What basic knowledge do beginners need to master
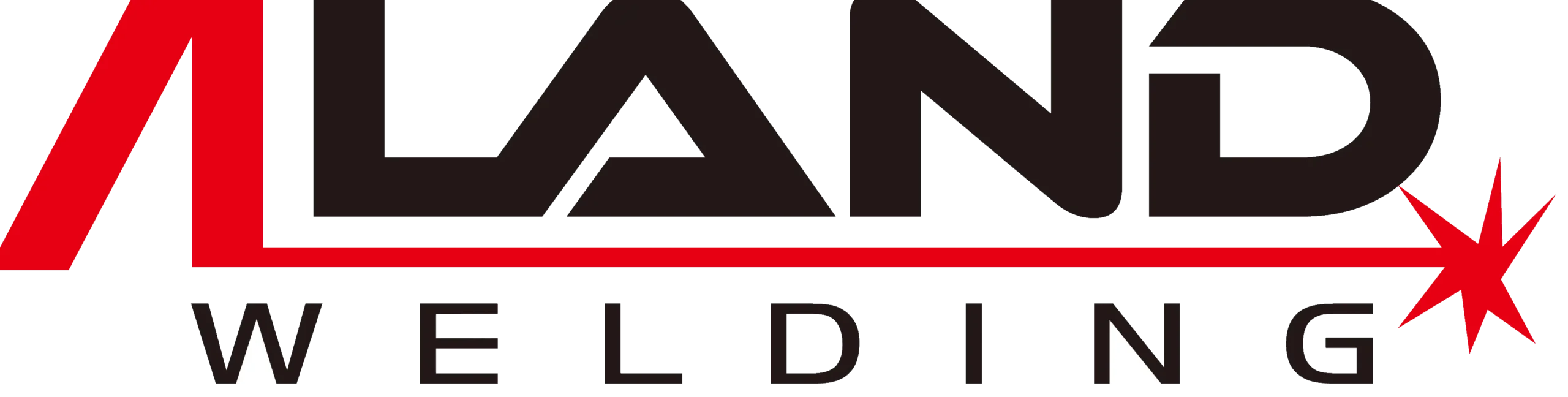
ALAND WELDING Let you feel the most sincere welding service

First
1. Metal mechanical properties include strength, plasticity, hard seat, toughness, fatigue strength, etc.
2. Hardness indicators can be divided into three types: Brinell hardness, Rockwell hardness, and Vickers hardness.
3. The ability of metal materials to conduct heat is called thermal conductivity.
4. The physical properties of metal include density, melting point, thermal expansion, thermal conductivity, electrical conductivity, etc.
5. Heat-resistant steel is steel that exhibits certain thermal stability and thermal strength at high temperatures.
6.Stainless steel is a material that resists corrosion by the atmosphere, acid, alkali, salt, etc., and is resistant to stains and rust.
7. The ability of metal materials to conduct current is called conductivity, and its measurement index is resistivity.
8. The temperature at which a metal changes from solid to liquid is called the melting point.
9. Weld symbols generally consist of basic symbols and guide lines. If necessary, auxiliary symbols, supplementary symbols and weld size symbols can also be added.
10. According to different heating and cooling methods, heat treatment can be divided into annealing, quenching, normalizing and tempering, etc.
Second
11. Any current whose direction and magnitude do not change with time is called direct current, and vice versa is called alternating current.
12. The step-like cracks formed along the steel plate rolling layer in the welded component are called lamellar tearing caused by welding.
13. When other conditions remain unchanged, when the welding speed increases, the pores tend to increase; when the welding current increases, the pores tend to increase; when the arc voltage increases, the pores tend to increase.
14. Manual arc welding is suitable for welding various materials such as carbon steel, low alloy steel, heat-resistant steel, low-temperature steel and stainless steel.
15. Manual arc welding can be used in various positions such as flat, vertical, horizontal, and upward, so it is widely used.
16. Compared with gas welding and submerged arc welding, manual arc welding has a finer metallographic structure and better joint performance in small heat-affected zones.
17. Welding process parameters refer to various physical quantities selected to ensure welding quality during welding.
18. Manual arc welding mainly selects welding rods based on the performance of the base material, the rigidity of the joint and the working conditions. When welding general carbon steel and low alloy steel, the strength level of the welding rods is mainly selected based on the principle of equal strength.
19. There are many factors to consider when selecting welding current for manual arc welding, but the main factors are the diameter of the electrode; the welding position; the weld bead level;
20.The basic forms of grooves commonly used in manual arc welding include I-shape; V-shape; double V-shape; double Y-shape; double U-shape groove with bell edge.
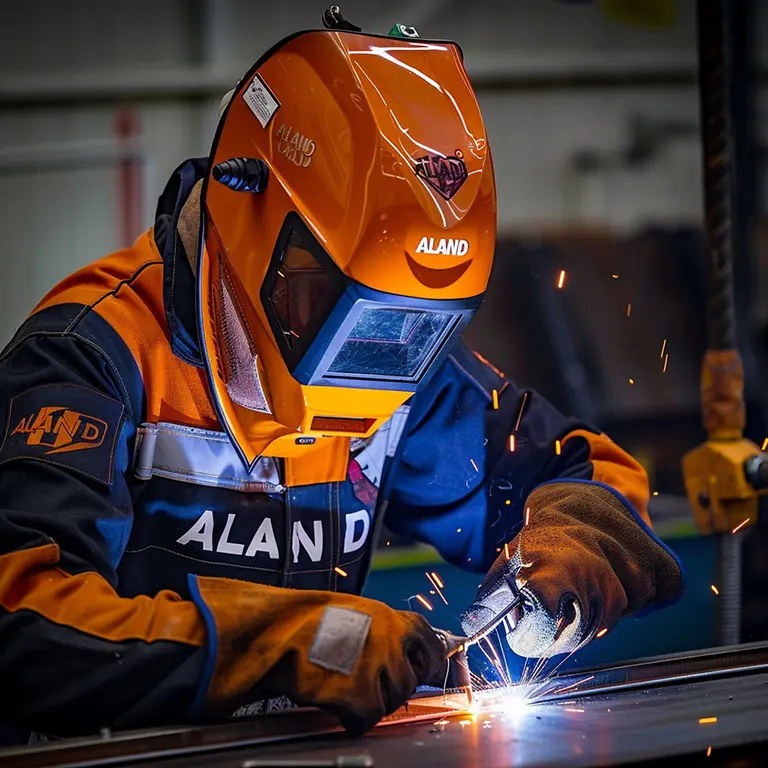
Third
21. Welding cracks are characterized by sharp notches and large aspect ratios. Moreover, these cracks exhibit distinctive features that can be identified during inspection.
22. The purpose of preheating is to reduce the cooling rate and improve the stress condition.
23. The slag of alkaline welding rod has strong desulfurization and dephosphorization capabilities.
24. Heating or insulating all (or part of) the weldment immediately after welding is called post-heating. It can effectively facilitate the escape of hydrogen in the welded joint, making it an important measure to prevent delayed cracks.
25. During welding, the molten pool fails to allow bubbles to escape during solidification, forming the remaining cavities called pores.
26.The molten slag remaining in the weld after welding, is called slag inclusion.
27.The coating layer that presses on the surface of the solder core is called coating.
28.The length of the welding rod depends on factors such as the diameter of the welding core, material, coating type, etc.
29. Steel for welding core can be divided into three categories: carbon structural steel, alloy structural steel, and stainless steel.
30. According to different uses, welding rods can be divided into carbon steel welding rods; low alloy steel welding rods; stainless steel welding rods; cladding welding rods; cast iron welding rods; nickel and nickel alloy welding rods; copper and copper alloy welding rods; aluminum and aluminum alloy welding rods; special purpose welding rods;
Fourth
31. A joint where the end faces of two weldments are relatively parallel is called a butt joint.
32. Butt joints without grooves are used for weldments of thinner steel plates, while butt joints with grooves are used for weldments of thicker steel plates that require full penetration.
33. An acetylene generator is a device that uses the interaction of voltage and water to produce acetylene.
34. The pressure reducing valve functions to reduce the pressure of the high-pressure gas stored in the cylinder to the required stable working pressure.
35. Welding is a processing method that uses heating, pressure, or both, with or without filler materials, to achieve atomic bonding of welded parts.
36. The angle between the vertical surface of the weldment and the groove surface is called the groove surface angle.
37. The junction between the weld surface and the base metal is called the weld toe.
38. When welding non-ferrous metals, cast iron, stainless steel, and other materials, one must usually use gas welding flux.
39.The fusible plug located on the shoulder of the bottle achieves the safety of acetylene bottles.
40. The ignition methods of welding arc include contact moment circuit ignition method and high-frequency and high-voltage arc ignition method.
Fifth
41. For manual arc welding, acidic electrodes are used for general structures, and alkaline electrodes are used for important structures.
42. The metal safety film in the cylinder valve achieves the safety of oxygen cylinders.
43. The metal cutting process includes three stages: preheating – burning – slag blowing.
44. In heat treatment production, the commonly used cooling methods are isothermal cooling and continuous cooling.
45. The necessary conditions for the generation and maintenance of arc are cathode electron emission and gas ionization.
46. The main sources of sulfur in welds are the base metal, welding wire, coating, or flux, etc. Therefore, the key measure to reduce the sulfur content in welds is to strictly control the sulfur content in welding raw materials.
47. The energy input from the welding energy to the weld per unit length during welding is called line energy.
48. The primary crystallization of the molten pool includes two processes: the generation of crystal nuclei and the growth of crystal nuclei.
49. Post-weld heat treatment methods include post-heating; high-temperature tempering; normalizing or normalizing plus tempering, etc.
50. There are two types of cracks produced when welding gray cast iron: thermal stress cracks and thermal cracks, among which thermal stress cracks are more common.
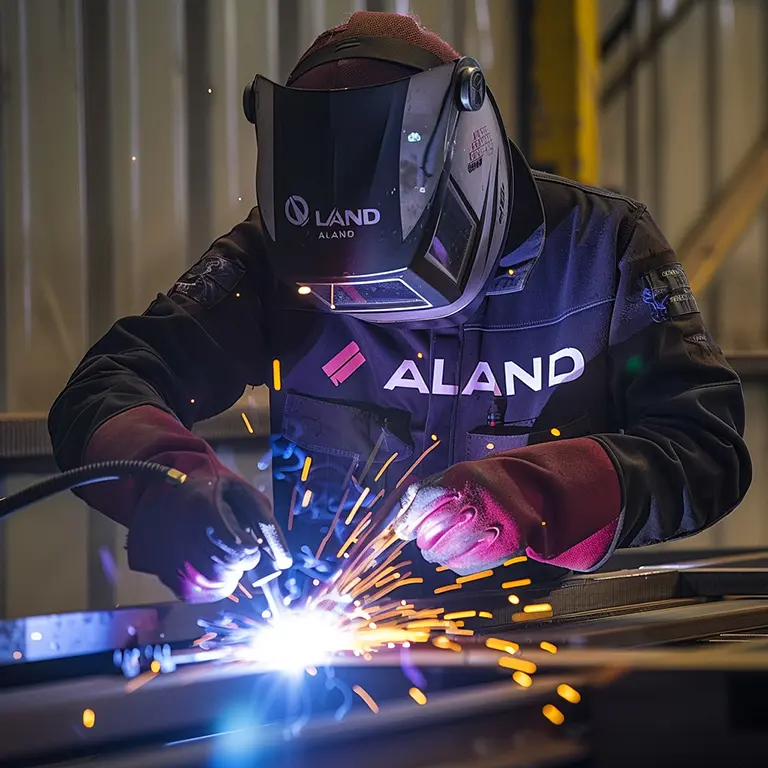
Sixth
51. The stress and deformation of the weldment in the direction perpendicular to the weld are called transverse stress and deformation.
52. For structures with asymmetric welds, the side with fewer welds should be welded first, followed by the side with more welds, which can reduce the overall deformation.
53. In order to offset the welding deformation, the weldment is artificially deformed in the opposite direction to the welding deformation before welding. This method is called the anti-deformation method.
54. The heat dissipation method is not suitable for materials with high hardenability for welding.
55. The flame correction method uses the plastic deformation produced by local heating of the flame to compress the longer metal after cooling, achieving the purpose of correcting the deformation.
56. The key to flame heating correction is to grasp the deformation caused by the local heating of the flame to determine the correct heating position. At the same time, one should control the temperature and the number of repeated heatings.
57. Flame heating methods include point heating; linear heating; and triangular heating.
58. Triangular heating is often used to correct bending deformation of thicker and more rigid components.
59. Preheating before welding can reduce the temperature difference and slow down the cooling rate, thereby reducing welding stress.
60.When using acetylene bottles, they should be used upright. If acetylene bottles are placed horizontally and used directly, they must stand for 20 minutes before use.
Seventh
61. During use, it is imperative not to allow grease to contaminate the pressure reducer.
62.Before use, it is advisable to check the injection and absorption performance of the welding torch.
63. When welding stainless steel composite plates, you should use three different welding rods of good quality to weld the same weld.
64. When connecting cast iron and low carbon steel joints using carbon steel electrodes, you can overlay a 4-5mm isolation layer on the cast iron groove first, and then assemble and spot weld after cooling.
Articles you may be interested in:
What is a plasma cutting machine
The difference between TIG VS MIG?
Why choose TIG welding? 4 major benefits
10 Common Types of Welding And Various Welding Principles?
The Most Complete Welding Defects And Solutions, A Must-read for Welders!(1)
The Most Complete Welding Defects And Solutions, A Must-read for Welders!(2)