The Most Complete Welding Defects And Solutions, A Must-read for Welders!
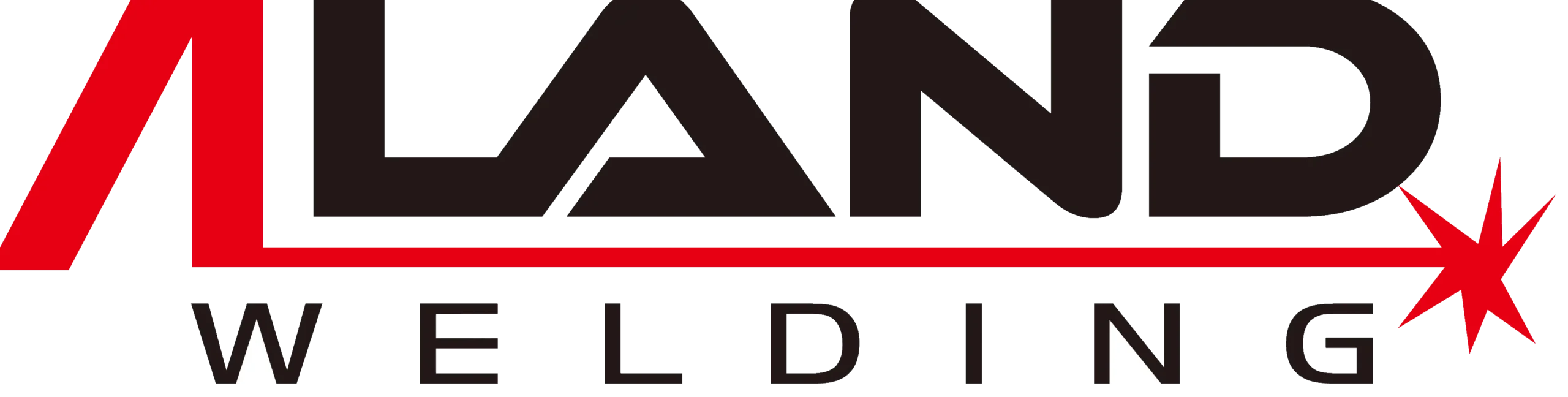
ALAND WELDING Let you feel the most sincere welding service
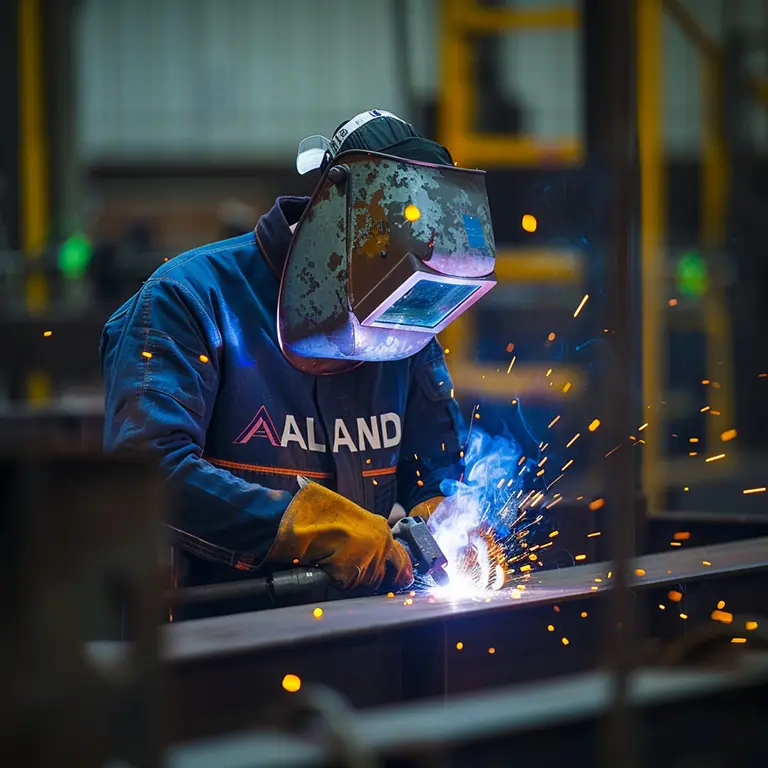
Welding Internal Defects
1、Stomata
(1)Phenomenon
Single, strip or group pores appearing in the weld are the most common defects inside the weld.
(2)Cause Analysis
The fundamental reason is that during the welding process, the gas generated by the welding itself or external gas enters the molten pool and does not have time to overflow the molten pool before solidifying and remains in the weld.
(3)Prevention
Preventive measures are mainly considered from two aspects: reducing the amount of gas in the weld and enhancing the overflow of gas from the molten pool. The main points are as follows:
1. Welding rods are required to be baked and installed in an insulating cylinder, ready for use;
2. The welding wire must be clean and free of oil stains and other impurities;
3. Clean the 10 to 15mm area around the weldment until it emits a metallic luster;
4. Pay attention to the surrounding welding construction environment, set up windproof facilities, and ensure that there is no draft when welding pipes;
5. During argon arc welding, the purity of argon gas should not be less than 99.95%, and the argon gas flow rate should be appropriate;
6. Use short arc welding as much as possible to reduce the chance of gas entering the molten pool;
7. The welder’s operating techniques are reasonable and the angles of the welding rod and welding gun are appropriate;
8. The welding line energy is appropriate and the welding speed cannot be too fast;
9. Preheat the weldment according to process requirements.
(4)Governance measures
1. Strictly follow preventive measures;
2. Strengthen welder training to improve operation level and sense of responsibility;
3. Take digging and filling measures for excessive pores discovered during the flaw detection process.
2、Slag
(1)Phenomenon
During the welding process, impurities such as coatings are mixed in the molten pool, and inclusions in the weld are formed after the molten pool solidifies.
(2)Cause Analysis
1. The weldment is not cleaned cleanly, the coating between multi-layer and multi-pass welding layers is not cleaned clean, the coating falls off in the molten pool during the welding process, etc.;
2. The arc is too long, the welding angle is too large, the welding layer is too thick, the welding line energy is small, the welding speed is fast, etc., resulting in the molten impurities in the molten pool not emerging and the molten pool solidifying.
(3)Prevention
1. Polish and clean the 10 to 15 mm surface area around the weld break of the weldment until it emits a metallic luster;
2. When multi-layer and multi-pass welding, clean the coating between layers;
3. The welding rods are baked as required, and unqualified welding rods such as eccentric or damp are not used;
4. Use short arc welding as much as possible and choose appropriate current parameters;
5. The welding speed is appropriate and not too fast.
(4)Governance measures
1. Thoroughly clean the surface of the weldment before welding;
2. Strengthen practice, become proficient in welding operation skills, and have a strong sense of responsibility;
3. Take measures such as excavation and filling to deal with the defects with excessive slag inclusion discovered during the flaw detection process.
3、Not fused
(1)Phenomenon
There are two main types of non-fusion: the root is not fused and the layers are not fused. The lack of fusion at the root mainly refers to the lack of fusion between the weld metal and the base metal and the welding joint during the base laying process; the lack of fusion between layers mainly refers to the lack of fusion of the weld metal between layers during the multi-layer and multi-pass welding process.
(2)Cause Analysis
The main reasons for lack of fusion are low welding line energy, fast welding speed or improper operation techniques.welding defects.
(3)Prevention
1. Increase the welding current appropriately and increase the welding line energy;
2. The welding speed is appropriate and not too fast;
3. Proficient operating skills, correct angle of welding rod (gun).
(4)Governance measures
1. Strengthen practice, improve operating skills, and make welders have a strong sense of responsibility;
2. For different base metals and welding materials, formulate and implement corresponding measures to deal with non-fusion defects at different locations.
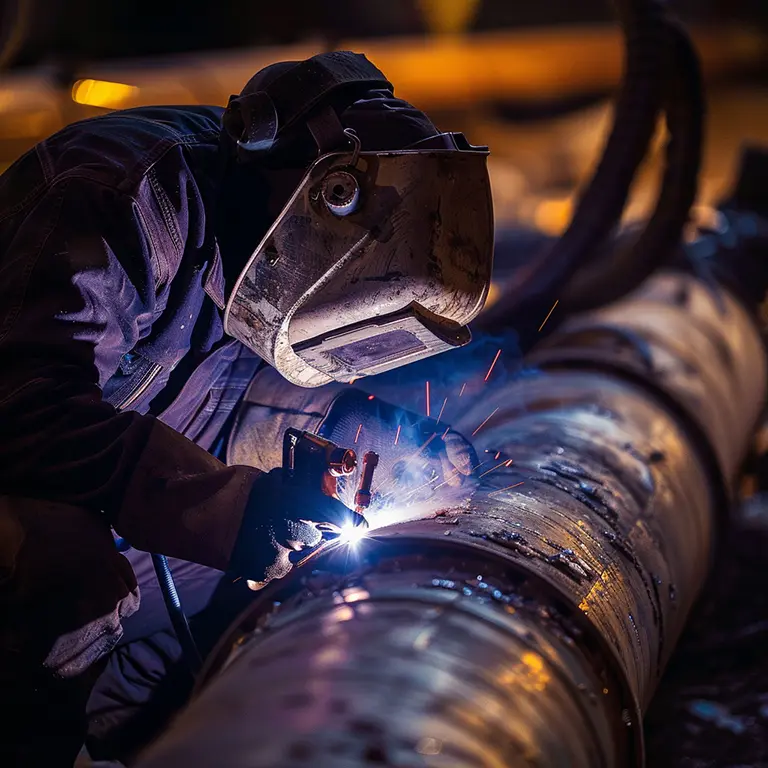
4、Pipe welding joint is not fully welded
(1)Phenomenon
When welding the welding joint, the weld penetration depth is not enough and the base metal is not penetrated.
(2)Cause Analysis
The main reasons for incomplete welding are: too small gap between joints, small groove angle, thick blunt edge, small welding line energy, fast welding speed, and improper welding operation techniques. welding defects.
(3)Prevention
1. Strictly implement the standard requirements for the gap between the mouths, and the best gap should not be less than 2mm.
2. The angle of the counter groove shall be in accordance with the wall thickness and the requirements of DL/T869-2004 “Technical Regulations for Welding of Thermal Power Plants”, or in accordance with the design requirements of the drawings. Generally, welding joints with a wall thickness less than 20mm adopt V-shaped grooves, with a single side angle of not less than 30°, and welding joints with a wall thickness of not less than 20mm adopt double V-shaped or U-shaped comprehensive grooves.
3. The thickness of the blunt edge is generally about 1mm. If the blunt edge is too thick, use mechanical grinding to trim it. For a single V-shaped groove, the blunt edge does not need to be left.
4. Choose appropriate line energy, welding speed and operating techniques according to your own operating skills.
5. Use short arc welding to increase penetration capability.
(4)Governance measures
1. The gap between the joints, the preparation of the bevel, and the thickness of the blunt edge meet the standard requirements;
2. Strengthen base practice and master the operation techniques, corresponding welding line energy and welding speed.
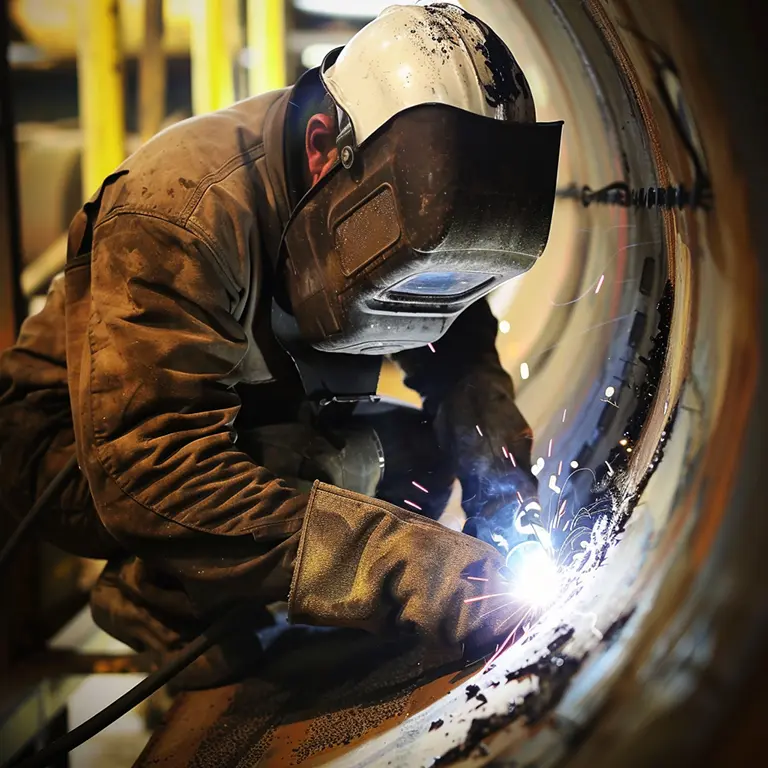
5、Nodules, protrusions, and depressions at the root of the pipe weld joint
(1)Phenomenon
These defects generally appear at the root of the hanging welding or tilt welding joint, the root weld protrusion or welding nodule appears at the flat welding and tilt flat welding positions, and the depression appears at the overhead welding position.
(2)Cause Analysis
The causes of these defects are: large gap between the openings, thin and wide blunt edges, too high temperature of the molten pool, excessive time in one place for the molten pool, improper control of the molten pool, and the thrust of the arc when forming dent defects. Not enough is also an important reason. welding defects.
(3)Prevention
1. The gap between the butt joints meets the standard requirements, generally 2 to 3 mm; for welding joints with uneven joint gaps, try to trim them to the specified requirements by mechanical grinding and other methods.
2. If the blunt edge of the groove does not meet the requirements, grind and trim it to the specified requirements.
3. Choose appropriate welding line energy and appropriate welding speed, and control the molten pool temperature within an appropriate range, not too high.
4. Use short arc welding as much as possible for overhead welding parts to enhance arc thrust.
(4)Governance measures
1. Before butt spot welding, check that the butt gap and the thickness and width of the blunt edge of the groove meet the standard requirements;
2. Strengthen practice and enhance the ability to master appropriate current parameters and control the appropriate temperature of the molten pool;
3. If the above-mentioned defects are discovered during the primer process, corresponding measures should be taken promptly.
6、Internal cracks
(1)Phenomenon
Internal cracking defects that occur in the weld seam, fusion line, and heat affected zone of the welded joint.
(2)Cause Analysis
The causes of cracks vary due to different steel types, welding methods, welding environments, preheating requirements, impurity content in welded joints, assembly and welding stress, etc., but there are two fundamental causes of cracks: the internal structure of the crack. Inducements and necessary stress. welding defects.
(3)Prevention
1. Prepare various welding conditions in strict accordance with the requirements of the regulations and work instructions;
2. Improve welding operation skills and become proficient in using welding methods;
3. Take measures such as reasonable welding sequence to reduce welding stress.
(4)Governance measures
1. Take corresponding countermeasures for each specific cause of cracks;
2. For welded joints that have cracked, formulate treatment measures, such as excavation and repair.