Introduction to welding stainless steel characteristics
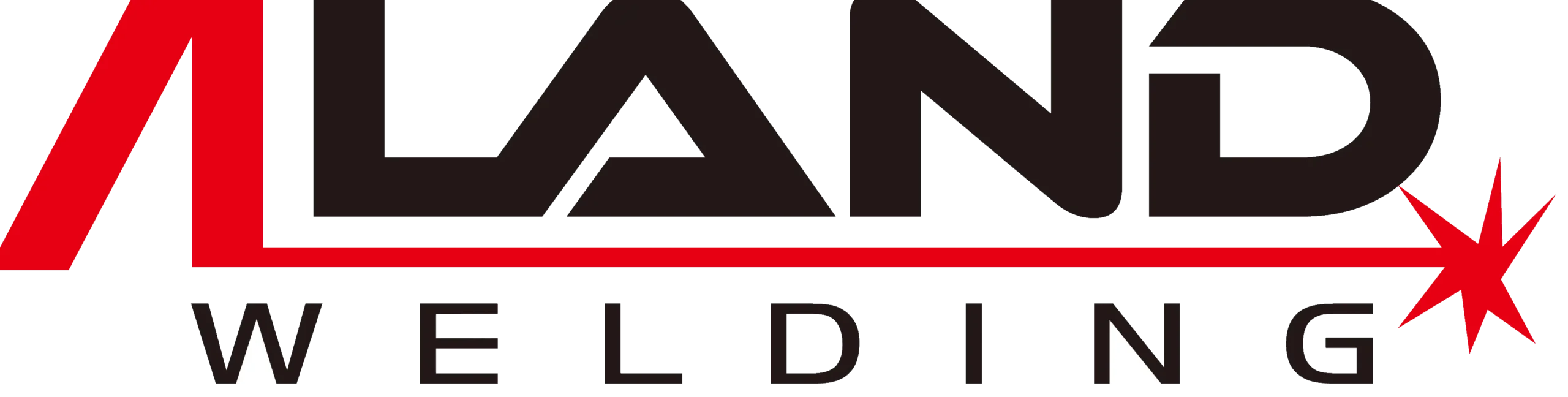
ALAND WELDING Let you feel the most sincere welding service
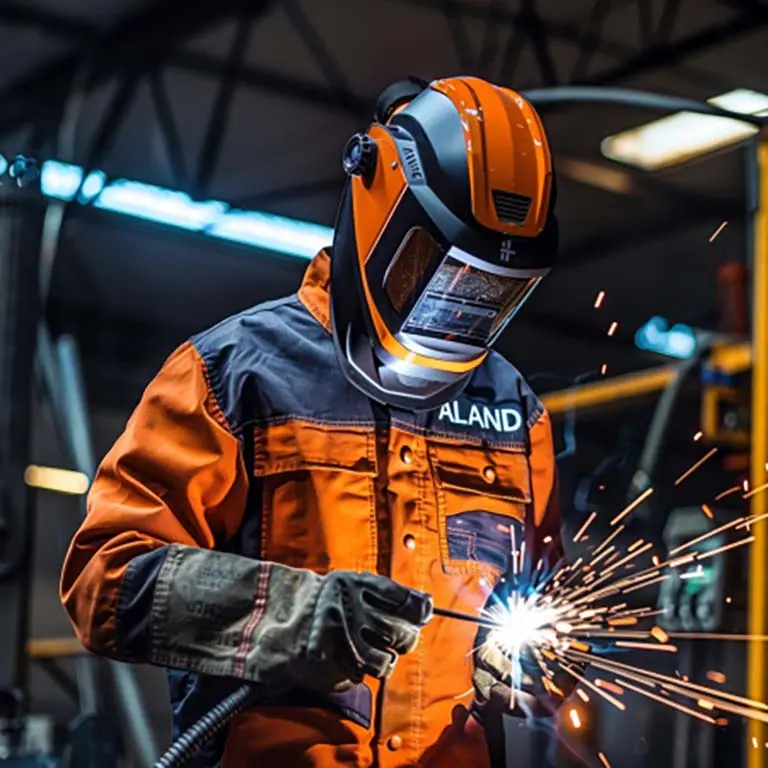
1. Introduction to stainless steel welding
Welding stainless steel refers to the process of joining stainless steel materials into a whole through heating or pressure. Stainless steel requires special attention when welding due to its high alloy content and unique physical and chemical properties. Common welding methods include TIG (tungsten inert gas welding), suitable for thin wall and precision welding; MIG (melting inert gas welding), suitable for thicker materials; arc welding, suitable for structural welding; and laser welding, suitable for for high-precision welding. During welding, pure argon or mixed gas must be used for protection to prevent oxidation, and parameters such as current, voltage, and welding speed must be strictly controlled. Pre-weld cleaning and post-weld treatment are also very important to prevent pores, cracks and other welding defects and ensure the quality and strength of the weld.
2. Characteristics of welded stainless steel
(1) Corrosion resistance Stainless steel is known for its excellent corrosion resistance, which must also be maintained after welding. Selecting the appropriate welding materials (such as welding wires and electrodes) and the correct welding process can ensure that the weld has corrosion resistance similar to that of the base metal. Use protective gas (such as pure argon) during the welding process to prevent oxidation and prevent the welding area from being eroded by corrosive media.
(2) High-temperature strength Stainless steel can still maintain good strength and toughness at high temperatures, which makes it suitable for equipment and structures in high-temperature environments. However, attention must be paid to controlling heat input during welding to avoid degradation of material properties due to overheating.
(3) Thermal Expansion Coefficient Stainless steel has a high thermal expansion coefficient and is prone to thermal stress and deformation during welding. In order to reduce deformation and residual stress, it is necessary to adopt reasonable welding sequences and fixtures, and to control welding parameters such as current, voltage and welding speed, especially when welding thin plates, precise control is required.
(4) Various welding methods Stainless steel can use a variety of welding methods, including: TIG welding (tungsten inert gas shielded welding): suitable for welding thin-walled stainless steel and precision components, with high weld quality and strong controllability of the welding process. MIG welding (melting inert gas shielded welding): suitable for thicker stainless steel materials, with high welding efficiency, but attention must be paid to spatter control. Arc welding: The equipment is simple and suitable for structural welding, but the quality of the weld is limited. Laser welding: used for welding with high precision and high quality requirements, but the equipment cost is high, suitable for welding parts with complex shapes and high requirements.
(5) Use of shielding gas When welding stainless steel, pure argon or an argon mixture is usually used as a shielding gas to prevent oxidation during the welding process. The flow and purity of the shielding gas directly affect the quality and appearance of the weld.
(6) Pre-welding treatment Before welding, the stainless steel surface must be thoroughly cleaned to remove grease, scale and other impurities. Incomplete cleaning can lead to welding defects such as pores and slag inclusions, affecting the quality of the weld. Common cleaning methods include mechanical grinding and chemical cleaning.
(7) Heat-affected zone control When welding stainless steel, heat input needs to be strictly controlled to prevent grain coarsening and embrittlement in the heat-affected zone. Especially when welding stainless steel with high carbon content, excessive heat input will lead to sensitization of the heat-affected zone and increase its susceptibility to intergranular corrosion. Appropriate welding parameters and cooling rates are key to controlling the quality of the heat affected zone.
(8) Weld aesthetics: The welds after stainless steel welding are usually required to be beautiful and smooth, especially in decorative applications. High-quality welding processes and technical levels have a significant impact on weld quality. A superior weld appearance can be achieved through proper welding parameter settings and welding techniques such as multi-pass welding and grinding.
(9)Post-processing After welding is completed, it is sometimes necessary to perform post-processing on the weld, such as passivation and pickling, to remove oxide scale and other impurities during the welding process and further improve the corrosion resistance and aesthetics of the weld.
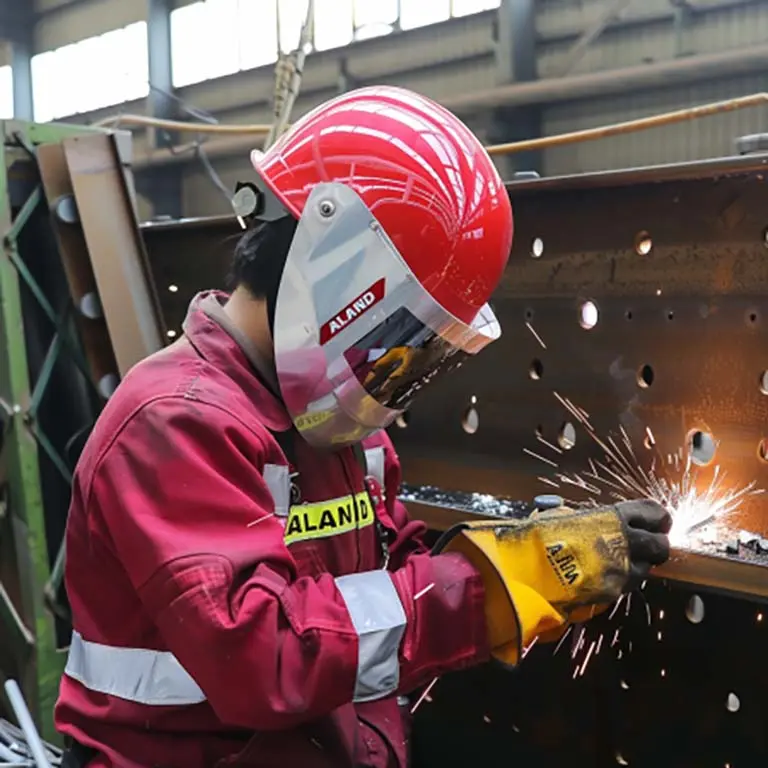
3. Advantages of stainless steel welding
(1) Excellent corrosion resistance Stainless steel can still maintain its excellent corrosion resistance after welding, which is particularly important for equipment and structures that need to withstand harsh environments (such as oceans, chemical plants, etc.). Correct welding procedures and material selection ensure that the weld has the same corrosion resistance as the base material.
(2) High strength and durability The structure of welded stainless steel has high strength and durability and can withstand high mechanical stress and repeated loads. This makes stainless steel welding widely used in fields that require high strength and long service life, such as construction, bridges, automobiles, and aerospace.
(3) Beautiful appearance. The welded seam after stainless steel welding can achieve a very beautiful effect through appropriate processing and has a good visual effect. This is particularly important in applications that require high appearance quality, such as architectural decoration, art production, and kitchen appliances.
(4) High temperature resistance Stainless steel can still maintain good mechanical properties in high temperature environments, and the welded components can be used in high temperature environments for a long time without failure. This makes stainless steel welding very advantageous in high temperature equipment such as boilers, heat exchangers and exhaust systems.
(5) Good low-temperature properties. Certain types of stainless steel (such as austenitic stainless steel) can maintain high toughness and strength at low temperatures and are suitable for use in low-temperature environments and refrigeration equipment, such as liquefied natural gas (LNG) storage tanks and transportation. equipment.
(6) Easy to maintain and clean. The surface of stainless steel is smooth and not easy to accumulate dirt. The welded structure and equipment are easy to clean and maintain, have a long service life and low maintenance costs. This is particularly important for industries with high hygiene requirements such as food processing and pharmaceutical equipment.
(7) Selection of various welding methods Stainless steel can use a variety of welding methods, such as TIG welding, MIG welding, laser welding and arc welding, etc. The most suitable welding process can be selected according to specific application requirements. This diversity makes stainless steel welding adaptable and has a wide range of applications.
(8) Reliable welded joints Through appropriate welding processes, stainless steel welded joints can achieve high strength and high reliability, and the performance of the weld can be comparable to that of the base material. Suitable for use in high-demand structures and equipment such as pressure vessels and high-pressure pipelines.
(9) Good processability Stainless steel materials have good processability and are easy to cut, form and weld. Cracks and deformations are less likely to occur during the welding process, ensuring welding quality and precision.
(10) Environmentally friendly stainless steel is a completely recyclable material. It still maintains its environmentally friendly properties after welding and meets the requirements of sustainable development. This is increasingly valued in modern industry.
In general, these advantages of stainless steel welding make it the material of choice in many industries, able to meet many requirements such as high strength, corrosion resistance, high temperature resistance, low temperature resistance, and aesthetics.
4. Defects and prevention of welded stainless steel
(1) Stomata
Reason: Insufficient protective gas or unstable gas flow during welding. The welding surface is unclean, with oil stains, rust spots or moisture present. The material itself contains impurities or oxides.
Prevention and treatment methods: Use high-purity protective gas, such as pure argon, to ensure stable gas flow. Thoroughly clean the welding surface before welding to remove oil, rust and moisture. Choose high-quality welding materials and avoid materials containing impurities.
(2) Cracks
Reason: The cooling rate of the welding heat affected zone is too fast. The welding parameters are set improperly, such as the welding current is too large or the welding speed is too fast. The material contains high carbon or other brittle elements.
Prevention and control methods: Preheat the welding area, control the cooling rate, and perform post-weld heat treatment if necessary. Set welding parameters reasonably to avoid excessive heat input. Use low carbon or stabilized stainless steel materials.
(3) Weld undercut
Reason: The welding current is too large or the welding speed is too fast. The angle of the welding gun or the welding posture is improper.
Prevention and treatment methods: Adjust the welding current and welding speed, and select appropriate welding parameters. Ensure correct welding gun angle and welding posture.
(4) Slag inclusion
Reason: The slag was not completely discharged during the welding process and remained in the weld. The quality of welding materials is not good and contains many impurities. Prevention and control methods: Use high-quality welding materials to reduce impurity content. Improve welding technology to ensure that slag can be completely discharged.
(5) Sensitization of heat affected zone
Reason: Excessive welding heat input causes grain growth and carbide precipitation in the heat-affected zone, increasing the tendency of sensitization. Stainless steel with high carbon content is prone to sensitization during welding.
Prevention and treatment methods: Control welding heat input to avoid excessive welding heat-affected zones. Choose low-carbon or stabilized stainless steel materials, such as 304L, 316L, etc.
(6) Deformation
Reason: The thermal expansion coefficient of stainless steel is high, and thermal stress and deformation are easily generated during the welding process. Improper welding sequence and lack of proper fixing and support during welding.
Prevention and control methods: Reasonably arrange the welding sequence and use clamps to fix the welding parts. Use segmented welding or symmetrical welding to reduce thermal stress and deformation.
(7) Welding spatter
Reason: Excessive current or improper shielding gas flow during MIG welding. Welding materials are of poor quality and contain impurities.
Prevention and treatment methods: Adjust the welding current and protective gas flow to ensure appropriate welding parameters. Use high-quality welding materials to reduce impurity content.
(8) Uneven color of welds
Reason: The protective gas coverage is uneven during the welding process. The welding speed is unstable, resulting in oxidation of the weld surface.
Prevention and treatment methods: Ensure a stable flow of protective gas and maintain uniform gas coverage during the welding process. Maintain stable welding speed and reduce oxidation.
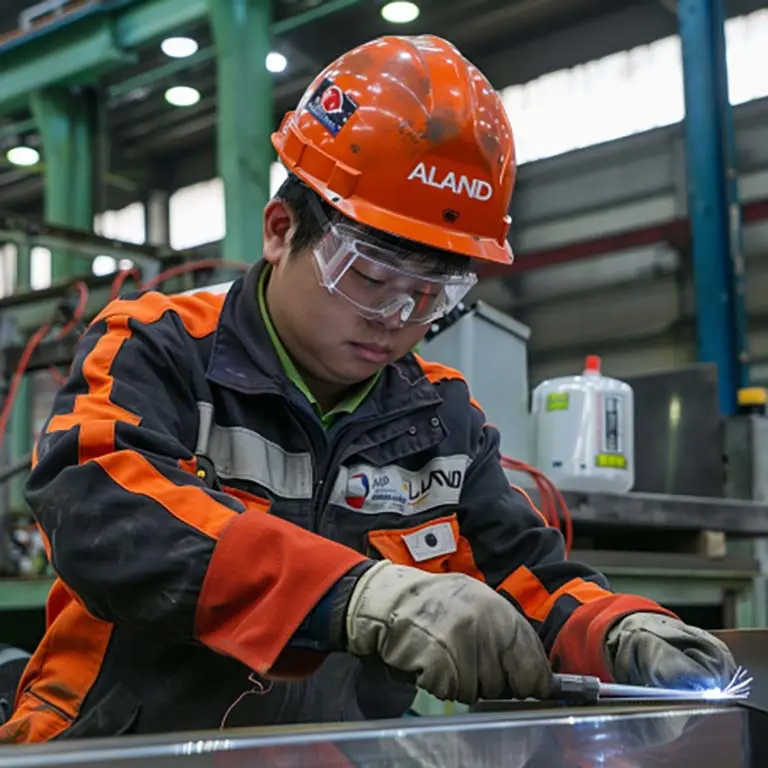
5. Things to note when welding stainless steel
(1) Choose the appropriate welding method. Choose the appropriate welding method according to the type and thickness of the stainless steel material: TIG welding (tungsten inert gas shielded welding): suitable for thin plates and precision welding, with high weld quality. MIG welding (melting inert gas welding): suitable for thicker materials and has high welding efficiency. Arc welding: often used for structural welding with simple equipment. Laser welding: used for welding with high precision and quality requirements.
(2) Use of shielding gas Use pure argon or an argon mixture (such as argon-helium mixture) as a shielding gas to prevent oxidation during the welding process. The shielding gas flow should be stable and cover the welding area.
(3) Selection of welding materials: Use welding wires and electrodes that match the base metal to ensure that the weld has physical and chemical properties similar to those of the base metal. Commonly used welding materials include 308, 309, 316 and other series.
(4) Clean the welding surface thoroughly before welding to remove grease, scale, rust spots and other impurities. Cleaning methods include mechanical grinding, chemical cleaning, etc.
(5) Preheating and post-heat treatment For some types of stainless steel (such as high-carbon or martensitic stainless steel), preheating is required before welding to reduce thermal stress and the risk of cracks. Appropriate heat treatment is performed after welding to restore material properties and reduce stress in the heat affected zone.
(6) Welding parameter control accurately controls welding current, voltage and welding speed to ensure weld quality. Excessively high current or too fast welding speed can cause weld defects such as undercuts, pores and cracks.
(7) Heat input control controls the amount of heat input to avoid material embrittlement and sensitization caused by excessive heat-affected zones. Use multi-pass welding and low heat input processes, especially when welding thin sheets and austenitic stainless steels.
(8) Welding sequence and fixation Arrange the welding sequence reasonably and use clamps to fix the welding parts to prevent deformation. Use symmetrical welding and segmented welding methods to reduce welding stress and deformation.
(9) Protective measures During the welding process, take appropriate protective measures, such as using protective glasses, gloves and protective clothing, to prevent welding arc light and splash damage.
(10) Ventilation and smoke exhaust Ensure good ventilation in the welding area and use smoke exhaust equipment to prevent welding smoke from harming health.
(11) Post-weld treatment After welding is completed, necessary post-processing is performed, such as weld grinding, pickling and passivation, to remove oxide scale and other impurities and improve the corrosion resistance and aesthetics of the weld surface.
(12) Quality inspection After the welding is completed, the weld shall be inspected for quality, such as visual inspection, X-ray flaw detection, ultrasonic inspection, etc., to ensure that the weld is defect-free and meets quality standards.