Introduction and use of common flux core welding wires
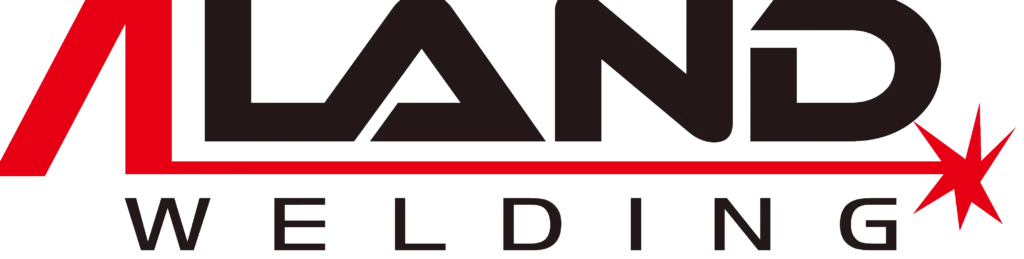
ALAND WELDING Let you feel the most sincere welding service
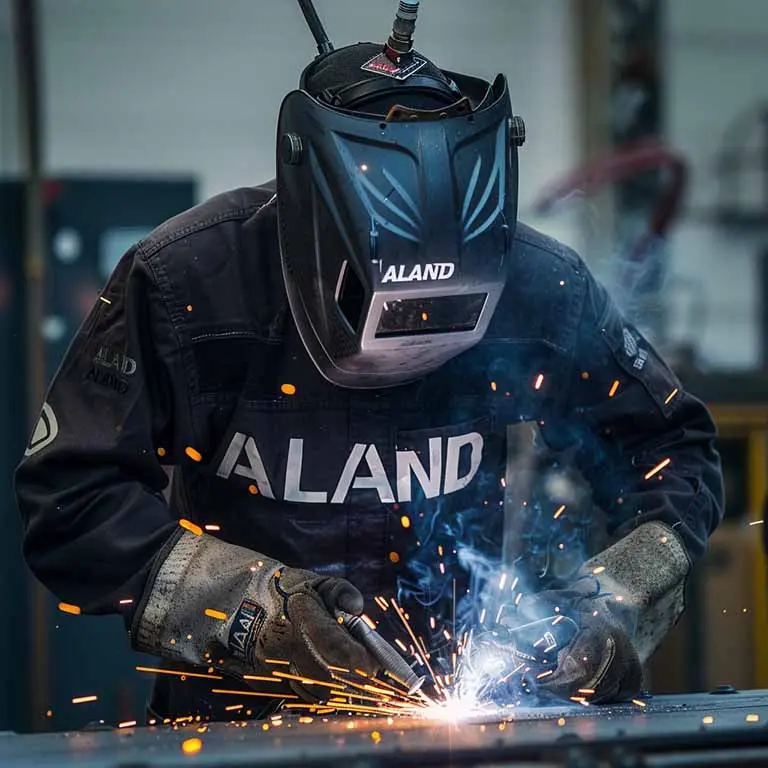
1. Concept of flux core welding wire
Flux core welding wire is a special welding material that is characterized by fillers in the middle, which may be flux, alloying elements or other chemicals. Compared with traditional solid welding wire, flux core welding wire offers greater flexibility because it can generate its own flux layer during the welding process, or generate a shielding gas through internal fillers. This feature makes flux core welding wire very popular in certain environments.
From an application perspective, there are two main types of flux core welding wire: self-shielded flux-cored welding wire and gas-shielded flux-cored welding wire.
(1) Self-shielded flux-cored welding wire produces shielding gas during welding, so no external gas supply is required, and it is suitable for outdoor and windy occasions. It forms a slag layer during the welding process, providing additional protection, although this means additional cleaning steps are required.
(2) Gas-shielded flux-cored welding wire requires additional shielding gas, usually carbon dioxide or mixed gases. This type of welding wire is more commonly used in industrial settings because it provides higher quality welding results and a wider welding current range. Gas-shielded flux-cored wire is commonly used in construction, manufacturing, and other areas where high-strength welding is required.
Advantages of flux core welding wire include higher productivity and deeper welding penetration. This wire is useful for welding thick metals or in applications requiring high welding speeds. Due to its internal filler, flux core welding wire can also add specific alloying elements during the welding process, thereby enhancing the strength and corrosion resistance of the welded joint.
2. Common categories of flux core welding wire
Flux core welding wire is a welding material whose core part contains components such as flux or alloying elements and is used to weld metals. Flux core welding wire can be divided into several main categories based on the nature and purpose of its internal filling. The design and usage environment of each category are different. The following is a detailed introduction to common categories:
(1) Self-shielded flux cored wire
Self-shielded flux-cored wire generates shielding gas through the internal filler during the welding process, eliminating the need for an external gas supply. This makes it suitable for outdoor welding and windy environments, as no gas bottles or gas lines are required. Self-shielded flux cored wire is typically used in the following situations:
Construction Sites: Since external gas protection may not be available when welding outdoors, this welding wire is popular on construction sites.
Repair and Maintenance: Because it is convenient and does not require a gas bottle, it is suitable for on-site repairs.
(2) Gas-shielded flux-cored welding wire
Gas-shielded flux-cored wire requires the use of an external shielding gas, such as a carbon dioxide or argon mixture. It is commonly used in industrial settings to provide higher weld quality and less weld spatter. Gas shielded flux-cored welding wire is suitable for:
Industrial manufacturing: On production lines, gas-shielded flux-cored wire provides high welding efficiency and quality.
Precision Welding: For welds that require high precision and quality, gas-shielded flux-cored wire is the first choice.
(3) Dual-phase flux cored wire
Duplex flux-cored wire combines the advantages of self-shielding and gas shielding. This wire works best with external gas shielding where higher weld strength and quality are required. Duplex flux cored wire is commonly used for:
Structural Welding: In building and bridge structures, duplex flux-cored wire provides additional strength and stability.
Shipbuilding: Since shipbuilding requires high-intensity welding, duplex flux-cored wire performs well in this area.
(4) Low hydrogen flux cored wire
Low-hydrogen flux-cored wire has a low hydrogen content, reducing hydrogen-induced cracking that may occur during the welding process. This wire is suitable for welding high-strength steels and other materials susceptible to the effects of hydrogen. Common applications include:
Pipe welding: Low hydrogen flux-cored wire reduces the risk of hydrogen-induced cracking and is suitable for welding pipes and pressure vessels.
High-strength steel structures: Low-hydrogen flux-cored wire is ideal where the strength and stability of the welded joint need to be ensured.
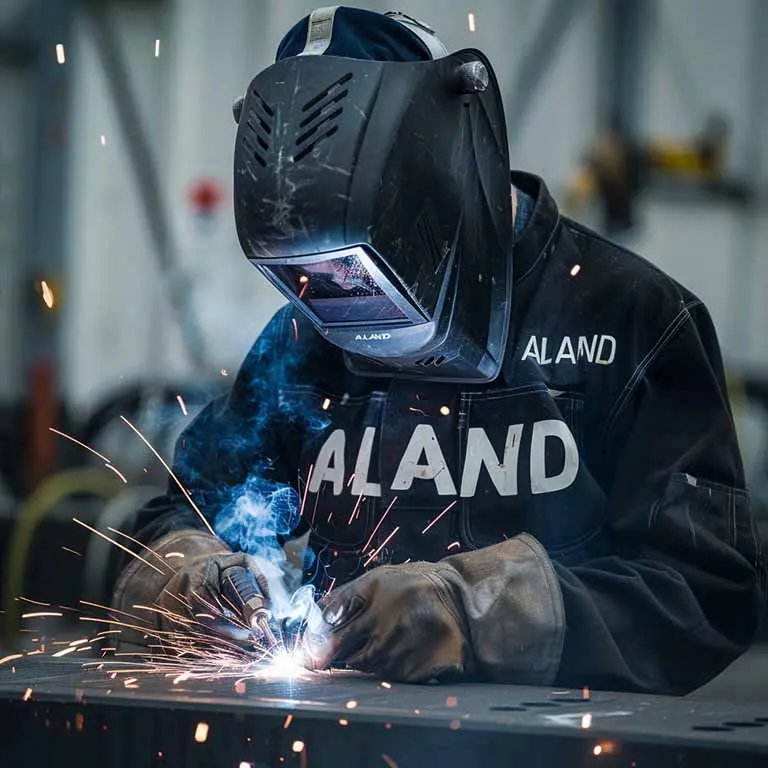
3. Advantages and disadvantages of flux core welding wire
Flux core welding wire is a welding material used for welding that is designed to contain flux or alloying elements inside the wire to provide a variety of functions. Flux core welding wire has many advantages that make it widely used in industry, construction and manufacturing, but it also has some disadvantages. The following are the advantages and disadvantages of flux core welding wire and their detailed introduction.
(1) Advantages of flux core welding wire
①High productivity
Flux core welding wire generally welds faster than solid wire, which means higher productivity. Because the internally filled flux or alloy can serve multiple functions, additional steps are eliminated and work efficiency is increased.
②Strong welding penetration
The flux core welding wire is designed to have deeper penetration during the welding process and can weld thicker metals. This makes flux core welding wire ideal for structural welding and heavy duty welding applications.
③Versatility
Flux core welding wire can have multiple functions depending on its internal filling. Self-shielded flux-cored wire does not require external gas, so it is suitable for outdoor or windy environments; gas-shielded flux-cored wire provides higher quality welding and is suitable for industrial and manufacturing fields.
④Welding quality
The welding quality of gas-shielded flux-cored wire is generally higher than that of self-shielded flux-cored wire, with less welding spatter and smoother welded joints. Therefore, it is very popular in precision welding and industrial production.
⑥Diversity
The diversity of flux core welding wire is reflected in a variety of types available, including self-shielded, gas-shielded, dual-phase and low-hydrogen flux cored wires. Each type provides flexible options for different application scenarios and welding needs.
(2) Disadvantages of flux core welding wire
①Higher cost
The cost of flux core welding wire is usually higher than that of solid welding wire, mainly because of its complex manufacturing process and the need to fill internal components. This means it may be less popular in cost-sensitive projects.
②Requires specific equipment
Flux core welding wire usually requires special welding equipment, such as welding machines and gas supply systems suitable for flux core welding wire (for gas shielded flux cored wire). This may increase equipment costs.
③Welding spatter and slag layer
Self-shielded flux-cored wires may produce high levels of welding spatter and form slag layers, which require additional cleanup. This can result in increased post-weld handling compared to solid wire.
④Complex operation
Operation of flux core welding wire can be more complicated than solid wire, especially for wires that require gas shielding. Welders need to understand how different types of flux-cored wires operate and ensure proper use of shielding gases.
⑤Welding quality fluctuations
Due to the complexity of the internal filler of flux-cored wire, welding quality may fluctuate from batch to batch and quality monitoring may be required.
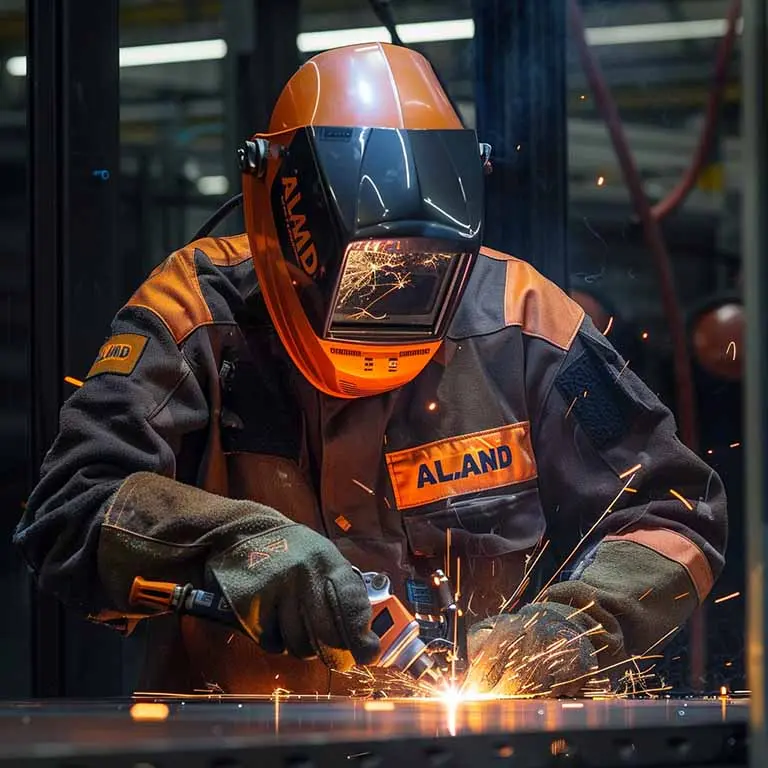
4. Applicable scenarios of flux core welding wire
Flux-cored welding wire is a special welding material used to weld metals, containing flux or alloying elements. Its unique design and performance characteristics make it popular in many welding applications. When to use flux cored wire depends on the welding environment, welding requirements and production efficiency. The following are detailed uses of flux-cored wire in specific situations:
(1) High productivity
Flux-cored wire typically welds faster than solid wire because the flux or alloying elements within it provide additional support during the welding process. This means that in industrial production lines, flux-cored wire can significantly improve production efficiency. Industries such as manufacturing and steel construction require high productivity, and flux-cored wire can help achieve this goal.
(2) Welding thick metal
Flux-cored wire has greater welding penetration, which makes it very effective when welding thick metals. Because of the high heat and penetration required for welding, flux-cored wire is the first choice for welding large steel structures, bridges, shipbuilding and other applications that require high penetration.
(3) Outdoors and windy environment
Self-shielded flux-cored wire generates shielding gas through the internal filler during the welding process and does not require an additional gas supply. Therefore, it is more suitable than gas-shielded flux-cored wire in outdoor and windy environments. For example, construction sites, repair sites, etc. often lack a stable external gas supply, and self-shielded flux-cored wire performs well in these situations.
(4) High-quality welding requirements
Gas-shielded flux-cored wire generally provides higher quality welds because the external shielding gas reduces oxidation and spatter produced during the welding process. This type of welding wire is suitable for applications requiring high-quality welding, such as automotive manufacturing, precision equipment production, etc. In these industries, the smoothness and consistency of welded joints are very important.
(5) Versatility
Flux-cored wire is available in a variety of types and configurations to meet different welding needs. Self-shielded flux-cored wire is suitable for applications that do not require external gas protection; gas-shielded flux-cored wire is used for high-quality welding; duplex flux-cored wire combines the advantages of both; and low-hydrogen flux-cored wire reduces the risk of hydrogen-induced cracking. This diversity makes flux-cored wire valuable in a variety of welding environments.
(6) High strength and structural welding
The strong welding penetration and additional flux support of flux-cored wire make it ideal for high-strength and structural welding. In areas such as bridges, construction, shipbuilding and pipeline construction, flux-cored wire provides high strength and structural integrity.
(7) Repair and maintenance
Self-shielded flux-cored wire excels in repair and maintenance applications because it requires no external gas shielding and is suitable for use in the field. In situations where on-site repair or maintenance is required, flux-cored wire conveniently provides fast and effective welding.
5. Possible safety of flux core welding wire
There are some safety hazards to be aware of when welding with flux-cored wire. These hazards are related to the welding environment, welding materials, and hazards generated during the welding process. The following is a detailed introduction to possible safety hazards when using flux-cored welding wire:
(1) Welding spatter
Flux-cored wire may produce large amounts of welding spatter during the welding process. These splashes of molten metal can cause burns and other bodily harm. Welding spatter can also cause fires or damage surrounding equipment. Therefore, you need to wear appropriate protective equipment such as fire-resistant clothing, goggles and gloves when welding, and make sure the work area is clear of flammable materials.
(2) Smoke and gas
A large amount of smoke and harmful gases are produced during flux-cored wire welding. These fumes may contain heavy metals, oxides, and other harmful substances, and long-term inhalation may have serious effects on the health of welders, including respiratory diseases and lung problems. Therefore, the welding environment needs to be well ventilated and the welder needs to wear appropriate respiratory protection.
(3) Risk of electric shock
There is a risk of electric shock during welding, especially as welding equipment using flux-cored wire often requires high voltages. The risk of electric shock is higher in humid or poorly grounded environments. To reduce the risk of electric shock, welders should ensure that their equipment is well grounded, avoid working in wet environments, and wear insulating protective gear.
(4) Fire and explosion
The high temperatures and welding spatter produced by welding can cause a fire or explosion, especially if there are flammable materials or volatile gases around. When using flux-cored wire, ensure that the work area is free of flammable materials and that fire-extinguishing equipment is available. Avoid welding in environments close to flammable gases to prevent the risk of explosion.
(5) Eye damage
The intense light and ultraviolet rays produced by welding can cause damage to the eyes, leading to photophthalmia (also known as welding eye). To prevent eye damage, welders should always wear appropriate welding goggles or face shields and avoid looking directly into the welding arc.
(6) Noise pollution
High levels of noise can be generated during welding, especially in large industrial welding environments. Long-term exposure to high-noise environments can cause hearing damage. Therefore, welders should wear hearing protection such as earplugs or earmuffs, especially in high-noise environments.
(7) Environmental pollution
The smoke and harmful substances generated by welding may cause pollution to the environment, especially when welding for a long time or in a closed environment. It should be ensured that waste and hazardous materials from the welding process are properly disposed of to avoid adverse effects on the environment.
This article summarizes the relevant knowledge of flux-cored welding wire and discusses its basic concepts, common categories, advantages and disadvantages, usage scenarios, and possible safety hazards.
First, we understand the basic concepts of flux cored wire. Flux-cored wire is a special welding material filled with flux or alloying elements to provide additional support and protection during the welding process. The unique feature of this welding wire is that it can form a protective gas or flux layer during the welding process, improving welding efficiency.
Next, we explored the common categories of flux core welding wire. There are mainly self-shielded flux-cored welding wires, gas-shielded flux-cored welding wires, dual-phase flux-cored welding wires and low-hydrogen flux-cored welding wires. Each category has its own unique features and application scenarios, such as self-shielded flux-cored wire for outdoor and windy environments, and gas-shielded flux-cored wire for high-quality welding.
Then, we analyze the advantages and disadvantages of flux-cored wire in detail. The advantages of flux core welding wire include high productivity, strong welding penetration, versatility and high-quality welding; the disadvantages include higher cost, need for specific equipment, welding spatter and complex operation.
Next, we discussed the usage scenarios of flux core welding wire. Flux cored wire is suitable for high productivity, welding of thick metals, outdoor and windy environments, quality welding, versatility, high strength and structural welding, and repair and maintenance. Its versatility and high efficiency make it popular in many welding applications.
Finally, we summarize the potential safety hazards that may exist when using flux-cored wire. These hazards include welding spatter, fumes and gases, electric shock risks, fires and explosions, eye damage, noise pollution and environmental pollution. To ensure safe welding, proper safety measures need to be taken and the welder wears the appropriate protective gear.
To summarize, flux-cored wire has an important place in the welding field, and its versatility and high productivity make it ideal for many applications. However, safety is always paramount when using flux-cored wire. Welding workers and engineers should remain vigilant and follow safe operating procedures to ensure a safe working environment. With proper usage and safety measures, flux-cored wire can be a reliable and efficient tool in the welding process.