The Most Complete Welding Defects And Solutions, A Must-read for Welders!(1)
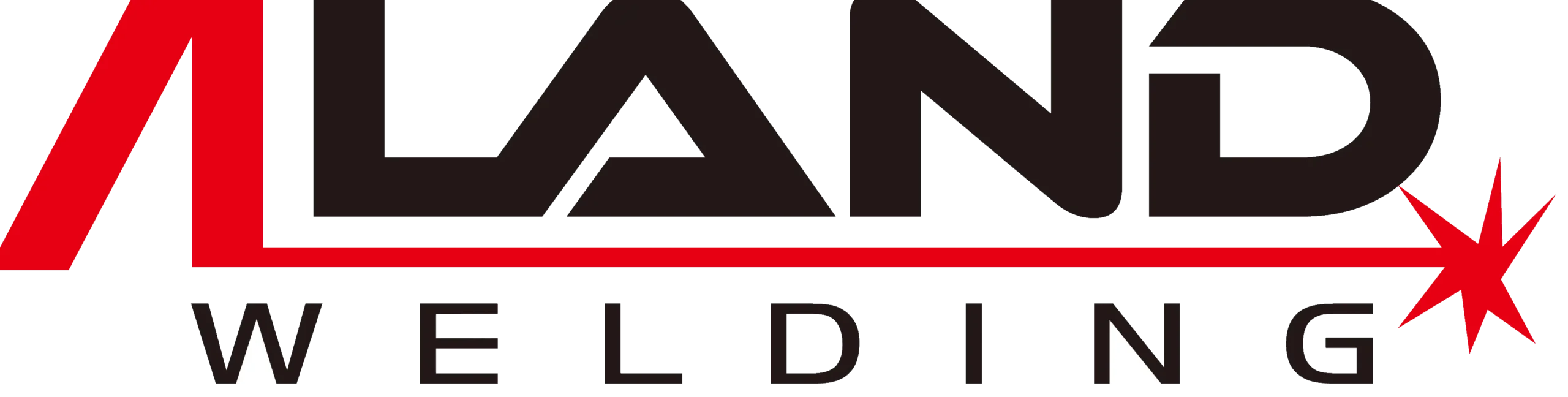
ALAND WELDING Let you feel the most sincere welding service
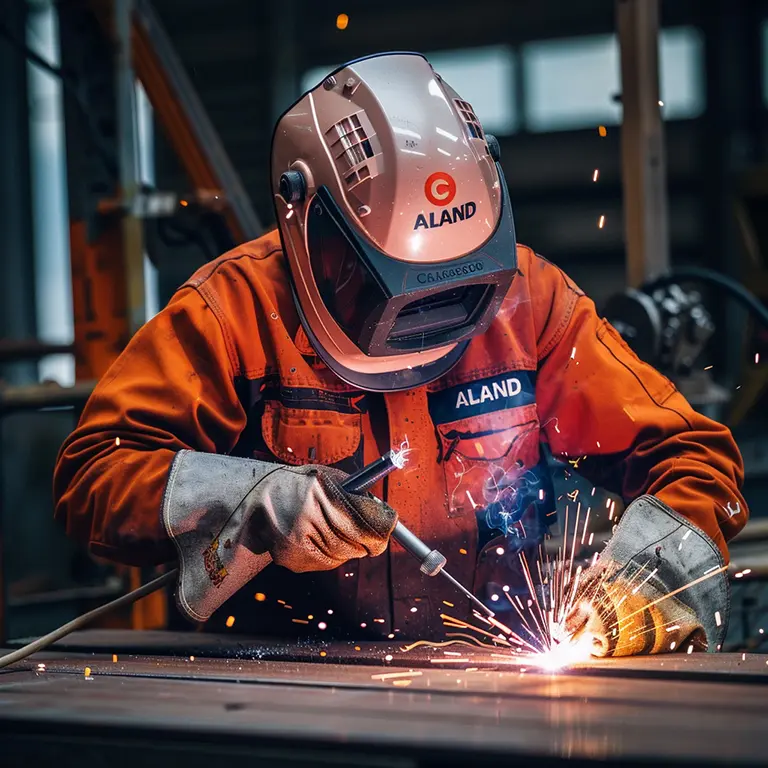
External Defects
1、Poor weld formation
(1)Phenomenon
The weld seam exhibits rough corrugation, uneven and irregular features. The transition between the weld seam and the base metal is not smooth, resulting in a poor welding joint and uneven weld seam.
(2)Cause Analysis
The reasons for poor welding seam formation include: improper groove angle of the weldment or uneven assembly gap; inadequate cleaning of the welding joint; welding current that is either too large or too small; transporting the rod (gun) during welding at either too fast or too slow speed; excessive or insufficient swing amplitude of the welding rod (gun); and improper selection of the welding angle of the welding rod (gun), etc. welding defects.
(3)Prevention
1.The groove angle and assembly clearance of the weldment must comply with the requirements of the drawing design or the implemented standards.
2.The groove of the weldment shall be polished and cleaned, free of rust, scale, grease and other dirt and impurities, and the metallic luster shall be exposed.
3. Strengthen welding contact, improve welding operation level, and become familiar with the welding construction environment.
4.According to different welding positions, welding methods, different gap gaps, etc., and in accordance with the welding process card and operating skill requirements, select reasonable welding current parameters, welding speed and angle of the welding rod (gun).
(4)Governance measures
1. Strengthen post-weld self-inspection and special inspection, and deal with problems in a timely manner if problems are found;
2. For welds with poor weld shape, perform grinding and repair welding;
3. Welds that fail to meet the acceptance standards and are poorly formed will be cut or replaced and re-welded;
4. Strengthen the study of welding acceptance standards and strictly follow the standards for construction.
2、Weld reinforcement is unqualified
(1)Phenomenon
The pipe weld and the plate butt weld exceed 3mm in reinforcement; negative reinforcement occurs locally; there is a significant difference in reinforcement due to the excessive difference in reinforcement; the height of the fillet weld is insufficient, or the size of the fillet is too large.
(2)Cause Analysis
Improperly selecting the welding current; having uneven speed of the rod (gun), either too fast or too slow; experiencing uneven swing amplitude of the welding rod (gun); and improperly selecting the welding angle of the welding rod (gun), etc. welding defects.
(3)Prevention
1. Select reasonable welding current parameters according to different welding positions and welding methods;
2. Enhance the welder’s sense of responsibility, the welding speed should be suitable for the selected welding current, and the speed of transporting the rod (gun) should be uniform to avoid sudden changes in speed and speed;
3.The swing amplitude of the welding rod (gun) is inconsistent, and the swing speed is reasonable and uniform;
4. Pay attention to maintaining the correct angle of the welding rod (gun).
(4)Governance measures
1. Strengthen the training of welders’ operating skills and improve the level of weld seam coverage;
2. Carry out necessary grinding and repair welding on the welds;
3. Strengthen post-weld inspections and deal with problems in a timely manner;
4. In the technician’s explanation, the welding angle requirements are explained in detail.
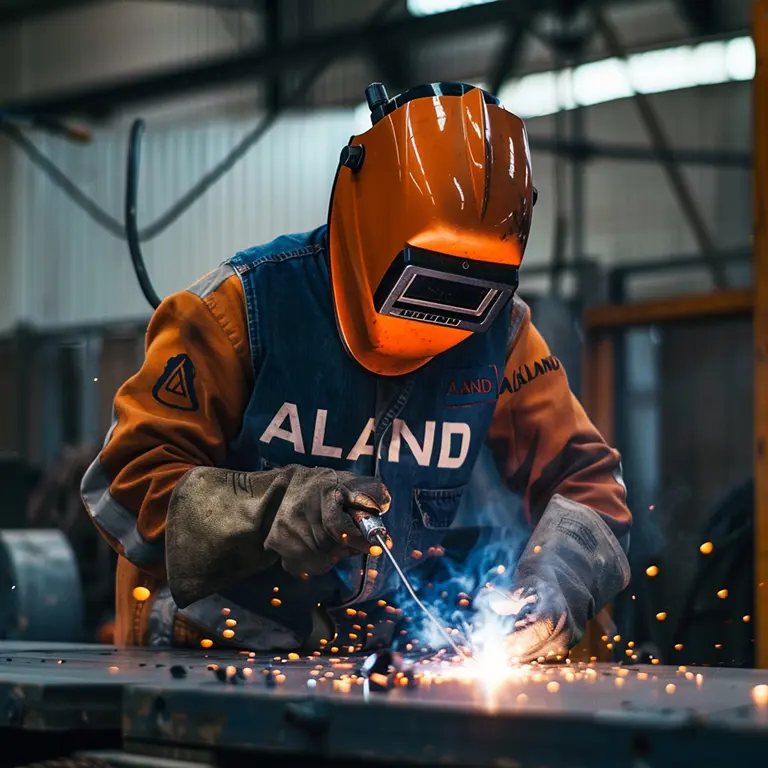
3、Weld seam width difference is unqualified
(1)Phenomenon
The edge of the weld is uneven, and there is a difference in width greater than 3mm.
(2)Cause Analysis
The swing range of the welding rod (gun) is inconsistent, too large in some places, and too small in other places; the angle of the welding rod (gun) is inappropriate; the welding position is difficult, hindering the welding personnel’s vision. welding defects.
(3)Prevention
1. Strengthen welders’ sense of responsibility and improve their concentration during welding;
2. Adopt the correct welding rod (gun) angle;
3. Be familiar with on-site welding positions and formulate necessary welding construction measures in advance.
(4)Governance measures
1. Strengthen practice, improve the welder’s operating technical level, and improve the ability to overcome welding in difficult positions;
2. Improve welders’ quality awareness and pay attention to the appearance quality of welds;
3. After the weld cover is completed, conduct timely inspections, repair unqualified welds, and perform repair welding if necessary.
4、Undercut
(1)Phenomenon
The weld does not fuse well with the wood, resulting in the appearance of grooves with a depth greater than 0.5 mm. The total length of these grooves exceeds 10% of the weld length or the length required by the acceptance standard.
(2)Cause Analysis
The welding line energy is high, the arc is too long, the angle of the welding rod (gun) is inappropriate, the feeding speed of the welding rod (wire) is inappropriate, etc. are all causes of undercutting. welding defects.
(3)Prevention
1. Select appropriate current parameters according to the welding project, location, and welding specification requirements;
2. Control the arc length and try to use short arc welding;
3. Master the necessary methods and techniques for transporting articles (guns);
4. The feeding speed of the welding rod (wire) is coordinated with the selected welding current parameters;
5. Pay attention to the angle of the welding rod (gun) when the edge of the weld seam melts and combines with the base metal.
(4)Governance measures
1. Grind, clean and repair the weld undercut found during the inspection to make it meet the acceptance standards;
2. Strengthen the learning of quality standards and improve the quality awareness of welders;
3. Strengthen practice and improve operational skills in preventing undercut defects.
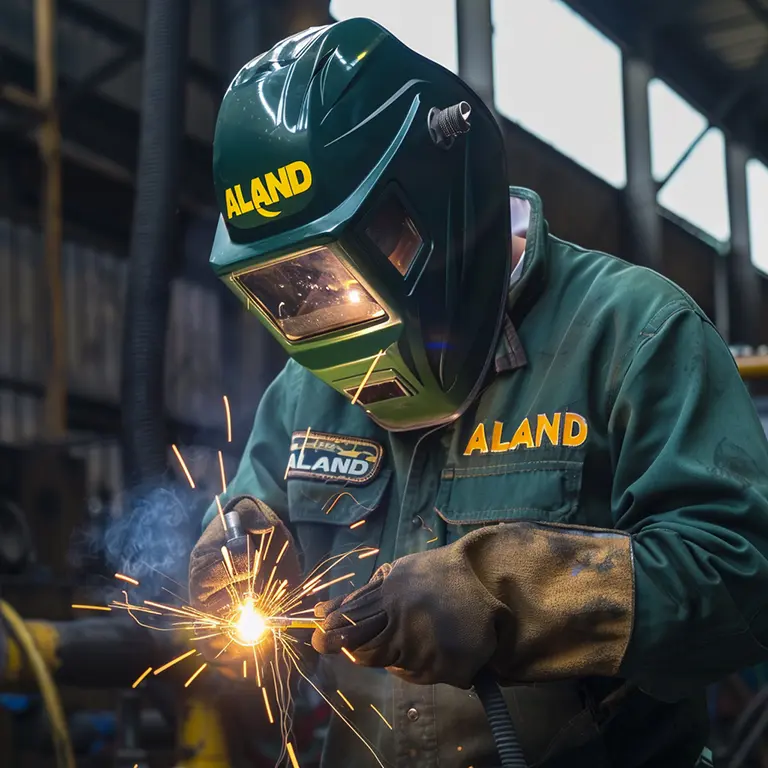
5、Wrong word
(1)Phenomenon
The manifestation is that the outer wall base metal on both sides of the weld is not on the same plane, and the misalignment exceeds 10% of the base metal thickness or exceeds 4mm.
(2)Cause Analysis
The joint of the weldment does not meet the requirements, and the welder fixes and welds when the joint is inappropriate. welding defects.
(3)Prevention
1. Strengthen the training and responsibility of installers;
2. Use necessary measuring tools during the matching process;
3. For weldments that do not meet the requirements, welders are not allowed to spot and weld.
(4)Governance measures
1. Strengthen the learning of standards and installation skills, and improve the technical level of installers;
2. For welded joints that have misaligned joints and do not meet the acceptance standards, they should be cut off, re-aligned and welded.
6、Bend
(1)Phenomenon
Due to the lateral shrinkage of the weld or the deviation of the installation counterpart, the base metal on both sides perpendicular to the weld does not align in the same plane, forming a certain angle.
(2)Cause Analysis
1. The installation port is inappropriate and forms a certain angle;
2. The deposited metal in the weld shrinks laterally during the solidification process;
3. The welding process is asymmetrical.
(3)Prevention
1. Ensure the quality of installation counterparts;
2. For large asymmetric welds, reserve anti-deformation allowance;
3. Symmetrical point fixing and symmetrical welding;
4. Adopt a reasonable welding sequence.
(4)Governance measures
1. Take flame correction measures for weldments that can use flame correction;
2. For asymmetric welds, reasonably calculate and take measures such as reserving anti-deformation allowance;
3. Adopt a reasonable welding sequence, minimize the lateral shrinkage of the weld, and adopt symmetrical welding measures;
4. For welded joints that are bent beyond the standard, remedial measures cannot be taken, such as cutting them off and re-welding them.
7、Crater
(1)Phenomenon
During the welding arc closing process, surface depressions are formed, often accompanied by defects such as shrinkage cavities and cracks.
(2)Cause Analysis
During welding arc closing, if the molten pool is not full, the arc is closed and the welding is stopped. The welder underestimates the arc closing situation and the arc stopping time is inaccurate. welding defects.
(3)Prevention
1. Extend the arc closing time;
2. Adopt the correct arc closing method.
(4)Governance measures
1. Strengthen the practice of welder operating skills and master various welding operation methods of arc closing, arc stopping and joints;
2. Strengthen welders’ sense of responsibility;
3. Grind, clean and repair the arc craters that have formed.
8、Surface pores
(1)Phenomenon
During the welding process, the gas in the molten pool does not completely overflow from the molten pool (part of it overflows), but the molten pool solidifies, forming holes on the surface of the weld.
(2)Cause Analysis
1. During the welding process, due to loose wind protection measures, gas was mixed into the molten pool;
2. The welding materials have not been baked or the baking does not meet the requirements, the welding wire is not cleaned cleanly, and the gas generated by itself enters the molten pool during the welding process;
3. The molten pool temperature is low and the solidification time is short;
4. The weldment is not cleaned cleanly, and impurities generate gas and enter the molten pool when welding at high temperatures;
5. The arc is too long, the flow of protective gas is too large or too small during argon arc welding, and the protection effect is not good, etc.
(3)Prevention
1. The base metal and welding wire should be cleaned as required.
2. The welding rod is baked as required.
3. Strict wind protection measures, no drafts, etc.
4. Choose appropriate welding line energy parameters, the welding speed should not be too fast, the arc should not be too long, and the operating essentials such as arc starting, rod movement, and arc stopping should be correctly mastered.
5. During argon arc welding, the flow rate of the protective gas flow is appropriate and the purity of the argon gas meets the requirements.
(4)Governance measures
1. Grinding and cleaning of welding materials and base metal shall be carried out strictly in accordance with regulations;
2. Strengthen welder training to improve operation level and experience;
3. For welds with surface pores, mechanically grind to remove defects and perform repair welding if necessary.
9、Surface slag inclusion
(1)Phenomenon
During the welding process, coating slag inclusions seen externally mainly appear between layers.
(2)Cause Analysis
1. When multi-layer and multi-pass welding, the coating between layers is not clean;
2. The welding line energy is small and the welding speed is fast;
3. Improper welding operation techniques;
4. The surface of the previous layer of weld is uneven or the surface of the weldment does not meet the requirements.
(3)Prevention
1. Strengthen the surface grinding of the weldment. During multi-layer and multi-pass welding, the coating between layers must be cleaned before sub-layer welding can be carried out;
2. Choose reasonable welding current and welding speed;
3. Strengthen welder training and improve welding operation level.
(4)Governance measures
1. Carry out welding in strict accordance with the requirements of the regulations and work instructions;
2. Grind and remove welds with slag inclusions on the surface, and perform repair welding if necessary.
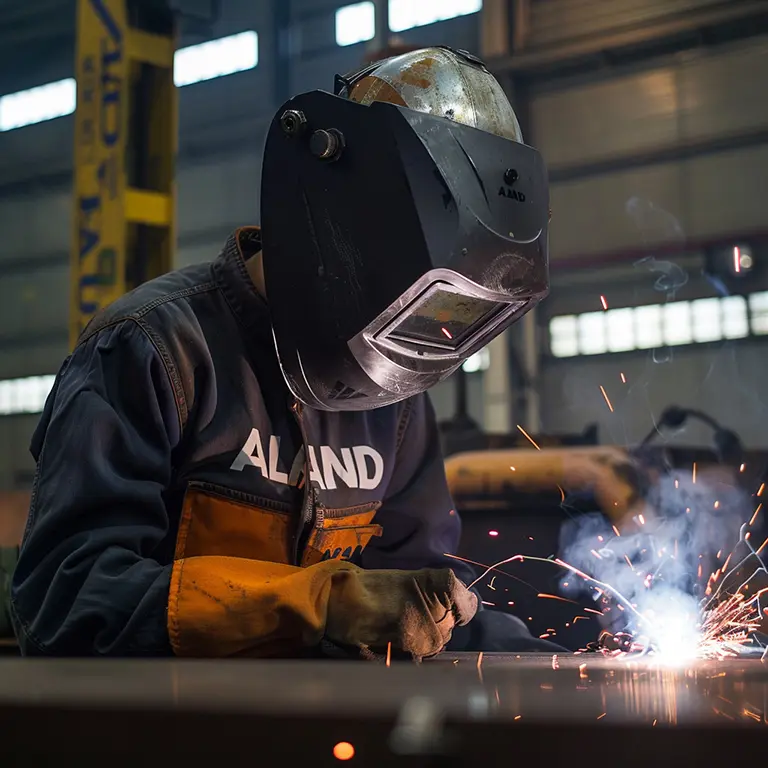
10、Surface cracks
(1)Phenomenon
Surface cracking defects that occur in the weld seam, fusion line, and heat affected zone of the welded joint.
(2)Cause Analysis
The causes of surface cracks are different due to different steel types, welding methods, welding environments, preheating requirements, impurity content in welded joints, assembly and welding stress, etc. However, the root cause of surface cracks is the internal inducement of cracks. There are two points about the necessary stress.
(3)Prevention
1. Prepare various welding conditions in strict accordance with the requirements of the regulations and work instructions;
2. Improve welding operation skills and master the welding methods used;
3. Take measures such as reasonable welding sequence to reduce welding stress.
(4)Governance measures
1. Take corresponding countermeasures for each specific cause of cracks;
2. Take excavation and repair measures for welded joints that have cracked.
11、The surface of the weld is not cleaned or not cleaned properly, and the arc scratches the weldment.
(1)Phenomenon
After completing the welding, someone does not clean the coating and spatter on the surface of the welded joint, or the cleaning is not done properly, resulting in the presence of coating or spatter. If someone does not take care during the welding process, the arc can scratch the pipe wall and other weldments, causing arc scars.
(2)Cause Analysis
1. Welders have a weak sense of responsibility and poor quality awareness;
2. The welding tools are not fully prepared or defective.
(3)Prevention
1. Check the tools and equipment before welding to make sure they are fully prepared and normal;
2. Strengthen technical communication, enhance welders’ sense of responsibility, and improve quality awareness.
(4)Governance measures
1. Develop preventive measures and strictly implement them;
2. Intensify on-site supervision and inspection, strictly enforce the acceptance system, and deal with problems found in a timely manner.
12、The welding seam of T-shaped welded joints such as supports and hangers does not include corners.
(1)Phenomenon
T-shaped welding joints are not fillet welded.
(2)Cause Analysis
1. The technical staff’s explanation is unclear or has not been disclosed;
2. Welding workers have insufficient experience or poor quality awareness, and do not know enough about its hazards.
(3)Prevention
1. Conduct technical briefing before welding construction to clarify the welding quality;
2. Welders perform welding in strict accordance with quality standards.
(4)Governance measures
1. Strengthen technical communication, improve welders’ quality awareness and understand the hazards;
2. Strengthen process supervision and welding acceptance, and deal with problems in a timely manner if problems are found.
13、Welding deformation
(1)Phenomenon
Welding deformation manifests itself in various forms such as warping, angular deformation, bending deformation, and wave deformation due to different weldments.
(2)Cause Analysis
Reasons for welding deformation include: unreasonable assembly sequence, strong alignment, small shrinkage freedom of the welding group, unreasonable welding sequence, etc. welding defects.
(3)Prevention
⑴ Develop strict welding process measures before welding, and determine the assembly sequence, welding sequence, welding direction, welding method, welding specifications, welding line energy, etc.;
⑵Conduct technical briefing before welding, and the welder shall strictly follow the measures;
⑶Use the anti-deformation method appropriately.
(4)Governance measures
⑴Construct in strict accordance with the measures;
⑵ Welding technicians guide welding on site;
⑶ Take necessary measures promptly when problems are discovered.