Basic introduction to common fluxes
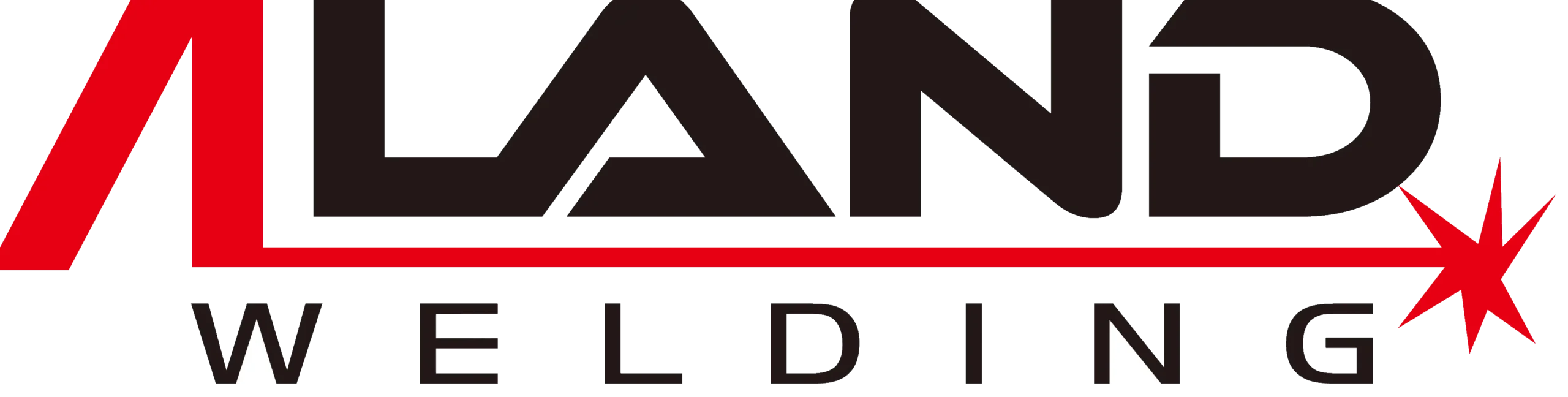
ALAND WELDING Let you feel the most sincere welding service
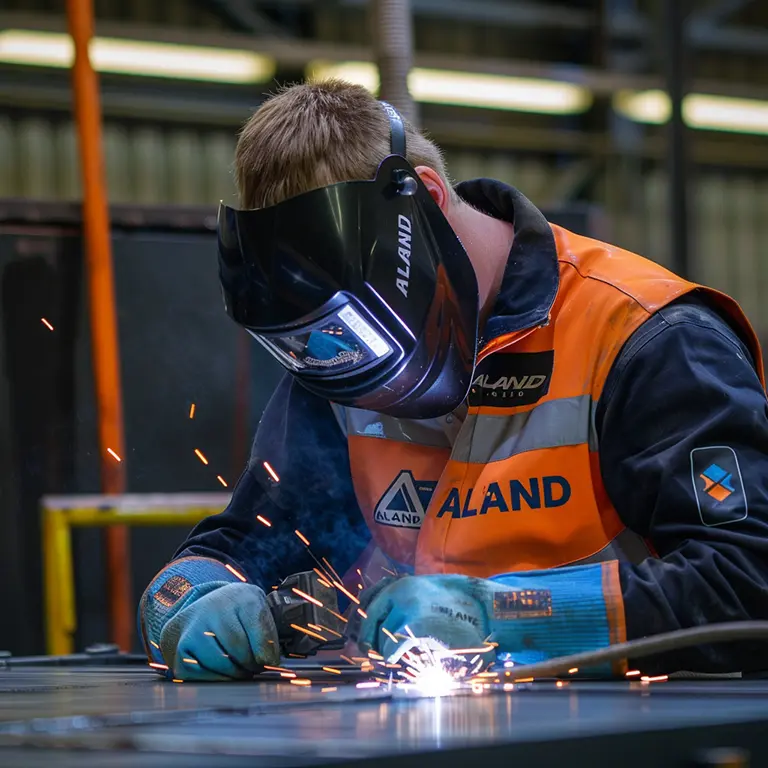
1. Concept of soldering flux
Soldering flux is an indispensable auxiliary material in the welding process, and its functions are diverse and important. First of all, soldering flux has a cleaning effect. They can effectively remove dirt, oxides and other impurities from the welding surface, ensuring the quality and reliability of the welded joints. This cleaning process is critical to obtaining high-quality welded joints, as surface contamination and oxides can lead to poor weld quality, reduced joint strength, and even weld failure.
Secondly, soldering flux can remove oxides on the metal surface, which will form obstacles during the welding process and reduce the welding quality and strength. By chemically reacting with oxides, flux can effectively remove them and provide a clean metal surface for welding, which is conducive to the fusion and diffusion of welding materials, thereby improving the quality and reliability of welded joints.
In addition, soldering flux can also facilitate the welding process. They help the solder make better contact with the base material and promote intermetallic diffusion as it melts, resulting in a stronger solder. Flux can also form a protective film to prevent the welding area from being polluted and oxidized by oxygen in the air, ensuring welding quality.
In addition, soldering flux also has the effect of reducing surface tension, which helps the flow of solder on the soldering surface, resulting in better soldering quality. Properly selected flux can also reduce the generation of gases during the welding process, reduce the formation of pores, and further improve the quality and reliability of welded joints.
Therefore, soldering flux plays an integral role in the welding process, and its selection and use need to be based on specific welding requirements, materials and conditions, and should be selected carefully to ensure welding quality and reliability.
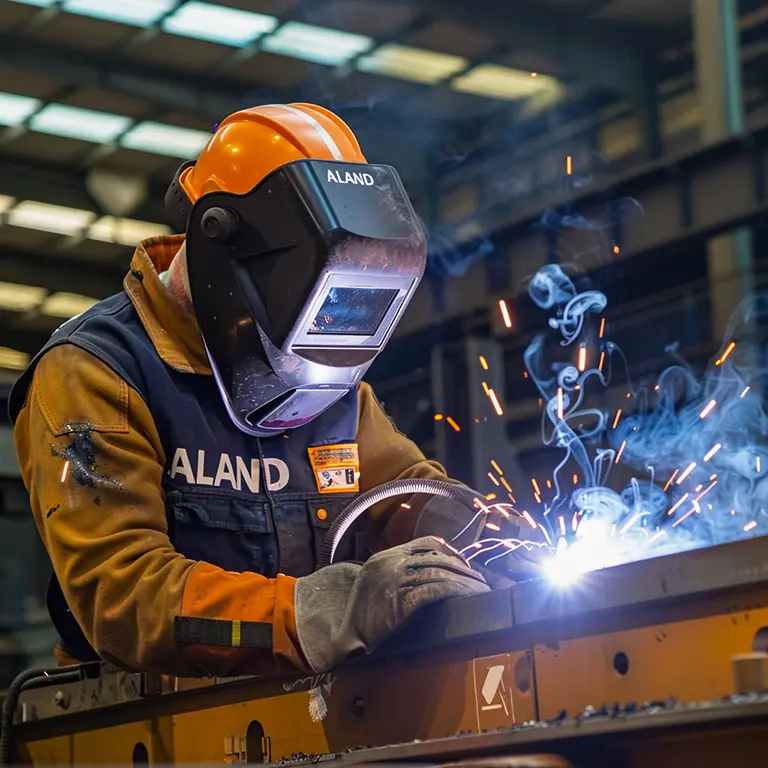
2. Classification of soldering flux
According to the manufacturing method of soldering flux, it can be divided into three categories: melting flux, sintering flux and bonding flux.
(1) Soldering flux: A certain proportion of various ingredients are smelted in a furnace, and the flux produced after water-cooling granulation, drying, and screening is called a soldering flux. The main advantage of smelting flux is that it has a uniform chemical composition, resulting in a weld with uniform properties. However, due to the high-temperature roasting process during the manufacturing process of the flux, the alloying elements will be oxidized, so iron alloys cannot be added to the flux. We can only rely on certain metal oxides to transfer a limited number of alloying elements through replacement reactions.
(2) Sintered flux is a kind of soldering flux that is made by adding a certain proportion of various powdery ingredients to an appropriate amount of binder, mixing and stirring, sintering at high temperature (400-1000°C) into blocks, and then crushing and screening. Sintered flux.
(3)Bonding flux is a flux made by adding a certain proportion of various powdery ingredients to an appropriate amount of binder, stirring, granulating and drying at low temperature (below 400°C). Formerly known as ceramic flux.
The latter two soldering fluxes are non-smelting fluxes. Since there is no smelting process, the chemical composition is uneven, resulting in uneven weld performance. However, if iron alloy is added to the flux, the alloying of the weld metal can be increased. Currently, smelting flux is widely used in production.
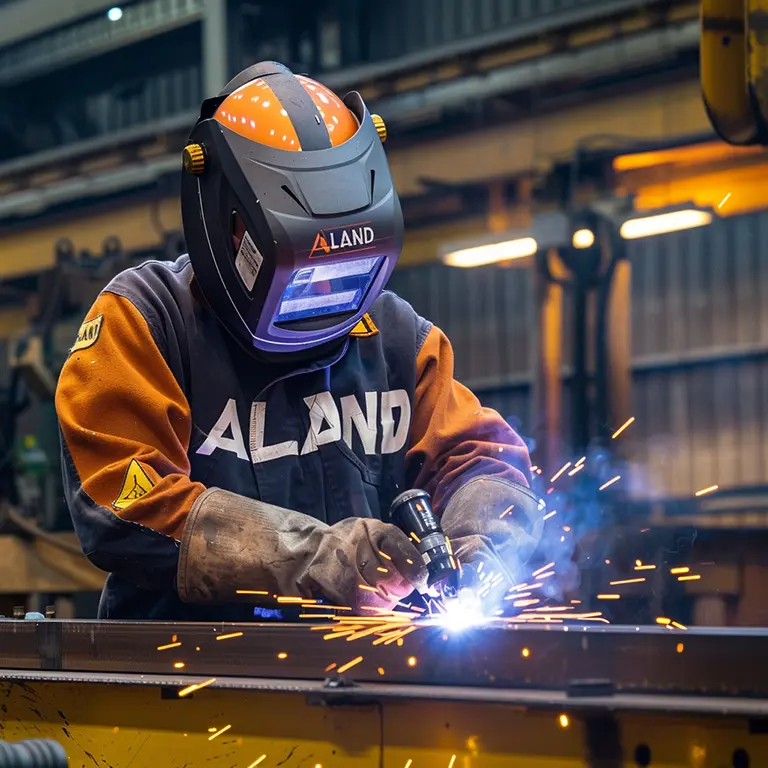
3. The role of soldering flux
The main active ingredient in the flux is rosin. Rosin will be decomposed by tin at about 260 degrees Celsius, so the temperature of the tin bath should not be too high.
Flux is a chemical that facilitates soldering. In soldering, it is an indispensable auxiliary material and its role is extremely important.
(1) Dissolve the oxide film of the welding mother
In the atmosphere, the surface of the base metal to be welded is always covered by an oxide film, with a thickness of approximately 2×10-9~2×10-8m. During welding, the oxide film will inevitably prevent the solder from wetting the base metal, and welding will not proceed normally. Therefore, flux must be applied to the surface of the base metal to reduce the oxides on the surface of the base metal, thereby eliminating the oxide film.
(2) Reoxidation of the base metal to be welded
The base metal needs to be heated during the welding process, and oxidation of the metal surface will accelerate at high temperatures, so liquid flux covering the surfaces of the base metal and solder can prevent them from oxidizing.
(3) Molten solder tension
The surface of the molten solder has a certain tension, just like rain falling on a lotus leaf. Due to the surface tension of the liquid, it will immediately coalesce into bead-shaped water droplets. The surface tension of molten solder will prevent it from flowing to the surface of the base metal, affecting the normal progress of wetting. When flux covers the surface of molten solder, it can reduce the surface tension of the liquid solder and significantly improve the wetting performance.
(4) Protect the welding base metal
The original surface protective layer of the material to be welded has been destroyed during the welding process. A good flux quickly returns to its role of protecting the welding material after welding. It can speed up the transfer of heat from the soldering iron tip to the solder and the surface of the soldered object; suitable flux can also make the solder joints beautiful
4. Performance of soldering flux
⑴The flux should have an appropriate activity temperature range. It starts to work before the solder melts, and plays a better role in removing the oxide film and reducing the surface tension of the liquid solder during the soldering process. The melting point of soldering flux should be lower than the melting point of solder, but not too different.
⑵The flux should have good thermal stability, and the general thermal stability temperature is not less than 100°C.
⑶The density of the flux should be less than the density of the liquid solder, so that the flux can spread evenly on the surface of the metal to be soldered, covering the surface of the solder and the metal to be soldered in a thin film, effectively isolating the air and promoting the wetting of the base metal by the solder.
⑷The residue of the flux should not be corrosive and easy to clean; it should not precipitate toxic and harmful gases; it should have water-soluble resistance and insulation resistance that comply with the regulations of the electronics industry; it should not absorb moisture and produce mold; it should have stable chemical properties and be easy to use storage.
5. The role of soldering flux in submerged arc welding
(1)Mechanical protection: The soldering flux melts into surface slag under the action of the arc, protecting the weld metal from the intrusion of gases in the surrounding atmosphere into the molten pool when it is in a liquid state, thereby avoiding pore inclusions in the weld.
(2)Transfer necessary metal elements to the molten pool.
(3)To promote a smooth and straight surface of the weld and a good shape, the melting point of the flux should be 10-30°C lower than the melting point of the solder. Under special circumstances, the melting point of the flux can be higher than that of the solder. If the melting point of the flux is too lower than that of the solder, it will melt prematurely and the flux components will lose their activity when the solder melts due to evaporation and interaction with the base material. The choice of flux usually depends on the properties of the oxide film. For alkaline oxide films such as oxides of Fe, Ni, Cu, etc., acidic flux containing boric anhydride (B2O3) is often used. For acidic oxide films, for example, for cast iron oxide films containing high SiO2, alkaline Na2CO3 is often used. The flux produces fusible Na2SiO3 and enters the slag. Some fluoride gases are also commonly used as fluxes. They react uniformly and leave no residue after welding. BF3 is often mixed with N2 to braze stainless steel at high temperatures. The flux used for brazing below 450°C is soft solder. There are two types of soft solder. One is water-soluble, which is usually composed of a single hydrochloride and phosphate or an aqueous solution of Soger salt. It has high activity and corrosion resistance. It is highly resistant and needs to be cleaned after welding. The other is a water-insoluble organic flux, usually based on rosin or artificial resin, with organic acids, organic amines or their salts of HCl or HBr added to improve the film removal ability and activity.
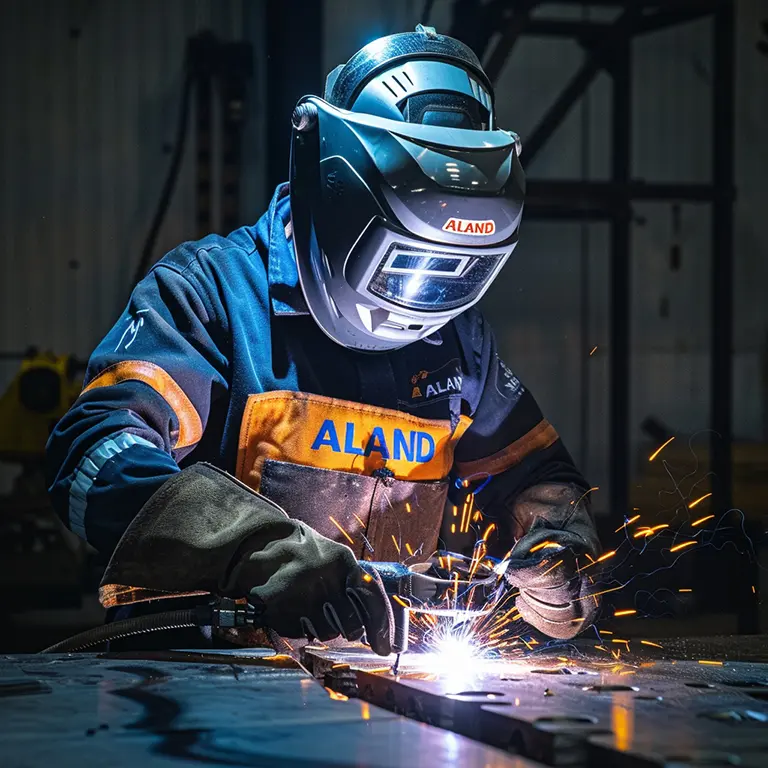
6.Control of soldering flux
(1)Drying and heat preservation control of soldering flux
Before using the flux, first bake it according to the specifications of the flux instructions. This drying specification is obtained based on testing and process inspection control, and has correct quality assurance data. This is an enterprise standard, and different enterprises require different specifications. Secondly, According to JB4709-2000 <<Steel Pressure Vessel Welding Regulations>> recommended flux drying temperature and holding time. Generally, when the flux is dried, the stacking height does not exceed 5cm. The welding material library often uses more instead of less in terms of the number of dryings at one time, and uses thicker instead of thin in terms of stacking thickness. This should be strictly managed to ensure the drying quality of the flux. Avoid stacking too thickly and extend the drying time to ensure the flux is thoroughly baked.
(2)On-site management and recycling and disposal control of soldering flux
The welding area should be cleaned and no debris should be mixed into the flux. The flux used for the flux pad must be distributed according to regulations. It is best to wait for use at about 50°C. The flux should be recovered in time to avoid contamination; it should be used multiple times in a row. The flux is sieved through 8-mesh and 40-mesh sieves to remove impurities and fine powder, and mixed with three times the new flux before use. It must be dried at 250-350℃ and kept warm for 2 hours before use. After drying, it must be stored in an insulated box at 100-150℃ for reuse next time. Storage in the open air is prohibited. If the site is complex or the relative environmental humidity is high, the control site must be managed in a timely manner to keep it clean, conduct necessary tests on the moisture resistance of the flux and mechanical mixtures, control the moisture absorption rate and mechanical inclusions, and avoid random piles and fluxes. mixed.
(3)Soldering flux particle size and distribution requirements
The flux has certain particle size requirements, and the particle size must be appropriate so that the flux has a certain air permeability and does not transmit continuous arc light during the welding process to avoid air contamination of the molten pool and the formation of pores. Flux is generally divided into two types, one with a normal particle size of 2.5-0.45mm (8-40 mesh), and the other with a fine particle size of 1.43-0.28mm (10-60 mesh). The fine powder smaller than the specified particle size is generally not more than 5%, and the coarse powder larger than the specified particle size is generally larger than 2%. The flux particle size distribution must be detected, tested and controlled to determine the welding current used.
(4)Control of soldering flux particle size and stacking height
If the flux layer is too thin or too thick, it will cause pits, spots and pores on the surface of the weld, forming an uneven weld bead shape. The thickness of the flux layer should be strictly controlled within the range of 25-40mm. When using sintered flux, due to its low density, the flux stacking height is 20%-50% higher than that of smelting flux. The larger the diameter of the welding wire, the higher the welding current, and the thickness of the flux layer will also increase accordingly; due to irregularities in the welding process and unfair handling of fine powder flux, intermittent uneven pits will appear on the surface of the weld. The appearance quality is affected and the shell thickness is partially weakened.
Articles you may be interested in:
Introduction To Welding Pad Process
Common Weld Aluminum Introduction
How To Choose Industrial Water Chiller
Introduction To Common Brazing Welding
Introduction To Common Pressure Welding
Introduction To Common Pipeline Welding
The Important Role Of Welding Positioners
Introduction To 1G To 6G Welding Positions
Underwater Welding Salary And Death Rate
Introduction To Common Welding Processes
Introduction to welding materials Welding wire
Introduction To Common Welding Carbon Rods
Selection And Introduction Of Common Welding Rods