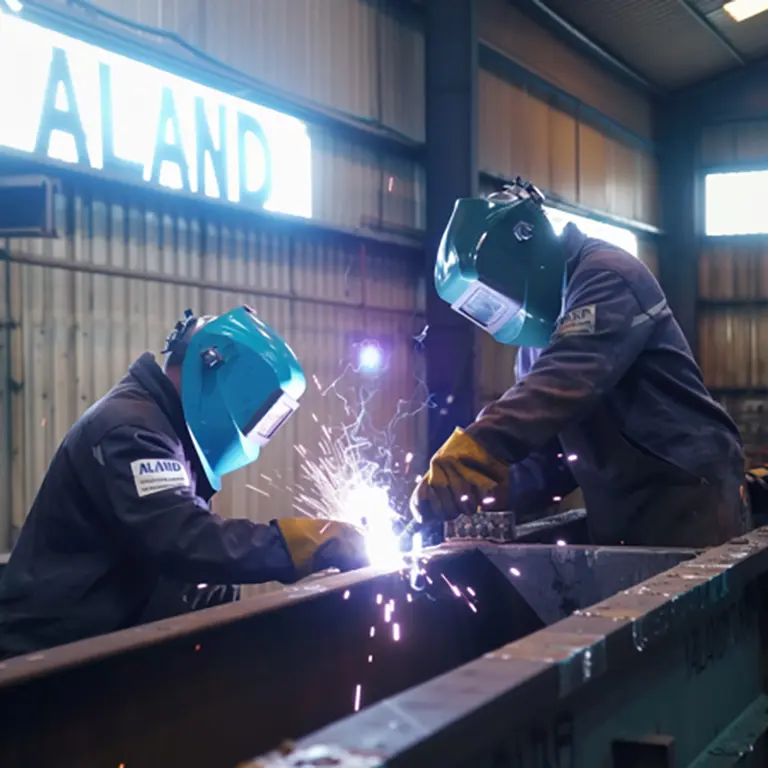
1. Concept of co2 welding
co2 welding (Gas Metal Arc Welding, GMAW), also known as MIG welding (Metal Inert Gas Welding) or MAG welding (Metal Active Gas Welding), is a common welding method that uses carbon dioxide (CO2) as a shielding gas. Used to protect the welding area to prevent oxygen from entering.
In co2 welding, an arc is formed between the electrode and the workpiece, melting the metal on the surface of the electrode and the workpiece to form a weld. At the same time, a protective atmosphere is formed by spraying carbon dioxide gas around the welding area to prevent the oxidation reaction between oxygen in the air and the molten metal, thereby ensuring the welding quality.
2. Principle of co2 welding
Carbon dioxide gas shielded arc welding (CO2 welding for short) is a welding method using carbon dioxide gas as a protective gas. (Sometimes a mixed gas of CO2+Ar is used). In terms of application, the operation is simple and suitable for automatic welding and all-round welding. It has poor wind resistance during welding and is suitable for indoor work. Because of its low cost and easy production of carbon dioxide gas, it is widely used in various large and small enterprises. Due to the special influence of the thermal physical properties of carbon dioxide gas, when using conventional welding power sources, the molten metal at the end of the welding wire cannot form a balanced axial free transition, and short circuit and droplet necking and blasting are usually required. Therefore, unlike MIG welding Compared with free transition, there is more splash. However, if a high-quality welding machine is used and the parameters are appropriately selected, a very stable welding process can be achieved and spatter can be reduced to a minimum. Due to the low price of the shielding gas used, the welding seam is well formed when short-circuit transition is used, and the use of welding wire containing deoxidizer can obtain high-quality welding joints without internal defects. Therefore, this welding method has become one of the most important welding methods for ferrous metal materials.
3. Introduction to the advantages of co2 welding
(1) Low welding cost. Its cost is only 40~50% of that of submerged arc welding and electrode arc welding.
(2) High production efficiency. Its productivity is 1 to 4 times that of electrode arc welding.
(3) Easy to operate. Open arc, no limit to the thickness of the workpiece, can be welded in all positions and can be welded downward.
(4) The weld seam has high crack resistance. Welds are low in hydrogen and contain less nitrogen.
(5) The deformation after welding is small. The angular deformation is five thousandths and the unevenness is only three thousandths.
(6) Welding spatter is small. When using ultra-low carbon alloy welding wire or flux cored welding wire, or adding Ar to CO2, welding spatter can be reduced.
4. Introduction to the disadvantages of co2 welding
co2 welding may encounter some defects and problems in practice, and these defects may affect the welding quality and performance. The following are some common defects of co2 welding:
Spatter: Spatter from the arc is a common problem during CO2 shielded welding. These spatters may cause unevenness in the weld area, affecting the quality and appearance of the weld.
Porosity: Porosity is another problem that may occur during welding, especially when there is poor gas flow during the welding process or there are impurities such as oil, moisture, etc. on the surface of the workpiece. Porosity may reduce the strength and tightness of the welded joint.
Porosity: Porosity is another problem that may occur during welding, especially when there is poor gas flow during the welding process or there are impurities such as oil, moisture, etc. on the surface of the workpiece. Porosity may reduce the strength and tightness of the welded joint.
Welding deformation: Due to the high temperature and high energy input of co2 welding, large deformation of the workpiece may occur during the welding process, especially when welding thin plates or large-sized workpieces.
Welding cracks: If the welding parameters are improperly selected or the workpiece design is unreasonable, co2 welding may cause cracks in the welded joints, affecting the welding quality and reliability.
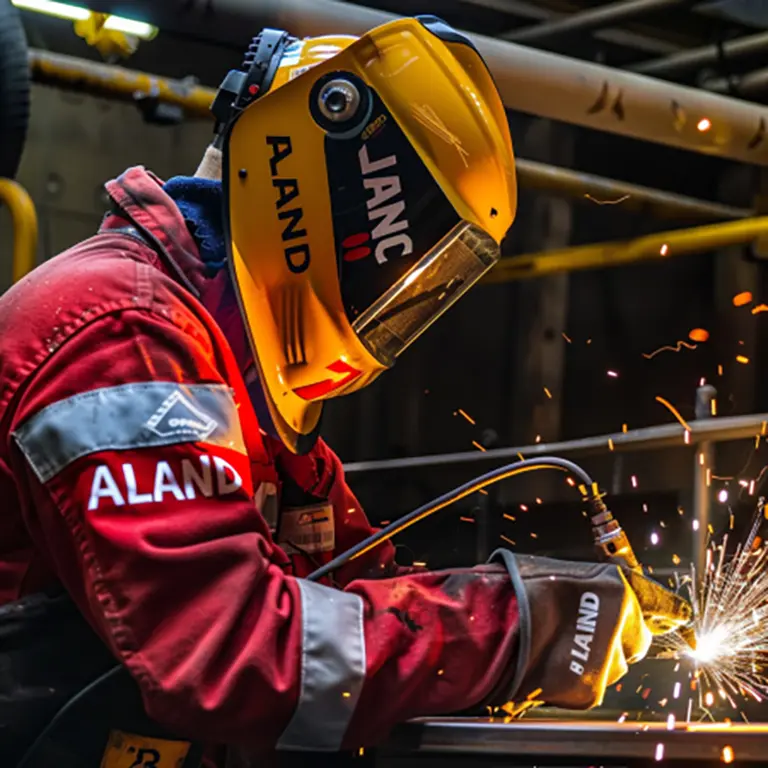
5. Welding smoke prevention and control
Composition and characteristics of welding smoke
Welding fume is formed by the oxidation and condensation of vapor generated by metal and non-metallic substances under superheated conditions. Therefore, the chemical composition of welding smoke depends on the composition of the welding materials (welding wire, electrode, flux, etc.) and the materials being welded, and the ease of evaporation. Welding materials and materials to be welded with different compositions will produce welding fumes of different compositions during welding.
The characteristics of welding fume are:
(1) The particles of welding smoke are small and the smoke is in the form of fragments with a particle size of about 1µm. (2) Welding fumes are highly viscous.
(3) The temperature of welding fume is relatively high. In the exhaust duct and filter element, the air temperature is 60 to 80°C.
(4) The amount of dust generated during the welding process is large. Generally speaking, the amount of smoke generated by a welder for 1 day is about 60 to 150g. The amount of dust generated per minute during welding (during cutting) by several welding (cutting) methods and the amount of dust generated per kilogram of melted welding material
Amount of dust generated by welding methods
carbon dioxide welding
Solid welding wire (diameter 1.6mm) 450~650 5~8
Flux cored wire (diameter 1.6mm) 700~900 7~10
CO2 gas shielded welding smoke hazards
Pollution in the CO2 gas shielded welding area is divided into two categories: chemical pollution and physical pollution according to different formation methods.
Chemical pollution
Chemical pollution refers to the harmful gases and smoke produced during CO2 gas shielded welding. When performing CO2 gas shielded welding, some harmful substances will be produced around the arc in the welding area.
The harmful substances produced by CO2 gas shielded welding can be divided into two categories. One category is harmful gases, mainly carbon dioxide (CO2), carbon monoxide (CO), nitrogen dioxide (NO2) and ozone (O3). One type is soot, the main components of which are ferric oxide (Fe2O3), silicon dioxide (SiO2) and manganese oxide (MnO). These harmful substances, except for carbon dioxide, which is ejected from the welding gun to protect the arc and molten pool and remains around the welding area before welding is used up, the rest of the harmful substances are produced from the welding arc and welding molten pool.
Physical pollution
Physical pollution mainly includes: ultraviolet, infrared, etc. generated by high-temperature arc light of CO2 gas shielded welding.
CO2 gas shielded welding smoke purification
- Natural ventilation
- Cartridge-type mobile welding fume purifier.
- High negative pressure welding fume dust collector
Natural ventilation has the lowest cost. Pure natural methods are mainly used to reduce the concentration of welding smoke in the workshop by opening windows for ventilation and setting up blinds.
The cartridge-type mobile welding smoke purifier aims the universal suction arm at the point where the welding smoke is generated. Through the negative pressure generated by the system, the dust and toxic and harmful gases generated in the welding smoke are inhaled into the purifier and collected. Cartridge-type mobile welding fume purifiers have a wide range of applications. It is convenient, flexible and easy to move. Can meet various flexible working conditions.
The high negative pressure welding smoke dust collector mainly connects the 50mm diameter hose directly to the welding head. The dust collector works when the welding machine is working, and stops when the welding machine stops. This ensures effective treatment of welding fume while using the minimum air volume. In addition, the high negative pressure welding smoke dust collector can be connected to a hose up to 20m long, and can be effectively connected to automatic welding machine heads. It overcomes the disadvantage that the mobile suction arm needs to be moved manually. Now we have achieved automation, and the network purification effect is remarkable.
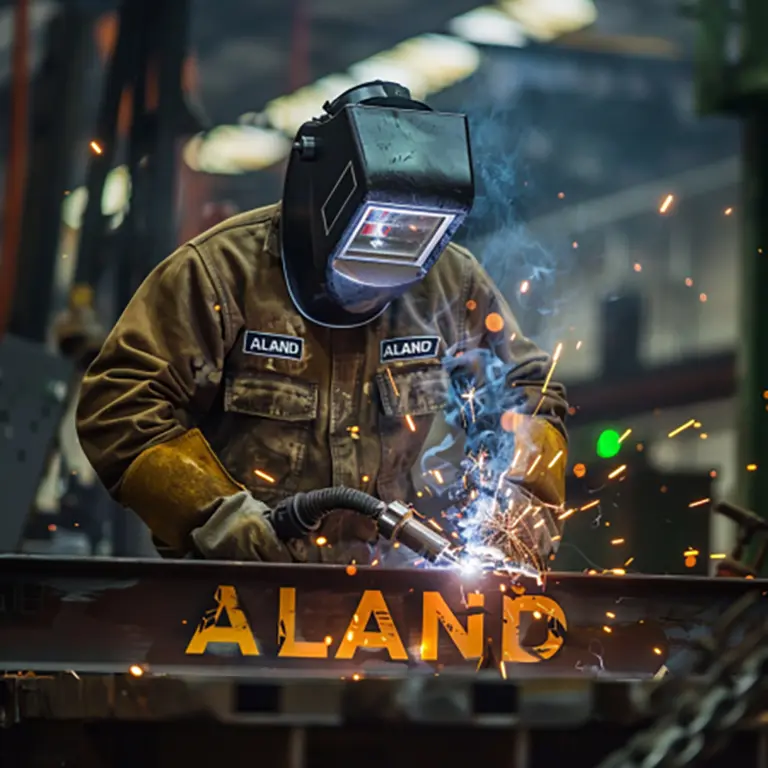
6. Applicable scenarios for co2 welding
co2 welding is widely used in many industrial and manufacturing fields, especially for carbon steel welding. The following are some applicable scenarios:
(1) Structural welding: co2 welding is commonly used in structural welding, such as automobile manufacturing, bridge construction, construction projects, etc. Due to its high efficiency and relatively low cost, it is ideal for high-volume production.
(2) Steel structure manufacturing: In the steel structure manufacturing industry, co2 welding is usually used to connect large steel components, such as steel beams, steel columns, etc. This welding method can complete the welding task quickly and efficiently.
(3) Pipeline welding: In petroleum, natural gas, chemical and other industries, co2 welding is widely used for pipeline welding. It can ensure the quality and sealing of pipeline welds and is suitable for high pressure and high temperature environments.
(4) Vehicle manufacturing: In the fields of automobile, ship and railway vehicle manufacturing, co2 welding is widely used to connect car bodies and structural parts, such as body panels, chassis, etc. It can provide a strong welding connection and has a fast welding speed.
(5) Machinery manufacturing: In the machinery manufacturing industry, co2 welding is often used to manufacture mechanical parts and equipment. It can weld workpieces of various shapes and sizes while ensuring welding quality and production efficiency.