Introduction to aluminum welding
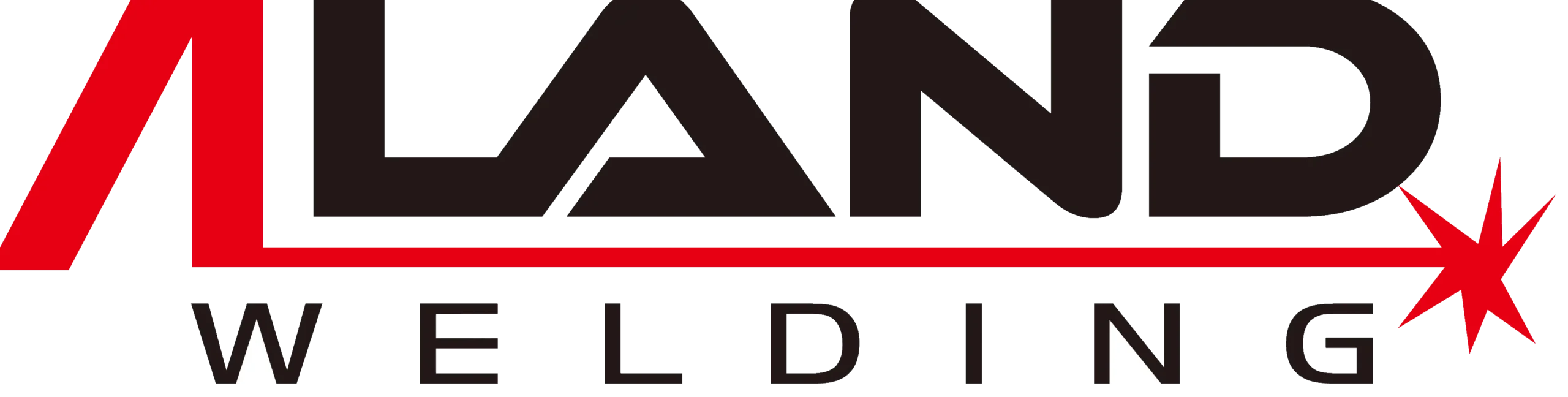
ALAND WELDING Let you feel the most sincere welding service
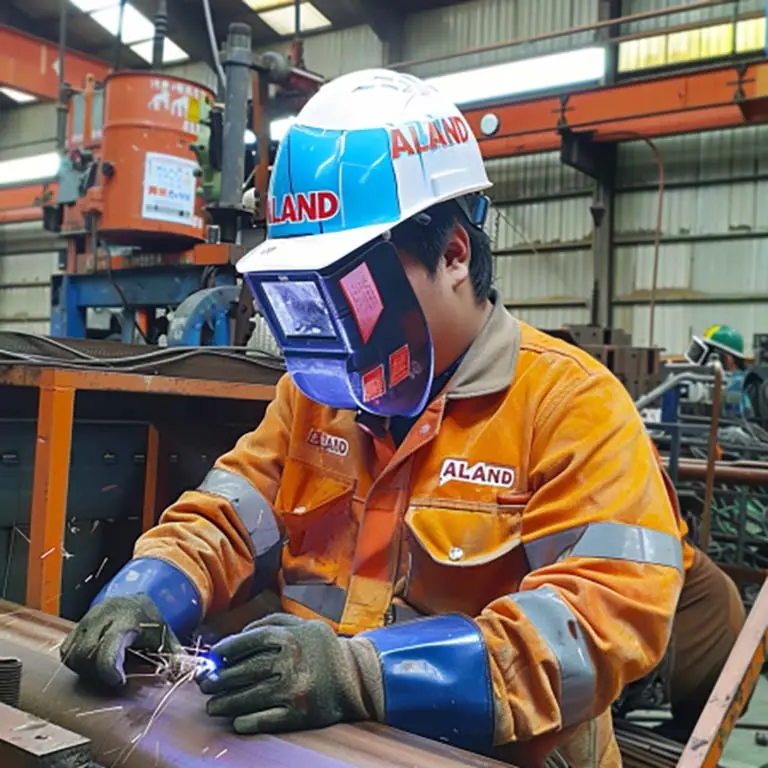
1. Concept of aluminum welding machine
Aluminum welding machines melt aluminum and aluminum alloy materials through heating or pressure to achieve a bonding effect. During the fusion process, welding wire or metal filling can be used, or two workpieces can be self-melted to fuse the molecules of the two workpieces. Process equipment that penetrates each other to form a permanent connection.
Aluminum welding machines usually have sophisticated control systems that can adjust welding parameters, such as temperature, welding speed, gas flow, etc., to meet the welding needs of aluminum materials of different thicknesses and models. They may also be equipped with automated features, such as welding robots or automatic feeding systems, to improve production efficiency and weld quality.
2. The function of aluminum welding machine
Aluminum welding actually melts aluminum and aluminum alloy materials through heating or pressure to achieve a bonding effect. During the fusion process, welding wire or metal filling can be used, or two workpieces can be self-melted to make the two workpieces fuse. Process equipment in which molecules penetrate each other to form permanent connections.
The aluminum welding machines often referred to in our daily life and industry are generally argon arc aluminum welding machines. Argon arc aluminum welding machines are divided into tungsten arc argon arc aluminum welding machines and melting electrode argon arc aluminum welding machines (MIG gas shielded welding). When using tungsten arc welding, AC arc welding must be used to weld aluminum and aluminum alloys.
3. Characteristics of aluminum welding
The aluminum welding machine uses low-voltage and high-current electric energy to instantly convert the electric energy into heat energy through the arc. It uses high-purity argon as the protective gas during welding to avoid pores and impurities during welding. At the same time, AC argon arc welding and MIG gas shielded welding are both It has a certain cathodic cleaning function and can directly remove the oxide film on aluminum and aluminum alloys. Because the aluminum welding machine is small in size, simple to operate, easy to use, has high welding efficiency, good welding seam formation, and large penetration depth, it can penetrate aluminum and aluminum alloy plates to achieve high-quality bonding effects, and the welding strength is the same as the base material and the sealing performance is the same. Well, it is widely used in various fields of industry and life.
The aluminum welding machine will produce arc light during use. The arc light contains infrared rays and ultraviolet rays, as well as harmful substances such as metal vapor and smoke. The tungsten rod in tungsten argon arc welding contains a small amount of radioactive elements, so adequate protective measures must be taken. , In addition, because argon is used as the protective gas, it is not suitable to operate in windy welding sites.
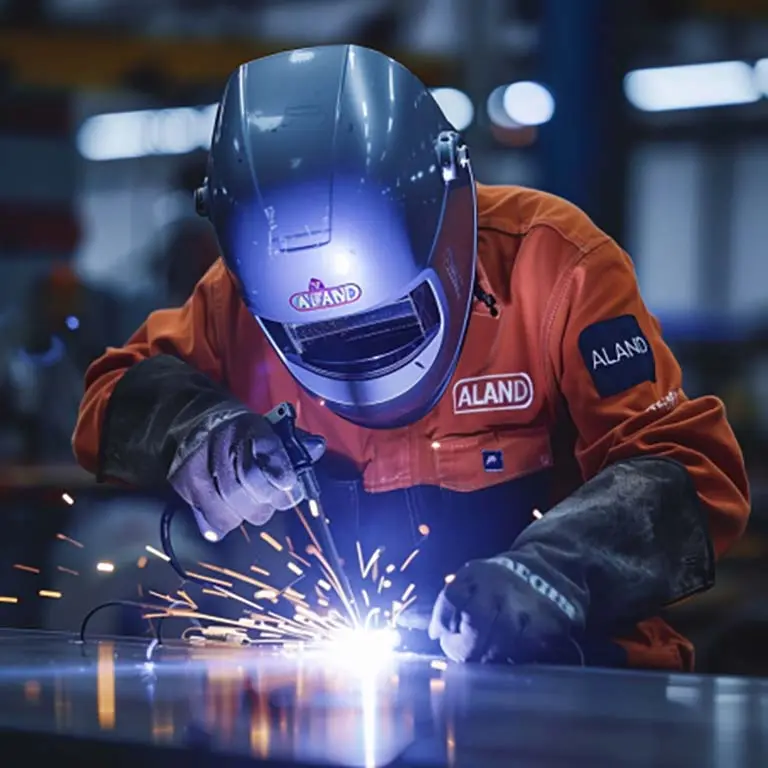
4. Development trends of aluminum welding
(1) High efficiency and energy saving
Aluminum welding has slowly shifted from traditional flame brazing to AC argon arc aluminum welding machines. The welding efficiency and level are a qualitative leap. With pulsed MIG gas shielded welding, the welding efficiency is higher than that of manual AC argon arc welding. 3 times. It will also save metal filling materials and auxiliary processes such as preheating when welding medium-thick aluminum plates, which can save 30%-50% of welding costs. It can be seen that in the future, pulse MIG gas shielded aluminum welding machines will be widely used to replace the AC argon arc aluminum welding machines that currently occupy a certain share.
(2) High quality and difficult connection effect
The pulse MIG gas shielded aluminum welding machine can meet the industrial welding requirements of medium and thick plates. There have been many domestic cases of welding to a thickness of over 60mm. However, for the welding of aluminum sheets with thickness below 0.8mm, pulse MIG welding technology is still quite lacking. Only Fronius aluminum welding machines in the world can weld it, so it is imperative to break this technical bottleneck.
(3) Digital automated welding
With the development of industrial technology, digital welding machines using microcontrollers, DSPs, FPGAs, etc. have gradually matured. Special welding machines or arc welding robots for automatic welding through point-to-point and bus structures have also been used in production, which can replace difficult tasks that cannot be completed manually. , high-intensity automatic welding operations, and digital aluminum welding machines support network remote monitoring and fault diagnosis; the automation of aluminum welding machines will also be widely promoted and applied in recent years.
5. Advantages of aluminum welding
(1) Lightweight and high strength: Aluminum is a lightweight metal but has good strength, so aluminum welded products usually have high strength and excellent weight ratio, and are suitable for applications that require weight reduction but require strength, such as Aerospace, automotive, etc.
(2) Corrosion resistance: Aluminum has good corrosion resistance, so aluminum welded products have high durability in harsh environments and can be used in corrosive places such as marine environments and chemical factories.
(3) Electrical conductivity: Aluminum is an excellent conductive material, so aluminum welding products are often used in electrical equipment, electronic products and other fields and can effectively conduct current.
(4) Plasticity: Aluminum has good plasticity and is easy to be processed into various shapes and sizes. Therefore, aluminum welded products can meet complex shapes and design requirements and are suitable for various engineering and design needs.
(5) Recyclability: Aluminum is a recyclable material, and aluminum welded products can be recycled and reused, which is beneficial to environmental protection and resource recycling.
(6) Good thermal conductivity: Aluminum has good thermal conductivity, making aluminum welded products suitable for applications requiring heat dissipation performance, such as computer radiators, automobile radiators, etc.
(7) Low cost: Aluminum materials are relatively cheap, and aluminum welding technology is mature and production costs are relatively low, so aluminum welding products usually have competitive prices.
6. Defects of aluminum welding
(1) Oxidation problem: Aluminum easily reacts with oxygen in the air to form oxides during the welding process, forming oxide scale or oxide slag, which will affect the welding quality and strength. Therefore, special welding processes and protective measures, such as inert gas protection, pretreatment, etc., are required to reduce the effects of oxidation.
(2) Low melting point: Aluminum has a lower melting point, which is about 660°C compared to many other metals, so the welding process requires controlling the heating temperature to avoid excessive melting or deformation.
(3)High thermal conductivity: Aluminum has high thermal conductivity, which causes the temperature of the welding area to quickly spread to the surrounding materials, easily causing overheating or local deformation of the welding area, requiring precise control of welding parameters and heating methods.
(4) Poor plasticity: Although aluminum has good plasticity, plasticity reduction may occur during the welding process, resulting in a reduction in the strength of the welded area, which needs to be improved through appropriate welding processes and subsequent heat treatment.
(5) Welding deformation: Aluminum materials have large linear expansion coefficients and thermal expansion coefficients, and are prone to deformation during the welding process, especially when welding large or thin-walled aluminum parts. Compensation measures or preventive measures need to be taken to Reduce welding distortion.
(6) Difficulty in welding different types of aluminum alloys: Different types of aluminum alloys have different chemical compositions and physical properties. Some aluminum alloys may be difficult to weld with other types of aluminum alloys or pure aluminum. Appropriate welding materials and processes need to be selected. Overcome this problem.
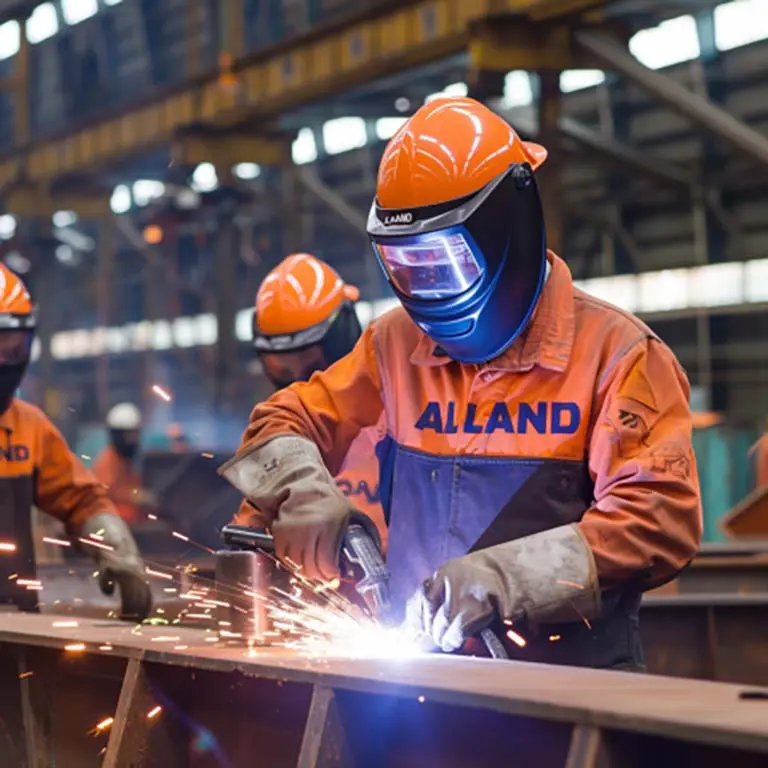
7. Application industries of aluminum welding
(1) Aerospace: The demand for lightweight materials in the aerospace field is extremely high, and aluminum and its alloys have become one of the preferred materials due to their lightweight and high-strength properties. Aluminum welding is widely used in the manufacture and repair of aircraft fuselages, engines, wings and other components.
(2) Automobile industry: Aluminum welding is also widely used in the automobile industry, especially in the manufacture of high-end cars, electric cars and energy-saving cars. Aluminum welding can be used in the manufacture of body structures, chassis components, cooling systems, and more.
(3) Electronics industry: Aluminum welding also has important applications in the electronics industry, such as the manufacturing of housings, radiators, connectors and other components for electronic products such as computers, mobile phones, and tablets.
(4) Construction engineering: Due to the light weight and corrosion resistance of aluminum, aluminum welding is often used in the manufacturing and installation of windows, doors, curtain walls, aluminum alloy plates, etc. in construction projects.
(5) Ship manufacturing: Aluminum alloy is commonly used in ship manufacturing to manufacture hulls, decks, cabins and other components. Aluminum welding technology is widely used in ship manufacturing and repair.
(6) Military industry: The military industry has high requirements for lightweight, high strength and corrosion resistance. Aluminum and its alloys play an important role in the manufacturing of military equipment. Aluminum welding is widely used in the manufacture of military aircraft, ships, and armor. Vehicles etc.
(7) Industrial Manufacturing: Aluminum welding is also used to manufacture other industrial equipment and machinery such as compressors, pumps, valves, etc.