Why choose TIG welding? 4 major benefits
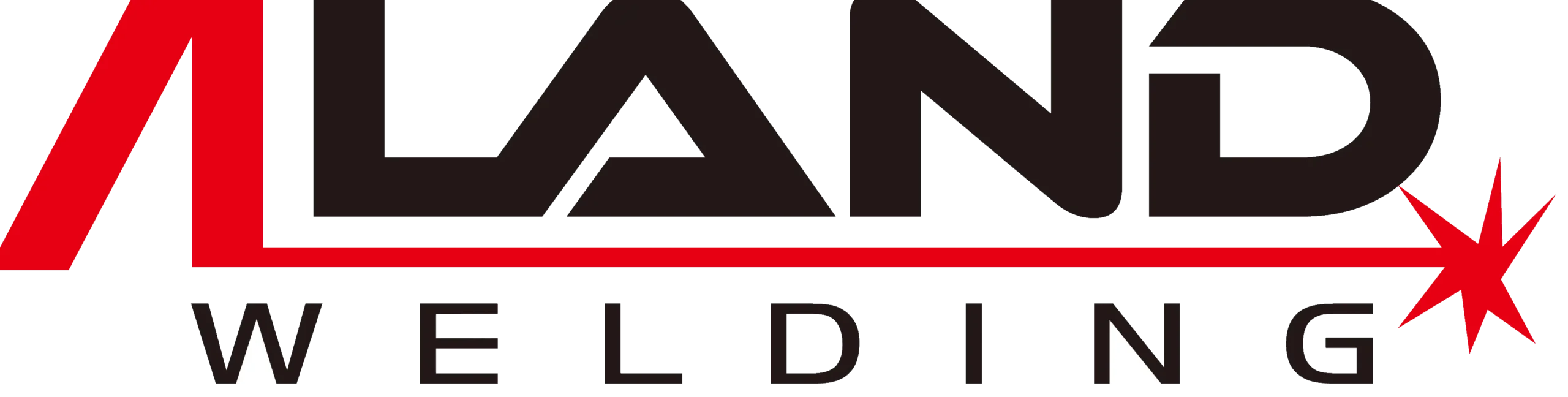
ALAND WELDING Let you feel the most sincere welding service
Tungsten inert gas welding is one of the two most common welding processes. This popular technology utilizes non-consumable tungsten electrodes to produce precise welds on various types of metals. Some of the shielding gases used in the TIG welding process are helium, argon, or a combination thereof.
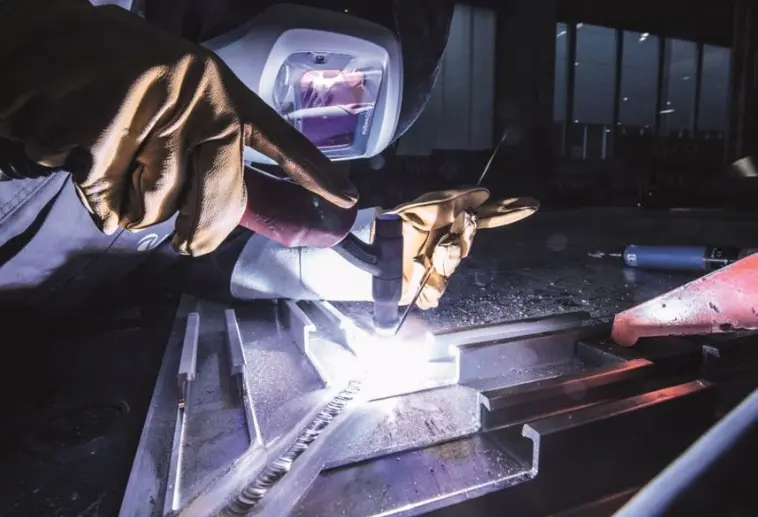
Many manufacturing processes and industries use TIG welding to produce their desired results. The process is most commonly used to weld together copper and brass alloys, magnesium, stainless steel and aluminum.
There are several reasons why TIG welding is the process of choice for many people. Let’s take a look at some of the advantages of this versatile process:
Versatility
Tungsten inert gas welding offers the benefit of versatility across a variety of industries. Because it can be used with a wide variety of base metals and metal alloys, this procedure can be used in many industrial applications.
TIG welding is used to repair or add value to components and machine parts in the automotive, aerospace, arts and crafts, construction, packaging and manufacturing industries.
Accurate
The low-amp welding guns used in TIG welding allow for greater precision, which sets it apart from other welding techniques. While high amperage amounts are suitable for large, thick metal rods, thin metal pieces require the precision that TIG welding can provide.
With TIG welding, you can handle critical joints and extremely precise welding projects. The ability to control welding variables such as heat provides accurate results.
Use a protective gas
This cost-effective advantage allows you to use one gas (usually argon) for the entire welding process. The tungsten inert gas welding process is capable of welding a variety of metal thicknesses and handling a variety of applications, all with the purchase of just one gas.
Control
TIG welding leaves a clean surface because the method leaves no slag behind once completed. The final product is clean and free of any mess, so no cleanup is required after the task is complete.
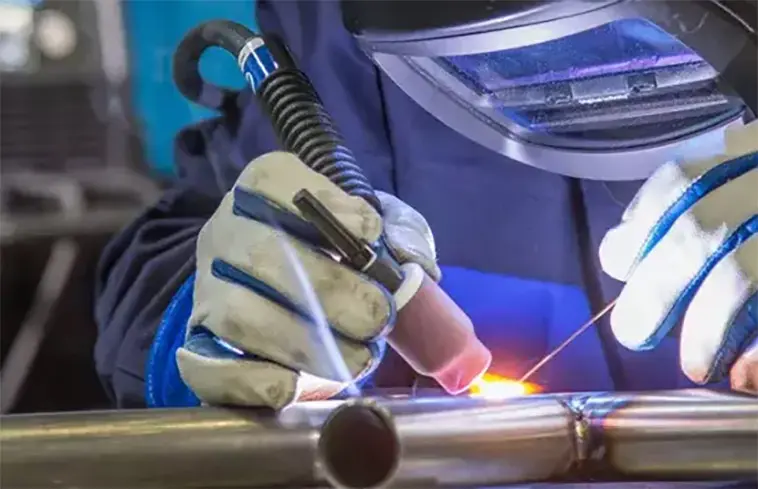
Advantages of TIG welding
(1)Argon can effectively isolate the surrounding air; it is insoluble in metal and does not react with metal; during the tungsten argon arc welding process, the arc also has the function of automatically removing the oxide film on the surface of the workpiece. Therefore, non-ferrous metals, stainless steel and various alloys that are easily oxidized, nitrided and chemically active can be successfully welded.
(2)The tungsten arc is stable and can still burn stably even under very small welding current (<10A). It is especially suitable for welding thin plates and ultra-thin plate materials.
(3)The heat source and filler wire can be controlled separately, so the heat input is easy to adjust and welding can be performed in various positions. It is also an ideal method to achieve single-sided welding and double-sided forming.
Disadvantages of TIG welding
(1)The melting depth is shallow, the deposition speed is small, and the productivity is low.
(2)The ability of the tungsten electrode to carry current is poor. Excessive current will cause the tungsten electrode to melt and evaporate, and its particles may enter the molten pool and cause slag contamination (tungsten inclusion).
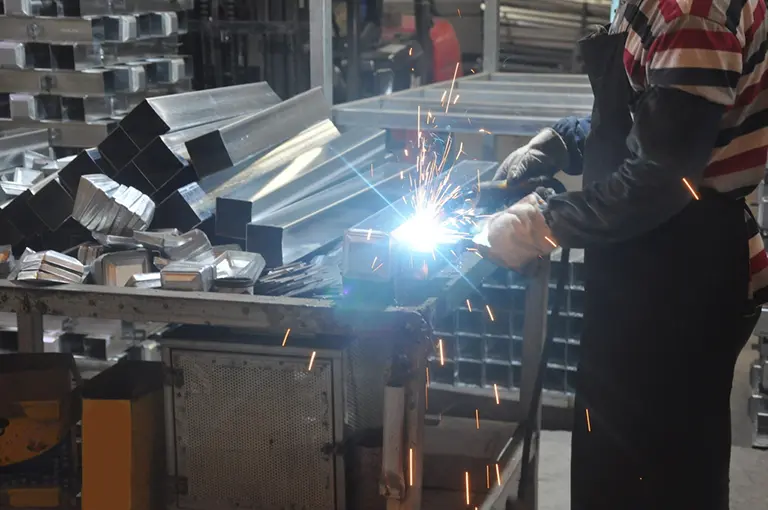
Not only does tungsten inert gas welding leave a clean surface, it also gives you considerable control over the heat and current. Thin, controllable welding machines allow you to produce high-quality welding materials that follow all curves and designs in the base metal.
Articles you may be interested in:
What is a plasma cutting machine
The difference between TIG VS MIG?
Why choose TIG welding? 4 major benefits
10 Common Types of Welding And Various Welding Principles?
The Most Complete Welding Defects And Solutions, A Must-read for Welders!(1)
The Most Complete Welding Defects And Solutions, A Must-read for Welders!(2)