Introduction to welding materials Welding wire
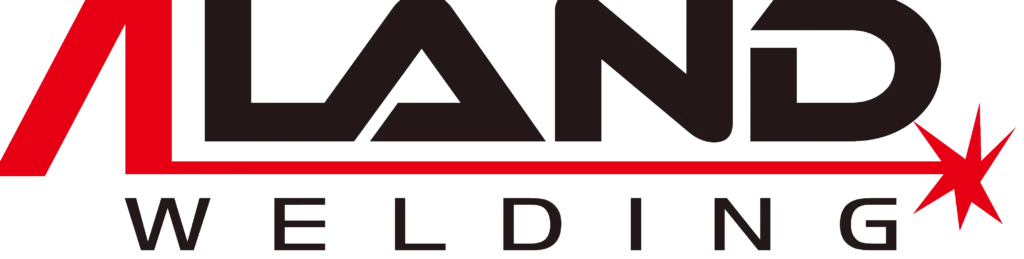
ALAND WELDING Let you feel the most sincere welding service
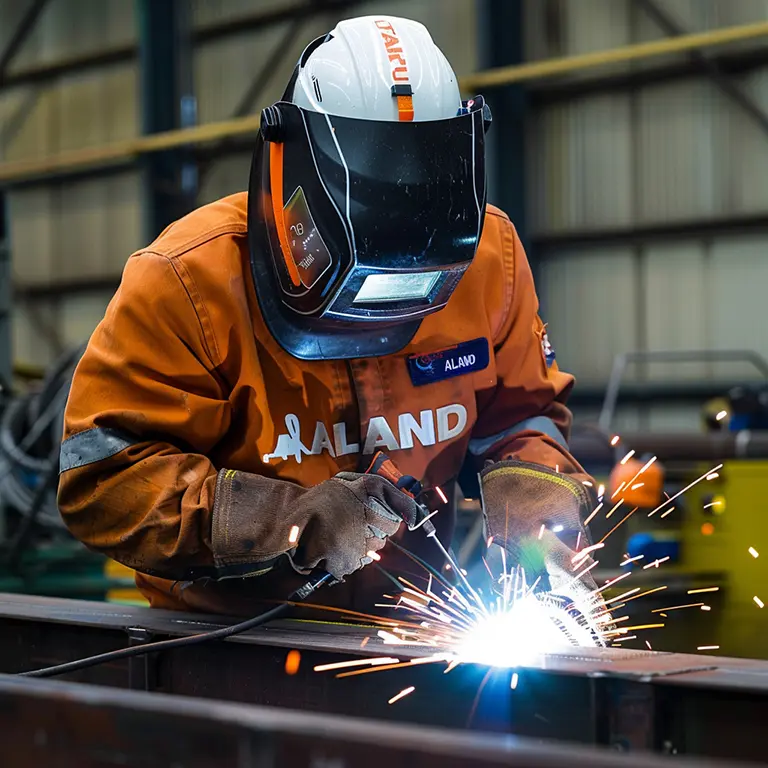
1. Introduction to Welding wire
Welding wire is a wire welding material used as a filler metal or as a conductive wire. In gas welding and gas tungsten arc welding, the Welding wire is used as a filler metal; in submerged arc welding, electroslag welding and other gas tungsten arc welding, the Welding wire is both a filler metal and a conductive electrode. The surface of the Welding wire is not coated with anti-oxidation flux.
2. Classification of Welding wires
(1) Rolling type
Most welding wires fall into this category, including carbon steel welding wires, low alloy structural steel welding wires, alloy structural steel welding wires, stainless steel welding wires and non-ferrous metal welding wires.
Common Welding wires:
①SKD11 > 0.5~3.2mm HRC 56~58 Welding and repairing cold work steel, metal stamping dies, cutting dies, cutting tools, forming dies, workpiece hard surfaces to produce argon welding rods with high hardness, wear resistance and high toughness. Before welding repair Warm and preheat, otherwise cracks may easily occur.
②63 degree cutting edge Welding wire> 0.5~3.2mm HRC 63~55, mainly used in welding broaching dies, hot working high hardness dies, hot forging master dies, hot stamping dies, screw dies, wear-resistant hard surfaces, high speed Steel, knife edge repair.
③SKD61 > 0.5~3.2mm HRC 40~43 Zinc welding, aluminum die-casting mold, with good heat resistance and crack resistance, hot gas punching mold, aluminum-copper hot forging mold, aluminum-copper die-casting mold, with good heat resistance and crack resistance Wear and crack resistance. Generally, hot-pressed casting molds often have tortoise-shell cracks. Most of them are caused by thermal stress. They are also caused by surface oxidation or corrosion of die-casting raw materials. Heat treatment is adjusted to an appropriate hardness to improve its life. It is not suitable for hardness that is too low or too high.
④70N > 0.1~4.0mm Welding wire characteristics and uses: joining of high hardness steel, zinc and aluminum die-casting mold cracking, welding reconstruction, pig iron/cast iron welding repair. It can be directly surfacing welded to various cast iron/pig iron materials, and can also be used to weld mold cracks. When using cast iron welding, try to lower the current and use short-distance arc welding. The steel is partially preheated. After welding, heating and slowly cooling.
⑤60E> 0.5~4.0mm Characteristics and uses: Specially used for welding high tensile steel, priming for hard surface production, and crack welding. High-strength welding wire, containing high nickel-chromium alloy composition, is specially used for welding and filling base to prevent cracking. It has strong pulling force and can repair cracks in steel after welding. Tensile strength: 760 N/mm² Elongation: 26%
⑥8407-H13 > 0.5~3.2mm HRC 43~46 Die-casting mold for making zinc, aluminum, tin and other non-ferrous alloys and copper alloys. It can be used as hot forging or stamping mold. It has high toughness, wear resistance and good resistance to thermal erosion. It resists high-temperature softening and has good resistance to high-temperature fatigue. It can be used for heat treatment of punches, reamers, rolling knives, grooving knives, scissors, etc. When welding, it is necessary to prevent decarburization. The hardness produced by hot tool steel after welding is too high and it is easy to break.
⑦- Anti-explosion primer Welding wire > 0.5~2.4mm HB~300 High hardness steel joint, primer for hard surface production, crack welding. High-strength welding wire, containing high nickel-chromium alloy content, is used for crack-proof bottom welding and filling bottoming. It has strong pulling force and can repair cracks in steel and weld and rebuild.
⑧718 > 0.5~3.2mm HRC 28~30 Mold steel for plastic products such as large home appliances, toys, communications, electronics, and sports equipment. Plastic injection mold, heat-resistant mold, anti-corrosion mold, good cutting and corrosion resistance, excellent surface gloss after grinding, long service life. The preheating temperature is 250~300℃ and the postheating temperature is 400~500℃. When doing multi-layer welding repairs, the retreat method is used for welding repairs, which is less likely to cause poor fusion and other defects.
⑨738 > 0.5~3.2mm HRC 32~35 Mold steel for plastic products that are translucent and require surface gloss, large molds, plastic mold steel for products with complex shapes and high precision. Plastic injection mold, heat-resistant mold, corrosion-resistant mold, good corrosion resistance, excellent processing performance, easy cutting, polishing and electric corrosion, good toughness and wear resistance. The preheating temperature is 250~300℃ and the postheating temperature is 400~500℃. When doing multi-layer welding repairs, the retreat method is used for welding repairs, which is less likely to cause poor fusion and other defects.
⑩P20Ni > 0.5~3.2mm HRC 30~34 Plastic injection mold, heat-resistant mold (cast copper mold). Designed with alloy components with low sensitivity to welding cracking, containing about 1% nickel, suitable for PA, POM, PS, PE, PP, ABS plastics, with good polishability, no pores or cracks after welding, and good polishing properties Smooth finish, after vacuum degassing and forging, pre-hardened to HRC 33 degrees, the cross-section hardness distribution is uniform, and the mold life is more than 300,000 years. The preheating temperature is 250~300℃ and the postheating temperature is 400~500℃. When doing multi-layer welding repairs, the retreat method is used for welding repairs, which is less likely to cause poor fusion and other defects.
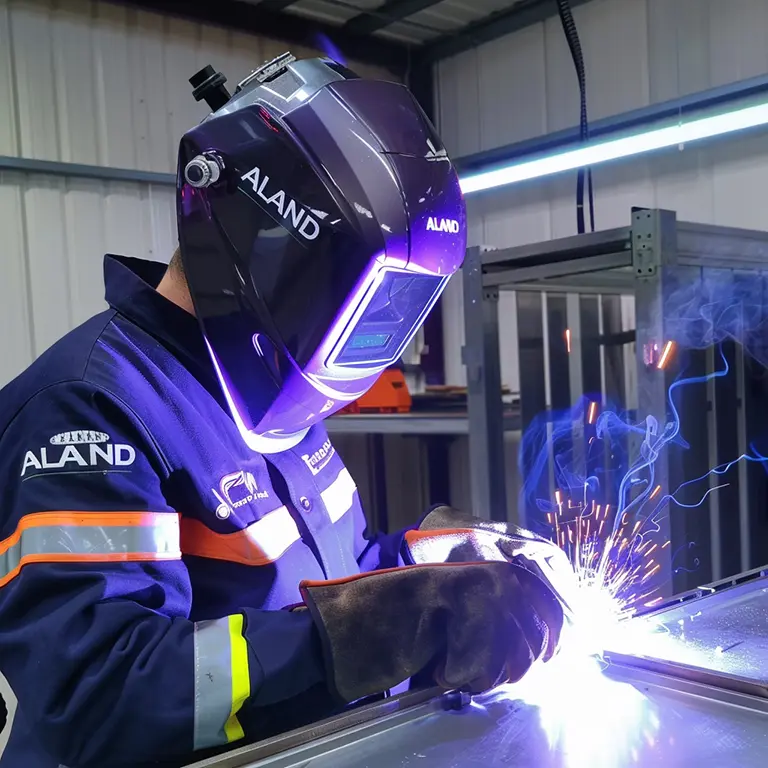
⑪NAK80 > 0.5~3.2mm HRC 38~42 Plastic injection mold, mirror steel. High hardness, excellent mirror effect, good electrical discharge machinability, and excellent welding performance. After grinding, it is as smooth as a mirror. It is the most advanced and best plastic mold steel in the world. It has easy cutting elements and is easy to process. It has high strength, toughness and durability. It has non-deformation properties and is suitable for mold steel of various transparent plastic products. The preheating temperature is 300~400℃ and the postheating temperature is 450~550℃. When doing multi-layer welding repairs, the retreat method is used for welding repairs, which is less likely to cause poor fusion and other defects.
⑫S136 > 0.5~1.6mm HB~400 Plastic injection mold, corrosion resistance and good permeability. High purity, high mirror finish, good polishability, excellent rust and acid resistance, less heat treatment deformation, suitable for PVC, PP, EP, PC, PMMA plastics, corrosion-resistant and easy-to-process modules and fixtures, super mirror corrosion resistance Precision molds, such as rubber molds, camera parts, lenses, watch cases, etc.
⑬ Ace steel > 0.5~2.4mm HB200 iron mold, shoe mold, mild steel welding, easy to engrave and corrode, repair of S45C, S55C steel, etc. The texture is fine, soft, easy to process, and will not produce pores. The preheating temperature is 200~250℃ and the postheating temperature is 350~450℃.
⑭BeCu (beryllium copper) > 0.5~2.4mm HB300 is a copper alloy mold material with high thermal conductivity. The main added element is beryllium. It is suitable for inner inserts, mold cores, die-casting punches, hot runner cooling systems, and thermal conductivity of plastic injection molding molds. Mouth, overall cavity of blow mold, wear plate, etc. Tungsten copper materials are used in resistance welding, EDM, electronic packaging and precision mechanical equipment.
⑮CU (argon welding copper) > 0.5~2.4mm HB200 This welding rod has a wide range of uses and can be used to repair electrolytic sheets, copper alloys, steel, bronze, pig iron, and general copper parts. It has good mechanical properties and can be used for welding repair of copper alloys, and can also be used to join welding steel with pig iron and iron.
⑯Oil steel Welding wire > 0.5~3.2mm HRC 52~57 Blanking dies, gauges, drawing dies, perforation punches, can be widely used in hardware cold stamping, hand decoration embossing dies, etc., general purpose special tool steel, wear-resistant, Oil cooler.
⑰Cr steel welding wire > 0.5~3.2mm HRC 55~57 Blanking die, cold forming die, cold drawing die, punch, high hardness, high toughness, good wire cutting performance. Warm up and preheat before welding repair. Please do post-heating after welding repair.
⑱MA-1G > 1.6~2.4mm, super mirror welding wire, mainly used in military products or products with extremely high requirements. Hardness HRC 48~50 maraging steel system, aluminum die casting mold, low pressure casting mold, forging mold, blanking mold, injection mold surfacing welding. Special hardened high-toughness alloy, very suitable for aluminum gravity die-casting molds and gates, extending the service life by 2 to 3 times, and can produce very precise molds and super mirror surfaces (gate repair welding, less prone to thermal fatigue cracks during use).
⑲ High-speed steel welding wire (SKH9) > 1.2~1.6mm HRC 61~63 High-speed steel, the durability is 1.5~3 times that of ordinary high-speed steel. It is suitable for manufacturing and processing difficult-to-process materials such as high-temperature alloys, stainless steel, titanium alloys, and high-strength steels. Tools, welding repair broaches, hot work high hardness tools, molds, hot forging master molds, hot punching dies, screw dies, wear-resistant hard surfaces, high-speed steel, punching tools, cutting tools, electronic parts, thread rolling dies, threads Plates, drilling rollers, rolling dies, compressor blades and various mold mechanical parts, etc… After strict quality control at European industrial standards, the material has high carbon content and excellent ingredients, with uniform internal structure, stable hardness, wear resistance, toughness, high temperature resistance, etc… The properties are better than those of other materials of the same grade.
⑳Nitrided parts welding repair wire > 0.8~2.4mm HB~300 Suitable for surface repair of molds and parts after nitriding.
(2) Casting
Some alloys, such as cobalt-chromium-tungsten alloy, cannot be forged, rolled or drawn, but are made by casting methods. It is mainly used for manual surfacing of workpiece surfaces to meet special performance requirements such as oxidation resistance, wear resistance and corrosion resistance at high temperatures. Continuous pouring and liquid extrusion can be used to produce cobalt-chromium-tungsten welding wires up to several meters long, which can be used for automatic wire-filling gas tungsten arc welding to improve welding efficiency and surfacing layer quality, while also improving labor conditions. Cast iron wire is sometimes used for repair welding of cast iron.
(3) Medicine cores
Roll a thin steel strip into a round or special-shaped steel pipe, fill it with a certain amount of powder, and draw it into a seam welding flux wire, or fill the steel pipe with powder and draw it into a seamless welding flux wire (see picture). This kind of welding wire has high welding and deposition efficiency, good adaptability to steel materials, and short trial production period, so its usage and scope of use are constantly expanding. This kind of Welding wire is mainly used for carbon dioxide gas shielded welding, submerged arc welding and electroslag welding. The composition of the powder in welding flux wire is generally similar to that of the welding rod coating. Welding flux wire containing slag-making, gas-making and arc-stabilizing components does not require protective gas during welding. It is called self-protected welding flux wire and is suitable for the construction of large-scale welding structure projects.
Gas-protected welding flux wires were developed and marketed as early as the early 1950s, but it was not widely used commercially until 1957. This method can be said to be a combination of the advantages of submerged arc welding and CO2 welding (referring to solid). The flux is wrapped in the Welding wire and protected by the surrounding CO2 gas, which can produce a softer and more stable arc and low temperature during welding. Splash is its characteristic. At the beginning of development, only large diameter welding wire (2.0-4.0mm) was available, which was used for flat and horizontal welding of major workpieces. It was not until the development of small diameter welding wire in 1972 that the fields of use of welding flux wire were greatly expanded.
Self-protected welding flux wire was developed shortly after the gas-protected welding flux wire was launched on the market, and it was quickly recognized by the industry for specific purposes.
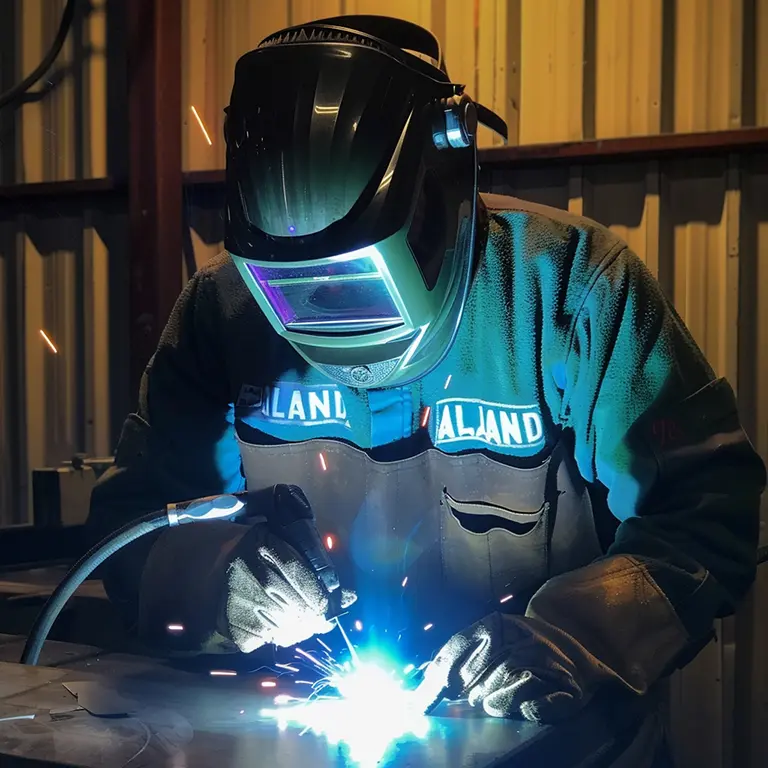
3. Advantages and disadvantages of Welding wire
advantage:
(1) Precise control of additives:
Welding wire additives can be precisely controlled to adjust the chemical composition and properties of the molten metal during the welding process. This allows the quality of the welded joint to be adjusted precisely as needed to meet specific engineering requirements.
Precise control of additives can also improve the performance of welded joints, such as increasing strength, ductility, corrosion resistance, etc.
(2) High efficiency:
Welding wire has high welding speed and production efficiency in the automated welding process. Compared with manual welding, Welding wire can achieve continuous supply, thereby reducing welding pause time and improving production efficiency.
Efficient welding speed and production efficiency can reduce production costs and increase factory productivity.
(3) High-quality welds:
Because the additives of the welding wire can be precisely controlled, the welds produced during the welding process are usually of higher quality. This includes aspects such as weld uniformity, sealing and corrosion resistance.
Quality welds improve the performance and reliability of your workpiece, extending its service life and reducing maintenance costs.
(4) Easy to operate:
Welding wire is relatively simple to use and is suitable for both manual and automated welding processes. The continuous supply of welding wire and the smaller arc length make the welding operation more stable and easy to master.
Operators can quickly master welding technology through simple training, thereby reducing labor costs and training costs.
shortcoming:
(1) Higher cost:
Compared with other welding materials, such as welding rods, the cost of welding wire is higher. This can increase welding costs, especially in mass production or cost-sensitive applications.
The high cost may limit the scope of welding wire use, especially if budget is limited and lower cost welding materials may be chosen.
(2) Affected by the external environment:
Welding wire is more susceptible to external environmental factors during the welding process, such as wind, moisture and pollutants. This may result in a decrease in weld quality, requiring additional measures to be taken to protect the weld area.
The influence of the external environment may cause welding defects, such as pores, oxidation and impurities, thereby reducing the quality and reliability of welded joints.
(3) External protective gas is required:
Some types of welding wire require an external shielding gas, such as argon or carbon dioxide, to prevent oxidation and contamination during the welding process. This increases the complexity and cost of the welding equipment and requires additional gas supply and management.
The need for external shielding gas increases the investment and operating costs of welding equipment, especially for automated welding systems, which may increase their complexity and cost.
(4) Restricted materials and processes:
Certain types of welding wire may not be suitable for specific types of materials or special welding process conditions. For example, some wires may not perform well for welding thicker workpieces or in high-temperature environments, which may limit their use in certain applications.
Material and process limitations may cause instability and unreliability in the welding process, thereby affecting the quality and performance of the welded joint.
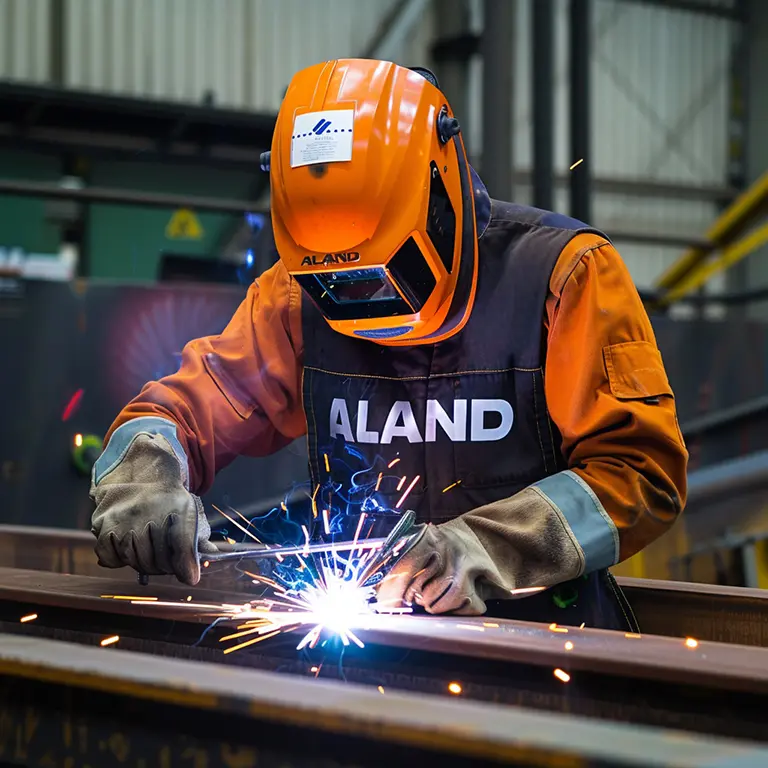
4. Selection of Welding wire
(1) Welding material type and thickness:
Understand the specific type of material being welded, including its chemical composition and physical properties. Different types of welding wire are suitable for different types of materials, such as carbon steel, stainless steel, aluminum alloy, etc. Also, consider the thickness of the material being welded, as some welding wires may be better suited for welding thicker materials, while others are better suited for welding thinner materials.
(2) Welding position and process requirements:
Understand the location and process requirements of welding operations, such as horizontal, vertical, transverse or welding in restricted spaces, etc. Different welding positions and process requirements may require different types of welding wire. For example, welding in a vertical position may require a wire with higher filling performance.
(3) Welding process:
Choose the appropriate welding process, such as gas shielded welding (MIG/MAG), flux-cored welding (FCAW), manual arc welding (SMAW), etc. Understand the characteristics and scope of application of each welding process, as well as their respective requirements for welding wires, so as to choose the most suitable welding wire type.
(4) Welding performance requirements:
Determine the performance requirements of welded joints, such as strength, sealing, corrosion resistance, etc. The type of welding wire is selected based on specific performance requirements. For example, when high strength and good corrosion resistance of the welded joint are required, stainless steel or special alloy welding wire may be selected.
(5) External environmental conditions:
Consider the conditions of the welding environment, such as wind speed, humidity, temperature, etc. Understand the characteristics of the welding environment and choose welding wire with good windproof or moisture-proof properties to ensure welding quality and efficiency.
(6) Cost considerations:
Consider performance requirements and cost factors. Choose the most appropriate wire type based on budget constraints and performance requirements. Sometimes, although a certain type of welding wire is more expensive, it may provide better welding performance and longer life, thus saving money in the long run.
(7) Quality certification:
Make sure the selected Welding wire meets relevant quality standards and certification requirements to ensure the stability of the welding process and the quality of the welded joints
(8) Supplier support:
Work with a reliable welding materials supplier for professional advice and support. Suppliers can often provide guidance on wire selection, use, and storage to help you make the best choice.
5. Storage of Welding wire
(1) The warehouse where Welding wire is stored should have a dry and ventilated environment to avoid moisture; liquids such as water, acid, and alkali should not be easily volatile.
Corrosive substances are present, and it is not suitable to coexist with these substances in the same warehouse.
(2) The Welding wire should be placed on a wooden pallet and cannot be placed directly on the floor or close to the wall.
(3) When accessing and handling the welding wire, be careful not to break the packaging, especially the inner packaging “heat shrink film”.
(4) Open the welding wire package and use it up as soon as possible (within a week). Once the welding wire is directly exposed to the air, its anti-rust time will be greatly shortened (especially in humid and corrosive media environments)
(5) Distribute welding wire according to the “first in, first out” principle to minimize product inventory time.
(6) Please store the welding wires according to their categories and specifications to prevent misuse.
Articles you may be interested in:
Different Welding Power Sources
Introduction To Welding Pad Process
Common Weld Aluminum Introduction
How To Choose Industrial Water Chiller
Introduction To Common Brazing Welding
Introduction To Common Pressure Welding
Introduction To Common Pipeline Welding
The Important Role Of Welding Positioners
Introduction To 1G To 6G Welding Positions
Underwater Welding Salary And Death Rate
Introduction To Common Welding Processes