Introduction to common Welding carbon rods
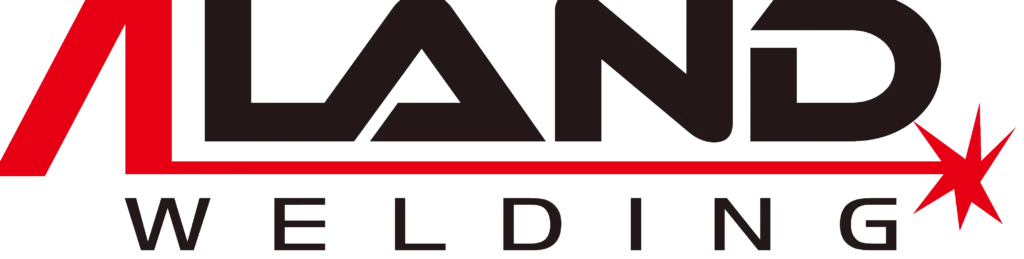
ALAND WELDING Let you feel the most sincere welding service
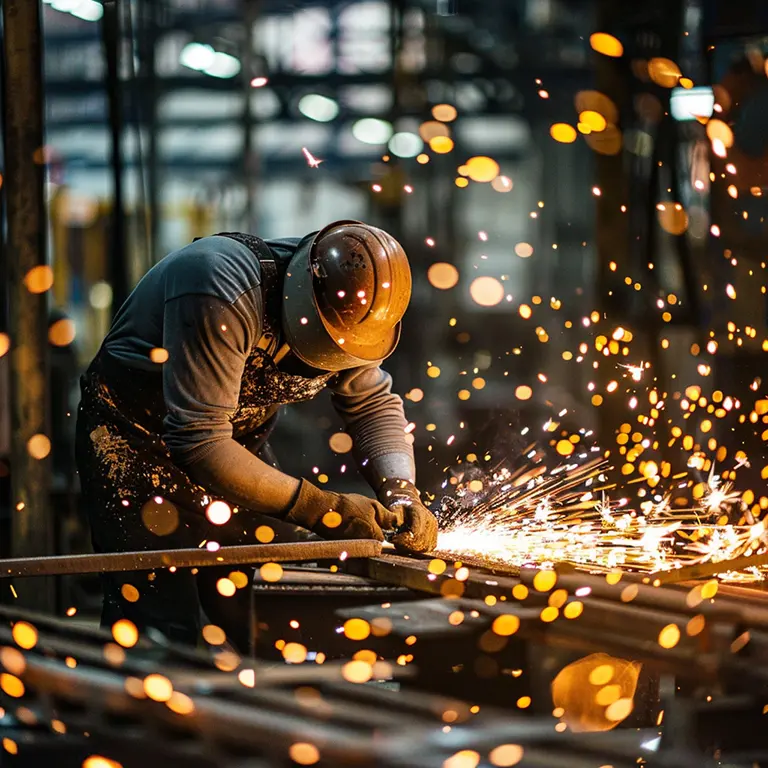
Welding carbon rod refers to a special method of welding using carbon rod (usually carbon or graphite material). In some specific welding applications, carbon rod is used as a welding material instead of traditional metal wire or electrode.
Welding carbon rod is usually used for welding special materials, such as some high-temperature alloys, ceramics, glass, etc. This is because traditional metal welding materials may introduce unnecessary impurities or produce undesirable reactions during the welding process of these materials. Carbon rods can provide a stable welding environment at high temperatures without introducing additional impurities.
The use of Welding carbon rod usually requires some special welding equipment and techniques. When using carbon rod for welding, it is usually necessary to control the temperature and welding pressure to ensure good welding results. In addition, the selection of carbon rods is also very important. The appropriate carbon rods need to be selected according to the specific welding materials and requirements.
1、carbon rod concept
Carbon rod is a non-metallic product. As a necessary pre-welding cutting consumable in the carbon arc gouging cutting process, it is made of carbon, graphite and appropriate adhesives, formed by extrusion, and baked at 2200°C. It is made by plating a layer of copper after the segment. It is high temperature resistant, has good electrical conductivity and is not easy to break. It is suitable for cutting metal into required shapes.
2.Carbon rod usage and performance
(1)Purpose
Because carbon rod is used at high temperatures, it is easy to conduct electricity and has good chemical stability. It is now widely used in national defense, machinery, metallurgy, chemical industry, casting, non-ferrous alloys, lightening and other fields. Especially black carbon rods are also used in ceramics, semiconductors, medicine, environmental protection, laboratory analysis and other fields, becoming today’s application The widest range of non-metallic materials. When cutting steel, there is no need to use flammable and explosive gases like oxygen-acetylene flame cutting, which is low cost and safe to operate. Arc cutting can be used to process a variety of metals that cannot be processed by gas cutting, such as cast iron, stainless steel, copper, aluminum, etc. It is highly efficient and can achieve ideal results.
(2)Performance
The component is hard and brittle, has a small expansion coefficient, can withstand rapid cooling and heating, is not easily deformed, has good chemical stability, has strong acid resistance, does not react with strong acids, has poor alkali resistance, and can corrode the decomposition rod at high temperatures. body.
The flexural strength of the carbon rod becomes harder as the temperature of the component increases. The resistance value of the component, reflected by the resistivity, is measured at 25 microohm.meter in accordance with the ministerial standards.
The surface load current density of the component is closely related to the raw material formula and pressing density of the black carbon rod, and can be adjusted as needed.
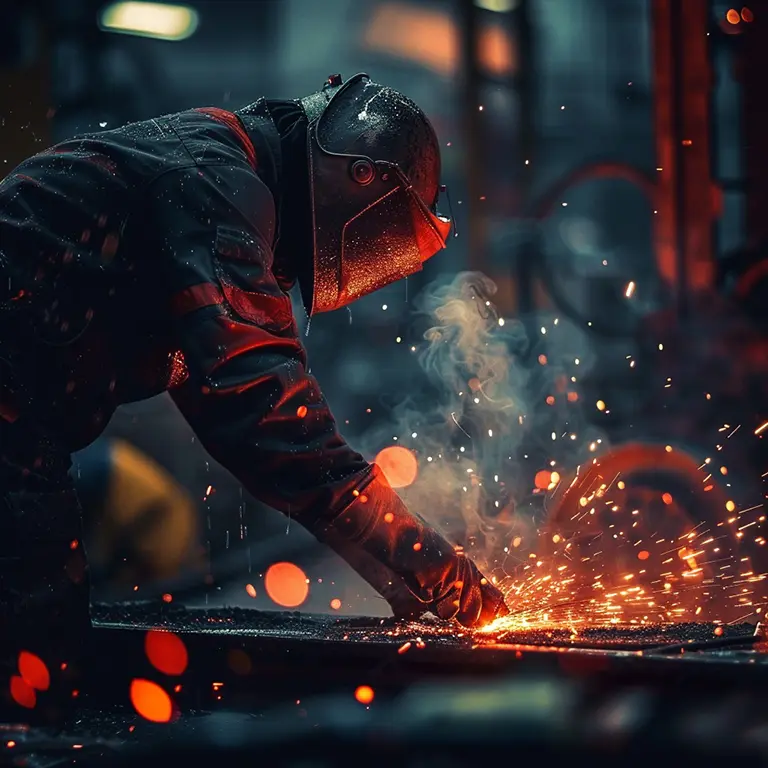
3.Welding carbon rod classification
Round carbon rod: mainly used for root cleaning of welds, back grooving and removal of welding defects;
Rectangular carbon rod: used for removing temporary weld beads and weld scars remaining on components, removing weld reinforcements and carbon arc cutting;
Connected carbon rods: suitable for automatic or manual welding guns. Continuous feeding can reduce the loss of residual carbon rods during use. The grooves have high precision, smoothness and uniformity, good stability and high efficiency.
4.Instructions for use of Welding carbon rod
(1) The carbon rod must be kept dry and must be dried before use when it gets wet.
(2) When used in DC power supply, the carbon rod is connected to the positive pole of the power supply and the working pole is connected to the negative pole.
(3) The compressed air pressure is maintained at 0.5-1.6MPa.
(4) The arc distance between the carbon rod and the workpiece is about 3mm, and the exposure of the carbon rod to the fixture is about 100mm.
(5) The carbon rod forms an angle of 45° with the workpiece and is planed along the tangential (or straight) direction.
(6) Carbon rods must be well ventilated when used. Operate according to working current.
5.Safety precautions for using Welding carbon rod
(1) Safety equipment: Make sure to wear appropriate personal protective equipment when performing welding operations, including welding masks, welding gloves, heat-resistant clothing, fire-resistant boots, etc. These equipment can effectively protect the skin from flames and thermal radiation.
(2) Working environment: Ensure that the welding work site has adequate ventilation to prevent harmful gases from accumulating in the work area. If possible, try to move welding operations outdoors or provide special exhaust equipment.
(3) Welding equipment inspection: Before using welding equipment, be sure to check the working status of the welding machine and accessories. Make sure the welding machine is functioning properly and that cables and power cords are intact.
(4) Carbon rod handling: Before using the carbon rod, check whether the carbon rod is damaged, deformed or contaminated. Damaged carbon rods may affect welding quality, while contaminated carbon rods may introduce impurities, affecting welding results.
(5) Preheating and temperature control: For some materials that require high temperature welding, the welding area needs to be preheated to reduce welding stress and deformation. In addition, the temperature of the welding area needs to be controlled to ensure that the material does not become too hot or too cold during the welding process.
(6) Welding technology: Select appropriate welding technology and parameters, including current size, welding speed, arc stability, etc. Maintain stable technique and speed during the welding process to ensure welding quality.
(7) Follow-up processing: After completing the welding, subsequent processing of the welding area needs to be carried out, including removing welding residues, cleaning the welding area, applying a protective layer, etc. These steps help improve the stability and durability of the welded joint.
(8) Quality inspection: Finally, perform quality inspection of the welded joints. Check whether the weld is uniform and complete, and whether there are pores, cracks and other defects. When necessary, non-destructive testing can be performed to ensure that the welding quality meets the requirements.
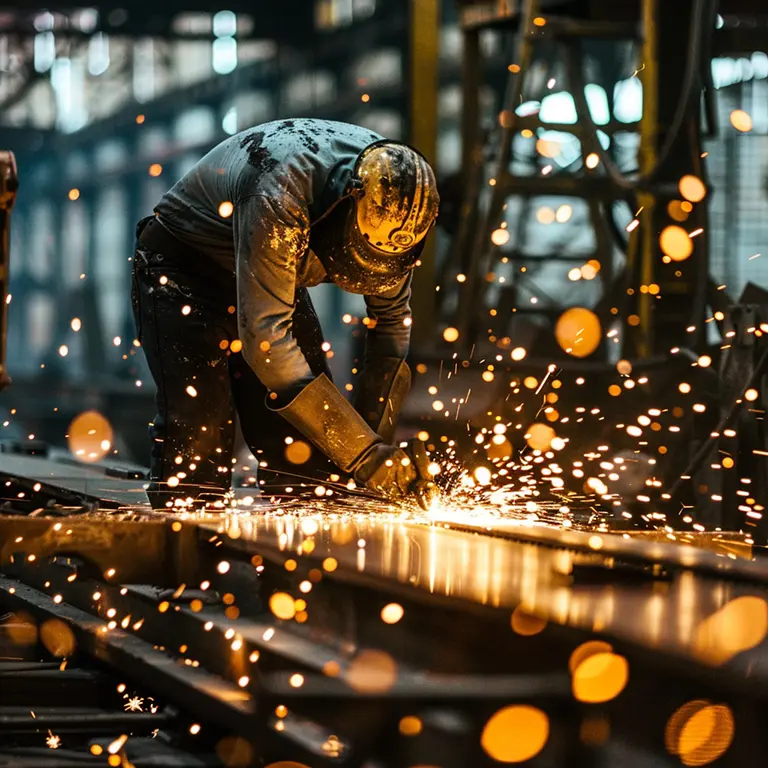
6.Usage scenarios of Welding carbon rod
(1) Aerospace industry: In the aerospace field, carbon rod is often used to weld high-temperature alloy components, such as turbine engine blades, jet engine combustion chambers, spacecraft structural parts, etc. These parts often need to withstand extreme temperatures and pressures, and carbon rod’s stability and high temperature resistance make it an ideal welding material.
(2) Automobile manufacturing industry: In automobile manufacturing, carbon rod can be used to weld special materials, such as carbon fiber composite body parts. The use of carbon rod can ensure the strength and conductivity of the welding joint while reducing the impact on vehicle weight and performance.
(3) Electronic device manufacturing: In electronic device manufacturing, carbon rod can be used to connect or repair components such as ceramic substrates and glass packages. These components are often used to make high-frequency circuits, sensors, lasers, etc. The welding properties of carbon rods ensure high-quality connections.
(4) Chemical equipment manufacturing: Chemical equipment usually requires special materials that are corrosion-resistant and high-temperature resistant, such as titanium alloys, nickel-based alloys, etc. Carbon rods can be used to weld these materials to ensure the stability and durability of the welded joint and avoid chemical reactions or material corrosion.
(5) Laboratory and scientific research applications: In the field of scientific research, Welding carbon rod is often used to connect or repair special materials in experimental devices, such as ceramic sample holders, high-temperature experimental devices, etc. The flexibility and controllability of carbon rods make them an important tool in the laboratory.
Articles you may be interested in:
Introduction To Welding Pad Process
Common Weld Aluminum Introduction
How To Choose Industrial Water Chiller
Introduction To Common Brazing Welding
Introduction To Common Pressure Welding
Introduction To Common Pipeline Welding
The Important Role Of Welding Positioners
Introduction To 1G To 6G Welding Positions
Underwater Welding Salary And Death Rate
Introduction To Common Welding Processes
Introduction to welding materials Welding wire